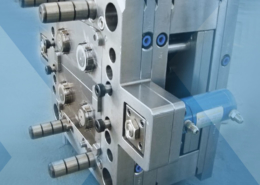
Precision injection molding experts | SCHOTT MINIFAB - precision injection
Author:gly Date: 2024-10-15
A: Polycarbonate has excellent qualities such as being transparent, high impact resistance, and stable thermal properties. These advantages have led to its use in production of robust and multipurpose molded parts.
From my point of view polycarbonate injection molding plays an important part in consumer electronics production including gadgets such as phones. Thus this light yet durable material is commonly chosen for manufacturing different smartphone cases, tablets’ casings or laptop’s shells etc.. The ability to absorb shocks well makes them a favorite among gadget makers because these things are subjected daily wear hence might easily break down if not shielded inside them by hardwearing substances like this one. Besides this it possesses features that facilitate easy shaping into intricate forms especially when crafting sleek modern looking designs that appeal to end users. Hence it comes forth that what makes polycarbonate such an invaluable component in consumer electronics is the combination of reliability with flexibility plus aesthetical options which designers are given access here.
Precision Machining: Molds are created using advanced machining techniques, including CNC (Computer Numerical Control) machining. This precision ensures that the molds’ cavities and details are reproduced accurately, down to the finest tolerances.
Precision injection molding is a highly accurate plastic manufacturing process. It involves injecting molten plastic material into meticulously crafted molds to produce components and products with extremely precise dimensions and high quality. This process requires strict control and precise mold design to ensure that the final products meet exact size requirements and have no defects. Precision injection molding is typically used in applications that demand high levels of precision and repeatability, such as the manufacturing of medical devices, automotive parts, electronic components, and aerospace components. This manufacturing method is essential for meeting stringent quality standards and highly precise design requirements.
A: The PC injection moulding technology entails regulating temperature and pressure correctly to enable the complete melting and flow of polycarbonate material into molds. Also cooling and ejection are equally significant techniques to avoid defects as well as maintain product quality.
Rigidity: Rigidity refers to a material’s resistance to deformation under load. In some cases, parts must remain rigid to maintain precision, while in others, flexibility may be preferred.
Measuring accuracy: To maintain the high stability of plastic products, the amount of hot melt plastic injected into the mold cavity must be equal each time.
Shrinkage: Materials used in precision injection molding should have low and predictable shrinkage rates. Material suppliers provide data on shrinkage rates for different materials, allowing mold designers to compensate for this effect during mold design.
Material selection is a critical consideration in injection molding, as it profoundly influences the final product’s precision and characteristics. precision injection molding often involves specific requirements for materials to achieve the desired level of precision. Here are some of the specific material requirements and considerations:
Maintaining the right injection pressure is essential to achieve quality in the process of polycarbonate injection molding. Injection pressure ranges recommended by leading sources from the top 3 Google websites usually vary between sixty and one hundred fifty megapascals. It helps in achieving complete mold filling while minimizing stress-induced defects.
High-Quality Mold Materials: Molds used in precision injection molding are typically made from durable and heat-resistant materials such as steel or aluminum. These materials withstand the high temperatures and pressures involved in the molding process, ensuring longevity and consistency.
The manufacturing process of precision injection molding is the same as that of traditional injection molding. The main processes include 6 stages. They are the preparation of raw materials, material melting, mold filling, cooling, mold opening, and post-processing. Click here to learn more about the injection molding process. The difference is that precision injection molding has higher requirements for mold design, materials, technical parameters, etc. Next, let’s take a look at the technical parameter requirements of precision injection molding during the production process.
With respect to quality and uniformity, performance of the injection molding system has huge impacts on. For example, by keeping accurate control over parameters like temperature, pressure and speed of injections, the molten polycarbonate will be distributed uniformly within the mold cavity. Moreover, these machines may also have automatic systems for monitoring or adjusting these parameters that make them more precise while minimizing chances of failure.
Precision injection molding stands out as a manufacturing process renowned for its multitude of advantages, each contributing to its significance in the manufacturing landscape.
Type: Academic Journal Article Summary: Published in the Journal of Polymer Engineering, this peer-reviewed article explores recent advances in polycarbonate injection molding technology. The study delves into innovations in material formulations, process optimization, and the development of new additives that enhance the performance and durability of molded parts. The research includes case studies and experimental data, providing scientifically validated information on improving the efficiency and quality of polycarbonate injection molding. This source is particularly relevant for researchers, engineers, and industry professionals seeking cutting-edge knowledge and technical data.
As we know, injection molding mold and machine are two key components in the injection molding process. Compared with traditional injection molding, precision injection molds, and machines have higher standards. In the next parts, we will learn what are the special requirements for precision injection molding molds and machines.
High Cavity Dimensional Accuracy: Achieving high dimensional accuracy within the mold cavity is crucial. Every contour, every corner, and every detail must align precisely with the desired specifications.
Precision injection molding finds a multitude of applications across a wide range of industries, each benefitting from its ability to deliver high-quality, consistent, and precise components. Here, we explore some key sectors where precision injection molding is crucial:
Type: Online Article Summary: This detailed article from Plastics Technology provides comprehensive guidelines on polycarbonate injection molding. It covers essential aspects such as material properties, processing parameters, and troubleshooting tips. The article also includes best practices for optimizing mold design, temperature control, and cycle times to achieve high-quality results. This source is highly valuable for both beginners and experienced professionals in the plastics industry, offering practical insights and expert recommendations for successful polycarbonate injection molding.
Plastics are a versatile class of materials used extensively in precision injection molding. They encompass a wide range of options, including polyethylene (PE), polypropylene (PP), polystyrene (PS), and polyvinyl chloride (PVC). Thermoplastics like polyethylene terephthalate (PET), polycarbonate (PC), and acrylonitrile butadiene styrene (ABS). These materials are prized for their dimensional stability and precision.
Investing in an efficient and reliable injection molding machine not only improves production speed and consistency but also minimizes waste and operational costs. As a result, selecting right machinery and maintaining it properly are vital for successful polycarbonate injection moulding operations which make optimum outcomes attainable.
Type: Manufacturer Website Summary: SABIC, a leading manufacturer of polycarbonate resins, offers a comprehensive technical data sheet and processing guide for their Lexan polycarbonate resin. The guide includes detailed information on material properties, recommended processing conditions, and application-specific considerations. It also provides tips on mold design, cooling systems, and post-processing techniques to achieve optimal results. As a direct source from a reputable manufacturer, this guide ensures accurate and industry-specific information for users involved in polycarbonate injection molding.
Dimensional Stability: Materials should exhibit excellent dimensional stability, especially when exposed to temperature variations.
By carefully monitoring and adjusting the above parameters, I am able to make high-quality polycarbonate parts with excellent accuracy and lower defect rates.
The medical industry relies on precision injection molding to create life-saving and life-improving devices with stringent quality standards. Applications include:
Have you ever noticed a whitening phenomenon in PVC product whitening? Some of your transparent PVC products, like shower curtains
Precision injection molding plays an indispensable role in the automotive sector, providing components known for their accuracy and reliability. Key applications include:
The manufacturing industry is associated with the Polycarbonate injection molding; a process that produces durable and versatile plastic products. This guide provides an all-encompassing view of polycarbonate injection molding techniques, advantages, and applications. This complex field can be navigated by understanding basic properties of polycarbonate materials and complexities of the molding process, which are elaborated in this guide. Either you are a professional who has been doing this for some time or a beginner looking to improve on skills, this article is a great resource to master over polycarbonate injection molding. Essential elements of the process such as material selection, equipment requirements, common challenges, and practical tips for achieving optimal results are outlined in this text.
The injection mold structure and design directly influence various aspects of the final product, including its dimensional accuracy, surface finish,
Precision injection molding is a fundamental process in modern manufacturing, known for creating accurate and intricate parts and components. Its importance in the manufacturing industry cannot be overstated. This method plays a vital role across various sectors. Let’s explore precision injection molding and its profound impact on the manufacturing landscape together.
In the medical field, polycarbonate injection molding is widely used because of its toughness, transparency, and compatibility with living tissue. For example, it can be used to make surgical tools, diagnostic units, blood oxygenators and IV parts. The strength of the plastic and its ability to withstand sterilization methods make it a good choice for reliable and safe medical devices. Importantly, its clearness allows observation of direct fluid flow which is significant in some types of diagnostic aids.
Whether you require components for the medical field, automotive industry, electronics sector, or any other application demanding excellence, Zhongde is your precision injection molding partner of choice. Contact us today and let’s bring your precision molding needs to life.
Polycarbonate is known for its exceptional strength and durability, which make it a good choice for molding. It has high impact resistance and does not crack or break under heavy loads. In addition, polycarbonate retains this property over a wide range of temperatures to ensure that the molded parts are reliable even under difficult conditions. However, it toughness and longevity leads to robust production pieces that can withstand heavy use while lengthening product life.
Complex Geometries: Many products produced through precision injection molding feature intricate and complex designs. Molds are tailored to accommodate these intricate geometries, allowing for the precise replication of intricate parts and components.
A: While looking for a reliable service provider specializing in injection molding using polycarbonate consider those with experience in polycarbonate processing, strong quality management systems, and positive customer feedback. It is important to ensure that your choice can handle this type of material better.
Smooth Cavity Surfaces: The interior surfaces of the mold cavity must be exceptionally smooth. Smooth cavity surfaces ensure that the injected material flows evenly and without obstruction, resulting in defect-free products.
A: Injection molding uses various classes of polycarbonates such as standard, optical, flame-retardant grades depending on application requirements. Each kind has unique attributes best fit for given injection molded parts.
In the world of manufacturing, precision is not just a goal; it’s the foundation upon which innovation and quality are built. Precision injection molding stands as a testament to this commitment to excellence. Throughout this post, we’ve delved into the intricacies of precision injection molding, uncovering its vital role in modern industry. Precision injection molding is more than a manufacturing method; it’s the embodiment of precision itself. It ensures that every component produced adheres to the strictest standards of quality, dimensional accuracy, and reliability.
From my experiences with polycarbonate injection molding processes, controlling wall thicknesses and melts temperatures are very fundamental. Making sure that there is an even wall thickness over the part eliminates issues such as sink marks, warpage, or uneven cooling that could affect its structural soundness or aesthetic appearance. An optimum thickness for polycarbonate components would be around 2.5 mm on this basis. Furthermore, it is important to monitor melt temperatures, maintaining them at between 250° C to 300° C so as to prevent thermal degradation of the melt flow’s consistency in order for material not lose its original properties through overheating. With these parameters under control, I am able to manufacture reliable high-quality polycarbonate parts that satisfy strict requirements of today’s consumer electronics industry.
Injection molding flow marks are a common injection molding defect. While flow marks generally do not influence the structural integrity
Precise Positioning Between Templates: In multi-cavity molds or molds with moving parts, precise positioning between templates is essential. This ensures that each part produced is consistent and free from defects.
A: Among the many uses for which it can be applied include optical lenses, medical devices, automotive components, consumer goods, electronics housings etc. The implications of versatility and strength on polycarbonates for these industries is overwhelming.
High-Pressure Capability: Precision often requires high injection pressures to fill intricate mold cavities completely. Machines designed for precision can exert the necessary pressures without compromising accuracy.
These steps are carefully regulated so as to produce good quality parts made of polycarbonate having excellent dimensional accuracy and surface finish.
Injection Speed Control: Controlling the speed at which molten material is injected is crucial for avoiding defects. Precision machines allow for fine-tuned control of injection speed.
In the aerospace and aviation industries, precision is paramount for safety and performance. Precision injection molding is used for:
A: In the injection molding technique for polycarbonate, its plastic form is melted and pushed into a mold cavity through an injection molding machine. After that, it cools down and solidifies to get the final shape where it gets removed from the mold.
To ensure high-quality, error-free polycarbonate parts that are efficiently made with precision, these technical parameters are necessary.
From my research on top three websites regarding injection molding, polycarbonate injection molding process entails some key steps. First, the polycarbonate raw material is fed into an injection molding machine where it heats up and melts. This molten material is then shot under pressure at very high speeds into a precisely formed mold cavity. The mold is normally cooled so that the polycarbonate solidifies into the shape desired. Once enough cooling has taken place, the molded part is ejected out of the mold. Parameters such as temperature control settings, injection pressure points and cooling periods are carefully regulated in order to produce quality parts without defects. By this method complex detailed components can be manufactured in large quantities with uniform accuracy
A: In polycarbonate injection molding, polycarbonate plastic is melted and injected into a mould to create different parts. It is widely used in making plastic parts that are durable and of high quality.
GOLDSUPPLIER.COM expands globally, offering quality business opportunities, cost savings, convenience, and expertise in international trade. Trusted and recognized internationally.
Cost-Efficiency in Large-Scale Production: The repeatability and efficiency of precision injection molding result in faster production cycles. This is especially advantageous when manufacturing high volumes of components.
The defining feature of precision injection molding is its ability to achieve exceptionally tight tolerances. Precision injection molding products adhere to tolerances as fine as 0.01mm to 0.1mm. This level of precision ensures that each part or component produced is almost identical, meeting even the most exacting specifications.
A: Some cons associated with this process include expensive materials used for production purposes; environmental and other process variations sensitivity; strict need for temperature regulation among others. When not handled properly during moulding however , it may also suffer from stress cracking.
Advanced Control Systems: Precision injection molding machines are equipped with advanced control systems that maintain precise temperature, pressure, and injection speed. These controls ensure consistency in each molding cycle.
From my point of view when considering design flexibility and precision offered by polycarbonate injection molding there isn’t an outstanding material for complex detailed designs like this one.it may be observed, therefore that it could be employed in intricate details with great accuracy/ preciseness such as small molds used in automotive industry which require several molds before achieving quality output unlike those made from other materials such as aluminum steel among others whose melting point are very low thus requiring care when designing because poor designs may lead into damages during chilling process but using PC will minimize these challenges.I think this would benefit various industries including automotive manufacturing, electronics (i.e., cell phone covers), medical device production (i.e., catheter tubing), where high precision and accuracy are crucial. In conclusion, polycarbonate is a good choice for many complicated applications because it can make parts that are highly specific and durable.
I believe that polycarbonate injection molding is a must for many automobile parts due to their high tensile strength, resistance to heat and reduced weightiness. This material is often employed in making headlamp lenses, interior items as well as other applications located under vehicle bonnet. These items have to withstand extreme temperatures and impacts without deteriorating since they have to meet strict safety requirements. These parts are also very flexible so as to suit any design ideas by engineers who always strive to improve both functionality and aesthetics of vehicles. Polycarbonate therefore becomes an important material in automotive industry due to its combination of durability and versatility.
Optimizing the mold temperature and injection speed is an important step in the polycarbonate injection molding process. Maintaining ideal temperatures within the mold ranging from 80°C to 100°C is essential to ensure a uniform smooth surface finish and avoid defects like shrinkage or warping. It is also of significance to balance injection speed since fast one may cause excessive shear stress leading to incomplete filling up the mold or material degradation. These parameters, when properly regulated by manufacturers of polycarbonate parts can enhance mechanical performance as well as aesthetics thus enhancing efficiency and consistency throughout production.
Polycarbonate is a highly durable, transparent and versatile thermoplastic. It is amorphous in nature which makes it resistant to impact and its optical properties are great making it a good choice in various industries. It can also withstand high temperatures and is naturally fire retardant thus appealing to applications with stringent safety standards. Additionally, the material can be easily shaped hence making it ideal for injection molding processes that are intricate and precise. The fact that it has a combination of strength, transparency as well as thermal stability makes polycarbonate the preferred material for many types of products ranging from consumer electronics to automotive parts.
Some of the key advantages I see with polycarbonate injection molding are resistance to impact as well as sustained use in high temperature environments. The impact resistance of polycarbonate is unmatched ensuring a tough element necessary in products that undergo extensive demand and harsh conditions. For example, safety gears or electronic housings are immensely valuable if they can absorb and take severe impacts without breaking apart. Moreover, polycarbonate performs extraordinarily across broad temperature ranges: it maintains its properties even at extreme temperatures thus making it suitable for different applications depending on environment. In other words, the combination of temperature stability and impact resistance enhances endurance of materials produced from polycarbonates.
Balance degree of fixed and movable platens A: less than 0.03mm when the clamping force is zero B: less than 0.005 mm when the clamping force is maximum;
Exceptional Accuracy: Tolerances as fine as 0.01mm to 0.1mm are routinely achieved. Each product mirrors the exact specifications of the master mold, ensuring uniformity and reliability.
The injection molding machine is an important aspect of the injection process and it is a key factor in manufacturing high-quality polycarbonate parts. It basically blends mechanical together with hydraulic mechanisms to ensure accuracy and effectiveness. The machine consists of two main units: an injection unit and a clamping unit. In this case, the first one melts the polycarbonate material and injects it into a mold whereas the second holds this mold tightly throughout injection as well as cooling stages.
Precision injection molding excels in producing parts with high repetition accuracy. Repetition accuracy refers to the consistency of dimensions and properties across multiple parts. In precision injection molding, product weight deviation is minimal, typically less than 0.7%. This means that each piece emerging from the mold closely matches the one before it. This level of consistency is crucial in industries where reliability and uniformity are paramount.
A: For information on Polycarbonates and Injection Moulding you may refer professional associations’ journals; manufacturers’ websites or industry’s technical resources. Industry conferences or workshops are also good sources of knowledge concerning new developments in Polycarbonate Injection Moulding Techniques.
A: These include mold temperature control parameters like screw barrel heat setting temperature cooling time at which material enters the mould at what speed injection should take place for optimum part quality. For instance determining necessary conditions required to achieve good product from polymers like PC.
For various reasons, injection molding is known to be the best method of making polycarbonate components. One of them is that it allows the production of precise and detailed parts which are important especially in electronic and automotive industries. Moreover, this process is highly efficient as large numbers of parts can be produced uniformly with minimal wastage.
It’s essential, first and foremost, to choose a starting point for injection pressure that will be sufficiently high for completely filling a mould cavity. The data shows that it is advisable to start with a pressure of roughly seventy megapascals and then adjust depending on part quality and fill time. A low pressure can result in incomplete filling or short shots whereas excessive flash or stresses may occur if the pressure is too high.
Once filled, the mold should have a holding pressure between thirty megapascals and seventy megapascals so as to compensate for material shrinkage when it cools down and solidifies. This holding pressure need not exceed the initial injection pressur.
Consistency: Whether producing one part or one million, precision injection molding maintains consistency. Each piece is virtually identical, free from defects, and meets stringent quality standards.
To achieve optimum results in polycarbonate injection molding, several key process parameters must be accurately controlled:
GETTING A QUOTE WITH LK-MOULD IS FREE AND SIMPLE.
FIND MORE OF OUR SERVICES:
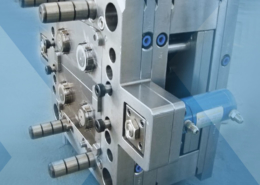
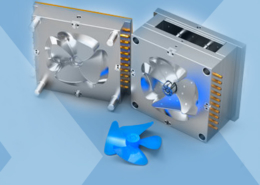
Plastic Molding

Rapid Prototyping
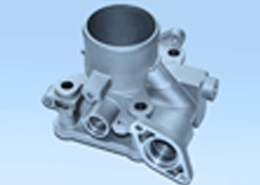
Pressure Die Casting
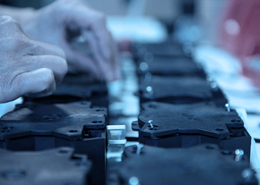
Parts Assembly
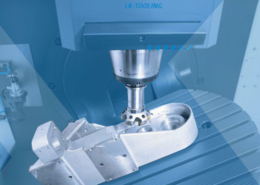