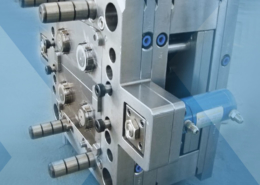
Precision injection molding of plastics - precision injection molding company
Author:gly Date: 2024-10-15
The two-shot injection molding process is similar to the regular injection molding technique, the only difference being that this former uses two injection nozzles that are released into a mold that has two crates. The process takes place in 4 main stages.
Reduced Post-Processing: The two-shot injection process is all-encompassing, everything is done in one move, and this cuts down the need for further processes like post-processing, which usually increase the cost, time, and energy consumption for nothing.
Our reputation as specialists stems from the millions of parts we’ve supplied in unfilled, glass, carbon fiber, bearing and wear grades of advanced polymer materials including:
Rubber: Rubber comes in many forms, and the most commonly used is a synthetic rubber, thanks to the many applications it can be used for. It is easier to melt, and mold is easily available, and has a very wide range of options as far as designing is concerned.
Certifications on all shipments: Drake Plastics provides a Certificate of Conformance with all products regardless of polymer composition at no charge. Special testing is also available at a reasonable cost.
Drake Plastics’ support capabilities can be especially beneficial to customers transitioning from a machined plastic or metal component to injection molding:
Thermoplastics: These are finely cut plastic materials that can be reused as many times as possible without losing any of their good attributes. It is loved mainly due to their low cost, low melting temperatures, and the fact that they are eco-friendly.
Annealing PEEK and other ultra-high performance thermoplastic parts: Drake has extensive experience in annealing to relieve internal stresses that can impair a part’s properties or cause it to deform over time. Residual stresses occur as an advanced polymer rapidly transitions from its hot melt phase to ambient temperature. This is especially problematic for parts with heavy or varying cross-section thicknesses that cool at different rates. Annealing under controlled conditions resolves this: by heating parts above the advanced polymer’s Tg or softening point, then cooling very slowly to a point below its Tg, the polymer chains relax uniformly, relieving residual stresses. Drake offers annealing on a custom basis. It is often utilized for injection molded parts that require exceptional dimensional stability or a crystallinity level that maximizes the polymer’s strength, toughness and chemical resistance.
Drake offers a diverse menu of services and capabilities to meet customer-specific requirements and industry compliance standards for injection molded parts. They include:
With decades of experience in melt-processing ultra high-performance thermoplastics, injection molding specialists, Drake Plastics has fine-tuned process conditions, designed and built specialized components for our molding equipment and invested in the technology needed to produce consistently high-quality injection molded parts in Torlon PAI, PEEK and similar advanced polymers.
Stage 2: The press on the first crate is opened, and the part that has been freshly created from the first injection is quickly transferred robotically to the second mold. This means that the first chamber is now free again, ready for the second injection.
Post-curing Torlon PAI parts: Every Drake-produced Torlon PAI product goes through an engineered post-curing processes, a key factor in realizing the full performance potential of this advanced polymer. This final step before shipment achieves Torlon PAI’s typical core Tg (glass-transition temperature) midpoint value of 540°F (282°C). In our decades of experience with the material, we’ve optimized curing cycles to produce Torlon PAI parts to achieve maximum structural strength, toughness, and resistance to wear and chemicals.
Improved Quality: The precision involved in this technique is off the charts, and when you combine that with the meticulous steps it follows and the raw materials used, the end product comes out with the best qualities one could ever wish for. This boosts customer confidence in your products and increases sales.
Like most molding processes, there are certain raw materials that are popular with people who use two-shot injection molding for their manufacturing needs. Each has the qualities needed to produce a specific type of end-product. These materials include the following.
Step 3: The press on the second chamber is closed, and the second injection is shot into the now open first chamber until it fills up just like the first one. This is to ensure uniformity of the end products.
So why are manufacturers clamouring to use the 2k injection molding technique for most of their production needs? The use of this technique has been gaining popularity, and that’s not by accident. The following are some of the reasons why.
Drake’s process technology includes In-cavity pressure transducers and RJG Systems that monitor process parameters inside the mold cavities to maintain ideal conditions. This important control leads to high quality and exceptional repeatability in every Drake injection molded part equipped with RJG.
Part Consolidation: The traditional methods of manufacturing usually split the production of different parts, which are then joined to make a single component. This is a lot of work and wastage of resources. Two-shot injection molding ensures that the number of parts needed is reduced significantly, saving time, energy, and costs.
Two-shot injection continues to gain popularity in manufacturing, and this means that very soon, the future will be ruled by those who were clever enough to jump on this bandwagon when it was picking up. Many other molding processes work in the same way, it all comes down to what you need to achieve and the product you plan to make. For more information on two-shot injection molding, visit our website at your nearest convenience or drop us a call and have all your concerns addressed by a team of experts to your satisfaction.
Thermosets: These are almost similar to thermoplastics, only that they cannot be reused. They are one-time-use plastics that are used to make various domestic and commercial tools. They are not good for the environment and for this reason they are not used too often.
Our production team’s ideas have a major impact on our reputation for superior quality. Among their initiatives: dedicated dryers for each resin to avoid cross-contamination. And they know purging can’t eliminate all residue after a run, so they do a full tear-down, polishing the screw and cleaning all components that contacted the melted polymer in the prior run before starting the next job.
Insert molding integrates functional metal components into injection molded parts during the molding process. The inserts are fixed in the mold cavity, and the polymer melt flows around the metal component as the molding process takes place. Electrical conductors, threaded fasteners, structural reinforcements and protective caps made from titanium, stainless steel and other metals are only a few of the possibilities for insert molding, and the technique is incorporated into many high-performance parts made from the advanced polymers Drake routinely molds. Other advantages include reduced assembly time in the customer’s operation and more secure integration of the molded-in metal component in the part.
Many customers describe our facility as the cleanest and most efficient they’ve experienced. Our all-electric injection presses yield precision parts from 0.03 to 20 oz. (0.85 to 570 grams). They use no hydraulics, adding to the cleanliness of our operation. Each machine is also equipped with a unique capability to compress or ‘coin’ parts during the molding cycle, enabling us to injection mold very heavy cross-sections without porosity or voids.
Glass: Glass is a rare molding raw material but is used on some special occasions. It is a little trickier to mold compared to the other materials on the list, and the end products are usually used in the medical industry.
Stage 1: The raw materials are loaded into both injection canisters, where they are exposed to heat and pressure so that they can maintain that viscous state necessary for injection to occur. The first molding crate is opened, and the first injection is shot into it as the other crate remains closed.
Metal: There are different types of metals that are used in injection molding, and the most common ones include steel, aluminum, and brass. These three are cheap, widely available, and molding them is much easier. Products made from them are also in high demand as they last longer.
Precision injection molding ultra high-performance plastics demands a solid understanding of each polymer’s unique behavior to avoid degradation and achieve optimum property and quality levels. Its melt characteristics and flow behavior must be factored into process conditions and hardware designs to preserve physical properties and achieve consistent quality in the high-pressure and high-temperature molding process.
Improved Efficiency: The process doesn’t require too many hands on the job. With most of it being automated, you end up saving money that would have gone into covering labor costs, and in return, you get precise robots that are able to handle the same work at ten times the speed and accuracy.
Near-net shapes provide an efficient, economical bridge between machining low part quantities from stock shapes and molding high volumes that require a significant investment in tooling. These forms or blanks are molded in low-cost tools and approximate the part’s as-designed dimensions. They are then machined to exact part dimensions. Using near-net shapes when production requirements reach the right levels yields a major savings in material vs. machining from rod or plate.
Drake Plastics’ Quality Management System is certified to the worldwide aerospace industry’s AS9100D(2016) as well as ISO 9001:2015 standards. These stringent requirements apply to all products we manufacture. Our ability to meet these standards stems in large measure from our team’s experience and their commitment to achieving the highest attainable levels of quality. We also support our team by investing in the best inspection technology available, including:
The best production and quality practices deliver maximum value to customers only when backed up by consistently exceptional service. Drake’s customer-centric culture is evident in our rapid response to requests for information, support and problem-solving. Drake’s on-time delivery performance is 98% or better. Our team sets 100% customer satisfaction as the norm and sustaining it determines our ongoing service-based investments.
Drake’s extensive in-house molding and machining capabilities combine to offer customers molded parts with complex geometries and features not possible with injection molding alone. Precision finish-machining adds deep undercuts, side or angled holes or ports, zero or negative draft sidewalls and other design elements that are impossible or impractical to mold. Our CNC machining also yields tighter part tolerances than can be achieved in molding. For example, machined feature tolerances on a molded part can be held to +/-0.0005 inch (+/-0.02mm).
Step 4: The second chamber is opened again, and the second part is transferred to it again using robotic arms. The process continues this way as fast as it can until the required number of products is clamoring attained.
Better Aesthetics: The process is handled in a controlled environment, and this makes it easy for any other modification to be added. This could be patterns, logos, texts, or colors that further enhance the overall appearance of the end product. These auditions are permanently engraved on the product, making it look more natural and complete.
Nylon: This is among the most common materials used and can be found everywhere on the planet. It is used to make strong mechanical parts that are used in the automotive, aerospace and other industries.
Design Range: With two-shot injection molding, you are free to try out as many designs as you want, even those that may seem to be impossible. The wide range of options available to this technique makes it a cost-effective and covenant method of making clear plastic and metallic mold products.
Drake invests in the best available molding and process equipment and control technology for materials like Torlon PAI, PEEK, Ultem PEI and other high-performance polymers. Our production team also takes extreme measures to achieve the highest levels of quality and performance in molded parts.
2K injection molding, also known as two-shot injection, is a process that uses two injections instead of one. Like any other molding technique, the two-shot injection has become very popular with manufacturers worldwide for various reasons. But how exactly is it carried out step by step? This is what we are going to look into today. We will be exploring the entire step-by-step process of two-shot injection molding, the machines used, the raw materials involved,,and finally a brief look at some of the benefits it brings to the table.
GETTING A QUOTE WITH LK-MOULD IS FREE AND SIMPLE.
FIND MORE OF OUR SERVICES:
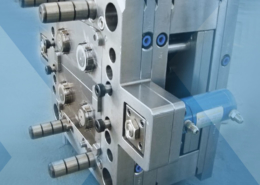
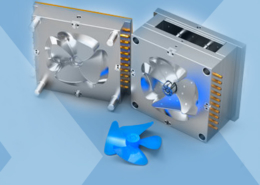
Plastic Molding

Rapid Prototyping
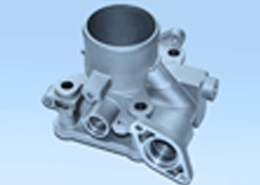
Pressure Die Casting
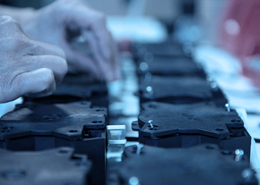
Parts Assembly
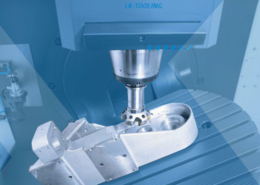