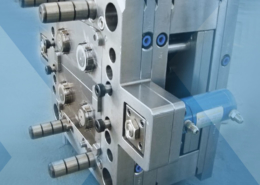
Prototype Injection Molding - prototype plastic molding
Author:gly Date: 2024-10-15
Get 7-day standard lead times on simple parts between 0.5 in. x 0.5 in. and 4 in. x 3 in. Upload your part to see if it’s eligible.
The clamping force of the machine should be greater than the clamping force. For the sake of safety, the clamping force of the machine usually needs to be greater than 1.17 times of the clamping force.
Today, with the internationalization of the market and the diversification of customer needs, our company has always adhered to the attitude of taking the forming site as the starting point, relying on the professional technical strength accumulated since the establishment of the company, and adopting the one-to-one implementation strategy to solve various problems with customers. .
Neither overmolding nor insert molding is restricted in their use to any particular industry or product type. Because both methods are so useful and adaptable, new practical applications are being found all the time that take advantage of their benefits. Here are a few examples:
Milacron is a leading manufacturer of plastic injection molding machines and is a global leader in the manufacture, distribution and service of highly engineered and custom systems in the plastics and processing industries, with a full portfolio of injection molding and extrusion equipment . Milacron maintains a strong market position and maintains leadership in process control systems, maintenance, repair and operational supplies for plastics processing equipment. Milacron provides customers with highly customized equipment, components and services throughout the life cycle of their plastics processing technology systems.
Sumitomo (SHI) Demag Plastics Machinery North America, Inc. is part of a global group of companies dedicated to helping plastics processors compete more effectively in the global marketplace. Sumitomo (SHI) Demag and its Japanese parent company, Sumitomo Heavy Industries (SHI), are one of the specialized manufacturers of high-precision, high-performance plastic injection molding machines with annual sales of more than 5,000 units. The world's largest manufacturer of IM machines. Its global injection molding machine development and production network consists of four factories in Japan, Germany and China, with more than 3,000 employees.
There is no doubt that investment in injection molding machines is expensive and needs to be carefully considered. If you are looking for a suitable plastic injection molding machine manufacturer, you can look to us at Log Machine or a Chinese injection molding machine manufacturer, because Chinese plastic injection molding machines provide competitive prices while ensuring high quality. Investing in the right injection molding machine will pay off.
After getting the above information, you can follow the steps below to choose a suitable plastic injection molding machine
Overmolding also offers more opportunities to be creative by applying colorful designs to improve the appearance of the part as well as its performance.
Inserts should be used whenever a plastic case needs to be occasionally opened for service and then locked tight again, such as when performing routine maintenance or changing batteries. They cost a little more but that cost is offset by making a much more durable end product.
Injection-molded parts are an indispensable part of modern production and life, occupying a very large share in the plastics processing industry. A high-end injection molding machine is very important due to its complexity, accuracy, manufacturing speed, etc.
Overmolding starts with a base substrate, on top of which a relatively softer TPE or TPU material is bonded. The base can be metal or plastic, although, in this article, we will focus on plastic applications primarily.
If the substrate is a plastic base, then it’s customary to mold it in the same production cycle. This is done because it’s more cost-effective to make the entire finished piece at one time, rather than paying to transport and store semi-finished goods. But the more important reason is that the elastomer will adhere much better to a still-warm, semi-cured, and “sticky” substrate.
The opening and closing stroke should be at least twice the height of the finished product in the opening and closing direction, and should include the length of the vertical runner; the holding stroke should be sufficient to eject the finished product.
Finished weight and number of cavities are used to determine the required "shot volume" and to select the appropriate "screw diameter".
With world-class "high cycle performance" as the core, through years of experience training, stronger and more evolved "long-life design" and "precise and stable molding" have been realized. In addition, it combines "advanced intelligence" with a new controller that is extremely easy to use. We respond to the diverse needs of various molding sites and contribute to improving productivity.
Headquartered in Austria and with 9 locations worldwide, ENGEL is the world's leading manufacturer of plastic injection molding machines. Besides machine building, it also offers a wide range of services. The company's main products include system solutions, electric, hydraulic and vertical injection molding machines, used machinery, control units, robots, process stabilization mechanisms, etc. Engel promises clamping forces of between 280 kN and 55,000 kN for its machines.
And overmolding adds cushioning and shock absorption to many common household items that might protect users from accidental injury.
This is just a partial overview of insert molding and overmolding. Are they the right solutions for you? Not sure how to apply them to your next project? Just contact our technical experts and we can offer helpful advice about how to get the best results from both processes.
The electric press, also known as Electric Machine Technology (EMT), reduces operation costs by cutting energy consumption and also addresses some of the environmental concerns surrounding the hydraulic press. Electric presses have been shown to be quieter, faster, and have a higher accuracy, however the machines are more expensive.
The projected area of ââthe finished product in the mold opening and closing direction is derived from the overall dimensions of the finished product.
The width and height of the mold must conform to the minimum mold size recommended by the injection molding machine. Too small is not acceptable.
In this case, it may be necessary to check whether the injection volume and injection speed of the machine are sufficient, whether it needs to be equipped with an accumulator, closed-loop control, etc. Screws that can provide higher injection pressures generally have lower injection speeds, and conversely, screws that can provide lower injection pressures generally have higher injection speeds. Therefore, when selecting the screw diameter, the injection volume, injection pressure and injection speed (injection speed) should be comprehensively considered and weighed.
You should consider using insert molding for a few main reasons. The first is that your product application needs strong mechanical fittings to hold two or more parts together, typically for an enclosure or housing. Threaded nutserts are great for this but there are many types of snap connectors as well.
Once the base cools and is semi-hardened, the mold is then rotated to a new position and connected to a separate nozzle, gate, and runner system. The remaining void of the mold tool cavity is filled with TPE or TPU elastomer, creating the overmold that bonds to the substrate.
The first conventional injection cycle forms the substrate, using a standard thermoforming resin. This resin fills the gate, runner, and cavity system of only one part of the mold, while the section representing the overmold is blocked.
When calculating the weight of the finished product, the number of cavities (how many cavities are in the mold) should be considered; for stability, the injection volume should be greater than 1.35 times the weight of the finished product, that is, the weight of the finished product should be within 75% of the injection volume.
Husky is a well-known manufacturer of plastic injection molding machines and the largest brand supplier of injection molding equipment and services to the plastics industry. The Husky team of more than 4,300 dedicated engineers, designers, innovators, materials and software experts around the world is focused on creating success and profitability for our customers in more than 140 countries.
Haitian is a leading plastic injection molding machine manufacturer in China. Haitian International Holdings Limited has accumulated more than five years of basic technical experience in the production of "Haitian" brand injection molding machines, and reached a new milestone in the company's history when it was listed on the stock exchange. The advanced corporate structure thus brings a crucial step towards the decisive globalization of the brand. The main focus of the Haitian brand is the development and production of standard injection molding machines for the mass production market. In this area, we create a vital competitive advantage for our customers through commercial efficiency, reliable machine design, extreme reliability and comprehensive support.
To get the best results from this process, product developers should be aware of the following limitations and potential disadvantages.
There are many different types of injection molding machines, and choosing the right type can bring greater benefits to your business.
Fanuc is a well-known CNC solution provider and plastic injection molding machine manufacturer. Teams of automation professionals work in customer service, engineering, finance, human resources, IT, logistics, operations, manufacturing, product development, sales and marketing, and training.
Hydraulic presses have historically been the only option available to molders until Nissei Plastic Industrial Co., LTD introduced the first all-electric injection molding machine in 1983.
Get 7-day standard lead times on simple parts between 0.5 in. x 0.5 in. and 4 in. x 3 in. Upload your part to see if it’s eligible.
Clamping force = the projected area of ââthe finished product in the opening and closing direction (cm2) × the number of cavities × the pressure in the mold (kg/cm2).
Now, if that design logic is applied to a fleet of aircraft or millions of automobiles on an assembly line, then the reduction in weight and cost becomes substantial.
In this article, we discuss insert molding and overmolding, the advantages of each, and the applications they’re best suited for. We hope these manufacturing insights, along with useful design tips, will help you get great results on your next plastic injection molding project.
While there are many advantages to insert molding, there are some potential drawbacks that designers should be aware of.
Hydraulic machines, although not nearly as precise, are the predominant type in most of the world, with the exception of Japan.
In this video, Gordon Styles, the founder and President of Star Rapid, goes into greater detail explaining how these processes work, and he gives examples of each. Be sure to check it out for more useful information.
The process is not limited to just two materials, and can theoretically be expanded to include an indefinite number of additional overmolds. However, in practice, more than two becomes increasingly complex and expensive.
The width and height of the mold should be smaller than or at least one side should be smaller than the large column spacing; the width and height of the mold should preferably be within the range of the mold tray size; the thickness of the mold should be between the mold thickness of the plastic injection molding machine.
Arburg is a German mechanical engineering company and a world-renowned manufacturer of injection molding machines. Owned by the Hehl and Keinath families, it ranks among the global industry leaders with its electric, hybrid and hydraulic plastic injection molding machines, turnkey systems and its industrial additive manufacturing systems.
Overmolding is a special form of plastic injection molding. Unlike conventional molding, where a finished product is made in one cycle, overmolding requires at least one additional injection cycle using a dissimilar material. This method is also known as 2K overmolding, two-shot molding, or even multiple material molding.
Inserts can be either male or female. Female inserts are used to make circular fittings inside the surrounding plastic. When these types of inserts have internal threads, they’re called nutserts. There are many advantages to using both male and female inserts to enhance a product’s appearance and utility.
Shibaura Machinery is a well-known manufacturer and solutions provider of plastic injection molding machines, Shibaura designs and manufactures industrial machines and solutions to provide customers with optimum productivity and profitability, and to provide excellent service and support to maximize their return on investment . To pursue this goal, conduct business in a responsible and respectful manner, contribute to the industrial base, and help create a high-quality society through the continuous development of innovative technologies with a focus on mechanics, electronics and systems.
Get 7-day standard lead times on simple parts between 0.5 in. x 0.5 in. and 4 in. x 3 in. Upload your part to see if it’s eligible.
Overmolding uses a special type of plastic injection molding tool, one that has a cavity for the substrate portion and another separate cavity representing the overmolded section.
Today, I would like to introduce you to the world's top 10 Plastic injection molding machine manufacturers, hoping to help you.
Ningbo Chuangji Machinery Co., Ltd. is located in Yuyao. Is a professional enterprise engaged in plastic injection molding machinery. Since the official launch of LOG Lange presses in 2007, the company's sales network has spread all over the world. It has established more than 50 dealers in mainland China, in North and South America, the CIS, Southeast Asia, Africa, the Middle East, and even Europe. There are dealers and service outlets in more than 20 overseas countries around the world. The company currently has four injection molding machine bases, covering a total area of more than 70,000 square meters, with an annual production capacity of more than 4,000 units. The company always adheres to the management concept of "focus, professionalism and concentration", and pays great attention to talent construction and technology development. Strong independent research and development capabilities and strict quality supervision system make Lange brand injection molding machines have the characteristics of energy saving, high pressure and high speed, precision and stability.
So far, the specifications of the clamping unit have been preliminarily determined, and the tonnage of the machine has been roughly determined. Next, the following steps must be performed again to confirm which injection unit has a better screw diameter.
Some engineering plastics require higher injection pressure and suitable screw compression ratio design to have better molding effect, so in order to make the finished product injection better, the selection of the screw also needs to consider the required ratio of injection pressure and compression ratio. .
JSW is a leading plastic injection molding machine manufacturer with many years of R&D manufacturing experience and extensive experience in manufacturing large electric injection molding machines ranging from 550 to 3000 metric tons.
Since there are many types of injection molding machines, it is necessary to correctly judge which type of injection molding machine or series should be used to produce the product, such as general thermoplastic or bakelite or PET material, single color, double color, multi-color-color, sandwich or mixed color . In addition, some products require conditions such as high stability (closed circuit), high precision, ultra-high injection speed, high injection pressure or rapid production (multi-circuit), and the appropriate series must also be selected for production.
Usually, the important factors that affect the selection of injection molding machines include molds, products, plastics, molding requirements, etc. Therefore, before making a selection, it is necessary to collect or master such information: such as mold size (width, height, thickness), weight, special design, etc.; type and quantity of plastic used (single raw material or multiple plastics); appearance size ( length, width, height, thickness), weight of injection molded products, etc.; molding requirements, such as quality requirements, production speed, etc.
When the raw material is injected into the mold cavity under high pressure, the clamping force is generated, so the clamping unit of the plastic injection molding machine must provide enough "clamping force" to prevent the mold from opening. The clamping force requirement is calculated as follows.
Which process is right for you depends entirely on your application. Keep in mind that they aren’t mutually exclusive molding methods because they serve different purposes. In fact, it’s not uncommon to find both used on a single product. Think, for example, of a power tool that has overmolded grips on the handle, but that also uses nutserts to bolt the case together.
From the mold size, determine whether the machine's "large column spacing", "mold thickness", "mold minimum size" and "mold tray size" are appropriate to confirm whether the mold can be placed.
Insert molding is used to put a rubber or plastic handle on a metal part, such as you might find on hand tools or kitchen knives. And insert molding is ideal for sealing wires and electrical connectors into permanent plastic housings that block out dust and moisture.
Product developers should consider overmolding in order to improve the grip and texture on parts that need to be held in the hand or to protect the end user against vibration, heat, or electricity. Overmolding is also a great way to permanently bond rubber to metal, as is found on wheels and casters.
Insert molding involves placing a pre-manufactured component, such as a threaded fitting or an electrical contact, onto a mounting pin or other fixture in a plastic injection molding tool. During the molding cycle, thermoforming resin surrounds this insert and solidifies, thereby permanently sealing it into place.
Servo injection molding machines claim to take advantage of the best features of both hydraulic and electric systems, but in actuality use almost the same amount of electricity to operate as an electric injection molding machine depending on the manufacturer.
Since its establishment in 1947, NISSEI is a leading manufacturer of injection molding machines, and has continuously improved its professional and technical characteristics. With the concept of "professional, profound and extensive", it has gradually expanded the industry scope of related technology applications. While paying attention to improving the performance of injection molding machines, it also researches Developed molds, forming support systems, forming processing and other related technologies.
In addition, in many cases, they will be classified by the function or application of the injection molding machine, such as our common PET preform injection molding machine, PVC Pipe injection molding machine, etc. Plastic Injection molding machine manufacturers usually prepare or customize corresponding injection molding solutions for you. You can ask your intended manufacturer in detail.
The mold and finished product should determine whether the "opening stroke" and "clamping stroke" are sufficient to remove the finished product.
Remember that overmolding is rarely used to cover the entire base substrate. Instead, apply overmolding in sections. For each of these, keep in mind these useful design tips:
There are some unique engineering challenges that designers might face when using insert molding. The advantages of added strength and versatility must be weighed against the need for a more careful design for manufacturing review. Here are some useful guidelines to consider:
Headquarters and main manufacturing facilities are located in Canada, with additional manufacturing facilities in the United States, Luxembourg, Switzerland, China and the Czech Republic. In addition, three technical centers in Japan, Luxembourg and Shanghai, as well as a worldwide network of locations.
The company's main business verticals are automotive, packaging, medical, electrical, sports and leisure, toys, construction, etc.
GETTING A QUOTE WITH LK-MOULD IS FREE AND SIMPLE.
FIND MORE OF OUR SERVICES:
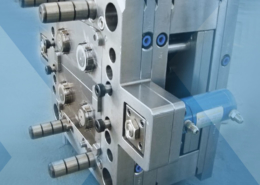
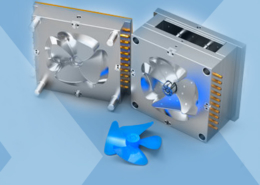
Plastic Molding

Rapid Prototyping
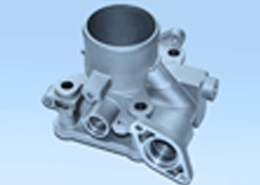
Pressure Die Casting
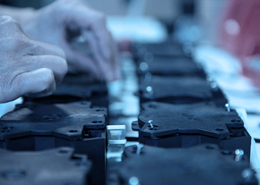
Parts Assembly
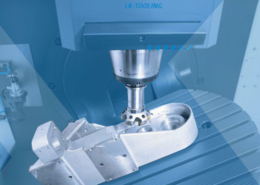