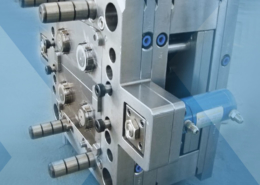
Proses Plastic Injection - Anwar Kholidi Nasution - proses injection molding pla
Author:gly Date: 2024-10-15
PCTFE is derived from replacing all remaining hydrogen atoms on the monomers with fluorine. The resulting material is ideal for pharmaceutical packaging thanks to its excellent strength, impact resistance, and moisture resistance.
There are many other ways in which these basic principles can be applied and in the literature, you will find multiple four and five-letter acronyms for detailed procedures. As I am writing this issue, some very good review articles on this topic have been accepted for publication in Electrophoresis (3, 4). Sensitivity and CE have been very much under discussion in the past years, one of the arguments for reduced sensitivity being the small capillary diameter and therefore the reduced detection path length. As so much can be gained by relatively little effort in the injection procedure, it is important to realise and to stress that detection concentration sensitivity cannot be 1:1 translated to sample concentration sensitivity. The stacking techniques have shown considerable gain over the years and concentration enhancements of 10–1000 times have been achieved.
Injection by applying a voltage is called electrokinetic injection. In electrokinetic injection, the amount injected of a certain sample component depends on the component’s mobility, the capillary diameter, the applied electric field and the injection time. This means that sample components with different mobilities are injected in different amounts . Consequently, electrokinetic injection is a selective or discriminative injection mode and for electrokinetic injection, one cannot say that a certain volume of sample is being injected. The amount of a compound injected can be estimated by:
Chemical resistance is crucial for devices exposed to cleaning agents and bodily fluids, ensuring longevity and reliability. Understanding and utilizing these properties to their best advantage is essential for maximizing device performance in medical applications.
The Two Principles of Injection Sample injection in CE is basically done in two different ways: by pressure difference or by applying a voltage. Injecting by pressure difference is called hydrodynamic injection. The volume of sample injected depends not only on the injection time and pressure, but also on the BGE viscosity, the capillary diameter and length. The sample volume injected can be estimated by:
PVC is derived from substituting a hydrogen atom with chlorine in the ethylene monomers, which reduces its reactivity to nonpolar liquids. It is also transparent and flexible, making it a strong choice for storing glucose and saline solutions.
Industry standards are essential guidelines that ensure end-users are safeguarded from undue risks associated with medical molded products. Regulatory bodies like the EU MDR (Medical Device Regulation) and the U.S. FDA (Food and Drug Administration) categorize medical devices into three classes, each correlating with a distinct level of risk. They include:
Good Injection Practice Summarizing, one can gain significantly in precision and sensitivity if appropriate attention is paid to the injection procedure. Most of the discussed tips and tricks are easily programmed in the method or require very little in the way of sample handling. So except for some time during method development, it is almost for free!
We discussed the significance of a constant electro-osmotic flow and good capillary conditioning for precision in our CE methods. Now we look at the importance of injection settings for precision. We will also have a first look at sample stacking and see that by carefully selecting our sample solvent we can gain sensitivity in our applications.
Medical-grade plastics like polyethylene, polypropylene, PVC, polystyrene, and silicone offer exceptional durability and biocompatibility. Understanding these properties and the material standards for each ensures you produce durable, reliable devices.
Analytical Training Solutions, brought to you by Separation Science, is the leading global portal for fundamentals, best practice, troubleshooting and method development training for chromatographic and mass spectrometric techniques. Comprehensive, self-paced online courses and validated learning provides a unique education resource for analytical chemists. Currently, we offer HPLC training, LC-MS training, GC training and GC-MS training.
In electrokinetic injection, an internal standard with similar mobility behaviour as the analytes of interest can be used to reduce injection variability caused by sample composition variability.
Figure 2: The top trace shows the injection of a standard containing two drug substances (DS 1 and DS 2) and some impurities (Imp a, Imp b and Imp c). The bottom electropherogram shows the injection of an injection solution product containing DS 2 and the impurities spiked in similar amounts as in the standard. The high DS concentration in the product causes migration time shifts and peak broadening (electromigration dispersion) of the later migrating impurities Imp b and Imp c. Imp a is not affected in this system. The broadened, dispersed peaks of Imp b and Imp c are harder to detect and integrate and have lower signal-to noise levels. Lower signal-to-noise levels mean reduced sensitivity. This example demonstrates that method development should preferably be performed with real samples and not just standard solutions.
Sterilization compatibility is also crucial to maintaining the hygiene and safety of medical devices. Injection molded parts must have high heat resistance to withstand various sterilization methods such as autoclaving, gamma radiation, or harsh chemical agents.
Plastic medical products have revolutionized and improved the quality of patient management globally, but not all materials are created equal. Choosing suitable plastic materials for your medical device manufacturing is essential, as it impacts the success and safety of your final product.
Through UnitedHealthcare, UMR creates and publishes the Machine-Readable Files on behalf of Crescent Industries, Inc. To link to the Machine-Readable Files, please click on the URL provided: https://transparency-in-coverage.uhc.com/
The mechanical and chemical attributes of plastics significantly influence the durability and functionality of medical devices. Some important mechanical properties include:
Join us as we explore different types of medical-grade plastics and the critical factors in injection molding material selection.
Sample Stacking Ideally, the injection plug length should be less than 1–2 % of the capillary length. That is if the sample matrix is similar to the BGE. In practice, it is common to make use of stacking mechanisms or online concentration techniques. Stacking reduces the injection bandwidth and increases the sample concentration and with that the sensitivity of the method. In its simplest form, stacking means that the sample is dissolved in a matrix that is at least 10 x less conductive than the BGE, for instance, water or diluted BGE. If dissolving or diluting the sample in water or BGE is not practical, similar effects can be achieved by injecting a water plug before or after the sample plug. When the voltage is applied, the low-conductivity sample zone will have a higher field strength than the BGE. Consequently, the analytes migrate faster until they reach the boundary of the BGE zone. In the more conductive BGE, the field strength is lower and the analytes stack, that is, slow down and concentrate, reducing the initial bandwidth (Figure 3).
For electrokinetic injection, the sample composition affects the ionic strength of the sample. Variable ionic strengths result in variable field strengths during the injection. This means that amount of analyte injected varies from sample vial to sample vial if the matrix is not the same for all samples.
Medical injection molding utilizes various types of plastic materials. Thermoplastics and thermosetting materials are prominent in this field. Thermosetting plastics have high melting points, chemical resistance, and mechanical strength due to the strong covalent bonds between polymer strands. However, these covalent linkages cannot reform once broken, resulting in permanent deformation. These properties make thermosetting plastics useful as adhesives and protective coatings.
Plastics, also known as polymers, consist of repeating monomers forming homopolymers or copolymers. These materials are arranged into linear or branched polymers, resulting in diverse plastics with unique features.
A small sample zone and short injection time reduce band broadening and maintain efficient peaks with high plate numbers. That is why the injection plug length should ideally be less than 1–2 % of the capillary length and why the injection time should be as short as possible. Simultaneously, the injection time is used in modern instruments to correct for pressure or voltage variability during injection. This improves injection volume precision but only works well if the injection time is at least 3 s.
Precise injection pressure differences and prevention of syphoning requires that the liquid levels in the vials are constant and the same. So fill all sample vials to the same levels. The inlet and outlet BGE vials have to be level. Do not put the waste vial at the outlet of the capillary when injecting, as this is probably the vial with the most variable liquid level.
Figure 1: An example of the effect of dipping (blue trace) or not dipping (green trace) the capillary inlet in a clean water vial after sample injection (courtesy of Beckman Coulter). When the capillary was not dipped in water after sample injection, the sample was stuck at the outside of the capillary. This migrated into the capillary after the run was started and the voltage applied, causing the extra sample peaks just after the proper sample peaks. The sample is reduced IgG and the application is the Beckman Coulter CE-SDS kit. This is a CGE protein sizing application comparable with SDS-PAGE. The protein sample is treated with SDS for denaturisation and β-mercaptoethanol for reduction. The original IgG antibody molecule is thus reduced to its heavy chain (HC) and light chain (LC). Also, some non-glycosylated HC (ng-HC) is visible. Because of the denaturisation, all proteins are covered with equal amounts of SDS per amount of protein, shielding the natural charge of the protein. That means that all proteins have the same charge/size ratio. The capillary is filled with SDS-gel buffer which is a linear polymer that through entanglement creates a molecular size sieve and the separation is size-based, just as in SDS-PAGE. Because of the gel, sample injection is electrokinetic (although hydrodynamic injection is also feasible (5)). Because of the unified charge/size ratio, the electrokinetic injection is discriminative, but not between the different proteins. The function of the internal standard (IS), a 10 kDa protein, is for migration time correction. Quantification is by internal normalization (sum corrected peak areas equals 100 %).
As sample injection for both injection modes depends on the capillary diameter and length, make sure to adjust the injection settings when testing different capillary dimensions.
PE consists of ethylene monomer units linked through addition polymerization. Its variants offer distinct mechanical properties suited for various applications:
Thermoplastics also feature weaker intermolecular forces, allowing them to melt and reform multiple times without permanent alteration. The material’s versatility and ability to withstand the remolding processes make it ideal for medical device plastic injection molding.
Should I select hydrodynamic or electrokinetic injection? Well, as usual, it depends. Generally speaking hydrodynamic injection is more precise than electrokinetic injection. However when working with viscous applications, hydrodynamic injection is cumbersome. An example is capillary gel electrophoresis (CGE). In CGE, the capillary is filled with a viscous gel buffer and usually electrokinetic injection is applied. Selectivity can be another reason for choosing electrokinetic injection. For instance if the analytes of interest are selectively injected into the capillary while the sample matrix components have a mobility in the opposite direction and remain in the sample vial. Selective injection also means that the amount injected of faster migrating compounds is bigger than the amount of slower migrating compounds. That is why quantitative analysis after electrokinetic injection requires appropriate calibration. Selective injection also implies that electrokinetic injection changes the composition of the remaining sample. So as a basic rule we can only inject once from a sample vial when applying electrokinetic injection.
To remove excess sample sticking on the outside of the capillary, dip the capillary after injection in a clean water or BGE vial (Figure 1). It is also advantageous to inject a BGE or water plug after sample injection to prevent sample loss by thermal expansion when the high voltage is switched on.
Usability involves factors like handling ease and comfort. Silicone, prized for flexibility and skin comfort, is common in wearable medical devices. Plastic mold technology provides the design flexibility to create intricate and ergonomic designs, enhancing the overall usability of medical devices.
Polypropylene is derived from substituting the ethylene monomer with a methyl group (CH3). It is harder than PE and offers better resistance to moisture and gases, so it's suitable for storing fluid drugs. PP is also autoclavable and chemically robust, expanding its utility for storing sterile drug products.
Even with all these precautions, sample introduction in CE is not as precise as in, e.g., LC. To reduce the effect of injection volume variability further, it is common to use an internal standard (IS). This is especially important when external calibration is used for quantification. For internal calibration (sum of the corrected peak areas equals 100 %) an internal standard is not required. If the function of the internal standard is only to correct for the injection variability of hydrodynamic injections, the IS can be anything that can be detected and does not interfere with the separation at hand.
Selecting the right materials for your medical devices is critical for determining the final product’s performance, safety, and efficacy. Here are a few key factors guiding the intricate injection molding material selection process.
Medical device aesthetics and usability contribute significantly to patient experience and acceptance. Visible prosthetics benefit from appealing, durable molding materials like colorable polycarbonate.
References 1. Capillary Conditioning — The Foundation of Precision in CE, CE Solutions issue 42. The CE capillary, CE Solutions issue 33. Recent advances in enhancing the sensitivity of electrophoresis and electrochromatography in capillaries and microchips (2010 – 2012), MC Breadmore, AI Shallan, HR Rabanes, D Gstoettenmayr, A Syazwani Abdul Keyon, A Gaspar, M Dawod, JP Quirino, (2012) Electrophoresis doi:10.1002/elps.2012003964. Contemporary sample stacking in analytical electrophoresis, A Šlampová, Z Malá, P Pantucková, P Gebauer, P Bocek, (2012) Electrophoresis doi:10.1002/elps.2012003465. Capillary gel electrophoresis for precise protein quantitation, Cianciulli, C., Hahne, T. and Wätzig, H (2012) Electrophoresis doi: 10.1002/elps.201200177
As your partner, Crescent Industries can provide expertise in injection molding manufacturing and uphold ISO standards, ensuring high-quality medical plastic products. Contact us for unparalleled quality, speed, and value in medical injection molding.
Samples and Standards Standards and samples should match in composition. If the standards are simple and clean, low conductive solutions and the samples contain for example lots of highly conductive salts, the resulting electropherograms and peaks can dramatically differ. Even the concentration of the analytes can influence the peak shapes, resolution and migration times of other analytes by electro-migration dispersion phenomena. An example is shown in Figure 2.
Thermoplastics can be hard yet highly flexible. They can resist bending but offer excellent tensile strength that protects them from breaking.
PEEK is celebrated for its unique biomimetic qualities and fatigue resistance. It's commonly used for orthopedic implants and prosthetics.
Also, correction for migration time variability can be a reason for using an internal standard. For example for identification by relative migration times or relative mobilities or for molecular weight or pI determinations of proteins.
Precision: The Details For good precision injection, there are more details we need to pay attention to. As viscosities and therefore injected volumes and amounts can vary 2–3 % per degree Celsius, the samples and capillary should have a constant, precise temperature. Solutions that come from the fridge need some time to attain room temperature or the temperature of the sample carrousel. A way to make sure that all sample and BGE vials have had time to get at a constant temperature is to programme the capillary pre-sequence conditioning (1) as part of the sequence.
Biocompatibility involves assessing how materials interact with living tissues. Medical devices often come into direct and prolonged contact with bodily fluids or tissues, making biocompatibility a top priority.
With the rapid advancements in healthcare, plastic has emerged as the favored material for prototyping crucial medical components:
To adhere to these tight tolerances and standards, injection molders must implement rigorous procedures at every production stage. Some of these standards include:
GETTING A QUOTE WITH LK-MOULD IS FREE AND SIMPLE.
FIND MORE OF OUR SERVICES:
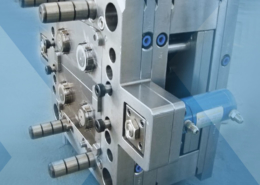
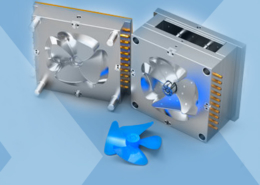
Plastic Molding

Rapid Prototyping
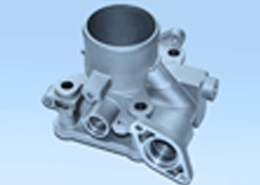
Pressure Die Casting
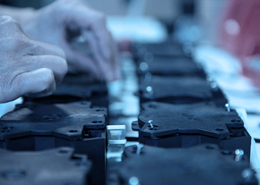
Parts Assembly
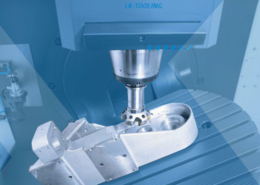