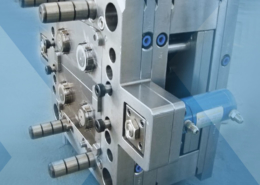
Precision injection molding of plastics - high precision injection molding
Author:gly Date: 2024-10-15
Basic features may include structure, shape, size, or other dimensions. It also tells us about the performance of the product. If you start manufacturing a specific product without creating a prototype, it will increase the chances of production of a defaulted product.
Commonly, 3D printing is the cheapest technique used to make low-price prototypes. The cost of prototypes produced through this technique remains constant. It means that its first and last copy shows the exact cost.
You may require a prototype for non-functional testing in which the prototype will reveal its actual suitable performance.
Most plastic prototype manufacturing processes have high startup costs and expensive tools but may create the parts at economical rates. You must choose a technique that can create your desired volume of the product at an affordable cost.
A prototype made with high-quality material is found at a high cost and vice versa. Techniques used for manufacturing prototypes also significantly affect their price.
This manufacturing technique is also designated as polyurethane casting or simply urethane casting. The process shows similarity with the injection molding technique.
These prototypes are designed using rough materials and must show how the end product will function. They are the rough representation of your design.
The process of plastic injection molding has the ability to make outstanding quality prototypes at economical rates for the various industrial sectors. They are precisely the replicas of the final products, exhibiting their main features and performance.
This process allows you to design the prototypes with varying complexities, i.e., simple to intricate. It is constructive for creating various plastic prototypes quickly at economical rates and considered superior to the vacuum-casting plastic parts fabrication technique.
Plastic prototyping is a vital process for product development, and the creation of prototypes is the foremost step in the process of parts fabrication.
Most designs demand complex geometries and tolerances that cannot be achieved through various manufacturing processes. Therefore, you must always select manufacturing processes that fulfill your requirements and create plastic prototypes with demanded designs.
You must remember the exact design you need for your plastic prototype. A variety of manufacturing processes are used for the creation of plastic prototypes. You must be choosy while selecting a specific technique for your designs.
The process is automated and enables machines to manufacture more precise parts with complex geometries and better surface finishes.
No human participation is required for CNC machining to manufacture parts for various industries, including consumer products, automotive, aerospace, and medical.
It depends on various considerations, such as if you choose a costly material and highly technical and latest methods for prototype fabrication; your project price will increase.
Fenton Precision Engineering Ltd is a UK company that was founded in the 1970s with its headquarters in Northamptonshire. This company is a one stop shop for all your molding needs offering various services such as in-house design, rapid prototyping, injection molding and assembly services, tool making and engineering, and CAD modeling. With over 50 years of experience, the company has earned its reputation in injection molding, having two different molding sites each site with presses ranging from 25 to 360 tonnes. Fenton Precision Engineering Ltd is ISO9001 certified in both its tool making experience and site maintenance. The company has many customers worldwide and offers extra services to its customers such as tool repair and maintenance.
Choosing the right mold manufacturing company will impact the quality of your mold designs, actual molds and the finished products. When looking for a mold manufacturing company, you need to consider factors like the level of the company’s machinery and technology, its mold manufacturing process, the time taken to produce the molds and the quality of its services. The UK has been among the leading suppliers of injection molding products with some companies standing out from the rest. In this post, we will look at the top 10 best mold manufacturing companies in the UK to help you make the right choice when looking for a molding partner.
ND Precision Products was formed by David Squire and Gordon Gregory in 1973, who were partners in precision tool making. The company grew quickly, establishing its first manufacturing factory in 1981, a 3000 sq feet floor that accommodated a wire erosion department. Today, the company is one of the leading companies in the UK in precision tools manufacturing such as plastic mold injection, press tools and laser welding machines repair. The company offers its molding tools to industries such as aerospace, automotive, medical and toy manufacturing. The company has an experienced workforce which uses their skills to provide solutions to various precision tool making challenges. The company also employs the latest engineering machinery and computer aided design skills to ensure its products are at par with the required standards and customer specifications.
The total production volume of the plastic prototypes shows close relation with the overall cost of the manufacturing technique.
Using the best suitable technique for manufacturing your prototype is a compulsory element. Choosing a suitable prototype manufacturing technique and considering several factors, such as purpose, form, cost, etc., before manufacturing prototypes can help you produce superb-quality.
The cutting tools are controlled by the instructions given by computer programs, resulting in a more accurate design. The prototypes also show greater consistency and meet all the required dimensions.
Kemal is a famous prototype manufacturing company that has manufactured many prototypes for years. We are using a variety of top-quality plastic to manufacture the best, high-quality prototypes for our customers.
You may need to make changes during manufacturing, such as tool modifications; otherwise, it can result in immeasurable loss. Designing a prototype will allow you to make changes according to your needed product.
The materials’ flexibility, rigidity, stress, strain, and other properties should be according to your desired properties in your final high-performing plastic prototype.
Injection molding is an excellent method for the production of plastic prototypes. It is commonly adopted when small quantities of prototypes are required. Injection molding is a technique widely adopted for creating identical components through the molding process.
Some other factors as more precise and complex designing and prototypes, require more time, machines, and cycle time, so cost increases when you need more precise, intricate parts.
TDL Mould CO LTD was established in 1995 and is a key player in the mold manufacturing industry. The company’s global reach and extensive experience in the industry indicate a potential influence on different markets in the UK and other parts of the world. TDL is an expert in injection molding, mold design, and manufacturing. They serve various industries like automotive, medical, electronics, and consumer goods. With over 25 years of experience, TDL has built a strong reputation for delivering durable molds and plastic components of the highest quality. Their services cover the entire process – from optimizing technical drawings in collaboration with clients for product design to efficient mold design and manufacturing to ensure optimized production. The company uses advanced techniques and state-of-the-art equipment to produce excellent plastic components for different uses. What sets them apart is their ability to provide comprehensive secondary services such as surface finishing, assembly, and packaging. This ensures that the final products meet the specific requirements and specifications of their clients. TDL demonstrates its dedication to excellence and innovation through its methodical approach to addressing challenges. The company has collaborated with leading automotive companies, focused on optimizing the manufacturing processes, increasing efficiency, and enhancing mold quality. This partnership highlights TDL’s expertise in delivering comprehensive solutions for mold manufacturing, making a significant impact in the industries they serve.
All these companies have their strengths and weaknesses regarding the mold manufacturing processes they use and the technologies they have adopted. Before you select a particular company, you need to do extensive research about the company so as to understand how they operate and whether they align with your needs and requirements. You should also consider the company’s quality control and cost so as to get value for your money.
Lead time is a critical measure in prototype manufacturing, and it depends on part design, size, the material used, and methods customers select for their prototype manufacturing.
The Midas Pattern Company Ltd was founded in 1989 in the UK as a tool making and molding business. This company has grown profoundly since its establishment, having 30 years experience in the trade. This company carries out its manufacturing and production activities in-house to ensure the highest quality and reduce the cost of subcontracting. The company is NQA accredited having BS EN ISO 9001:2015 certification. Midas Pattern specializes in prototyping and production of polyurethane moldings, model making and tool making. The company has recently been certified as carbon neutral, undertaking the green initiative for environmental conservation.
Its suspension is followed by pouring the liquid silicon into it to form the silicon-based casting mold. After that, it is allowed to cure in a heat chamber.
The complexity of the design also dramatically affects the price of the prototype. The price enhances as the complexity of the prototype increases. A complex prototype is more costly than one with less complexity.
This selection offers exceptional performance prototypes at an economical cost. Plastic prototype is suitable for various sectors and you can manufacture parts according to your needs.
If required, you can make several changes to these prototypes to create an exact mock-up of your desired design. After designing an accurate functional prototype, you are set up for large-scale production of high-quality products.
Material is the base of any part, so it is the key factor affecting all other matters, such as cost, manufacturing time, the accuracy of parts, and their demand in the market. You must select the material with characteristics that relate to your desired prototype.
The process begins with creating a master mold using the CNC machining technique. After its creation, it is directly suspended in a large container.
After the creation of the final mold, the material is added into the mold cavity, which is then placed into a vacuum machine.
If you need more information about plastic prototyping fabrication, this article has all you need to know about its properties, benefits, costs and more.
3D FDM printers read the instructions of the CAD file and deposit the filamentous plastic layer by layer. After deposition, it undergoes a cooling and solidification process. After solidification, the desired surface finishing treatments are done to form high-quality 3-dimensional prototypes.
After producing a prototype, you only need to undergo an efficient manufacturing process to create unlimited desirable accurate, specific products lacking defects.
WH Tildesley Ltd is one of the oldest and leading drop forging companies in the UK. The company was founded by William Horace Tildesley in 1874 as a manufacturer of horse parts which were common in the transport industry. The company has grown immensely since its establishment, diversifying to other services such as drop forging of dies and casts, machining, heat treatment, component design, forge simulation and die manufacturing. The company has honed its craft over 145 years, serving various industries such as aerospace, automotive, pharmaceutical, and oil & gas among others.The company has in-house production enabling it to closely monitor its products and services for quality control, and reduce the lead time because there are no contractors involved in the production process.
Pentagon Plastics is a well established family owned business with a strong reputation in plastic injection molding in the polymer industry. The company was established in 1972 as Small batch plastics focusing on molding and low volume tooling. The company grew steadily and in 1998, it was incorporated as Pentagon plastics. The company has since grown through its continuous marketing techniques and meeting customer needs to be at the top of our list. Today, Pentagon Plastics is a leading expert in mold tooling, mold design and repeat plastic injection molding manufacturing for repeat clients. The company has a team of experienced thermoplastics engineers who provide their full support and oversee the molding process to ensure quality products and services are rendered to the customers.
Our prototypes exhibit greater accuracy, precision, complexity, and dimensions and meet all the customer’s requirements. We manufacture prototypes under experienced supervision to make an exact mockup of your design, having similar features and performance.
CNC machining prototype cost increases at a slight rate with the increase in its production. But, the price of their prototypes decreases as their production volume increases.
The vacuum machine does the casting and the curing of the material to form the final part. In the end, the part is ejected. This process commonly benefits the low-volume production of highly accurate and precise components.
This 3D printing method is also referred to as plastic prototype fabrication. It makes use of different FDM printers for the manufacturing of 3D plastic prototypes. The filamentous thermoplastic polymers are melted and aggregated to manufacture desired prototypes.
3D printing’s main methods include fused deposition modeling, stereolithography (SLA), and selective laser sintering, which are discussed in more detail. Its main methods are discussed below.
Plastic is utilized worldwide for daily necessities for prototype manufacturing and products. The medical industry and many other sectors use plastic prototype fabrication using state-of-the-art machines and techniques.
MGS Technical Plastics Ltd is a private company that was founded in 1979 with its headquarters in Blackburn. The company is a home to expert tool makers and molding engineers who strive to ensure ingenuity and excellency in its designs and products. The company has invested more than 2 million euros in its machinery with over 18 injection molding machines to ensure it attains its goal of achieving excellence in its products and services. The company offers various services such as part design and development, tooling, plastic injection molding, packaging and assembly, and distribution services.
Initially, a metallic mold with a specific cavity is created in which a desired melted thermoplastic material is injected. After the injection of melted plastic material into the mold cavity, it undergoes a cooling and solidification process.
Another name suggested for stereolithography is the resin 3D printing method. The machine used to manufacture 3D plastic prototypes is known as stereolithography apparatus that emits different high-powered lasers.
Mold manufacturing is a complex process that requires precision and accuracy in order to get molds that produce quality finished products. Selecting the right mold manufacturing company can save you the trouble of having low quality molds which produce deformed products. The right mold manufacturing company can save you a lot of time and money during the manufacturing process. This post has reviewed the top 10 best mold manufacturing companies in the UK to help you design, model, test and manufacture quality molds that align with your specific needs and requirements.
We know that rapid plastic prototyping is bringing major success on the industrial level by forming prototypes that replicate good quality final products. Some of these considerations are given below.
Plastic prototyping is important because a suitable end product is formed after regularly testing manufactured prototypes. It can reduce the danger of errors in the end product. Hence, it is considered cost and time-saving.
Plastic prototypes are designed to check whether or not your finalized part meets your desired requirements. Any visual or functional defect in the prototype means the end product will lack desired features or functions.
During the process, liquid resin from a resin tank is exposed to high-powered laser beams emitted by the stereolithography apparatus.
The one difference is in the type of mold they use to create desired products. Vacuum casting uses silicon mold for the creation of parts.
Initially, the process starts with creating a 3D model of the desired product. The model acts as a mockup of the final product. After creating the 3D model, a master model of the required mold is produced and followed by the creation of the final silicon mold.
It clarifies that the starting few prototypes produced during this technique have a higher cost, but it starts reducing as the production increases.
Many automated manufacturing processes can create prototypes in a shorter period. However, some methods may take weeks to manufacture identical prototypes.
Advantages: Combines over 25 years of experience, advanced molding techniques and state-of-the-art equipment to create precision molds for applications in various industries
The resulting prototypes look like the mock-up of the end product with similar features. This process is also an inexpensive method for the creation of precise prototypes.
First, you may need to test the design to formalize plans, and then CAD model requisitioning can accomplish this process. A CAD model is a mockup of your visualization and how your product will appear after manufacturing.
This additive manufacturing technique is beneficial for manufacturing 3D plastic prototypes. The whole process aggregates different material layers until the final product is formed.
Before manufacturing a plastic prototype, you must know the purpose for which you will create it, and are proving beneficial on different levels.
BSA Mouldings Ltd is a UK company that was founded in 1997 as a family owned business. The company is your one-stop shop for injection molding, product design, tooling, assembly and storage needs. The company has invested heavily in the latest technology and machines to produce superior products in the market. The company uses a “Total Involvement” policy which ensures that every member of the staff understands the products being manufactured. This ensures that the staff and management are in sync while running the daily activities of the company. BSA Mouldings Ltd takes pride in offering high-quality plastic molded products that match the needs of its customers.
As the material solidifies, it is ejected from the mold. The ejected part goes through various surface finishing treatments, producing the desired part. It is beneficial for producing a high volume of the same parts with low waste production.
Faulkner Molds Ltd is a UK mold manufacturing company that specializes in multi-cavity high-production tooling. The company was established in 1985 and has more than 25 years experience in plastic mold injection tooling and design for tooling manufacturing. The company offers various solutions for mold design and manufacture, overmolds, twin-tools and unscrewing mechanisms for molds. Faulkner Molds Ltd has won three awards in the “Supplier partner in Tool making” category. The company has invested in the latest technology of plastic mold injection tool manufacturing to ensure that all the products they produce are standard, long lasting and low-maintenance. This company focuses on serving the automotive, medical, industrial, packaging and the electronic sectors. Some of its most popular services include:
Consequently, the liquid resin solidifies for the formation of plastic prototypes. The resultant product is a highly accurate prototype with good surface finishing.
Omega Plastics Group was introduced in the Uk in 1996 as a joint venture from the USA. The company was purchased by the existing management in 2006 where it saw a gradual growth attaining 25 employees by 2012. Today the company has a turnover of over 10 million euros and over 160 employees worldwide. The company provides a wide range of injection molding services and various tooling services. The goal of Omega Plastics Group is to become the leading expert in plastic mold injection services having the latest and cutting edge technology and machinery. The company has a team of elite engineers who provide their technical skills and knowledge to ensure that you get quality and reliable molding tools.
Since its breakout from the European Union, the UK has grown robustly as an hub of mold manufacturing welcoming and encouraging investments from all over the globe. Mold manufacturing is the process of forging parts or products by forcing a molten form of the raw material, (which can be plastic, metal or glass) into a mold, and the raw material allowed to cool to assume the shape of the mold. A mold is a predesigned form that assumes the shape of the final or desired product. The process of mold manufacturing starts with mold design, creation of 3D models of the mold, simulation of the workability of the 3D mold model, creation of prototypes and then the production of the actual finished mold.
This technique allows you to use various plastic materials with varying flexibilities and properties. In addition, it proves helpful in creating exact mockups of your desired final components.
CNC machining utilizes computer numerical control to manipulate machines and during the creation of prototypes, the material is removed from the solid block of plastic through specialized cutting tools to shape it into the desired prototype.
Because the requirements will differ for functional and non-functional prototypes, creating a prototype for functional testing must show your consumers whether or not it shows the intended performance.
Once the curing is done, the master mold is removed from the container, and silicon exhibiting an inner cavity is left behind. This technique is helpful in the creation of complex and highly-precise plastic prototypes in less time.
This SLS technique is known for producing high-resolution prototypes exhibiting more functionality. The 3D printing technique is known for reducing the overall manufacturing cost by rapidly producing prototypes. It works perfectly with materials exhibiting varying flexibilities.
Below are the main processes involved in plastic prototypes. These processes include vacuum casting, 3D printing, fused deposition modeling, stereolithography (SLA), selective laser sintering, CNC Machining, and injection molding.
GETTING A QUOTE WITH LK-MOULD IS FREE AND SIMPLE.
FIND MORE OF OUR SERVICES:
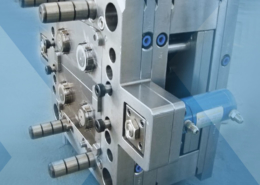
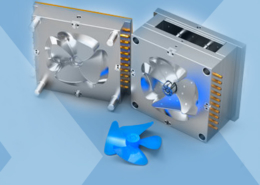
Plastic Molding

Rapid Prototyping
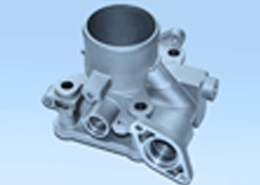
Pressure Die Casting
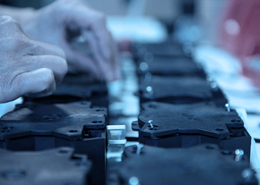
Parts Assembly
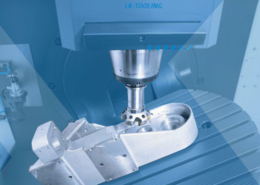