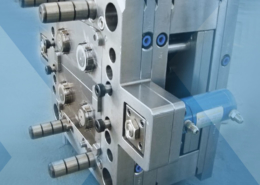
Product & Part Manufacturing | Australia's Leading ... - injection moulding manu
Author:gly Date: 2024-10-15
Draft angles help with removing the part from the mold without damaging it. Shrinkage happens as the plastic cools, so you need to account for it in the design to make sure the final product is the right size.
HITOP is committed to assisting customers by offering a comprehensive one-stop solution, encompassing product design enhancement, initial sample creation, mold fabrication, injection molding, and product assembly.
We are committed to helping you elevate quality standards, fostering enterprise growth, and actualizing your internationalization strategy.
They’ll be easier to release from the mold, reducing the chances of damage during production. So, taking the time to polish and finish the mold properly really pays off in the end.
Before jumping into full production, it’s crucial to test the mold to make sure everything works as planned. This step, often called mold testing or tool sampling, involves running a few cycles with the mold to produce sample parts.
You can also read our Ultimate Guide to Injection Molding to read about injection molding technology or view our plastic injection molding services page.
Other hard plastics used in molding include ABS (Acrylonitrile Butadiene Styrene) and POM (Polyoxymethylene), which are known for their durability and precision in finished parts.
Making adjustments now ensures that when you start full production, the mold will produce high-quality parts consistently. Testing might take some extra time, but it saves you from bigger headaches down the road.
Side actions are beneficial because they increase the options for what part geometries your part can have. Learn which type is best for your project.
Precision is everything here. Even the smallest mistake can lead to problems later on, like parts that don’t fit together or look the way they should.
Lifters create and release internal undercut features. Similar to slides, lifters move into place via a cam as the tool closes and move away as the tool opens.
When side actions are unavoidable, it is important to understand which type of side action your manufacturer recommends for your part, as each has different cost impacts on your tooling costs. The following table describes the different types and their use cases.
These complex plastic molds are durable and can produce highly detailed parts. However, it’s essential to properly prepare the mold surface (e.g., through adequate release agents) to ensure the resin does not stick to the mold and can be demolded easily.
The injection molding process itself is straightforward: molten plastic is injected into the mold under high pressure. The plastic fills the mold cavity, cools, and hardens into the desired shape.
That’s why it’s so important to keep a close eye on the machining process. Regularly checking the work as it progresses helps catch any issues early so they can be fixed before they become bigger problems.
Yes, you can make your own plastic molds for small-scale projects or prototyping. The process typically involves selecting a suitable molding material (such as silicone for flexible molds or thermosetting plastics for rigid molds), designing the mold based on the desired shape of the plastic part, and then using techniques like casting or machining to create the mold.
When picking a material, think about how strong the mold needs to be, how much it will cost, and how many parts you plan to produce. If you’re making thousands of parts, steel might be the better choice because it holds up under repeated use.
CNC machining is where your mold starts to take shape. This step is all about using precision tools to carve out the mold from the chosen material, whether it’s steel or aluminum.
An unscrewing action is an automated motor or manual hand screwing that creates screw or threaded features. These actions prevent damage to the threads with careful unwinding between cycles.
When designing, it’s important to think about things like parting lines, draft angles, and shrinkage. Parting lines are where the mold separates, and you want to make sure they’re placed in a way that doesn’t affect the look or function of the part.
The quality of the final plastic part depends a lot on how well the mold is finished. If the mold is polished correctly, the plastic parts will look better and perform better, too.
Injection molding side actions are inserts (sometimes referred to as âfeaturesâ) added to the mold in order to create undercut geometry. Undercut features are perpendicular to the main parting line and cannot be produced with a straight-pull mold, or in other words, by pulling apart the two halves of the mold and ejecting the part. When side actions are added to the mold, they allow material to flow around them to form the undercut feature. The side actions must then be removed manually or automatically to allow part ejection.Â
Repetition is key in mass production. The injection molding machine runs cycle after cycle, producing hundreds or thousands of identical parts.
Collapsible cores are mechanisms that release a circular undercut feature in a method similar to a lifter. These allow the actions to collapse inward, providing clearance for part ejection.
In short, CNC machining turns your design into reality, and making sure it’s done right is key to producing a mold that works perfectly.
It should also be noted that because side actions do not follow the general tool direction, undercut features require draft angles specific to the actionâs movement. For more design strategies, download our Injection Molding Design Guide.
Side actions are beneficial because they increase the options for what part geometries your part can have. However, side actions can dramatically increase molding production costs, so it is helpful to consider whether you need them or whether you can avoid them by designing slot features.
Hand loads are used for prototype and low-volume tooling as a cheaper alternative to automated slides and lifters. Hand loads can be adaptable to different part configurations in one tool.
Hand-loaded cores are substitutes for slides or lifters, and are manually placed features which are molded around and then manually removed from the part. These are replaced each cycle.
Getting the design right from the start makes the rest of the process smoother and helps avoid costly mistakes later on.
During testing, you’re looking for any defects or issues in the parts, like warping, incomplete fills, or surface imperfections. If you spot any problems, this is the time to fix them.
The first step in making a hard plastic mold is designing it carefully. A detailed design is crucial because every little detail affects the final product. This is where CAD (Computer-Aided Design) software comes in handy.
For DIY enthusiasts or those looking to prototype designs, creating your own molds can be a cost-effective solution. However, for mass production or highly detailed parts, professional mold-making might be required.
Choosing the right material for your mold is a big deal. Common options include steel and aluminum, each with its own pros and cons. Steel is strong and durable, making it great for molds that need to last a long time, especially in high-volume production.
Once the mold passes testing, it’s time to move into full-scale production. Setting up the mold for this stage involves securing it in the injection molding machine and making sure everything is aligned correctly.
Yes, hard plastics can be used as molds for resin casting, particularly when creating small, detailed parts or when a rigid mold is required. Materials like ABS or high-density polyethylene (HDPE) are commonly used for this purpose.
Polycarbonate is often considered one of the hardest plastics suitable for molding. It offers exceptional strength, impact resistance, and clarity, making it ideal for a wide range of applications, including bulletproof glass, eyewear lenses, and electronic components.
Slides create and release external undercut features by collapsing into place via a cam as the tool closes. It then pulls away as the tool opens.
CNC machines follow the design you created earlier, cutting with incredible accuracy to ensure every detail is just right.
Hi, I am Sparrow Xiang, COO of the HiTop company, me and my team would be happy to meet you and learn all about your business, requirements and expectations.
The goal here is consistency—each part should be exactly like the one before it, with no variation in quality. With the right setup and careful monitoring, the process runs smoothly, delivering large quantities of high-quality plastic parts.
Learn the step-by-step process of making a hard plastic mold, from designing with precision to selecting the right materials and ensuring flawless production. This guide covers everything you need to know to produce high-quality plastic parts efficiently and consistently.
But if you’re only making a small batch, aluminum could save you money while still getting the job done. The key is to match the material to your specific needs so that you get the best performance without overspending.
On the other hand, aluminum is lighter and less expensive, which works well for smaller production runs or when you need to keep costs down.
Polishing the mold might seem like a small step, but it makes a huge difference. A well-polished mold ensures that the plastic parts come out smooth and free of defects.
This step removes any rough spots or tiny imperfections left from the machining process, giving the mold a clean, smooth surface.
The two side actions, shown in dark grey, intersect the mold perpendicular to the parting line. Image Credit: Shutterstock.com/Solcan Design
GETTING A QUOTE WITH LK-MOULD IS FREE AND SIMPLE.
FIND MORE OF OUR SERVICES:
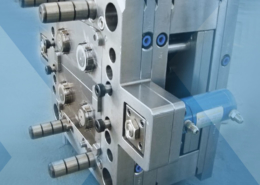
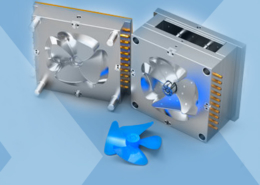
Plastic Molding

Rapid Prototyping
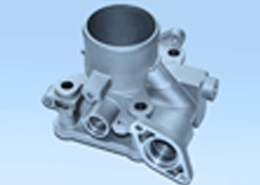
Pressure Die Casting
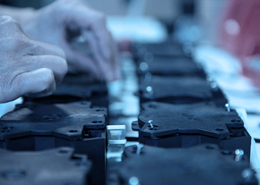
Parts Assembly
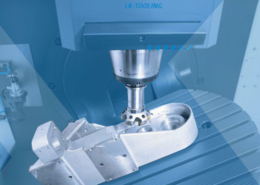