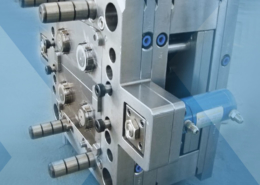
Proper Procedure for Collecting Short Shots - short shot molding
Author:gly Date: 2024-10-15
Flow restrictions, hesitation of flow, and inadequate venting are all common short-shot defects due to inadequate mold design. Flow restrictions often come from the positioning, dimensions of runners and their gates, and how the molten plastic is poured into the mold.
Consult Flying Tiger today if your business is looking for a partner to co-create reliable, high-quality manufacturing outputs.
With many accumulated years of experience with numerous domestic and foreign clients, Flying Tiger is confident in assisting corporate customers in quickly identifying the cause of short shots and other injection molding defects, thereby assisting in cutting down on resource waste and boosting product yield.
For instance, an oversized machine may have trouble controlling pressure if the shot size is less than 25% of its capacity, whereas an undersized machine will not have enough pressure or ram speed. Meanwhile, the barrel and mold wall should be heated to prevent the molded plastic from cooling too quickly.
Additionally, because the filling speed is excessively high, chances are that there is insufficient time to release the air via the separating surface.
Overall, several factors can lead to the occurrence of short-shot defects, and they all have mutually limiting and influencing effects. Manufacturers must consider how these factors relate to one another, in order to devise a solution to reduce and correct short-shot defects. Note that It is often an ongoing process of monitoring and reviewing.
Adreco Plastics has built up an enviable reputation for quality and durability when it comes to plastic injection moulding for the medical and healthcare sectors. Our products are being used in a wide range of applications in hospitals, clinics, doctors’ surgeries, pharmacies and healthcare settings in the UK and abroad.
Therefore, beyond the choosing material, better control of mold and melt temperatures also aids in enhancing plastic flow. Flying Tiger offers a range of mold temperature controllers that help you achieve just that.
Another potential reason is that the vacuum condition is not suitable for molds—Molds require a place for displaced air to escape, or they will develop air traps or poor venting.
A "short shot," as the name suggests, occurs when the mold-forming filling stops before the mold chamber is fully filled with the melt, leaving holes or thin sections and producing a defective product.
Our team of highly knowledgeable engineers and manufacturers have honed their skills and sharpened their understanding through close liaison with R&D experts and medical device pioneers to help them learn new ways to deliver medical treatments using the advanced plastic injection moulding techniques that Adreco Plastics has become renowned for.
Our automotive customers have come to rely on our ability to deliver high-quality, low-cost plastic injection moulded parts, tools and components for vehicles across the UK and beyond. However, we don’t just work in this single sector. We are also a leading supplier to defence and security, agriculture, construction, retail, automotive, packaging and lighting.
Poor venting happens when air is trapped during filling the cavity, creating counterpressure. When the melt is first injected into the hollow, under most circumstances, it immediately seals the cavity, trapping air in the remaining local spaces.
All our products are designed and manufactured to exacting industry standards and are created using top quality plastics and polymers to ensure premium performance. We have been accredited with ISO 9001 since 2006 and we make it our business to stay up-to-date with all the latest advances in thermoplastic technology. This dedication to quality is reflected in the versatility and durability of our work.
The production line might have a resin with a high viscosity measured by the Melt Flow Index (MFI), depending on the chosen material. MFI is a good starting point, even though it may not tell the complete story since there are two other factors of concern that may also be involved.
Our quality standards are exacting and everything that we produce is subjected to rigorous safety testing and quality control.
These holes frequently appear around the borders of the finished product or in areas where the mold wall is typically thin—these areas are the last places a mold would commonly fill.
Manufacturers can immediately notice that the choice of material affects the flow or movement of the molten plastic inside the mold chamber in the mold cavity because it is a recurring factor in many problems.
Overall, it is crucial to comprehend the various varieties of plastic injection molding equipment and how varying sizes and types might be beneficial.
Like any production process, plastic injection molding manufacturing can have problems and faults. Short shots, often known as "shorts," are one of the most typical quality concerns when the final product is incomplete because the mold did not entirely fill. This article will examine the most frequent causes of this issue and how plastics manufacturers can troubleshoot short shots to maintain high-quality and lean production.
To find out how our medical moulding services can help you and your business, or to request a quote for medical tooling and moulding, please get in touch.
Demand for top-quality medical injection moulding components and tools for the medical sector is growing. Innovations and advancements in technology lead to the need for more sophisticated medical tools and devices.
The secret to effective manufacturing and preventing either flow or pressure concerns is to match the right part with the proper molding machine.
Our moulding and tooling teams can produce any plastic medical device, instrument, or component required—these range from the smallest of widgets to large-scale, complex assemblies. We offer a complete manufacturing process tailored to our medical sector customers’ exact needs and delivered across three shifts working round the clock, five days a week.
In plastic injection molding, a flow hesitation occurs when the flow slows down or stops due to variations in mold thickness. Inconsistent mold thickness causes the flow range of the melt to be too broad and its flow resistance to be excessive.
The most frequent cause of failure to fill the mold is the appearance of something that interferes with the flow, and one of the leading candidates for flow issues is the type of plastic polymer itself.
The imbalanced flow in each cavity of a multi-cavity mold can generate local short shots. But when the injection molding machine's capacity is adequate, this defect is primarily brought on by the uneven flow in each gate or the uneven distribution of the mold cavities.
Nozzles, sprues, runners, gates, and thin product walls are among the parts that could obstruct melt flow. By raising the nozzle's diameter and temperature, besides utilizing a nozzle with a low flow resistance, the flow resistance of the nozzle can drop to the desired level.
Short shots are one of the most frequent problems with plastic injection molding. There are numerous causes of them, but the primary ones are improper injection pressure and speed, including uncontrolled pressure loss brought on by resistance.
Therefore, it is squeezed instead, leaving some partially empty spaces in the cavity and shortening the shot of the molded item. To remove the air, the process must have vents built or ejection pins installed.
There are a variety of tools, procedures, and materials available for manufacturers to avoid short-shot defects. Four of the most tried-and-tested remedies are listed below:
GETTING A QUOTE WITH LK-MOULD IS FREE AND SIMPLE.
FIND MORE OF OUR SERVICES:
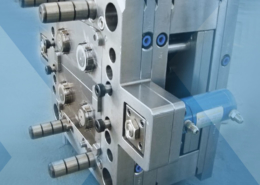
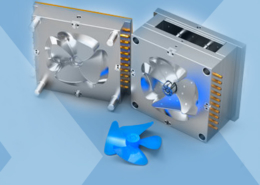
Plastic Molding

Rapid Prototyping
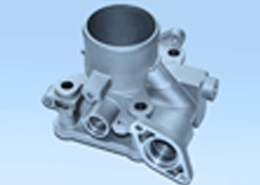
Pressure Die Casting
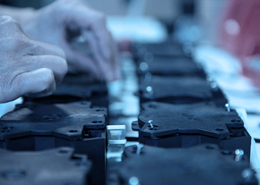
Parts Assembly
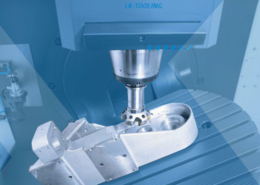