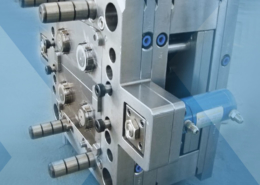
Precimax Plastics - Injection moulding and tooling in South ... - injection moul
Author:gly Date: 2024-10-15
A combination of peck drilling and cooling liquid should be used in order to allow the plastic to cool when being drilled. It is also advised to utilize drills with a thinned web to further restrict friction and heat generation. The hole should be drilled step wise, successively increasing the diameter of the drill and potentially expanded with a boring tool for an improved finish. An example of this would be attempting to reach a bore diameter of 55mm, first drilling with a ø10mm and ø25mm drill bit and finishing with either a ø55mm drill or completing with a boring tool.
To ensure efficient chip removal and prevent issues such as friction, heat build-up, and saw blockage, it is important to use a band saw, circular saw, or reciprocating saw with widely spaced teeth and adequate set. Proper clamping of the work table is also essential for preventing vibrations and ensuring smooth cutting. Combination blades with a 0° tooth rake and 3° to 10° tooth are generally the most effective for sawing in order to reduce frictional heat. That being said, hollow ground circular saw blades without set will yield smooth cuts up to 3/4” thickness.
PLEASE NOTE: This guide has been contracted from the experience of Tynic Automation’s Engineering Department. It is intended as a helpful suggestion in experimentation and should not be entirely relied upon. Any expenses caused as a result of this guide Tynic is not liable.
If a coolant is necessary during machining to ensure optimum surface finishes, adherence to close tolerances and to reduce material burn. Water soluble oil types are often found to be the most effective. Petroleum based coolant fluids my be suitable for some plastics, however, they can lead to environmental stress cracking in amorphous engineering plastics such as Polycarbonate or Acrylic. In these cases, pure water or compressed air is often the more suitable choice.
These guidelines are intended to provide a general overview for those unfamiliar with working with plastics, but it is important to note that the optimal machining conditions may vary depending on the specific part being produced. One key consideration when machining plastics is that they are generally softer than metals, which can make it more challenging to maintain precise tolerances during and after machining. Aiming for tolerances of +/- .05 millimeters for engineering plastic components, although it is possible to achieve tighter tolerances with certain materials that are more dimensionally stable.
When performing a large volume of machining, tungsten carbide tipped or diamond bit tools are often the go-to option, especially when working with glass or carbon fiber reinforced materials. That being said, carbon steel, high speed steel, and hard metal tools can also be effectively utilized.
If you encounter any issues during the machining process, such as undesirable surface finishes or unexpected material behavior, it may be helpful to refer to the troubleshooting quick reference for guidance on how to resolve them. By understanding the unique characteristics of plastics and using the appropriate machining techniques, you can achieve high-quality results in your work.
In comparison to traditional materials such as metals, plastics are usually softer, allow a higher feed rates and wear machines/tools significantly less. Despite this, they drastically differentiate when it comes to which plastics are easiest to machine. Common problems include surface burning, chipping, bowing out of tolerance, poor finishes and cracking.
GETTING A QUOTE WITH LK-MOULD IS FREE AND SIMPLE.
FIND MORE OF OUR SERVICES:
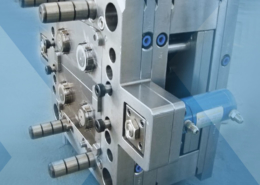
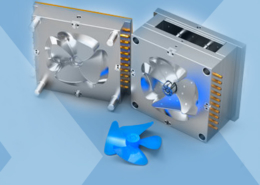
Plastic Molding

Rapid Prototyping
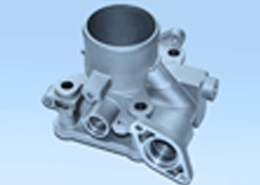
Pressure Die Casting
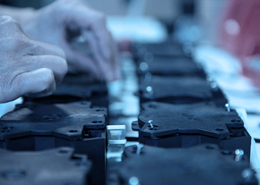
Parts Assembly
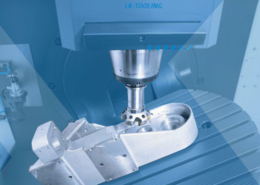