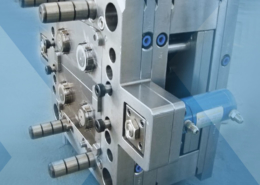
Prototype Plastic Injection Molding Online Quotes - prototype injection molding
Author:gly Date: 2024-10-15
With over 20 years of experience in the industry, HITOP has a history of exporting high-quality molds to the world. They can handle all sizes and weights of molds, showing their strength.
The company offers Short-run, medium-run, and long-run Injection Molding, Insert Molding, Over Molding, Hot Runner Molding, and Cold Runner Molding.
From design and prototyping to mold creation, manufacturing, and fulfillment. No outsourcing and no complexity; they cover the entire process. Their commitment to quality and American manufacturing means consistent results, fast turnaround, and good parts.
Have you ever thought about how all those plastic things around you got there? From water bottles to phone cases, plastic injection molding is the magic behind many everyday items. It uses molds to shape molten plastic into specific shapes.
Established in 1982 as Amtech Mold & Engineering in Fraser, Michigan, Hi-Tech Mold & Engineering has become an industry leader. Throughout the years, they have added capabilities and facilities to meet customer needs.
They do it all in-house, from product design and prototyping to final production and fulfillment. So, you have one-stop shopping for all your plastic parts needs.
Founded in 2000, Valencia Plastics has become a full-service plastic injection and blow molding manufacturer. Their mission is to turn ideas into products and guide clients through the entire development process from concept to shelf. They are a recommended partner for companies looking for reliable plastic parts.
The company also invests in the latest technology and processes to meet your specific needs. Their core values – respect, trust, excellence, communication, and teamwork – guarantee a collaborative and professional working relationship.
Britech Industries was founded in 1984 as a small Florida supplier of basic rubber parts. They started by serving local manufacturers with extruded rubber products like grommets. Their customer-centric approach led them to add custom molded parts and die production in 1995.
They serve a wide range of clients. It includes some of the world’s most innovative companies in technology, defense, aerospace, medical, automotive, and IoT.
Second, they put quality first. ISO 9001 certified and using high-grade materials, your parts will meet the highest standards. Third, Valencia Plastics is eco-friendly. They use recycled resins and energy-efficient practices whenever possible.
Apart from this, it covers Custom Inventory Management, Component Sourcing, Prototyping, Part Assembly, Specialized Packaging, Product Testing, and Program Management.
Remedies: Increase the injection pressure or speed. While these two parameters are related, it is not proper to adjust them both at the same time. Adjust them each independently and monitor the results closely to determine whether or not the other needs adjustment. As a rule-of-thumb, it is best to make adjustments in increments of no more than 10% of the original setting.
We are committed to helping you elevate quality standards, fostering enterprise growth, and actualizing your internationalization strategy.
Hi-Tech Mold & Engineering is the ideal partner for a business enterprise in search of a comprehensive one-stop manufacturing solution.
Several reasons to choose Bennett Plastics for your injection molding needs. They will communicate openly and work closely with you to ensure your project meets your vision.
HITOP is committed to assisting customers by offering a comprehensive one-stop solution, encompassing product design enhancement, initial sample creation, mold fabrication, injection molding, and product assembly.
Injection molding is used in many industries to make so many different parts. It’s a process of injecting molten plastic into a mold cavity that cools and solidifies into shape.
Britech Industries is experienced and innovative. Over 35 years in the business and always adding more to what they do to meet customer needs.
Rapid prototyping and secondary processing services are also available for automotive, electronics, and medical products.
Remedies: Increasing the barrel temperatures will allow the flow fronts to stay hotter longer and complete the filling of the mold. Make sure the proper profile is being used and that the material heats progressively as it travels through the barrel from rear to front.
Our Ironwood, Michigan, and Two Rivers, Wisconsin, facilities have a team with over 200 years of combined experience. So, you can trust us with your toughest projects.
Kaysun works with you throughout the entire process. This is evident from their pre-production phase where it spends a lot of time understanding your application. The partnership approach ensures a seamless transition from design to production and reduces potential issues and time-to-market.
Founded in 1946, Kaysun Corporation has a long history in the injection molding industry. It aims to make a positive impact on people’s lives through the products we make and the services we provide. Kaysun is more than just a supplier; it is a partner that will exceed your expectations.
HITOP doesn’t just sit back and settle for the status quo. They actively seek and integrate the latest technology to achieve higher precision in their injection molding process. That’s what excellence means to them.
Choosing the right injection molding company means high-quality parts and fast production. This article looks at the top 10 plastic injection mold companies worldwide. Here are some of them:
Remedies: Inspect the non-return valve mechanism and replace worn or damaged components. This wear is normal but is accelerated by molding materials that have reinforcements (such as glass) in them. The valve should be inspected at least every three months.
Remedies: Increase the back pressure to increase the melt temperature and improve the ability for the fronts to flow. This is best accomplished by starting at the minimum of 50 psi and increasing in 10-psi increments until the proper flow is attained. Do not exceed 300 psi. The higher the back pressure the hotter the plastic, and excessive back pressure will thermally degrade the plastic.
Quality and service are evident in their just-in-time inventory and custom manufacturing. Whether you require rubber parts, custom extrusions, or injection molded plastics, Britech can be a one-stop shop for your needs.
Remedies: Relocate, or redesign, the gate so that the molten plastic is directed against an obstruction such as a core pin. This will cause the material to disperse and continue to flow instead of slowing down.
Address: Ironwood Plastics, Michigan Location (Ironwood Division), 1235 Wall Street, Ironwood, MI 49938. P: 906.932.5025
Ironwood Plastics has several reasons why you should choose them for your complex molding needs. They have a team that has over 200 years of combined experience. Also, they handle your toughest projects; insert molding and engineered materials are our specialty.
Remedies: Place the mold in a machine that utilizes the 20% to 80% rule. This states that, ideally, a barrel should be sized such that 50% of the capacity is used every shot, but based on heat sensitivity of the material being used, that ratio can be between 20% for most materials and 80% for heat sensitive materials. This formula allows enough time for the material to absorb heat properly before being molded.
Remedies: Increase the mold temperature to the point at which the material has the proper flow and packs out the mold with maximum fill. Start with the material suppliers recommendations and adjust accordingly. Allow 10 cycles for every 10-degree change for the process to re-stabilize.
Remedies: Decrease the feed throat temperature. The material supplier can provide the proper temperature value for a specific material. Make sure there is no obstruction in the water line used for cooling the feed throat.
Remedies: Vent the mold by grinding thin (0.0005''-0.002'') pathways on the shutoff area of the cavity blocks. The viscosity of the plastic being molded determines the depth of the vent. Stiff materials can utilize deeper vents but fluid materials require thinner vents. In either case, the concept is to remove air from the mold as fast as possible with as deep a gate as the material viscosity will allow.
It offers CNC Machining, Additive Manufacturing, Plastic Injection Molded Components, Value-added assembly, Product Design and Development.
Their online marketplace is the bridge between manufacturers and a global network of suppliers. Businesses can source parts, get quotes and lead times, and reduce development time and supply chain volatility.
Remedies: Utilize a material that has the stiffest flow possible without causing non-fill. Contact the material supplier for help in deciding which flow rate should be used for a specific application.
The products include 3D Printing (plastic and metal), CNC Machining, Injection Molding & Tooling, Sheet metal fabrication, Prototype Fabrication, and more.
Several reasons are there to choose Four Processes for your injection molding. Open communication and honesty build trust that everyone is working towards the same goal.
Hi, I am Sparrow Xiang, COO of the HiTop company, me and my team would be happy to meet you and learn all about your business, requirements and expectations.
HITOP Industrial has high-capacity molding machines that can mold up to 3500 tons – multi-cavity, two-color, gas assist, and low-pressure molds.
Several reasons to choose Valencia Plastics for your plastic molding needs. First, they offer a complete solution, from concept development to production.
Founded in 1979, Ironwood Plastics has been a leader in complex injection molding for years. Acquired by CTB, a Berkshire Hathaway company, in 2010, we continue to invest in the latest technology and quality craftsmanship.
Remedies: If possible, run the machine on the automatic cycle, using the operator only to interrupt the cycle if an emergency occurs. Use a robot if an ``operator'' is necessary. In addition, instruct all employees on the importance of maintaining consistent cycles.
It offers Plastic Injection Molding, Blow Molding Products, Design and Development, Mold Making, Inventory Management, and Additional Services.
Their one-stop shopping eliminates the need to manage multiple vendors and saves you time. Fathom has a national footprint with over 450,000 sqft of manufacturing space across 12 facilities. All that capability is under one roof.
And the company is run by a team of old hands with tech, finance, and manufacturing experience. That’s cutting-edge tools, options, and leadership – Xometry is the future of smart manufacturing.
The main products include Injection Molding, 3D Printing/Prototyping, Custom Plastics Mold Design, Value-Added Finishing Warehousing and Fulfillment.
The internet helped them grow, and now they have dedicated divisions for custom rubber extrusions and injection molded plastics. They are a one-stop shop for all rubber and plastic needs.
It analyzes complex parts in real time and matches buyers with the best suppliers globally. Time and money saving and production optimized. Xometry also has convenience in spades through its marketplace.
Fathom’s commitment to innovation and full service makes them a great partner for your product development journey. They offer everything from rapid prototyping to low to mid-volume production.
Short Shots and/or Non-fill can be defined as an incomplete molded part caused by insufficient material injected into the mold. Non-fill can be an extension of a flow line or knit line condition.
Looking for a quality injection molding partner that goes above and beyond? Contact HITOP Industrial today to talk about your project and get a quote.
Xometry was founded in 2013 and is now a leading digital company in the $2.4 trillion manufacturing industry. The company is based in Maryland and uses AI to make manufacturing and procurement easier.
In 1974, Hubert Fox, a US Army veteran and entrepreneur, founded Four Process Ltd. started as a small machine shop. More than a manufacturer, Four Process is your reliable friend working with you through the entire process.
But HITOP’s goal is not just to comply. They want to create real value for their customers, drive their satisfaction, and exceed their expectations. HITOP sees customer satisfaction as the starting point, not the finishing line, of its service.
Remedies: Examine the gates and runners to determine if any burrs or other obstructions exist. If possible, perform a computer analysis to determine the proper sizing and location of gates and runners. Ask the material supplier for data concerning gate and runner dimensioning for a specific material and flow rate.
The plastic injection molding world is huge, and many companies are vying for your business. Choosing the right one depends on your project needs and priorities. This article listed the top 10 injection molding companies in the world, their areas of expertise, and unique selling points.
In 1987, they moved to a new, larger facility in Rochester Hills, Michigan, and became Hi-Tech Mold & Engineering. This was the start of a period of rapid growth, with four more plants added in Rochester Hills by 1995.
For companies looking for a reliable partner with a history of complex projects, Ironwood Plastics stands out. They have the experience and the technology to handle the toughest jobs.
This has accumulated over forty years of experience, which in turn equates to their knowledge of the sector. Client-centric approach equals the organization’s focus on client needs in each phase of the process. It ensures the timely delivery of products.
Need metal injection molding, die casting, or metal stamping? Xometry has access to all the manufacturing capabilities you need, and it is an all-in-one online platform.
The company values everything, be it high-quality parts, cost savings, and product improvement recommendations. Their commitment to reliability means projects will get done on time and on budget.
As an ISO company, HITOP puts quality first. Their strict adherence to international standards means both their injection molds and end products are top-notch.
But if you want cost and global, HITOP Industrial might be the way to go. Their quality and innovation, combined with competitive pricing, make them a contender.
Founded in 1984, Fathom Digital Manufacturing has grown from a traditional manufacturer to a leading on-demand digital manufacturing platform.
We’ll look at their experience, niches, and what sets them apart. Whether you’re looking for a partner for your next project or just interested in plastic molding, this is for you.
HITOP Industrial was founded in 2002 and is now an injection molding big gun. They have the people and services – mold design, creation, prototyping, and production of injection molded parts.
Remedies: It is best to use an automated system that replenishes material in the hopper as it is used. That way the machine will never run out of plastic. If manual systems are utilized instead, the employee in charge must understand the importance of keeping the hopper filled. Alarm units can be used to emit an audible signal when the material in the hopper reaches a preset level.
Founded in 1982, Bennett Plastics is your go-to custom plastic injection molder in the NY area. Their 36,000 sq. ft. facility in Paterson, NJ, has state-of-the-art equipment. It also has a team of experts to get the job done.
GETTING A QUOTE WITH LK-MOULD IS FREE AND SIMPLE.
FIND MORE OF OUR SERVICES:
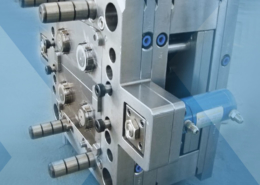
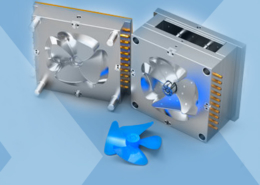
Plastic Molding

Rapid Prototyping
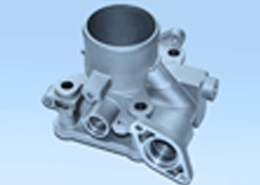
Pressure Die Casting
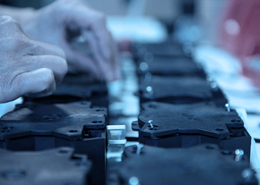
Parts Assembly
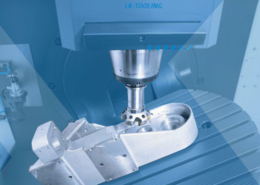