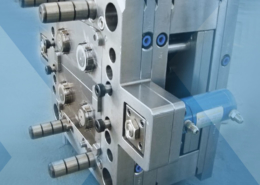
Precision Injection Molding Services | Aprios - plastic molding services
Author:gly Date: 2024-10-15
Among our comprehensive plastic molding services, thermoplastic injection molding produces precise molded parts that are suitable for a range of applications.
Insert molding and over-molding are additional processes that can be worked into both thermoplastic and thermoset parts.
Thermoplastic components, produced through the thermoplastic injection molding process, possess several key characteristics that contribute to their versatility and widespread use in various industries. Here are some notable characteristics of thermoplastic components:
Acrylonitrile butadiene styrene (ABS), high-density polyethylene (HDPE) and thermoplastic polyurethane elastomer (TPU) are commonly used thermoplastic polymers — a plastic material that becomes pliable or moldable at an elevated temperature and solidifies once it has cooled — used in injection molding projects.
A similar process, over-molding involves molding one material (usually a softer or different type of plastic) over another previously molded part to add new properties and enhance the appearance of the original part.
A commodity resin, ABS is a suitable choice for producing inexpensive and strong plastic that will hold up against external conflict. ABS injection molding is resistant to humidity, temperature and frequency of use, making it a top choice among injection molding materials. It’s even resistant to most oils and acids, making it popular for furniture, packaging and toys.
TPU injection molding is popular in the manufacturing of sporting goods, medical devices and is a favorite for use in automobile manufacturing. An engineering resin, TPU is pricier than working with ABS or HDPE.
We use cookies to personalise content, to provide social media features and to analyse our traffic. We also share information about your use of our site with our social media and analytics partners who may combine it with other information that you’ve provided to them or that they’ve collected from your use of their services. You consent to our cookies if you continue to use our website.
ABS injection molding is often used to manufacture sporting goods, medical devices and industrial applications. So, how do you make ABS plastic molds? It’s easy to get the raw materials for, is considered to have good overall performance, it’s inexpensive, and ABS is among the most common plastic resins used for injection molding manufacturing.
While thermoset molding is an irreversible process due to the chemical reaction that occurs during the necessary curing process, thermoplastic molding is easily reversible. Thermoplastic parts can be re-melted and molded repeatedly without causing the material to deteriorate. At Leech Industries, we offer our customers the option to use recycled materials if this meets your needs.
Considering the benefits of ABS, HDPE and TPU injection molding can help you determine which are the best injection molding materials to meet your project needs.
Another inexpensive commodity resin, HDPE plastic for injection molding is melted into a moldable state and is then transferred into the cavity of the mold once it has reached the correct temperature to meet your HDPE injection molding needs. Note that as soon as it’s in the cavity, it begins hardening quickly. HDPE is popular for its customization control and is among the most efficient choices for injection molding manufacturing.
There’s another injection molding resin type you may want to look at if you require an alternative to glass: polycarbonate injection molding. Polycarbonate is a lightweight resin that is pliable and has a natural UV filter.
If you’d like to acquire prototypes before going forward with your plastic molding projects, utilize Leech’s prototyping solutions to test parts before putting them through to full production. Contact us to find out more.
TPU injection molding is best suited for applications that require the elasticity of rubber with high tear strength. TPU is elastic, can be painted, performs well at high temperatures, and is resistant to water, fuel and chemicals. TPU also needs little or no compounding.
In insert molding, a pre-formed component (known as the insert) is placed into the mold and molten plastic is injected to surround and bond with the insert. This insert is typically a distinct component, typically either a metal or a different plastic part. Insert molding is often used for adding discrete components within a single part.
An engineering resin, polycarbonate is an amazing alternative to glass, as it’s transparent and resistant to cracks and breaks. From manufacturing light fixtures to eyewear and medical devices, polycarbonate injection molding is a popular resin type. However, polycarbonate is not always preferred, since it’s prone to scratching.
HDPE injection molding is made from the polymerization of ethylene. Its strength-to-density ratio is superb, designating it a standard choice in the manufacturing of water bottles, milk jugs, plastic envelope mailers, piping and food storage containers.
Want to learn more about ABS, HDPE, TPU or polycarbonate injection molding, or ready to get started on your own injection molding prototype? Contact our experts to start your project today!
GETTING A QUOTE WITH LK-MOULD IS FREE AND SIMPLE.
FIND MORE OF OUR SERVICES:
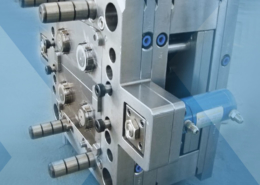
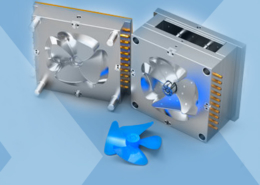
Plastic Molding

Rapid Prototyping
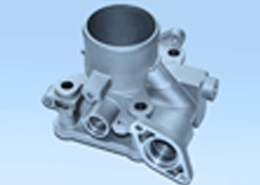
Pressure Die Casting
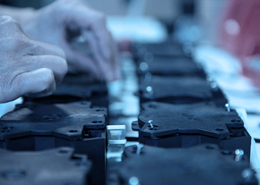
Parts Assembly
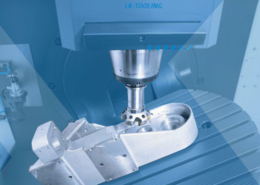