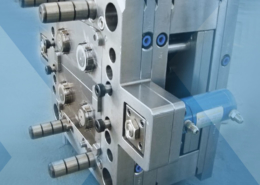
Precision Plastic Injection Molding Services | Large Part & ... - precision plas
Author:gly Date: 2024-10-15
To assist in the prevention of inhibition, a standard practice is to use a barrier coating. A barrier coating is an agent applied to the master to prevent the inhibiting property from coming in contact with the uncured rubber. Acceptable coatings can be polyvinyl alcohol, acrylic sprays or the use of paint primers.
Released earlier, this video remains a valuable recruitment tool and is being re-promoted in celebration of Manufacturing Day 2024.
Six myths of rapid tooling will be dispelled by examining the truth. This will enable the moldmaking and injection molding industries to better accept and sell the growing trend of aluminum tooling.
Traditional book mold with urethane casting still inside the mold. The book mold process is used when hand pouring urethane material. Photo credit, all: Prototech Engineering Inc.
This webinar will provide an overview of new developments in hot runners, controllers, mold components, predesigned molds, process monitoring and mold maintenance equipment. These advancements are designed with the goals of lowering scrap rates, optimizing process temperatures and managing energy consumption. The solutions also aim to support productivity and may contribute to extending the operational lifespan of tooling equipment. Agenda: Innovative undercut and thread-forming components Predesign mold bases and plate control Melt delivery and control solutions Process monitoring and maintenance
Steps to improve data-driven decision-making and key features of a cloud-based system for mold monitoring and asset management.
The purpose of this process is to eliminate the air bubbles that result from mixing, which can interfere with exact surface reproduction. A bubble next to the master pattern will cause a void. When a casting material is introduced, a bump will occur on the reproduction, adding time in the flash clean-up process. De-air the mixture in a bell jar or vacuum chamber capable of pulling 29 inches of mercury. Under this process, the liquid will froth and rise considerably. The bubbles will break and the material will recede to its starting level.
The method for casting these urethanes is similar to the book mold technique. The difference is that an extra gate is added, which allows the cavity of the mold to fill from the bottom to the top. Once the mold is cut open, each side of the mold is sprayed with a mold release and put together with tape, rubber bands, staples or clamps.
A connected software solution streamlines the moldmaking process by providing a unified source of design data, enhancing efficiency and reducing errors, with five key steps benefiting from this integration.
One type of mold is the single-stage or book mold. This type of mold calls for the prototyper to suspend the master inside a mold box and then proceed to encapsulate the part with silicone rubber until the mold box is full. Once the rubber has cured, the mold can be cut in half with a knife. By cutting the mold in this manner, a parting line is created, along with a rippled texture assuring alignment of the two sides of the mold. This is the fastest and most cost effective way to make a silicone mold.
Materials found to cause inhibition are sulfur containing modeling clays, natural rubbers, arnincs, neoprene, unsealed wood and even wax from paper cups. When in doubt, a patch test is recommended. Inhibition has occurred if the rubber is gummy or totally uncured after the recommended cure time has passed.
When used for conformal cooling in plastic injection, 3D printing opens a wide range of design freedom. This design freedom enables designers to develop highly-efficient thermal regulation networks. However, this blessing also comes at the expense of not only higher manufacturing cost but also higher design cost as the designer could spend weeks to develop optimal cooling channels. This webinar will explore strategies and tools — including SimForm, a front-end thermal simulation app — to help tool designers and tooling managers maximize the benefits of 3D printing while minimizing manufacturing and design costs. Agenda: 3D printing applied to the plastic injection industry 3D printing pros and cons Tools and methods to facilitate the integration of 3D printing
Mixing should take place in a plastic container four to five times larger than the material volume to allow for expansion during vacuum degassing/de-airing. Vacuum degassing/de-airing is recommended for all silicone rubbers when not using automatic dispensing equipment.
Again, the material will froth and rise. The air bubbles will break and the urethane recedes to the starting level. Pour the urethane into the mold gate in a thin stream. Continue pouring until the gate is full and the urethane has been released through the vent ports.
Prior to making the mold, venting and gating should be considered. Vents and gates must be formed to control the flow of urethane into the mold. The size and location of the gate required for a specific mold is determined by the volume and shape of the master (i.e. the greater the volume, the larger the gate area). Other factors include wall thickness of the master and viscosity and pot life of the casting compound.
Join MoldMaking Technology Editorial Director Christina Fuges as she gets the latest news on this mold builder's use of VR for mold design education.
Utilizing helpful products and services for mold maintenance, repair and surface treatment (MRST) can save moldmakers time and money. Access more information about MRST in this exclusive, online-only content, including a suppliers list, products, services and more.
Start the casting process by spraying or brushing a release agent on each side of the mold. Put the mold together and affix with tape, rubber bands or screws through the wood frames on two-part molds. Since most urethane systems consist of a resin and hardener, carefully mix these components in a container, much like silicone. Allow for expansion during the degassing process, but at a lesser rate. Place the mix in the vacuum chamber and start the degassing process.
Gerardo (Jerry) Miranda III, former global tooling manager for Oakley sunglasses, reshares his complete mold design checklist, an essential part of the product time and cost-to-market process.
When choosing a silicone, one major consideration is the silicone’s resistance to inhibition. Inhibition in silicone rubber is caused by certain contaminants in or on the master to be molded. These contaminants will impair or stop the crosslinking necessary for silicone rubber to cure, resulting in tackiness at the master or total lack of cure throughout the mold.
With the right equipment, technology and staff, we’re well-prepared to meet your demands and exceed your expectations—no matter how stringent they may be.
Once the prototyper determines which type of mold is to be made and which silicone is applicable, it is time to prepare the silicone for the mold. Begin by accurately weighing the silicone base and catalyst, following the manufacturer’s instructions for the correct mix ratio.
In ISO 9001 quality management systems, the Management Representative (MR) plays a crucial role. While the 2015 version of ISO 9001 no longer mandates this position, having a trusted management member serve as an MR remains vital for streamlining operations and maintaining quality standards.
This very important step in production of a mold takes just a few minutes and is well worth the time spent. Remove the material from the chamber and begin pouring in the mold frame. Pour at the lowest point, allowing the silicone to flow around the master. Do not pour directly over the master. This may cause a wave effect and potentially trap air. Continue pouring until silicone has reached the top of the mold box or at least 1 inch above the master. Set the mold aside to cure following the manufacturer’s instructions. After the mold has cured, separate the mold halves or cut the book mold open (establishing a parting line) and remove the master. The mold is now ready for urethane casting.
Join MoldMaking Technology Editorial Director Christina Fuges as she gets the latest news on this mold builder's use of VR for mold design education.
The popularity of silicone rubber molds has prompted urethane manufacturers to produce a wide variety of urethanes. These materials have specifications ranging from a 10 shore A through 85 shore D durometer, to products having a 45 to60 second pot life and a five-minute demold time. Other urethanes have an operating temperature of 225°F up to 300°F.
The last step in part reproduction is finishing. To finish the prototype part, simply cut off the gates and vents and remove any flash that may have occurred. Smooth any rough areas with a fine file and sandpaper. Should any voids be present it is possible to mix the urethane material, degas and fill with a fine point tool. After this material has cured, remove any excess with a file or fine-grit sandpaper.
Formnext Chicago is an industrial additive manufacturing expo taking place April 8-10, 2025 at McCormick Place in Chicago, Illinois. Formnext Chicago is the second in a series of Formnext events in the U.S. being produced by Mesago Messe Frankfurt, AMT – The Association For Manufacturing Technology, and Gardner Business Media (our publisher).
Silicone rubber for rapid prototyping and moldmaking is available in two types: addition cure (platinum base) and condensation cure (tin base). Characteristics of addition cure silicones include:
MoldMaking Technology Editorial Director Christina Fuges sits down with Murphy Forsyth, GM – Injection Molding and Director Of Marketing for Zero Tolerance LLC in Clinton Township, MI.
It’s easy to imagine the advantages automation offers the moldmaking process, but it's challenging to change one’s mindset, develop a plan and invest.
Discover how CAD/CAM functionality tailored for the mold industry can significantly enhance the mold design process. In part three of the webinar series, Cimatron will focus on designing waterlines and cooling components. It will demonstrate how CAD/CAM tools can verify drill line depths for water lines and baffles, ensure that minimum steel requirements are met while placing water lines, and provide a complete list of all baffle cutoff lengths. Additionally, it will explore how to confidently design runners and gates using CAD functionality specifically developed for these aspects of mold design. Agenda: Waterlines and verification Conformal cooling Baffles and charts Runners and gates
After attending IMTS, it's clear that the integration of advanced technologies is ready to enhance precision, efficiency and automation in mold manufacturing processes. It’s a massive event, so here’s a glimpse of what the MMT team experienced firsthand.
Discover how to enhance your mold design process with CAD/CAM software specifically tailored for the moldmaking industry. In part two of this webinar series, Cimatron will demonstrate how to intelligently design mold components, such as slides and lifters, using powerful CAD/CAM tools to accelerate the design process. Additionally, it will cover how to avoid errors and ensure design accuracy for ejector pins by checking clearance distances, calculating cutoff heights correctly, and thoroughly documenting all ejector components. Agenda: Slides Lifters Inserts Ejection pins and charts
Next, the urethane is placed in a cartridge with separate cylinders for the resin and hardener. This cartridge is placed in a dispensing gun similar to a caulking gun and is operated manually or by air pressure. An elaborate dispensing system may be purchased that includes variable mix ratios, line heaters or custom-built to your specifications. A static mix nozzle is attached to the end of the cartridge so the resin and hardener will mix thoroughly. Under low pressure, the urethane is injected in the mold until it flows from the vent. At this point, the mold is placed in a pressure tank to help eliminate bubbles. In approximately five minutes, the mold is ready to open.
SLA masters were finished by experienced model makers. Then, a silicone mold was created and a urethane casting (black part) was ran.
Steel supplier discusses high thermal conductivity metal powders that also address the skills gaps via user-friendly materials and promote sustainability via durability and higher cycle counts.
With the exception of CNC machining, rapid prototyping technologies use a layering technique in their creation. To ensure a quality polyurethane cast part, a post-processing finishing is required in most cases. This finish can be applied by sanding, filing and painting to achieve a uniform smoothness or desired textured effect.
After attending IMTS, it's clear that the integration of advanced technologies is ready to enhance precision, efficiency and automation in mold manufacturing processes. It’s a massive event, so here’s a glimpse of what the MMT team experienced firsthand.
We also work with our customers to devise inventory solutions to meet their unique needs for safety stock, and “just in time” delivery.
Do you have a complex custom injection molding project? Perhaps you are looking for a supplier for an on-going source of premium molded parts. No matter what your requirements may be, if you need a flexible, responsive, first-class injection molding solution, we can provide it. With over three decades of engineering and injection molding behind us, we can complete almost any type of injection mold tooling or plastic molding project.
Considerations for selection should be hardness (durometer rating), tensile strength, impact strength, elongation, heat deflection temperature and clarity. All urethane manufacturers provide specification sheets to assist in selection.
MoldMaking Technology addresses the complete lifecycle of the manufacture and maintenance of a mold—from design to first shot—by providing solutions and strategies to moldmaking professionals charged with designing, building and repairing molds. About Us
A water-based, eco-friendly plastic mold cleaning system helps Rankine-Hinman Manufacturing restore flow rates and avoid big-ticket failures on complex and costly molds.
Engineers use properly preloaded bolts, blocks, springs and side-action cores to enhance functionality and reliability in various mechanical systems.
Coretech Systems’ Moldex3D 2023 strengthens simulation performance, provides user-friendly interfaces and cloud services, streamlines workflow and strives to connect the virtual to the real.
Prototyping has been around for a number of years. With the addition of one word, “rapid,” a new industry has been created. Economic concerns along with global competition make additive fabrication a must. An inexpensive and frequently used method in the prototyping process is casting urethane parts from silicone rubber molds. The urethane materials of today, along with moldmaking techniques from previous years, give prototyping the respect it deserves.
A focus on electrode design and automation helps toolroom improve efficiency, reduce tooling costs and deliver higher quality products.
Understanding and facing the moldmaking industry’s obstacles to growth requires a strategy focused on increased profitability.
The first step in the duplication process is to create the master pattern. In the past, masters were created in pattern shops from clay, wood or plastics. Today, we can add rapid prototyping (RP) technologies to help in the creation of masters. These technologies include stereolithography and selective laser sintering by 3D Systems, fused deposition modeling from Stratasys, PolyJet from Objet Geometries, 3DP from Z Corp and CNC machined masters.
Steps to improve data-driven decision-making and key features of a cloud-based system for mold monitoring and asset management.
To accelerate the curing process, it is permissible to place the mold in a warming oven. Once the curing process is complete, separate the two sides of the mold and demold the duplicate part. To cast more parts, repeat the procedure. Silicone rubber molds will yield approximately 20 parts using this casting method; however, more or less parts are attainable depending on part complexity.
The skin mold or brush-on technique is used for extremely large parts with deep undercuts, tall vertical walls or both. To make this type of mold, the moldmaker begins by applying a pre-coat layer of silicone and catalyst mixture. This coating should be poured over or brushed onto the master. If air bubbles form during this procedure, break them with a light air spray or by hand. Once the pre-coat becomes tacky, a layer of silicone with the consistency of butter is then applied. This “buttering” technique continues until a layer of 3/8 inch is formed. Adding more layers will help with tear resistance. After the silicone has cured, a mold box is constructed and the skin mold is backed or supported with a material made from plaster or urethane foam.
The multi-stage or two-part mold is more labor intensive in its construction than the single-stage mold, but provides for better control of a parting line and will enable the casting of larger parts by providing mold stability. The multi-stage mold is achieved by forming a parting line with modeling clay. A mold box is constructed and filled with silicone that covers one half of the master. After the first pour cures, the mold is inverted, modeling clay is removed and the silicone released from the frame. The frame can then be replaced and the second mold half poured and cured.
Steel supplier discusses high thermal conductivity metal powders that also address the skills gaps via user-friendly materials and promote sustainability via durability and higher cycle counts.
Identify pain points, tackle each one strategically and maintain flexibility to keep your moldmaking business on a path to growth.
In addition to insert molding, clean room molding and other molding processes, we also provide add-on services to complement your molded products. Our services include assembly and other processes – just tell us what you need to make your project a success.
MoldMaking Technology editorial director Christina Fuges chats with Kevin Hartsoe, president of Neu Dynamics to reveal their five best practices for improving efficiencies in culture, technology, process, measuring success and staying competitive ... in 5 minutes.
After attending IMTS, it's clear that the integration of advanced technologies is ready to enhance precision, efficiency and automation in mold manufacturing processes. It’s a massive event, so here’s a glimpse of what the MMT team experienced firsthand.
After attending IMTS, it's clear that the integration of advanced technologies is ready to enhance precision, efficiency and automation in mold manufacturing processes. It’s a massive event, so here’s a glimpse of what the MMT team experienced firsthand.
Explore the standout articles of September, featuring innovations, expert insights, and strategies to boost efficiency and quality for your moldmaking needs.
At this point, re-introduction to the vacuum chamber is recommended to take care of any trapped air. If a chamber is unavailable, the mold can be placed in a pressure pot and cured under 80 to 110 psi until the urethane’s gel time has been reached. Use of a pressure chamber compresses any bubbles or voids to microscopic size, thus producing a void-free, bubble-free part.
In ISO 9001 quality management systems, the Management Representative (MR) plays a crucial role. While the 2015 version of ISO 9001 no longer mandates this position, having a trusted management member serve as an MR remains vital for streamlining operations and maintaining quality standards.
We know that our customers not only need great products; they also need high-caliber service that adds value to their business at a competitive price. We aim to work with you to meet your goals, offering adaptable delivery and production arrangement that can be geared to your requirements. To find out more about our services or discuss your project, call us at (503) 685-9000.
Discover how to enhance your mold design process with the right CAD/CAM tool for parting and cavity design. This webinar will explore CAD/CAM capabilities including how hybrid solid/surface modeling can streamline workflow and improve accuracy. Learn how to confidently tackle parting, runoff, and shutoff, ensuring precision and efficiency in your designs. Agenda: Part analysis QuickSplit techniques Parting and runoff strategies Shutoff solutions
Over the years, we have invested heavily in our equipment and staff. This means is that we have ample capacity to complete a variety of projects. We have capability to mold items up to 8 pounds, as well as objects as light as .4 ounces. Our machinery and processes enable us to work to extremely tight tolerances, creating products which are consistent of the right dimensions.
To prevent mold shift, mold locators are vital for precise alignment of mold halves to produce accurate parts. Adding locators in the mold can be accomplished in several ways. A simple technique is to cut a notch in the first side of the mold. A reversal of this depression is formed as the opposite side of the mold is cast. Mold locators may be placed in the setup of the first side of mold construction. Upon curing, remove these locators and pour the second side of the mold.
How-to, step-by-step instructions that take you from making the master pattern to making the mold and casting the plastic parts.
Join this webinar where Hexagon will explore how state-of-the-art CAD/CAM technology can drive your business forward. Learn how to optimize tool paths, enhance design accuracy and reduce lead times with advanced simulation. Discover the power of automation and real-time data for continuous improvement. Tailored for mold and die manufacturers, this session offers actionable insights to boost productivity and quality. Don’t miss this opportunity to gain a competitive edge in progressive die manufacturing. Agenda: Key challenges in progressive die manufacturing Optimizing tool paths Enhancing mold and die design accuracy Reducing lead times with simulation Automating processes for greater efficiency Leveraging real-time data for continuous improvement
Our equipment is nothing without expertise. For 30 years, we’ve led the way in molding and contract assembly services for a diverse customer base.
This article describes the techniques used to cast quality urethane parts from a silicone rubber mold using a five-step duplicating process:
Diamond compounds, with their varied grades, colors and base options, provide a comprehensive solution for mold builders in need of precise and superior polishing across diverse materials and applications.
Once the master is built, a silicone rubber mold can be constructed. The most important characteristic of silicone rubber is the reproduction accuracy. Silicones are widely known for their extreme degree of detail duplication. Silicone rubber also provides the flexibility to construct molds in different ways.
The need for data to track information and the history of the mold-building process is ever-increasing, and mold component solutions can help.
Partnership brings cutting-edge training in scientific molding to RJG’s new facility to further develop future workforce skills.
As previously mentioned, urethane manufacturers have developed what is known as “quick cast” or “fast set” urethane. These particular urethanes have a gel time of 45 to 60 seconds with a demold time as short as 5 minutes. Another advantage is higher heat deflection temperatures and increased mold life. Using these urethanes, the prototyper is able to cast 15 to 30 parts per day with overall quantities reaching several hundred parts.
Would you ever leave your valuables unprotected? Neither would we. Your molds are an investment in your company and critical to your business—we understand this. That’s why we store and protect our customers’ molds in a water and fire safe storage area.
Smart sensors and sophisticated process and measurement data management are driving intelligent moldmaking to new heights.
GETTING A QUOTE WITH LK-MOULD IS FREE AND SIMPLE.
FIND MORE OF OUR SERVICES:
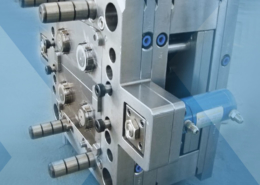
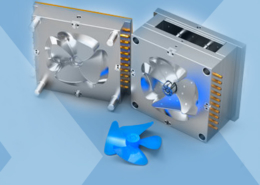
Plastic Molding

Rapid Prototyping
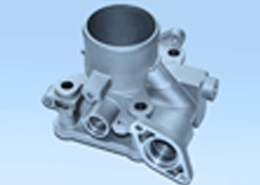
Pressure Die Casting
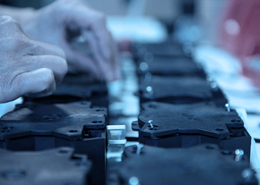
Parts Assembly
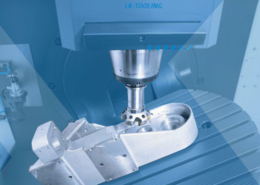