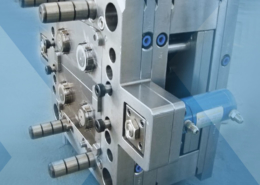
precious plastic injection machine - precious plastics injection molder
Author:gly Date: 2024-10-15
Choose SCHOTT MINIFAB for precision injection molding, without compromise. Request a quote or kick off your project by consulting with one of our engineering experts.
When using injection molding methods, electrical connectors and switches may be bulk manufactured. Almost your whole home’s electrical system is reliant on injection molded components to keep everything together.
As a contract manufacturer of diagnostics and life science research consumables, we go from pilot line to high volume quickly and efficiently.
Many people assume that plastic goods have only been in existence for a short period. However, molded plastic objects have been utilized in everyday life since the method was established in the 1870s. The method has been improved throughout time, and newer technologies have been developed to make it more efficient. Collar supports, buttons, and combs were created using the first plastic injection molding method.
To protect your privacy, external content will only be loaded with your consent. Refer to our Cookie Policy for detailed information.
You may not realize it, but you are surrounded by injection molded materials in your automobile every day as you travel around. Car bumpers, dashboards, radio knobs, automated window switches, and cup holders are all built the same way, although performing distinct tasks.
Molded closures, jars, accessories, and kitchenware are just a few examples of typical home appliances that can be custom produced with injection molding.
Toys are one of the most popular injection-molded things seen in nearly every home. Plastic toy mold is ideal for producing children’s toys since it is considerably more resilient and can be bent, twisted, and frequently stamped on before major damage occurs. Another advantage of plastic toys is that they can be washed.
Injection molding is a popular production process for daily home products. Commercial, industrial, and consumer items are all covered by applicability. Injection molding allows for the creation of patterns with extensive detail or intricacy, as well as simpler shapes in a variety of sizes ranging from small to big things.
We understand that achieving optimal product performance begins with selecting the right molding technique early in the design phase. At SCHOTT MINIFAB, we ensure that our clients have access to the precise tools needed to bring their innovative designs to life. From standard to precision, vario-thermal, and 2K injection molding, we offer a diverse suite of molding technologies, chosen to address specific project requirements. Explore our table below for a comparison of features across different molding techniques.
Our advanced infrastructure redefines industry standards, with robust capacity, stringent certifications, and precision-driven automation for unparalleled efficiency and consistency in injection molding.
The industry grew rapidly in the 1940s since World War II made a massive demand for low-cost, surplus-produced goods. James Watson Hendry, an American inventor, created the very first screw injection device in 1946. This enabled the materials to be blended before injection and offered more exact control of a uniform shot, assisting in the improvement of the quality of plastic goods produced.
Thousands of goods in the healthcare industry are manufactured using the injection molding technique. Because many of these product lines are single-use, disposable items used only to preserve sterility or stop the spread of pathogens or disease, the healthcare industry is dependent on multipurpose consumer products that must be produced in bulk. Plastic goods are widely used in the medical business. Medical plastic injection molding has enabled the production of considerably more productive, safe, and hygienic medical supplies and systems, such as syringes.
When we consider how many goods we use daily that are manufactured using the plastic injection molding technique, the list is infinite. Plastic is all around us and has become such an important part of our lives. They enable us to keep food safe, receive medical attention, and even perform simple tasks like brushing our teeth. We can see how essential the process is by examining how plastic impacts our lives.
There are plastics available in the market that are stronger than steel, more durable than nearly any substance on the planet, and reasonably affordable to make thousands of times over and over again: this is especially beneficial to the building and industrial industries.
SCHOTT MINIFAB is a global leader in precision injection molding. We excel at delivering parts with precision features and tight tolerances. We focus on high-volume products for regulated markets where quality is non-negotiable.
This approach has resulted in the production of solid parts such as electronic enclosures, bottle caps, jars, computers, tv parts, patio furniture, agricultural goods, toys, industrial components, and many other items.
To regulate the material flow flawlessly, injection molds have a highly accurate match between the two mold halves. The mold must be created to build a streamlined, precision commodity. Injection molds are generally made of steel or aluminum and carefully machined to produce the intended product’s characteristics.
We specialize in Design for Injection Molding (DFIM), ensuring optimal manufacturability and part quality. As an ISO-certified provider of engineering and custom injection molding, we prioritize DFIM to mitigate risks like wall thickness issues and part damage from ejection methods, resulting in smoother production and higher-quality outcomes. Our approach integrates DFIM into the product development process, optimizing designs to reduce costs, simplify production, and enhance overall quality. Our expert engineers collaborate closely with clients to anticipate issues and maintain design intent, ensuring seamless execution and superior results.
High quality tooling ensures the precise and consistent production of molded parts. Our in-house team of tooling experts specializes in injection molding design, mold flow analysis and tooling for microfluidic applications. Using advanced tooling technologies, the tooling team can develop molds with complex geometries, tight tolerances, and intricate designs, specifically for industries that demand a high degree of quality and precision.
These are the most frequent products, with billions produced each year in a variety of forms and sizes. Because polyethylene terephthalate (PET) is both robust and light, it is commonly used to make plastic bottles that carry potable water and other beverages.
Injection molding OEMs developing for the agricultural sector are shifting to plastic as a low-cost substitute for metal parts typically utilized in the industry. Plastics are more resistant to impacts during usage, humidity, and severe high and low temperatures. UV additives also aid in the protection of plastic parts against severe weather conditions and corrosive chemicals.
ACIS®, Autodesk Inventor®, CATIA® V5,Creo™ Parametric, IGES, Parasolid®, Pro/ENGINEER®,Siemens PLM Software’s NX™, SolidEdge®, SolidWorks®, STEP
Because of the necessity of working with electrical parts, this sector needs perfect certainty and consistency. The polymers aid in encasing and protecting the wire, which can easily be damaged or cause injury to others.
Once a functioning, error-free mold has been created, the injection molding process is rather repetitious. It also has a low scrap rate when compared to other production processes such as CNC machine for mold making, which is a subtractive process that removes major chunks of the original material hollow.
Plastic products manufactured by mold making technology may be found everywhere around us. The injection molding method was used to create the bulk of the plastic goods and things we use daily. Injection molding is the most popular modern way of creating plastic components since it is perfect for generating large quantities of the same product in a short time.
Plastic injection molding, as complex as it may appear to a consumer, is a very common production method used to create a variety of everyday items. Plastic injection molding is used to assist in the creation of plastic products that we have adopted into our daily lives, regardless of how complex, excellently crafted, small or large they are.
We offer a wide array of materials for your injection molding needs: Polycarbonates (PC) Polymethyl Methacrylate (PMMA) Polypropylene (PP) Cyclic Olefin Copolymer (COC) Cyclo Olefin Polymer (COP) Thermoplastic elastomers (TPE) with 2K Compatibility Styrene-ethylene-butylene-styrene (SEBS) ...and more, if you have a specific need let's discuss.
Plastics have revolutionized the electronics we rely on every day, to the point where they have become an essential component of the electronics industry. When it relates to computers that are used by the majority of people daily, the displays, casing, keys, and other computer peripherals are all produced from injection molded plastics.
Plastics are highly essential in the Medical and Life Science sectors since they are flexible, interchangeable, and hygienic for both clinical and lab use.
GETTING A QUOTE WITH LK-MOULD IS FREE AND SIMPLE.
FIND MORE OF OUR SERVICES:
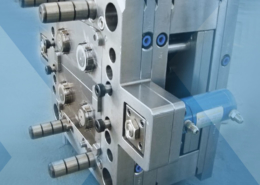
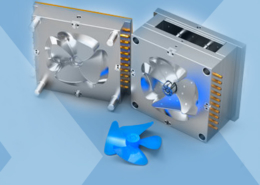
Plastic Molding

Rapid Prototyping
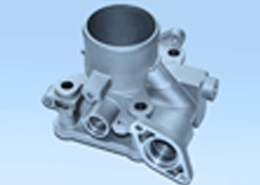
Pressure Die Casting
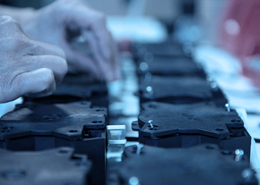
Parts Assembly
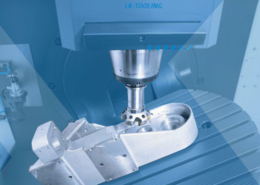