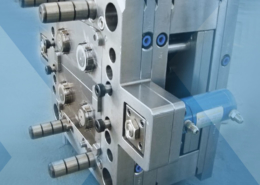
PPE Injection Molding: Safeguarding Lives Through Precision Manufacturing
Author:gly Date: 2024-06-08
In recent times, the global demand for Personal Protective Equipment (PPE) has surged dramatically, driven by the ongoing pandemic and heightened awareness of workplace safety. At the heart of PPE production lies the process of injection molding, a sophisticated manufacturing technique that enables the mass production of intricate and high-quality protective gear. This article aims to explore the intricacies of PPE injection molding, shedding light on its significance, processes, materials, applications, and future prospects.
Significance of PPE Injection Molding
PPE injection molding plays a pivotal role in safeguarding frontline workers, healthcare professionals, and individuals against occupational hazards and infectious diseases. With its ability to produce complex designs with precision and consistency, injection molding ensures that PPE meets stringent quality standards and regulatory requirements.
Moreover, the scalability of injection molding allows for rapid production ramp-up during times of crisis, ensuring uninterrupted supply chains and timely distribution of essential protective gear.
The Injection Molding Process
The process of PPE injection molding begins with the design phase, where engineers develop 3D models of the desired protective equipment using Computer-Aided Design (CAD) software. These designs are then translated into molds, which are precision-machined to exact specifications. Molten thermoplastic materials, such as polypropylene or polycarbonate, are injected into the molds at high pressure, where they cool and solidify to form the final product.
Quality control measures, including visual inspection, dimensional analysis, and material testing, ensure that each piece of PPE meets required standards before distribution.
Materials and Properties
The choice of material for PPE injection molding depends on the specific application and desired properties of the protective gear. Common materials include polypropylene, ABS, polycarbonate, and polyethylene, each offering a unique balance of strength, flexibility, and chemical resistance.
For example, face shields and goggles require materials with excellent optical clarity and impact resistance, while respiratory masks demand materials that are breathable, hypoallergenic, and resistant to moisture and contaminants.
Applications and Industry Impact
PPE injection molding finds applications across a wide range of industries, including healthcare, manufacturing, construction, and hospitality. In the healthcare sector, it is used to manufacture face masks, face shields, gloves, and gowns, providing vital protection against infectious diseases for medical personnel and patients alike.
In manufacturing and construction, PPE such as safety helmets, goggles, and earplugs are essential for preventing occupational injuries and maintaining workplace safety standards. The widespread adoption of PPE injection molding has significantly contributed to reducing workplace accidents and mitigating health risks in various industries.
Future Prospects and Innovations
Looking ahead, the future of PPE injection molding is characterized by ongoing innovations in materials, design, and production techniques. Advanced materials with enhanced antimicrobial properties, improved breathability, and eco-friendly attributes are being developed to meet evolving safety requirements and sustainability goals.
Furthermore, the integration of digital technologies such as Artificial Intelligence (AI), Internet of Things (IoT), and Additive Manufacturing promises to revolutionize the PPE manufacturing landscape. Real-time monitoring of production processes, predictive maintenance, and customized design solutions will optimize efficiency, reduce waste, and ensure the continuous supply of high-quality protective gear.
Summary:
In summary, PPE injection molding serves as a cornerstone of modern healthcare and workplace safety, providing essential protection against hazardous environments and infectious diseases. With its precision, scalability, and versatility, injection molding enables the efficient production of high-quality protective gear that meets the evolving needs of diverse industries. Embracing innovation and leveraging emerging technologies will further enhance the efficacy, sustainability, and accessibility of PPE, ensuring the well-being and safety of individuals worldwide.
GETTING A QUOTE WITH LK-MOULD IS FREE AND SIMPLE.
FIND MORE OF OUR SERVICES:
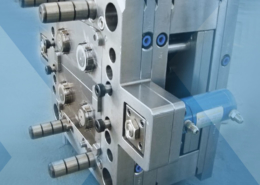
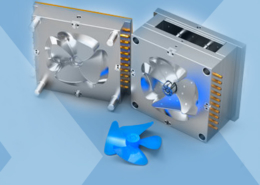
Plastic Molding

Rapid Prototyping
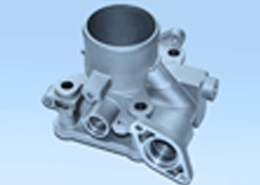
Pressure Die Casting
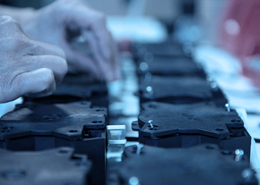
Parts Assembly
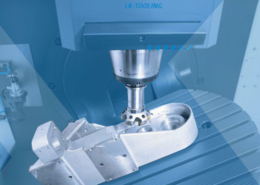