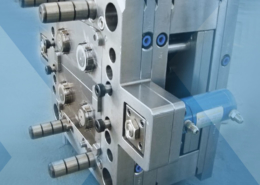
Exploring the Versatility of Products Made by Injection Moulding
Author:gly Date: 2024-06-08
Introduction:
Products made by injection moulding have revolutionized various industries, offering unparalleled versatility, efficiency, and cost-effectiveness. Injection moulding, a manufacturing process wherein molten material is injected into a mould cavity, has become the cornerstone of modern manufacturing. From automotive components to consumer electronics, the applications of injection moulding are vast and diverse, catering to the needs of countless sectors worldwide. This article delves into the intricacies of products manufactured through injection moulding, highlighting their significance and impact on industries and consumers alike.
Advantages of Injection Moulding:
Cost Efficiency:
Injection moulding enables mass production of intricate parts at a fraction of the cost compared to traditional manufacturing methods. The ability to produce high volumes with minimal material waste makes it a preferred choice for companies aiming to optimize production costs without compromising quality.
Precision Engineering:
One of the most remarkable aspects of injection moulding is its ability to create complex geometries with exceptional precision. With advancements in moulding technology and computer-aided design (CAD), manufacturers can achieve intricate shapes and tight tolerances, ensuring consistent quality across production batches.
Fast Turnaround Time:
In today's fast-paced market, speed is paramount. Injection moulding offers rapid production cycles, allowing companies to swiftly respond to changing consumer demands and market trends. From prototyping to full-scale production, the streamlined process of injection moulding minimizes lead times, facilitating quicker product launches and time-to-market advantages.
Applications Across Industries:
Automotive Sector:
Injection moulding plays a pivotal role in the automotive industry, producing components ranging from interior trim panels to exterior body parts. The lightweight yet durable nature of injection-moulded plastics contributes to fuel efficiency and vehicle performance, while also enhancing design flexibility and aesthetic appeal.
Electronics and Consumer Goods:
In the realm of electronics and consumer goods, injection moulding facilitates the production of sleek, ergonomic casings, housings, and enclosures for devices such as smartphones, laptops, and home appliances. The seamless integration of functionalities and the ability to incorporate intricate details make injection-moulded products indispensable in these sectors.
Medical Equipment:
In the medical field, precision and reliability are paramount. Injection moulding delivers sterile, high-quality components for medical devices, equipment, and disposable consumables. From syringes to implantable devices, the stringent manufacturing standards upheld by injection moulding ensure compliance with regulatory requirements and patient safety.
Sustainability and Environmental Impact:
Material Innovation:
Advancements in material science have led to the development of eco-friendly polymers and biodegradable resins suitable for injection moulding. By adopting sustainable materials, manufacturers can minimize environmental footprint and address growing concerns about plastic waste and pollution.
Energy Efficiency:
Injection moulding processes have become increasingly energy-efficient, thanks to innovations such as electric injection moulding machines and energy-saving technologies. By optimizing energy consumption during production, manufacturers can reduce carbon emissions and contribute to a greener, more sustainable future.
Waste Reduction:
The precise nature of injection moulding results in minimal material wastage during production. Additionally, the ability to recycle and reuse scrap materials further reduces the environmental impact associated with manufacturing, fostering a circular economy model that prioritizes resource efficiency.
Conclusion:
In conclusion, products made by injection moulding represent a cornerstone of modern manufacturing, offering unparalleled versatility, precision, and efficiency across various industries. From automotive components to medical devices, the applications of injection moulding are vast and diverse, catering to the evolving needs of consumers and businesses worldwide. Embracing sustainable practices and technological innovations, the injection moulding industry continues to drive progress towards a more efficient, eco-friendly future. As we look ahead, further research and development in materials science and process optimization hold the key to unlocking new potentials and pushing the boundaries of what's possible with injection moulding technology.
GETTING A QUOTE WITH LK-MOULD IS FREE AND SIMPLE.
FIND MORE OF OUR SERVICES:
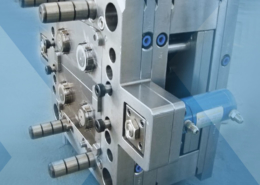
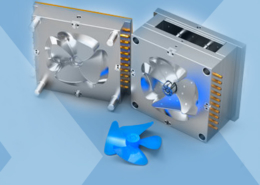
Plastic Molding

Rapid Prototyping
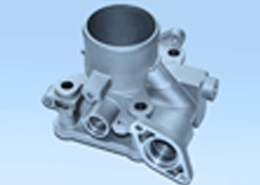
Pressure Die Casting
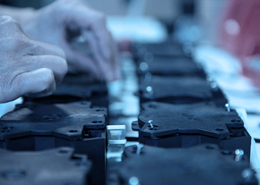
Parts Assembly
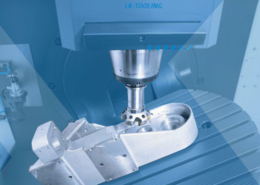