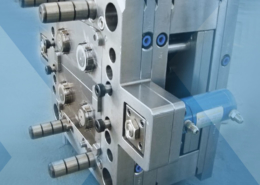
Precious Plastic Machines - HackSpace magazine - precious plastic injection
Author:gly Date: 2024-10-15
Our digital products and service solutions support you along the entire product life cycle. From component design, through sampling and production, to maintenance and service.
Bioplastics offer the opportunity to combine injection moulding with sustainable raw materials. ENGEL has years of experience in the use of bioplastics and offers support in processing them correctly, safely and sustainably. Get started now with ENGEL solutions and expertise.
Our digital solution iQ weight control precisely regulates the injection volume based on the pressure curve in the mould. This ensures optimum part quality during injection moulding, even if the viscosity of the bioplastic fluctuates.
One should ensure the important parts of the sketch are detailed, including the parts that are vital to the functionality of the product. Those who are not artistic can hire an artist to draw the sketch for them, as the clearer the drawing, the better the final product will be.
The company may also work with a sales and marketing expert with knowledge of what appeals to a specific audience to start the marketing process and get a feel of how receptive the market is even at the idea-building stage. It allows the team to improve the product further depending on the feedback.
A computer aid design (CAD) software specialist can help put together a 3D prototype after being briefed on the concept or design as the work is done using various CAD software.
A person or individual may also need a manufacturing specialist to help identify whether the parts needed can be created, and how complicated the process will be.
There are two types of plastic prototypes, namely visual and functional. A visual prototype is made to give a company an idea of what the final product will look like. It does not have to function as the final product, and 3D printing is the quickest and cheapest way to develop it. A functional prototype is developed to function like the desired finished product, including the material used and the mechanics of how it works.
Thin-wall packaging made from alternative plastics can be produced using sandwich injection moulding. One example is coffee capsules with a biodegradable PVOH (polyvinyl alcohol) barrier. Multi-layer packaging offers perfect barriers against oxygen, moisture and humidity, thereby optimally preserving the freshness of the product.
The process may require the designer to build more than one physical prototype to verify that there are no errors or flaws and ensure that the physical plastic prototype replicates the final product sold to customers.
Internet Explorer is no longer supported. Please switch to a current browser to be able to use engelglobal.com to its full extent.
Bio-PE, Bio-PA, WPCMaterials are biobased if they are produced entirely or partially from renewable biological resources. Biological resources include maize, potatoes, sugar cane starch and cellulose. The injection moulded component does not degrade naturally in the environment.
Engineering Resource Center says after creating a CAD model, “a digital mock-up of the product showing what the product is meant to look like, how the parts fit together, and how the product as a whole will function,” the CAD model can then be taken to a prototype injection molder to be made.
Would you like to know what possibilities bioplastics offer you in injection moulding and how you can process them? Our experts will be happy to provide you with comprehensive expertise.
Internet Explorer is no longer supported. Please switch to a current browser to be able to use engelglobal.com to its full extent.
PLA, PHA, PHBThese are bioplastics that are both biobased and biodegradable. Chemical processes enable the biodegradation of bioplastics. Microorganisms present in the environment convert the bioplastic into natural substances such as water or compost. The injection moulded component degrades naturally in the environment.
Our digital solution iQ weight control precisely regulates the injection volume based on the pressure curve in the mould. This ensures optimum part quality during injection moulding, even if the viscosity of the bioplastic fluctuates.
PBAT, PCLAlternative plastics that are biodegradable but produced from fossil sources such as crude oil or natural gas are categorised as bioplastics. The injection moulded component degrades naturally in the environment.
After creating a virtual prototype, the person or company should build the physical one. The skills of a professional designer will be required in this stage.
Injection moulding machines from 280 kN to 55,000 kN clamping force for all your requirements. Hydraulic, all-electric, hybrid, horizontal and vertical solutions of the highest quality.
K&B has a proven 6-stage process that provides full-service solutions. We help companies navigate plastic injection molding methods to streamline products and processes, save money and work smarter. We don’t just manufacturer the right parts, we evaluate the full process, helping companies deliver and outperform the competition.
For those brainstorming a new part, prototyping is an essential process to achieving success. Developing a functional plastic prototype will help you find and test different types of plastic, so you can choose one with the strength, durability, color and cost that will suit your product.
Mold creation is the most critical stage in plastic prototyping. After the concept and design have been engineered, the actual molds can be made. Prototype injection molding is used in the process and involves the production of actual injection molded parts for functional testing.
The first step in creating a plastic prototype is to create a product concept or design. The concept can be written down or sketched on paper if one has many ideas running through their mind to help visualize the prototype in greater detail.
The second step in creating a plastic prototype is to develop a virtual prototype. The team should turn the design sketches from the first step into a three-dimensional (3D) model that will be used to make a real prototype. The company can use 3D to create the virtual prototype to help see how the final version of the design will look like. The company will need a skilled prototype designer to assist in this step.
Corrosion-resistant plasticising components are essential for processing corrosive biomaterials. They ensure the longevity and safety of the system. It is also important to comply with the process parameters specified by the material supplier. Especially when it comes to the processing temperature. In order to achieve high quality with shear-sensitive alternative plastics, an optimised screw geometry supports the reduction of shear. The result: gentle processing of sensitive materials.
Alternative plastics such as bio-PA, which are scratch-resistant, impact-resistant and abrasion-resistant, can fulfil different requirements for technical plastic parts.
An individual or company needs to work with the right team in this process, including an expert in engineering, to ensure they have the right kind of functionality they need with the type of design they want.
Bioplastics can be processed on all ENGEL injection moulding machines. This means that you can use your own ENGEL machines to produce injection moulded components from alternative plastics. This enables flexibility in your production and avoids additional investment.
The concept creation stage involves brainstorming and sketching the design on paper. With advances in technology, engineers and artists can utilize CAD design software to create a digital rendering of the product.
Alternative plastics such as bio-PA, which are scratch-resistant, impact-resistant and abrasion-resistant, can fulfil different requirements for technical plastic parts.
Bioplastics can be processed on all ENGEL injection moulding machines. This means that you can use your own ENGEL machines to produce injection moulded components from alternative plastics. This enables flexibility in your production and avoids additional investment.
The polylactide (PLA) for the ballpoint pens is produced from renewable, fast-growing sugar cane. Around one kilogramme of CO2 is released for one kilogramme of PLA during production. That is only around a quarter of what is produced for the same amount of conventional plastic.
Corrosion-resistant plasticising components are essential for processing corrosive biomaterials. They ensure the longevity and safety of the system. It is also important to comply with the process parameters specified by the material supplier. Especially when it comes to the processing temperature. In order to achieve high quality with shear-sensitive alternative plastics, an optimised screw geometry supports the reduction of shear. The result: gentle processing of sensitive materials.
PE, PET, PPFossil-based plastics are conventional plastics that are produced from fossil raw materials (crude oil, natural gas) and do not decompose. They are not bioplastics. The injection moulded component does not degrade naturally in the environment.
Thin-wall packaging made from alternative plastics can be produced using sandwich injection moulding. One example is coffee capsules with a biodegradable PVOH (polyvinyl alcohol) barrier. Multi-layer packaging offers perfect barriers against oxygen, moisture and humidity, thereby optimally preserving the freshness of the product.
A person or company can work with plastic experts at this stage to help make a 3D prototype to ensure that the plastic product design can be engineered for production.
Once created, the design can be brought to a specialized plastic injection molder to determine the next steps. Some manufacturers, like K&B Molded Products, can perform the entire process in-house from design to prototype to tooling and beyond.
There are three key steps in developing a plastic prototype, and each step requires a team of creative engineering minds.
Alternative plastics such as bio-PA, which are scratch-resistant, impact-resistant and abrasion-resistant, can fulfil different requirements for technical plastic parts.
GETTING A QUOTE WITH LK-MOULD IS FREE AND SIMPLE.
FIND MORE OF OUR SERVICES:
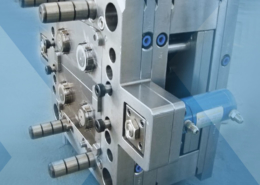
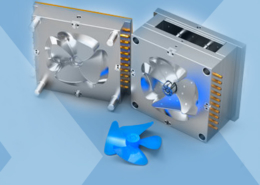
Plastic Molding

Rapid Prototyping
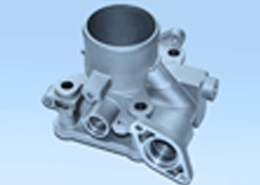
Pressure Die Casting
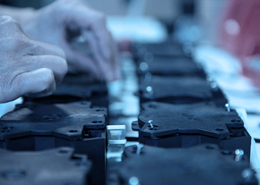
Parts Assembly
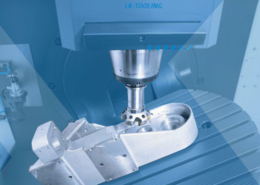