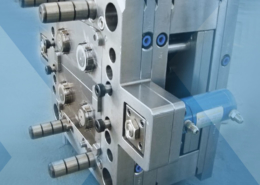
Prototype Injection Molding: When and Why To Use It. - prototype injection
Author:gly Date: 2024-10-15
Polyethylene is an extremely common type of the plastic, and its properties can vary based on a chosen density. It is used for things like food packaging and trash bags, though those applications are not likely injection molded. When it comes to injection molding, polyethylene is used to make things such as toys, housewares, and hard cases such as some toolkits and lunchboxes. It is a cheap and tough plastic with a wide range of options, but with less temperature resistance and can be harder to mold in intricate designs.
Through UnitedHealthcare, UMR creates and publishes the Machine-Readable Files on behalf of Crescent Industries, Inc. To link to the Machine-Readable Files, please click on the URL provided: https://transparency-in-coverage.uhc.com/
Another very commonly used type of plastic, polypropylene has numerous applications. It is hard, but also keeps its shape well, and can even be folded many times without breaking. An example of this would be the plastic cap on a condiment bottle that folds open to access a pour spout. It is food-safe and heat-resistant, but not flame resistant. It also sees use in other items such as containers and packaging, tools, toys, or even textile fabric. PP is highly recyclable.
Do you need design-for-manufacturing (DFM) assistance? Or, are you ready for production? We have a full suite of services to offer and a lifetime mold guarantee.
Due to its crystalline structure, polyoxymethylene sports impressive rigidity and resistance to friction. This makes it ideal for many engineering applications such as gears, bushings, and pulley wheels. POM is also used to make parts for mechanical systems in cars, locks, and firearms, or for stiff parts such as knife handles or eyeglass frames. It resists water and oils, but not fire or UV light.
Crescent started by designing and building End-Of-Arm-Tools (EOAT) for each pf the four injection molds. We than use a quick change feature for each EOAT, Allowing easy and accurate switching back and forth during tooling changes.
At Rex Plastics, we can create custom injection-molded parts out of whatever types of plastic are best for your product. Not only that, but we also offer mold making, prototyping, pad printing, and many other services for startups and OEMs. Reach out to us for a quote today!
When it comes to injection molding polystyrene, there are two types of plastic that are variants of this resin: high impact (HIPS), and general purpose (GPPS). GPPS is more brittle, and therefore can break more easily. Both are lightweight and inexpensive, and resist water as well as radiation. This is useful in medical equipment, since it is often sterilized with gamma rays. HIPS is also in products such as car panels, gasoline tanks, drinking cups and many consumer products such as computer housings. While GPPS is in disposable cups and utensils, rigid packaging, petri dishes and more. A variant of PS is also used to make styrofoam, but this is not injection molded. PS is flammable and degrades with UV light and some chemicals.
Polycarbonate is the strongest plastic for injection molding. Its toughness and moldability makes it useful in engineering applications, and its transparency makes it a stronger alternative to glass.
Polyethylene is the most common type due to it being a low-cost material with many varieties. You can find polyethylene in food packaging, water bottles, bags, housewares, and many more products.
Crescent purchased their new cobot specifically to remove the molded tubs from the mold and place them on conveyor for packaging.
TPU is actually a type of TPE, but is used so often that a distinction is made. When injection molded, it is much more durable than typical TPE, offering greater resistance to things like temperature, chemicals, abbraison, wear and tear. However, it is harder and less flexible, and more expensive. Manufacturers use TPU for products like phone cases, power tools, drive belts, and caster wheels.
Polycarbonate is another clear plastic like acrylic, but it is much stronger. It is stiffer, more durable, and can withstand a wider range of temperatures. This allows manufacturers to use PC in a variety of applications, such as eyewear lenses, greenhouses, vehicle headlight covers, medical devices, LED lights, and clear tubing. It is also a glass substitute like acrylic, and while it is tougher, it is more expensive.
It’s easy to get confused by the many types of plastic for injection molding that exist. There are many options for what to use in a plastic product, but by becoming familiar with the types of plastic you can ensure you are using what is best for the job.
Acrylic is a lightweight, shatter-resistant plastic also known as plexiglass. Since it is transparent and can withstand weathering effects like sunlight, heat, and rain, manufacturers often use acrylic as an alternative to glass. However, it is not good for bearing too much weight. Also, grease or oils can stain acrylic easily. Acrylic is mostly in windows, display cases, solar panels, light fixtures, and other clear applications.
Nylon is a polyamide that offers very high resistance to friction, abrasion and heat. This makes it ideal for mechanical applications such as gears, bushings and bearings, and other parts that see a lot of movement and friction. However, it does not do well with water. It also isn’t naturally flame-resistant but can be made fire retardant.
Acrylonitrile butadiene styrene, or ABS, is one of the more tough, inexpensive types of plastic. It resists impact, scratching and staining, but does not do well under sunlight or weathering. Due to this it is often seen in products like computer keyboards, plastic toys, wall socket covering plates, and interior car parts.
To create plastic parts, manufacturers use a process called plastic injection molding. Plastic injection molding involves injecting molten plastic into a mold to form the product. The plastic then cools in the shape of the product, creating the final product. Once you understand what plastic injection molding is, you can then look into the types of plastic it uses.
Discover the countless benefits of partnering with us for all your injection molding manufacturing needs and let us show you why we are the perfect match for your business.
For over half a century, Crescent Industries has been leading the charge in providing top-tier medical injection molding solutions to the ever-evolving medical, pharmaceutical, and dental industries. Starting with diagnostic well plates, we've expanded our expertise to include Class I, II, and III medical devices and components, utilizing a wide range of medical-grade resins. Our state-of-the-art machines, automated quality inspection equipment, and scientifically-backed molding processes guarantee that YOU can rely on our services with confidence. And if that wasn't enough, we offer ISO 7 cleanroom molding, assembly, and packaging services to provide you with a complete solution for your medical products. With complete quality control and inspection, including IQ, OQ, PQ validations, and lot traceability, we uphold the critical medical quality standards required for plastic injection molding medical parts. Trust us to bring your medical device projects to life!
TPE is a blend of various hard and soft components to achieve a wide range of flexibility, and therefore has some shared properties of rubber. This includes its elasticity, which makes it useful in footwear, seals, tubes and valves. Some of these applications include medical products like catheters or breathing devices. While it usually returns to its original shape, it can wear out with continued use and begins to lose this property under high heat exposure. It is also more expensive compared to other types of plastic.
GETTING A QUOTE WITH LK-MOULD IS FREE AND SIMPLE.
FIND MORE OF OUR SERVICES:
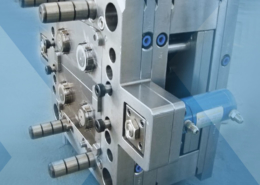
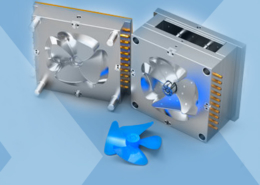
Plastic Molding

Rapid Prototyping
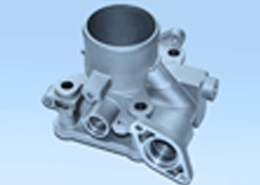
Pressure Die Casting
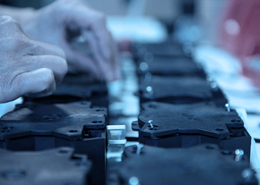
Parts Assembly
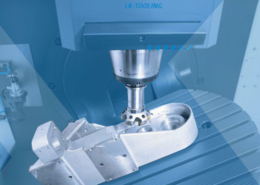