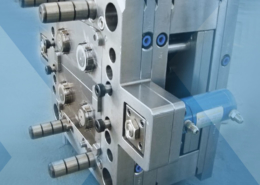
Exploring Plastic Molding in Electrical Applications: Innovations and Insights
Author:gly Date: 2024-06-08
In today's rapidly evolving technological landscape, plastic molding plays a pivotal role in the production of electrical components, revolutionizing the way we interact with and utilize electronic devices. This article delves into the realm of plastic molding in electrical applications, providing a comprehensive overview, exploring key aspects, and highlighting emerging trends in this dynamic field.
Introduction: Unveiling the Intersection of Plastic Molding and Electronics
The fusion of plastic molding techniques with electrical engineering has ushered in a new era of innovation, enabling the seamless integration of electronic components into various devices and systems. From consumer electronics to industrial machinery, the marriage of these disciplines has transformed the landscape of modern technology, driving advancements in efficiency, functionality, and design.
Material Selection: The Foundation of Electrical Plastic Molding
Central to the success of plastic molding in electrical applications is the careful selection of materials, balancing considerations such as conductivity, durability, and thermal stability. Polycarbonate, ABS, and polyamide are among the preferred materials for molding electrical components, offering a unique combination of properties tailored to the demands of the application. Furthermore, advancements in material science continue to expand the palette of options available to manufacturers, enabling the development of innovative solutions for a diverse range of electronic devices.
Design Considerations: Optimizing Performance and Functionality
Effective design is paramount in the realm of plastic molding for electrical applications, influencing not only the aesthetics but also the performance and functionality of the final product. Incorporating features such as precise tolerances, cable management channels, and heat dissipation mechanisms enhances the reliability and longevity of electrical components, ensuring optimal performance in real-world conditions. Moreover, leveraging computer-aided design (CAD) software and simulation tools empowers designers to iterate rapidly and refine their designs, streamlining the development process and minimizing time to market.
Manufacturing Processes: From Injection Molding to Overmolding
The manufacturing processes employed in plastic molding for electrical applications are as diverse as the components themselves, each offering unique advantages and considerations. Injection molding, with its high precision and scalability, remains a staple in the production of intricate electrical enclosures and connectors. Similarly, overmolding techniques enable the encapsulation of delicate electronic components within a durable and protective housing, safeguarding against environmental factors and mechanical stress. Furthermore, advancements in additive manufacturing technologies, such as 3D printing, are poised to revolutionize the prototyping and customization of electrical components, offering unprecedented design freedom and agility in production.
Quality Assurance: Ensuring Reliability and Safety
In the realm of electrical plastic molding, quality assurance is paramount, with stringent standards and regulations governing the production and deployment of electronic devices. From rigorous testing protocols to adherence to industry certifications, manufacturers must uphold the highest standards of reliability and safety to instill confidence in consumers and stakeholders alike. Additionally, leveraging advanced inspection techniques, such as automated optical inspection (AOI) and X-ray imaging, enables early detection of defects and anomalies, mitigating risks and ensuring the integrity of electrical components throughout their lifecycle.
Environmental Sustainability: Embracing Responsible Practices
As the global focus on sustainability intensifies, the plastics industry is undergoing a paradigm shift towards more environmentally conscious practices. In the realm of plastic molding for electrical applications, this entails adopting renewable materials, optimizing manufacturing processes to minimize waste, and implementing recycling initiatives to reduce the environmental footprint of electronic devices. Moreover, fostering collaboration across the supply chain and embracing circular economy principles are essential steps towards achieving a more sustainable future for the industry.
Future Outlook: Navigating Emerging Trends and Opportunities
Looking ahead, the intersection of plastic molding and electronics presents a myriad of opportunities for innovation and growth. From the proliferation of internet-connected devices to the rise of electric vehicles and renewable energy systems, the demand for advanced electrical components continues to soar, driving investment and research in new materials, manufacturing techniques, and design methodologies. Furthermore, as societal priorities shift towards sustainability and resilience, the industry is poised to embrace new challenges and opportunities, catalyzing the development of innovative solutions that redefine the boundaries of what is possible in the realm of plastic molding for electrical applications.
Conclusion: Shaping the Future of Electronics Through Plastic Molding
In conclusion, plastic molding has emerged as a cornerstone of innovation in the realm of electrical engineering, enabling the creation of sophisticated and reliable components that power the devices and systems we rely on every day. By embracing advanced materials, design principles, and manufacturing techniques, manufacturers can unlock new possibilities and drive progress towards a more connected, sustainable, and electrified future. As we continue to push the boundaries of what is possible, let us harness the transformative power of plastic molding to shape a brighter, more electrifying tomorrow.
GETTING A QUOTE WITH LK-MOULD IS FREE AND SIMPLE.
FIND MORE OF OUR SERVICES:
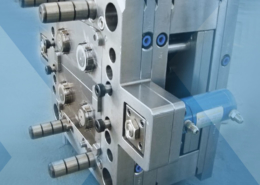
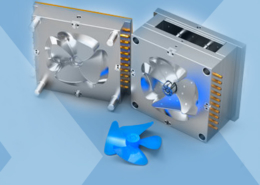
Plastic Molding

Rapid Prototyping
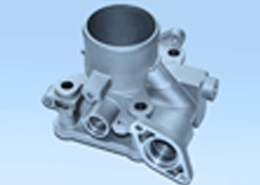
Pressure Die Casting
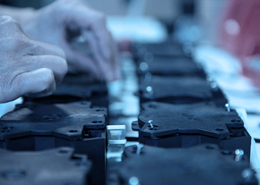
Parts Assembly
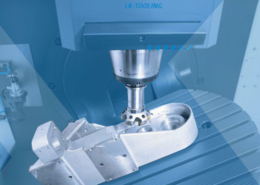