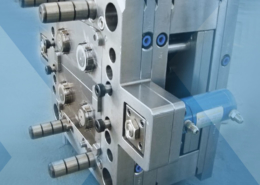
Plastic pallet moulds play a pivotal role in the manufacturing industry, serving
Author:gly Date: 2024-06-08
Design and Construction
Plastic pallet moulds are meticulously designed and constructed to ensure precision and durability. The design process involves intricate engineering to create moulds that can withstand the pressures and temperatures involved in the plastic injection molding process. High-quality materials, such as stainless steel or aluminum, are often utilized to enhance the longevity of the moulds and maintain the integrity of the pallets produced.
The construction of plastic pallet moulds involves precision machining and shaping techniques. Computer-aided design (CAD) software is commonly employed to model the intricate details of the moulds before they are fabricated. CNC machining technology is then utilized to carve out the precise shapes and dimensions required for the mould cavities. This meticulous construction process is essential for ensuring the accuracy and consistency of the produced pallets.
Material Selection
The choice of materials for plastic pallet moulds is critical in determining their performance and longevity. Factors such as heat resistance, corrosion resistance, and wear resistance must be carefully considered when selecting materials for mould construction. Stainless steel is a popular choice due to its excellent mechanical properties and resistance to corrosion and wear. Aluminum is also favored for its lightweight nature and thermal conductivity, which facilitates efficient cooling during the molding process.
In addition to the base material, surface treatments and coatings are often applied to plastic pallet moulds to further enhance their properties. Surface treatments such as nitriding or chrome plating can improve hardness and abrasion resistance, prolonging the lifespan of the moulds and reducing maintenance requirements. These material selection considerations are crucial for ensuring the reliability and efficiency of the plastic pallet manufacturing process.
Injection Molding Process
The injection molding process is a complex sequence of steps that requires precision and control to produce high-quality plastic pallets. Plastic pallet moulds play a central role in this process, dictating the final shape, size, and characteristics of the pallets. The process begins with the preparation of raw plastic material, which is heated and injected into the mould cavity under high pressure.
Once the plastic material fills the mould cavity, it is allowed to cool and solidify, taking on the shape of the mould. Proper cooling is essential to ensure uniformity and structural integrity in the final pallets. After cooling, the mould opens, and the newly formed pallets are ejected, ready for further processing or use.
Conclusion
In conclusion, plastic pallet moulds are integral components of the manufacturing industry, facilitating the production of durable and reliable pallets for various applications. The design, construction, material selection, and injection molding process all play crucial roles in ensuring the quality and efficiency of plastic pallet production. By understanding the complexities of plastic pallet moulds, manufacturers can optimize their processes and enhance product quality, contributing to the smooth operation of supply chains and logistics networks. Looking ahead, continued advancements in mould design and technology hold the potential to further improve the performance and sustainability of plastic pallet manufacturing processes.
GETTING A QUOTE WITH LK-MOULD IS FREE AND SIMPLE.
FIND MORE OF OUR SERVICES:
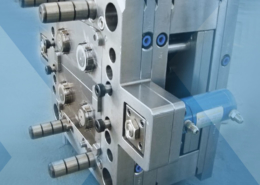
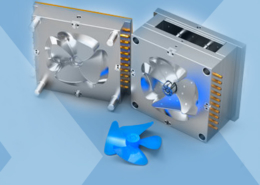
Plastic Molding

Rapid Prototyping
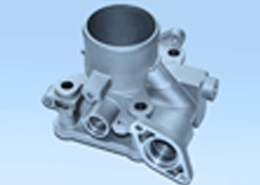
Pressure Die Casting
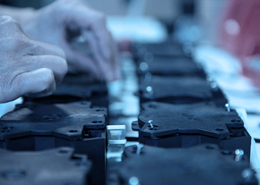
Parts Assembly
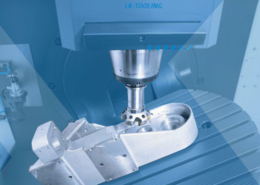