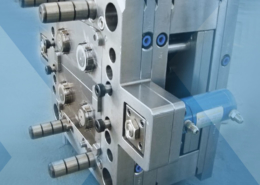
PPMouldTek - pp mold
Author:gly Date: 2024-10-15
What is double-shot injection molding and how to do it? To understand the two shot injection molding technology, let’s learn about its definition, working principle, characteristics, and applications.
The appearance material is hard and multi-shot without surface treatment. Most of it is used in transparent products. For example keyboard keys, mouse, mobile phone protective case, etc.
To save time, preheat the next batch of plastic in a presto pot or microwave and pour in the melting pots. Color change time will be less than 5 minutes by doing this.
The two-shot injection molding is realized on the double shot injection molding machine. One material is injected into a product, and then on the two-shot machine, it jumps to the mold cavity corresponding to another injection barrel by turning the mold. The part is used as an insert, and another material is injected into it to form an integrated two-material product. The injection molding machine is a dual barrel and dual mold cavity. The injection molding process is to produce products of two materials at the same time, but the products of one cavity will enter the next cavity as inserts. Double shot injection molding technology is also called dual material injection molding technology. It is a technology of mixed injection molding of two plastic materials into plastic products. Its technical connotation is actually to use a mold component to shape the shape and weld the molding work in the mold. Therefore, the fundamental principle is to plasticize two different plastic raw materials, Then the mold is welded and installed to achieve the purpose of two shot injection molding.
As a two-shot injection molding machine is affected by its manufacturing purpose, two identical machine injection plasticizing devices are needed. This is not only the requirement of its technology but also the ability to rotate and transform. In addition to the same structure, the two sets of injection devices with the same specifications also need to have the same function. During injection molding, the raw material temperature, injection pressure, and injection rate in the two sets of equipment can be adjusted consistently, so as to keep the indexes of plastic products injected at the same level, and then carry out relevant fusion and welding work. If the parameters of the two sets of equipment are inconsistent, they shall be adjusted to the same level as far as possible.
These are built when ordered, lead time is normally one to two weeks and will include everything needed to operate when delivered. (excluding an air compressor) Just plug in & play. Payment options are available. See below for more information
The two heat controllers are used to control and monitor the plastic temperature in each heating pot. A temperature difference of up to 30 F between the pots is obtainable.
– When the appearance surface of the second layer is soft glue, try not to disconnect during the design, and try to design a glue inlet point to complete all the appearance design surfaces.
The appearance material is soft glue, which needs to be used frequently. It is not allowed to open or loosen in the process of use. The products with high-performance requirements and high adhesion requirements. For example toothbrush handle, tool products, screwdriver, three prevention products, mobile phone watch, etc.
– Since the appearance is transparent, the wall thickness must be uniform in the structural design, and there must be no unevenness unless it is deliberately designed into such a texture.
All prices are in USD Copyright 2024 JACOBS MOLD & MACHINE. Sitemap | Shopping Cart Software by BigCommerce
The melting pots are cleaned by being drained completely and then wiped out with cloth wrapped on a wood dowel rod. The pots must be hot. It only takes a few minutes.
– When the first layer is hard glue, the thinnest part of the wall thickness design of the structural surface shall not be less than 0.6mm to prevent insufficient glue injection.
The other one is overmolding, a two or multi-step injection molding process, a part of one material is molded on an injection molding machine, which is put into another mold as an insert, and then injected with the second material. The simplest explanation is that two-shot injection molding is the one-time molding of an injection molding machine, just throw the material into the injection molding machine, and come out to be the finished product you need. Overmolding is to put in the products to be combined before molding and then through injection molding.
– When the appearance surface of the second layer is hard glue, the wall thickness is designed between 0.6-2.0mm and the conventional design is 0.8mm to prevent appearance problems caused by molding defects.
This machine has two separate melting pots and a nozzle that connects both which allows you to work with two colors, singly or simultaneously. Injecting laminate two color baits is possible.For use with vinyl plastisol only. (Standard soft plastic bait material)
The appearance material is hard transparent, and no obvious impurities can be seen in the appearance of transparent parts, which looks like a product with a sense of thickness in texture. For example Apple Wireless Mouse, LETV mobile power supply.
– When used as a transparent light guide, it still needs to be designed as evenly as possible, with less uneven rubber positions and fewer stiffeners to prevent light from passing through and seeing the shadow of the internal structure.
If the down payment option is selected an email will be sent to you when the machine is completed. Then select the final payment option and the machine will be shipped to you. You will receive two invoices/receipts for the down/final payment option. Shipping charges are added in the final payment option.
The initial heat up time is 20 minutes (slightly longer when full of plastisol) and will maintain an operational temperature indefinitely after the initial heating time.
The plastic can be heated directly inside the machine. Colorants and additives can also be added to the plastic in the machine.
Results will vary when injecting laminate two colors baits depending on the mold layout.I can guarantee that two full streams of plastisol of different colors will flow out of the nozzle of this machine, but I can not guarantee how the plastisol will flow inside a mold. Every mold may fill out differently and those variances will have to be processed out with temperature and PSI adjustments to achieve your desired results.
– When the appearance surface of the second layer is soft glue, the wall thickness is designed between 0.4-2.0mm and the conventional design is 0.8mm to prevent appearance problems caused by molding defects.
GETTING A QUOTE WITH LK-MOULD IS FREE AND SIMPLE.
FIND MORE OF OUR SERVICES:
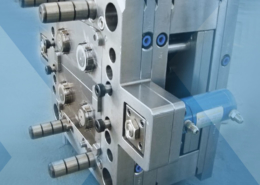
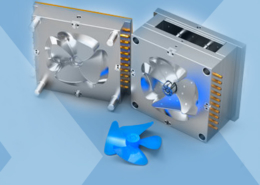
Plastic Molding

Rapid Prototyping
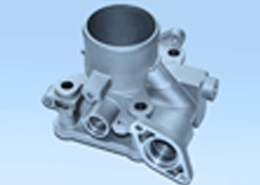
Pressure Die Casting
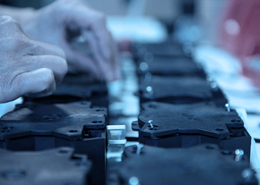
Parts Assembly
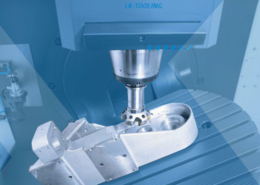