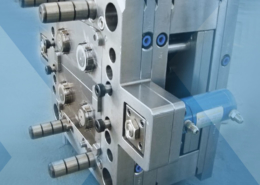
POM / Delrin acetal - delrin injection
Author:gly Date: 2024-10-15
Polyamides are a very popular injection molding material but just like any other plastic material, they are not suitable for every application. There are various issues that can arise in the nylon injection molding process. Some of the challenges and considerations that one must take into account before applying Nylon resins to an application are listed below:
Another benefit is there is no apparent vestige. The valve gate makes a clean break from the part, leaving only a fine witness line from the valve gate pin. This makes the valve gate system a great option for cosmetic parts that are decorative, as well as for medical applications where gate vestige is not allowed.
In ISO 9001 quality management systems, the Management Representative (MR) plays a crucial role. While the 2015 version of ISO 9001 no longer mandates this position, having a trusted management member serve as an MR remains vital for streamlining operations and maintaining quality standards.
Discover how to enhance your mold design process with CAD/CAM software specifically tailored for the moldmaking industry. In part two of this webinar series, Cimatron will demonstrate how to intelligently design mold components, such as slides and lifters, using powerful CAD/CAM tools to accelerate the design process. Additionally, it will cover how to avoid errors and ensure design accuracy for ejector pins by checking clearance distances, calculating cutoff heights correctly, and thoroughly documenting all ejector components. Agenda: Slides Lifters Inserts Ejection pins and charts
Cold runner molds do have their advantages. They are simple in design, relatively inexpensive to build and easy to maintain. However, hot runner molds have proven to be a much better alternative for most applications.
To illustrate further, a long-time molder ran a single-cavity mold using a cold sprue with a branch of a runner to make little nylon wheels. The customer ran 21 seconds to fill each part and scrapped the sprue and runner with every cycle. Then he would machine each wheel because he worried it wasn’t truly round, adding yet another step to the production process.
Discover how CAD/CAM functionality tailored for the mold industry can significantly enhance the mold design process. In part three of the webinar series, Cimatron will focus on designing waterlines and cooling components. It will demonstrate how CAD/CAM tools can verify drill line depths for water lines and baffles, ensure that minimum steel requirements are met while placing water lines, and provide a complete list of all baffle cutoff lengths. Additionally, it will explore how to confidently design runners and gates using CAD functionality specifically developed for these aspects of mold design. Agenda: Waterlines and verification Conformal cooling Baffles and charts Runners and gates
In ISO 9001 quality management systems, the Management Representative (MR) plays a crucial role. While the 2015 version of ISO 9001 no longer mandates this position, having a trusted management member serve as an MR remains vital for streamlining operations and maintaining quality standards.
Steel supplier discusses high thermal conductivity metal powders that also address the skills gaps via user-friendly materials and promote sustainability via durability and higher cycle counts.
MoldMaking Technology addresses the complete lifecycle of the manufacture and maintenance of a mold—from design to first shot—by providing solutions and strategies to moldmaking professionals charged with designing, building and repairing molds. About Us
Costs are determined based on the hot runner requirements. A single-cavity mold will typically require a hot sprue bushing and those calculations are straightforward. However, when the mold has more than one cavity, there are a few factors to consider.
All successful mold build projects start with examining the part to be molded to ensure it is moldable and will meet the customers' production objectives.
Explore the standout articles of September, featuring innovations, expert insights, and strategies to boost efficiency and quality for your moldmaking needs.
A water-based, eco-friendly plastic mold cleaning system helps Rankine-Hinman Manufacturing restore flow rates and avoid big-ticket failures on complex and costly molds.
Nylon 6 & 66 are both synthetic polyamides that are semi-crystalline and possess great strength and excellent durability.
Gerardo (Jerry) Miranda III, former global tooling manager for Oakley sunglasses, reshares his complete mold design checklist, an essential part of the product time and cost-to-market process.
Released earlier, this video remains a valuable recruitment tool and is being re-promoted in celebration of Manufacturing Day 2024.
In the early days of injection molding, cold runners were the only method for delivering plastic to a mold that ran more than one part. It is a method still used today. Cold runners usually comprise two or three plates, and a nozzle delivers the molten plastic into the mold via a sprue, then through channels or runners that lead to the mold cavities that are then filled to make plastic parts. Typically, the sprue requires the most time to cool because it is usually thicker than the runners and parts.
Nylon 66 exhibits excellent abrasion resistance thus, Nylon 66 polymer is extensively applied to carpets, upholstery, and conveyor belts.
After attending IMTS, it's clear that the integration of advanced technologies is ready to enhance precision, efficiency and automation in mold manufacturing processes. It’s a massive event, so here’s a glimpse of what the MMT team experienced firsthand.
Since its invention, Nylon 6 has been applied to various industries. It has been a popular choice and has been applied to various projects such as surgical sutures, musical instrument strings, toothbrush bristle threads, fishing nets, and filaments. In addition, it is a popular choice in the textile industry for hosiery and knitted garments.
Valve gate systems use either pneumatic, hydraulic cylinders or servo drives to actuate a valve gate pin to control the flow of plastic into a cavity, giving the molder more control over the molding process. Several advantages can be gained by using a valve gate system, including enlarging the gates to fill the part faster, decreasing cycle times.
In comparison to other Nylon grades, PA 11 has lesser desirable mechanical properties but it has various advantages such as being lightweight and lower water absorption rate.
Finally, he was convinced to try a hot sprue bushing and immediately saw significant savings on material by direct gating the hot sprue to the part. In addition, the gate location changed from the periphery to a central location on top of the part. As a result, he could reduce his cycle time from 21 seconds to 15 seconds and no longer needed the secondary operations because of the more balanced gate location, freeing up manpower for other work.
There are very few plastics in the manufacturing industry that combine the versatility, performance, and value of Polyamides.
When used for conformal cooling in plastic injection, 3D printing opens a wide range of design freedom. This design freedom enables designers to develop highly-efficient thermal regulation networks. However, this blessing also comes at the expense of not only higher manufacturing cost but also higher design cost as the designer could spend weeks to develop optimal cooling channels. This webinar will explore strategies and tools — including SimForm, a front-end thermal simulation app — to help tool designers and tooling managers maximize the benefits of 3D printing while minimizing manufacturing and design costs. Agenda: 3D printing applied to the plastic injection industry 3D printing pros and cons Tools and methods to facilitate the integration of 3D printing
We ensure that you have a seamless manufacturing process from prototype to production. You can contact us to further understand how Nylon Injection Molding can be implemented for your project. Contact VEM tooling and request a quote today.
A connected software solution streamlines the moldmaking process by providing a unified source of design data, enhancing efficiency and reducing errors, with five key steps benefiting from this integration.
The next major differences are the water absorption rates and heat deflection temperatures. Nylon 6 tends to absorb more water and has lower heat deflection temperatures than Nylon 66. It is thus not suitable for applications that require the plastic to be exposed to water at high temperatures.
Join this webinar where Hexagon will explore how state-of-the-art CAD/CAM technology can drive your business forward. Learn how to optimize tool paths, enhance design accuracy and reduce lead times with advanced simulation. Discover the power of automation and real-time data for continuous improvement. Tailored for mold and die manufacturers, this session offers actionable insights to boost productivity and quality. Don’t miss this opportunity to gain a competitive edge in progressive die manufacturing. Agenda: Key challenges in progressive die manufacturing Optimizing tool paths Enhancing mold and die design accuracy Reducing lead times with simulation Automating processes for greater efficiency Leveraging real-time data for continuous improvement
This webinar will provide an overview of new developments in hot runners, controllers, mold components, predesigned molds, process monitoring and mold maintenance equipment. These advancements are designed with the goals of lowering scrap rates, optimizing process temperatures and managing energy consumption. The solutions also aim to support productivity and may contribute to extending the operational lifespan of tooling equipment. Agenda: Innovative undercut and thread-forming components Predesign mold bases and plate control Melt delivery and control solutions Process monitoring and maintenance
Standardization and quality are part of our companies core values. We deliver the best possible experience and product to our customers, every single time consistent. Take a look at our certificates!
Nylon injection molding has various benefits and limitations. Though, polyamides are a popular material choice for injection molding techniques, we must note that it has both advantages as well as disadvantages.
The first step to switch over to a hot runner mold is to perform a design analysis to ensure that a hot runner is appropriate for the application. For example, determine if the material being molded is suitable for a hot runner design, which is an essential consideration whether the mold is new or being retrofitted. Though most resins are amenable to hot runner usage, there are exceptions. Consult your material supplier for their recommendations. If a hot runner system is deemed feasible, determine whether to go with a thermal gate or valve gate system. This is a good time to seek input from a knowledgeable hot runner supplier who can recommend suitable options. Most hot runner suppliers also offer Moldflow analyses to ensure the hot runner system is balanced and to assist with a part fill study.
Moldmakers and molders who use hot runner systems in their molds will be the first to disclose that it is often the most expensive part of the mold build. But they quickly add that it is worth the investment based on reduced cycle time, resin cost, elimination of post-processing, product lifecycle, etc. Meanwhile, hot runner holdouts are skeptical, wondering why they should add thousands of dollars to the upfront cost of a mold when the cold runner system gets the job done. So, let’s examine the facts.
Molders then must perform secondary operations, which begin with trimming gates, if necessary. Dealing with the runners and sprue requires the molder to perform post-molding operations such as regrinding and pelletizing, then mixing with virgin plastic, if the reuse of plastic is permitted. Unfortunately, many engineering and medical applications do not permit regrind reuse or only allow a small percentage. Any remaining scrap plastic must be disposed of or sold for pennies on the dollar.
Join MoldMaking Technology Editorial Director Christina Fuges as she gets the latest news on this mold builder's use of VR for mold design education.
Nylon is a type of plastic that is composed of polyamide resins, which is obtained either through the polycondensation of diamines and dibasic acids or through the ring-opening polymerization of lactams which is formed by the dehydration of amino acids.
Steps to improve data-driven decision-making and key features of a cloud-based system for mold monitoring and asset management.
Valve gate systems are more expensive than thermal gates because they require more components to actuate the valve pins. Still, they can be ideal for more complex molding applications, including molds that demand sequential filling.
After attending IMTS, it's clear that the integration of advanced technologies is ready to enhance precision, efficiency and automation in mold manufacturing processes. It’s a massive event, so here’s a glimpse of what the MMT team experienced firsthand.
The need for data to track information and the history of the mold-building process is ever-increasing, and mold component solutions can help.
Intralox's integration of the Alpha Laser ALFlak has significantly improved their tool room efficiency when it comes to difficult welds and urgent repairs.
Thermal gate systems are the most common and economical. Thermal describes the type of shut-off used to stop the flow of plastic into the mold cavity. The small gate freezes as the part cools and stops the plastic flow so that the part can be ejected. If the gate is too big, the thermal seal will fail, causing stringing or drooling.
MoldMaking Technology Editorial Director Christina Fuges sits down with Murphy Forsyth, GM – Injection Molding and Director Of Marketing for Zero Tolerance LLC in Clinton Township, MI.
It should be noted that it is not unheard of for molders to use cold runners in prototype or short-run production molds, particularly when trying out a new product design. However, once that design is perfected, a larger production mold would include a hot runner system or hot sprue bushing to produce the product more rapidly and cost-effectively in much larger quantities.
After attending IMTS, it's clear that the integration of advanced technologies is ready to enhance precision, efficiency and automation in mold manufacturing processes. It’s a massive event, so here’s a glimpse of what the MMT team experienced firsthand.
After hydrolysis, hydrogen bromide undergoes nucleophilic substitution with ammonia to form 11-aminoundecanoic acid, which is polymerized into nylon 11.
Polyamides, also referred to as Nylon in the manufacturing industry can be processed through standard injection molding. It demonstrates various chemical and physical properties that make it an ideal choice for manufacturing both, thin- and thick-walled parts.
The numbers 6 and 66 refer to the type and quantity of polymer chains in their chemical structure. Nylon 6 is made from one monomer which has 6 carbon atoms whereas Nylon 66 is made from 2 monomers in which each one has 6 carbon atoms, thus it’s called Nylon 66.
Nylon 11 also referred to as Polyamide 11 or PA 11 is a non-biodegradable polyamide. Nylon 11 has lesser amides in its structure and it thus exhibits increased resistance to dimensional changes that are often observed due to moisture absorption.
Gerardo (Jerry) Miranda III, former global tooling manager for Oakley sunglasses, reshares his complete mold design checklist, an essential part of the product time and cost-to-market process.
Nylon was patented by DuPont in 1935 and has since then been one of the most popular plastics to be used in various industries.
Engineers use properly preloaded bolts, blocks, springs and side-action cores to enhance functionality and reliability in various mechanical systems.
(a) Cold runner design — a shot weight of 59 grams and estimated cycle time of 30 seconds (b) hot to cold runner system — a shot weight of 37 grams and estimated cycle time of 23 seconds and (c) direct gate hot runner system — a shot weight of 26 grams and estimated cycle time of 19 seconds. Photos Credit, all images: PCS Company
Smart sensors and sophisticated process and measurement data management are driving intelligent moldmaking to new heights.
It’s easy to imagine the advantages automation offers the moldmaking process, but it's challenging to change one’s mindset, develop a plan and invest.
After attending IMTS, it's clear that the integration of advanced technologies is ready to enhance precision, efficiency and automation in mold manufacturing processes. It’s a massive event, so here’s a glimpse of what the MMT team experienced firsthand.
Steel supplier discusses high thermal conductivity metal powders that also address the skills gaps via user-friendly materials and promote sustainability via durability and higher cycle counts.
Moldmakers and molders who use hot runner systems in their molds will be the first to disclose that it is often the most expensive part of the mold build. But they quickly add that it is worth the investment based on reduced cycle time, resin cost, elimination of post-processing, product lifecycle, etc.
What exactly does a hot runner do? If you’ve been in the injection molding industry for any length of time, you might think the answer is obvious, but it is not.
Intensive workshop teaches the process of mold maintenance to help put an end to the firefighting culture of many toolrooms.
Nylon resins exhibit excellent strength, stiffness, heat resistance, resistance to wear, and chemical resistance to hydrocarbons. Nylon is a relatively low-cost polymer that is easy to process and can be reinforced with glass or carbon fiber to increase mechanical and thermal properties. Let’s take a look at some of its properties through the below infographic:
A focus on electrode design and automation helps toolroom improve efficiency, reduce tooling costs and deliver higher quality products.
Nylon is a hygroscopic substance as it readily absorbs water from its environment. Hygroscopic materials tend to attract water either through absorption or adsorption. Nylon is also known in the injection molding industry for its many variations. In this article, we have described such features and their various types in-depth.
The very first example of Nylon that was developed by Dupont’s team was Nylon 66. Later, many other variations were developed. Today, nylon comes in four main grades: Nylon 11, 12, 46, and 66. Nylon can be reinforced with glass for greater mechanical strength and that refers to the various grades of Nylon. In addition, there are many varieties of PA such as PA6, PA66, PA610, PA11, PA12, PA1010, PA612, PA46, PA6T, PA9T, and MXD-6 aromatic polyamide, etc.
Identify pain points, tackle each one strategically and maintain flexibility to keep your moldmaking business on a path to growth.
Nylon is a hygroscopic material that must be dried properly during processing to maintain its physical properties. In appearance, nylon plastics can be either white, milky white, or yellowish, and are either transparent or translucent crystalline resins. These Nylon resins can also be imparted with any color.
Formnext Chicago is an industrial additive manufacturing expo taking place April 8-10, 2025 at McCormick Place in Chicago, Illinois. Formnext Chicago is the second in a series of Formnext events in the U.S. being produced by Mesago Messe Frankfurt, AMT – The Association For Manufacturing Technology, and Gardner Business Media (our publisher).
It is polymerized either through omega trinitrophenyl aminolauric or laurolactam monomers. They both have 12 carbons, hence the name ‘Nylon 12’.
Understanding and facing the moldmaking industry’s obstacles to growth requires a strategy focused on increased profitability.
What exactly does a hot runner do? If you’ve been in the injection molding industry for any length of time, you might think the answer is obvious, but it is not.
Reducing cycle time and costs while also freeing up your machines for other projects are advantages gained by using hot runners that no one can ignore. But where does one begin transitioning from cold to hot runners?
Join MoldMaking Technology Editorial Director Christina Fuges as she gets the latest news on this mold builder's use of VR for mold design education.
Discover how to enhance your mold design process with the right CAD/CAM tool for parting and cavity design. This webinar will explore CAD/CAM capabilities including how hybrid solid/surface modeling can streamline workflow and improve accuracy. Learn how to confidently tackle parting, runoff, and shutoff, ensuring precision and efficiency in your designs. Agenda: Part analysis QuickSplit techniques Parting and runoff strategies Shutoff solutions
If your project requires plastic parts to endure high temperatures and resistance to chemicals and abrasion, Nylon can be a perfect choice. VEM Tooling has the expertise and the team that is required for your Nylon injection molding project. At VEM Tooling, we offer quick quotes and dependable service.
There is no doubt about it: More and more molds are being designed to include hot runner systems or hot sprue bushings. For those who build and run hot runner molds, it is not hard to see the reasons why. While expensive to build, hot runner molds can be more economical in the long run than their cold runner counterparts. Still, there are many hot runner holdouts, so it is time to build the case for transitioning from cold to hot runner molds.
One of the major differences between the two types of Nylon is mold shrinkage. The mold shrinkage of Nylon 6 is lower than Nylon 66 and thus, the dimensions of the final plastic part manufactured are generally as expected with Nylon 6. In the case of Nylon 66, you need to account for the higher mold shrinkage.
Diamond compounds, with their varied grades, colors and base options, provide a comprehensive solution for mold builders in need of precise and superior polishing across diverse materials and applications.
Nylon 46, also referred to as Polyamide 4/6 is a semi-crystalline, yellowish thermoplastic. It is made through condensation polymerization of 1,4-diaminobutane with adipic acid.
Polyamide, abbreviated for PA, is a popular injection molding material. A polyamide is a type of polymer that has amide groups in a recurring form in the main polymer chain. The chemical formula for amide groups is (R―CO―NH―R′) and the chemical structure of polyamides is as follows:
Both thermal and valve gating systems are available for single and multicavity applications. In the single-cavity mold, a hot sprue bushing will be used. In a multicavity mold, the system requires manifold(s) and nozzles within a hot-half stack. No matter the cavitation, there is always material savings.
While Nylon 6 and 66 are primarily very similar, they also have distinct differences. These differences are largely due to the differences in their chemical structure and are illustrated through the following infographic:
While both hot runner and cold runner systems have their benefits, for design flexibility as well as reduced cycle times and costs, hot runner systems will probably be the better choice.
Nylon was developed by DuPont and is a generic name for polyamides. DuPont refers to E. I. duPont de Nemours, an American company that was founded in July 1802. Since the 20th century, DuPont has invented various types of polymers that are extensively applied to a wide array of industries. Some of the popular plastics besides Nylon are Lycra, Teflon, Freon, Neoprene, etc.
GETTING A QUOTE WITH LK-MOULD IS FREE AND SIMPLE.
FIND MORE OF OUR SERVICES:
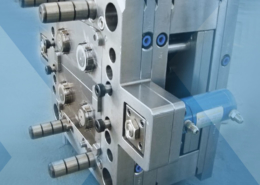
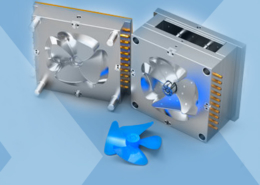
Plastic Molding

Rapid Prototyping
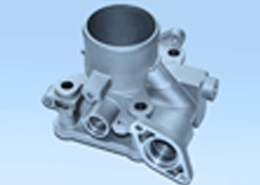
Pressure Die Casting
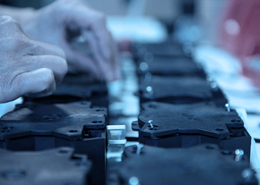
Parts Assembly
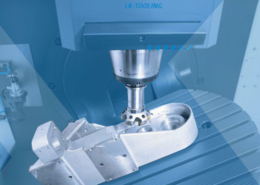