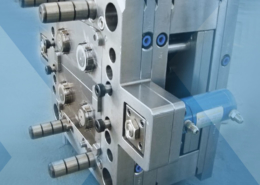
PP injection molding process services - viewmold.com - pp mold
Author:gly Date: 2024-10-15
At Romeo RIM, we rarely use steel tooling as large RIM parts tend to be ordered in lower volumes. And since reaction injection molding works at much lower temperatures and pressures, the cost of steel doesn’t justify its use.
In other words, there is still no consistency in recycled materials. Until this is addressed, using recycled materials for injection molding must be managed smartly.
Contact Bozilla Corporation today and let's discuss how we can successfully contribute to your project. Bozilla Corporation’s Injection molding Team has over 21 years of experience analytically and on the floor. We specialize in optimization, consulting, engineering, troubleshooting and Autodesk Moldflow software training. Additionally, our plastics engineers have a full understanding of polymers and how they influence an injection molded part. Your success is our success. Our skilled Team is focused upon meeting the goals and timelines of our customers.
Chris Czeczuga is a Plastics Engineer, Injection molding expert, Military Veteran and the President of Bozilla Corporation. He has proven success with many Fortune 500 companies throughout the injection molding industry. A graduate from UMass Lowell, he is Expert Certified with Autodesk, has 20+ years of field experience, intimate knowledge of injection molding part, tool and feed system design. Bozilla Corporation's success is built on providing the highest level of injection molding simulation and consulting advice to businesses who have short lead times, require an efficient, cost-effective molding process, and desire to produce a correct part the first time.
Working with a Tier 1 supplier to a major OEM, there was a discussion with the molders on the floor, people molding the parts on the injection molding machine, and their personal experiences.
We mentioned above that the two main components to molding a good part are the tooling and the process. When your tool gets shipped to your RIM molder, it is up to them to have the right manufacturing process in place to ship a quality part.
Because they are responsible for the quality of the part they are molding, they make decisions (call an audible) and replace the recycled resin with a locally available equivalent virgin resin. This protects them from producing unacceptable.
Unfortunately, the reaction injection molding process does not have any such predictive tools. And because of that, it will be very important to choose a RIM Manufacture with good standards and procedures to get the best parts possible.
The lead times for all tool materials will vary. Heavier, denser steel is much more difficult to machine than, say, aluminum which, of course, effects the lead time. Below is a list of tooling types with an approximated lead time.
However, you are still using recycled material, and 20% of the material has a history of being degraded. Unfortunately, properties will be lost, influencing the quality of the part.
And while the process is important, tooling will hit you in the pocketbook right from the start. In fact, in some cases, the cost of tooling is a factor in choosing a molding process. Therefore, it will be important to know everything that goes into creating a tool so that you can better understand where your money is going.
Nickel Shell tooling is also very expensive, but much lighter than steel making it easier to work with, machine and ship. This type of tooling can also achieve an extremely high gloss finish.
To give you some more insight into what goes in to making a tool, here are the lead times broken down by each step of the mold making process.
Currently, material suppliers are working with recyclers to have test methods put in place to address these issues with recycled materials. The caution is that these test methods reveal the problem vs. fix the problem. How do the recyclers/material suppliers create quality control with regard to molecular weight variation? Suppliers might say they can test the material with an MFR flow test. Unfortunately, an MFR flow test is a zero viscosity test, which does not capture the true shear rate the material will experience during the injection molding process.
Aluminum tooling is a popular option because it still performs relatively well at higher temperatures and pressures. And with the advancement in aluminum technologies over the years, there is a decreasing need to use steel tooling in even higher volumes.
The typical response to this situation is to combine a certain percentage of recycled material with virgin resin. By combining the recycled materials (uncontrolled variation of molecular weight) with virgin resin, which is very controlled, the blend will allow the process to maintain control, thus allowing the part to meet specifications. There may be a loss of 5% of the properties, so it will still make and meet standards.
We utilize cross functional reviews from product engineering to manufacturing engineering to operations…we discuss moldability, manufacturability, shipping and handling.
Composite or epoxy tools are limited to short, prototype runs only as these tools generally don’t last much longer than 100 shots. The options for a desired surface finish is also very limited.
However, it is essential to note that the percentage of added recycled material vs. part quality is not a 1:1 ratio, e.g., adding 20% of recycled resin does not equate to 20% loss of properties. For instance, you can test the recycled resin of 1 lot of material, and it may meet specs, but the next lot is completely different, thus knocking the process out of control. This lack of conformity may continue throughout the entire recycled resin being used.
The industry can adapt by designing parts to accept more variation, allowing increased recycled material content. For example, the part could be globally or locally thickened to allow for more process variation without loss of part quality.
It is essential to know that the reclamation process breaks the polymer's molecular structure down, making it lesser quality because the properties of that original polymer have been degraded. Recycled resin has a smaller molecular weight( length of chains) and varying viscosity, making it unpredictable. Virgin resin has molecular weight consistency/control with much less variation, giving it consistent properties.
Typically, tools used for reaction injection molding are much the same as those used in injection molding and are made from (in order of cost) Steel, Nickel Shell, Aluminum, Epoxy, or in some cases, Silicone. The decision to choose any one of these over another will depend on a number of factors including the temperature and pressure requirements of the process, the surface finish of the part and the number of parts needed.
However, there are better ways to measure Rheology since it is necessary to know the molecular weight variation. But, there is no way to correctly measure this vital detail on recycled material because there is so much fluctuation in its properties.
At Romeo RIM, we utilize Aluminum tooling almost exclusively. This is because Reaction Injection Molding (RIM) doesn’t require high temperature and pressure. Our engineers learn to understand your project and can match you with the right grade aluminum to help maximize your ROI.
If you are familiar with injection molding, you may have heard about a mold flow analysis. This is a computer model that simulates the flow of the material into the mold. With this type of analysis, you can accurately predict the flow to achieve a quality part within the first few shots, if not the first.
The media once called my dad the 'Godfather of San Antonio Recycling' for his life-long efforts at keeping reusable materials out of our landfills and back into usage. Unfortunately that became increasingly difficult to do in the U.S. for a variety of reasons, including that 'recycling' things like plastics is almost impossible to do at the 'household' or ‘post-consumer’ (co-mingled, unreliable, and incompatible) level vs. materials procured from 'industrial' sources. Everything is 'recyclable', but at what cost...?! Is it worth spending $10 to produce something that's only worth $5...?! I like to use the analogy of the $5 bill…if I put a $5 bill on your front doorstep, would you go get it…?! Sure, but if I put the same $5 bill on the steps of the U.S. capitol, would you go get it…?! And why not? See my point…?! As you can see from several recent videos (from India), this type of hands-on recycling is very labor intensive and, thus, not feasible in many countries where labor is not so cheap.
Now, the response in the industry and all industries to using recycled materials is, when possible, to take a certain percentage of recycled material and blend it in with the virgin resin.
With over 35 years of experience manufacturing reaction injection molded parts, we are EXPERTS in understanding how our material will react within the mold so that you get a good, quality part every time.
Plastics, unlike metals, cannot have any impurities, otherwise they break down chemically, which is one reason their recycling is extremely limited. You cannot have polyvinylchloride (PVC) in with high-density polyethylene (HDPE), polypropylene (PP), polystyrene (PS) etc. This is why we need to address the ‘packaging’ of these products. When you have a PS drink container with an HDPE cap and a PP and/or paper label…how are you going to profitably separate and recycle them all?! You can’t…not on a scale to make it worthwhile. That’s why ‘curbside’ or ‘post-consumer’-based product(s) recycling doesn’t work. You’ve got aluminum foil, in with diapers, in with water bottles, in with milk jugs, in with ballpoint pens, in with….! Anyway, I could go on and on, as I'm extremely familiar with recycling and solid waste management, having founded and run, along with my dad, Resource Recovery Systems here in the U.S., Taiwan, and Mexico for years. I’d love to see plastics recycling become a reality in this country and elsewhere, but a LOT of things have to change before that can actually happen…
Our manufacturing philosophy starts with Lean practices which helps to eliminate waste, either from wasted movements or actual material waste.
Also, one video showed recycled materials being used in creating new products, such as pipes and conduit. This is actually not feasible in the U.S. and elsewhere where ‘virgin’ plastics are mandated and recycled input is prohibited. These are the types of things they don’t tell consumers when recycling, especially ‘curbside’, is hyped and then most of the materials collected wind up in landfills anyway. My father singlehandedly built and operated these types of machines for plastics (and cardboard and metals) recycling, but was eventually shut down by the government entities (TCEQ) who supposedly promote recycling but then put hard-working entrepreneurs out of business and redirect all the materials that WERE being recycled into landfills…oftentimes at great distance from their source…NIMBY (Not In My BackYard)!
So, with recycled material, even though you may be able to create a good test method, there's no way to create consistency because of the history of the recycled material.
Steel Tooling is the most expensive but also the strongest. Steel tooling is used any of the following instances: when high temp and pressure is required (SMC), when producing very large volumes (50,000+) or when a Class A high gloss surface finish is needed.
Because Nickel Shell tooling is even lighter than Aluminum, we at Romeo RIM utilize nickel shell tools when the size of the parts begin to push the upper limits of our size capacity. We also use them to achieve a very high gloss surface finish (70-80 on a 60 degree scale).
In the first phase of the plastic recycling process, the material goes through the injection molding process, which partially degrades the material (molecular weight reduction). Then, it is potentially exposed to UV, temperature fluctuations, or chemicals, which contributes to the degradation process. Next, the plastic is ground up and typically cleaned with a thermal or chemical process, further degrading the material. Finally, the reclaimed plastic is ready to, again, be beaten up in the injection molding machine.
GETTING A QUOTE WITH LK-MOULD IS FREE AND SIMPLE.
FIND MORE OF OUR SERVICES:
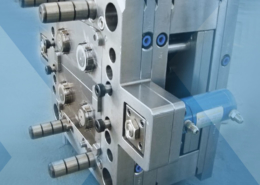
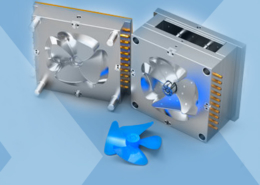
Plastic Molding

Rapid Prototyping
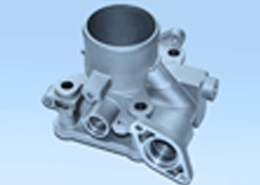
Pressure Die Casting
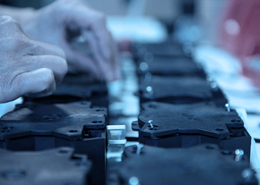
Parts Assembly
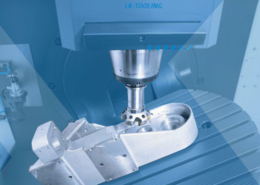