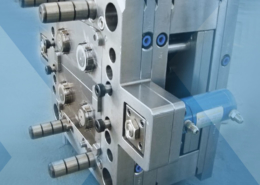
Prototype Injection Molding | Custom Plastic Manufacturing - prototype plastic m
Author:gly Date: 2024-10-15
The medical industry has found a steadfast ally in injection moulding. Elia Guidorzi, international marketing executive at Tecni Waterjet discusses how this technique plays a crucial role in healthcare advancements.
Keyflex manufactures parts and tooling for a wide range of thermoplastic materials such as Polycarbonate, ABS, Polyester and blends. Our expertise means that we are able to advise which material is best suited to your requirements. Over-moulding with TPR gives a rubber feel and impact resistance while our high quality precision parts also have a tight tolerance.
At Keyflex, we understand that each project is unique and requires a tailored approach. Our plastic injection moulding solutions are designed to meet the specific needs of our clients, providing them with the flexibility and reliability they need to achieve their goals. Whether you're looking for a one-of-a-kind solution or need to order in bulk, we have the expertise and resources to meet your needs. Browse our website today to learn more about our plastic injection moulding services and how we can help you bring your ideas to life
These include the intended use, the environment in which the device will operate, and the complexities of human anatomy.
The choice of materials in injection moulding isn’t arbitrary. It requires a careful balancing act between functionality, safety, and cost.
Delving into the specifics of injection moulding reveals a complex yet elegant process. It's a ballet of machinery, materials, and meticulous control, choreographed to produce precision medical devices.
All plastic injection moulding items come in a wide range of colour options including most Pantone colours or silver-plating for a chrome look. Like all our products, plastic moulding can be created for a wide range of flexible designs and we can accept IGES, STEP, PARASOLID and other 3D formats or we can design the part to suit your requirements. When designing a keypad and plastic housing for your product, the ability to have the tooling and production of both parts done in one production plant eliminates problems created when one part does not fit correctly with the other, as the parts are carefully checked together during production, ensuring correct operation in the finished product.
1. Draft Angle2. Undercut3. Wall Thickness (too thick or too thin)4. Sharp Steel5. Draft angle of shut off area, the texture6. Shrinkage7. Miscellaneous Issues
Keyflex is a leading provider of high-quality plastic injection moulding solutions, offering a range of customised services for a variety of industries. Our team of experts in plastic moulding technology utilise state-of-the-art equipment and technology to ensure that each product is manufactured to the highest standards of quality and performance.
Its roots stretch back to the late 19th century, evolving from producing combs and buttons to intricate medical components. This journey has been marked by continuous refinement and adaptation, mirroring the medical field's own evolution.
Keyflex contact information: Australia Head OfficeAddress: U4/ 15 Rosslyn Street, West Leederville Western Australia 6007Phone: +61 (8) 9388 7366Email: sales@keyflex.com.auKeyflex contact information: Hong Kong office502 Golden Gate Commercial Building 136-138 Austin Road KowloonPhone: +852 8120 7299Email: info@keyflex.com.hk
One of the key components of our plastic injection moulding process is our commitment to exceptional tooling. Our in-house tooling capabilities include the design, manufacturing, and maintenance of moulds, ensuring that each product is made to precise specifications. Our tooling is designed to be durable and efficient, reducing production time and improving the overall quality of each product.
In an industry where sterility is paramount, injection moulding rises to the occasion, employing stringent sterilisation protocols.
The future of injection moulding in medical applications is bright, fuelled by relentless innovation and technological advancements.
The industry is making strides towards sustainability, reducing its environmental footprint while maintaining product quality.
Injection moulding, at its core, is the art of crafting objects by injecting molten material into a mould. It's akin to a modern-day alchemy where raw plastics transform into life-saving devices.
Injection moulding in medical device manufacturing isn't just a process; it's a pillar of modern medicine. Its role, often understated, is undeniably critical, shaping the future of healthcare one device at a time. As technology advances, so will the capabilities of injection moulding, promising even more innovative and life-changing medical devices.
Selecting an injection moulding services partner is a decision that echoes through every device produced, impacting countless lives.
Quality control is the guardian angel of injection moulding, ensuring each product meets the highest standards of safety and efficacy.
GETTING A QUOTE WITH LK-MOULD IS FREE AND SIMPLE.
FIND MORE OF OUR SERVICES:
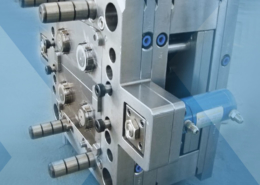
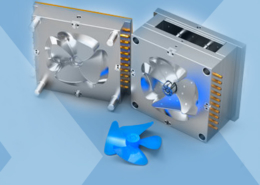
Plastic Molding

Rapid Prototyping
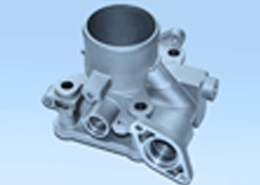
Pressure Die Casting
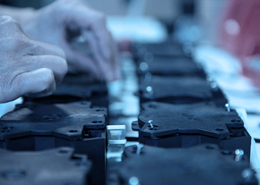
Parts Assembly
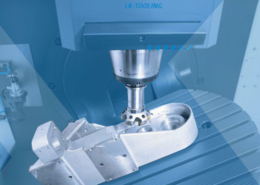