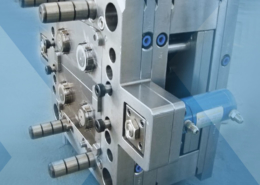
POM injection molding processing condition - viewmold.com - pom injection moldin
Author:gly Date: 2024-10-15
Another important advantage of using softer injection moulds is that they rarely have a negative impact on component quality: when proper design requirements are taken into account, plastic parts made in low quantities are just as good as those produced using hardened steel moulds.
Low-volume injection moulding uses softer aluminium moulds and inserts instead of hardened steel ones, which are usually simpler and less expensive to produce. These moulds are obviously not as durable as their hardened steel counterparts, but manufacturers benefit because they don’t always need to be when manufacturing low-volume components. Soft moulds, when used strategically, can lower tooling costs and shorten production times.
It's the ideal solution for tanks, kayaks, coolers, floats, bins, and marine markers. This cost-effective technique shines brightest when production volumes fall below 1,000 units annually on a single tool, making it particularly attractive to inventors, start-ups, and small businesses seeking efficient manufacturing solutions.
Our depth of experience in rotational moulding allows us to deliver products with consistent wall thickness, resulting in structural integrity and optimal performance.
Our rotational moulding process in tandem with cleverly designed tooling can ensure an impeccable finish, enhancing the visual appeal and functionality of your products.
Rotomolding, a thermoplastic molding process, is best suited for manufacturing large, one-piece hollow parts and double-walled open containers.
At the same time, hardened steel, which is needed for conventional moulds, requires a substantial upfront time and financial investment. Moulds made of aluminium or lower-grade steel, on the other hand, are much less costly to make and can be made far quicker. Manufacturers may use these moulds to test and produce viable parts without having to commit to large minimum orders, allowing them to fine-tune component design and production as required. This enables producers to start manufacturing faster and, in many cases, greatly increase speed-to-market, reducing the time it takes to see a return on investment.
At Plastic Fabrications, we specialise in rotational moulding, a technique using Low Density Polyethylene (LDPE) to create sophisticated custom components in complex shapes and sizes. With a rich history of catering to diverse client requirements, we have earned a reputation as one of Australia’s most trusted companies in custom moulding. We pride ourselves on transforming your ideas into tangible realities. Our team of skilled designers and engineers goes beyond mere plastic part production; we offer comprehensive custom plastic moulding solutions tailored to your needs. No project is too complex, niche, or small for us.
Fletchers team were challenged to design and build a pallet for internal movement within the factory allowing slip unloading onto export pallets externally. The pallet then became part of the infrastructure within their production line needing it to be robust, strong, and specific. Plastic Fabrication collaborated with the Fletchers team providing the technical input of a Rotational Moulder and the experience of designing and developing the largest plastic pallet range in the Southern Hemisphere. The result earned Fletchers a 2006 MLA Safety award and huge improvements in efficiency, safety and productivity.
Our expertise in plastic injection moulding helps us to provide a complete turn-key solution for your plastic manufacturing needs, whether it’s an automotive part for bespoke custom builds or prototype construction for healthcare system components.
As the moulding material is not exposed to external pressure, the risk of defects in the finished product is minimised, ensuring consistent quality and durability.
We at Stephens Plastic are always looking for ways to improve our performance. That means working closely with and of our customers during the process, from design and prototyping to post-production and delivery, to ensure that they receive high-quality parts manufactured on a budget and delivered on time. Contact us today to learn more about how we can bring your ideas to life.
Stephens Plastic has the expertise, knowledge, and experience to provide just what you need, whether it’s 10 or 100,000 plastic parts, thanks to its ability to provide both low and high volume injection moulding.
We have been established for many years and with our young and vibrant management team have vast experience in all aspects of plastic injection moulding – from the design stages through to the final packaged product.
Some of the cookies we use are essential for the site to work. We also use some non-essential cookies to collect information for making reports and to help us improve the site. The cookies collect information in an anonymous form. To control third party cookies, you can also adjust your browser settings.
Our custom-moulded products are built to withstand demanding environments, providing long-lasting performance and reliability.
Please contact us if you would like to receive a quotation and/or to find our more about how we can provide the service you are looking for.
Our Low Volume Injection Moulding is a specialised service that provides complete production-quality parts in quantities of 10,000 or less bits, depending on the method. Our low-volume moulding, also known as short runs, is closely supervised and regulated to ensure that all aspects of mould design and construction are met. Small and medium-sized companies, as well as small-batch manufacturing, benefit from this form of production.
From small car parts weighing 2kg to 10,000-liter tanks weighing up to 300 kilograms, we excel at delivering tailor-made solutions across a broad range of applications.
GETTING A QUOTE WITH LK-MOULD IS FREE AND SIMPLE.
FIND MORE OF OUR SERVICES:
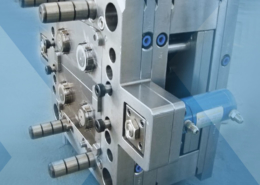
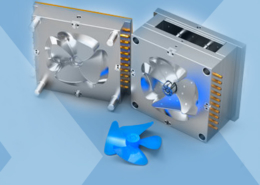
Plastic Molding

Rapid Prototyping
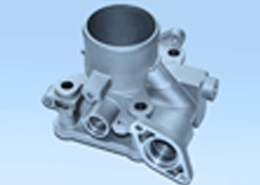
Pressure Die Casting
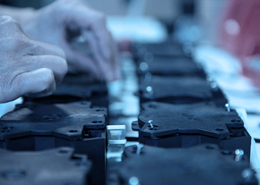
Parts Assembly
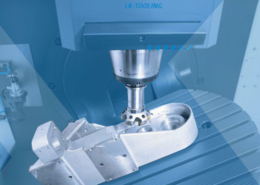