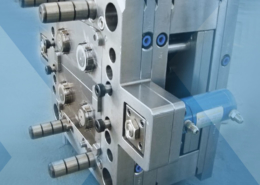
Prototype Plastic Injection Molding Online Quotes - prototype injection
Author:gly Date: 2024-10-15
The Plastic Injection Moulding Business must register the unit with local authorities as per section 6 of the Factories Act, 1948, as the facility falls under the definition of “factory”. Documents required for obtaining this licence will vary as per the state where the business is located. However, a standard list of documents required are
The pollution caused by plastic injection moulding business aspects is regulated by the respective State Pollution Control Board, which issues them Consent to Establish (CTE)[1]. The manufacturer/producer must obtain the certificate before the manufacturing facility is instituted as per the Air Act and the Water Act. Before commencing the operation of the Injection Moulding Business, the second certificate, i.e. Consent to Operate (CTO), is issued by the same board only after a satisfactory site inspection.
A broad range of products: a variety of plastic parts from syringes to parts of medical devices can be made using plastic moulding. This technique is widely used in various industries such as the medical industry (for bottling and packaging), electronics and electrical Industry, toy Industry, food and beverage packing industry, construction industry, and daily needed consumer products like buckets, drums, etc.
If the owner of the Plastic Injection Moulding business wants to apply for Micro, Small, and Medium Enterprise (MSME) registration, he must fulfil all formalities via the online portal of the authority and upload the mandated documents.
Low cost of production: though the initial cost of injection moulding machines and setting up the entire facility is somewhat costly, the price of production per piece is very low.
Whether you’re using custom plastic injection molding to manufacture medical devices more efficiently, to prevent contamination of apparel products, or to reduce the weight of car parts and components, Sonoco has the experience, expertise, and craftsmanship to ensure the success of your project.
Sonoco provides custom injection molding services to make plastic parts and components for virtually any product application across a range of industries. Businesses who demand the best use our custom injection-molded plastics in a wide variety of products, from surgical-grade medical devices to highly technical automotive components.
Just over 100 years ago, the first injection moulding machine was introduced as a means of mass production. The device was simple but effective, but since then, the innovation in the technology has led to changes in many aspects of the machine speed, fit and finish of the product and customizability of the machine to churn out products of different shapes and sizes. Injection moulding is a process of manufacturing that allows the production of plastic parts in large quantities. It is typically used as a mass-production technique for a whole plastic item or any plastic part/s of other products that are later assembled. Though the injection moulding process can also include materials like metals, glasses, elastomers etc., it is most commonly used with thermoplastic and thermosetting polymers. Many small and medium plastic injection moulding businesses in India today compete in a particular segment because of many factors like mass production of a specific product but limited due to machinery or infrastructure. It is also done to reduce the additional cost due to changes in product type.
Plastic moulded parts provide a solution for high volume and cost-efficiency. The recent trend of keeping parts lightweight and cheap without much joints is a desired feature for many products today, and the plastic injection moulding business ticks all the boxes. The growth of many industries spurs the demand for moulded parts, such as the automotive industry, where the day-to-day changes in design to enhance fuel efficiency by reducing the weights resulted in increased use of plastic moulded parts. If a solid business plan is met with proper guidance and assistance at the initiation and setup of such businesses, plastic injection moulding businesses will go a long way with the rising demand for plastic moulded components in medical device manufacturing.
Less waste Generation: Injection moulding produces a very low amount of waste. As the entire process is mechanised, a minimal amount of waste can be ground back into pellet form and reused.
The India injection moulding machine market size was estimated at 0.73 billion US Dollars in 2021 and is projected to grow at a CAGR of 6.1% from 2022 to 2030. The dies and moulds market in India is segmented by end-user (automotive, construction, electronics, machine tools, and others) and application (casting, forging, and injection moulding). If we look at the end-user, the automotive segment will have a significant market share in this growth during the abovementioned forecast period.
Registering the plastic injection moulding business with appropriate authorities will help obtain subsequent authorisation and licences from different authorities like the CPCB and SPCB/PCC. The documents needed in this regard are
If a manufacturer comes under the definition of the term “producer” under the Plastic Waste Management Rules, he/she will need an Extended Producer Responsibility (EPR) Authorisation from the CPCB. Documents required in this regard are
A fire certificate is granted by the concerned fire department of the respective state to ensure that commercial property is built with adequate fire-resistant measures. The standard documents needed are
At Sonoco, we believe in harnessing the power of process to drive innovation. Our proprietary i6 Innovation Process leverages market insights with advanced technical expertise to fully imagine, test, produce and deliver 360-degree solutions. While innovation demands creativity, free-thinking and imagination, the i6 Innovation process gives it direction, power and purpose. Adhering to this disciplined approach is vital to helping solve problems and consistently deliver repeatable, scalable custom plastic injection molding services for our customers.
Guiding customers through every stage of a custom precision molding project, our comprehensive approach includes advanced design and engineering assistance, mold making, prototyping, real-world testing and automated assembly services.
Repeatability: Plastic injection moulding is a repeatable process, and the product delivered is exactly similar. The first part can be the same as the hundredth, the thousandth, or more. If someone produces a large number of parts over the course of years, it is beneficial to have consistency and efficiency in the products, which further gives a business an advantage over other means of production. In contrast, any other production process may take different dyes or techniques altogether to make the same part. Also, the scope of variation in terms of colour, shape, design and size of the products is limitless.
According to a Central Pollution Control Board (CPCB) report, India produces approximately 3.3 million metric tons of plastic waste annually due to. Despit...Read More
Extended Producer Responsibility (EPR) is a legal responsibility imposed on producers of certain products that the producer introduces in the market that a...Read More
GETTING A QUOTE WITH LK-MOULD IS FREE AND SIMPLE.
FIND MORE OF OUR SERVICES:
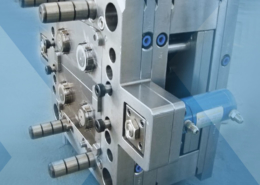
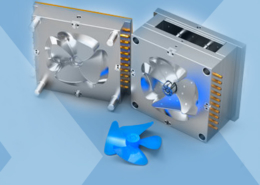
Plastic Molding

Rapid Prototyping
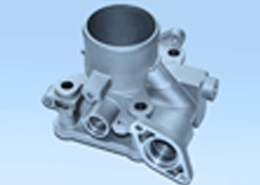
Pressure Die Casting
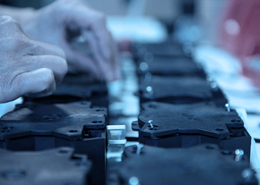
Parts Assembly
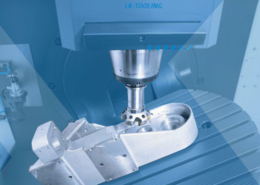