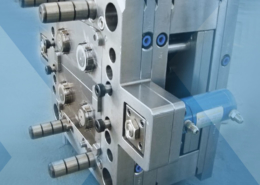
Polypropylene (PP) Injection Molding Manufacturer - pp moulding
Author:gly Date: 2024-10-15
The kind of plastic you choose for your prototype influences its price and use. Selecting the plastic that best meets your demands is crucial since different plastics have different prices and features.
Our business strategy and operating plan is built upon People, Process Control, and Technology. We believe that by combining the best talent with proper technology to control the injection molding process we will manufacture consistent high quality parts for our customers. We also believe that culture is a strategic advantage and when we can foster an environment where people care for each other they will take care of the equipment, resin, customers and company.
Even if you have a fantastic concept in your head, it might take much work to convey it to others appropriately. You can fill the gap by giving a practical example of your idea in a plastic prototype.
World Class Service – We listen to our customers, anticipate their needs, and seek to exceed their expectations prior to them having to ask.
The number of prototypes you want and the resulting cost implications are other crucial factor in plastic prototyping. Consider your prototype needs for testing, confirmation, and market evaluation. This helps you determine the most cost-effective production processes for your volume.
What exactly is it that you need to verify or test? Your prototype’s quality and complexity needs will be determined by the objectives that you set for it.
Generally, you start with a 3D or computer-aided design (CAD) model to make a plastic prototype. The actual prototype’s physical design is based on this digital illustration.
CNC machining (“computer numerical control”) is a subtractive manufacturing method employing CNC machines to form plastic prototypes accurately.
A plastic prototype enables you to engage with your design physically while testing its functionality and assessing its usability. You can spot design issues by handling, using, and experimenting with the prototype.
Contact Kemal Plastic Injection Molding Services for a detailed pricing estimate on your plastic prototype. Based on your precise needs, required quantities, and preferred materials, we will provide comprehensive cost estimation for your plastic prototypes.
3D printing is perfect for making a few prototypes at a minimal cost. If you require more prototypes, injection molding or vacuum casting may be cheaper. Prototyping is efficient and cost-effective when volume and budget are balanced.
Understanding the prototype’s function is the first step in plastic rapid prototyping. Consider the issue you’re attempting to address by asking yourself possible questions.
The expense of your project may also be affected by its urgency. Due to the need for speedier manufacturing processes or prioritized resources, rush orders or expedited production may be subject to additional fees.
Utilize Kemal Plastic Injection Molding’s experience and the versatility of plastic prototyping to quickly and effectively bring your ideas to life.
This article allows you to assess and enhance your product’s design, usability, and aesthetics, giving you the trust you need to proceed with the mass production process.
You can transform the digital design into a physical plastic product using several prototype methods, including CNC machining, 3D printing, or injection molding.
Innovative and Creative – Our employees are the most valuable asset of the company and the only asset that has the ability to innovate and generate creative ideas to provide solutions to customer challenges. We will encourage teamwork, creative thinking, and innovation as a primary avenue to add value to our customers, reduce cost and improve quality.
For example, 3D printing could be effective if your design asks for a straightforward geometric form. However, methods like CNC machining or injection molding may be more suitable if you are working on detailed and complicated designs.
What level of detail should you include in your proof-of-concept model? Do you want to make a precise replica of the finished product? Choosing the best prototype approaches and procedures would be easier if you knew the complexity level.
You may give your ideas life and evaluate their functioning, design, and compatibility with the help of plastic prototyping. It lets you test your plastic product concept and assess its viability, usefulness, and innovation.
While computer simulations and schematics are helpful, they only explain how your product will work in actual situations.
Plastic prototyping is a technique that enables you to use plastic materials to build a prototype or actual model of your intended product. Before going on with mass manufacturing, it’s a valuable strategy for testing and verifying your idea.
Plastic prototyping provides a variety of applications and benefits that may significantly speed up your product development process. Rapid prototyping techniques for plastic may help you save time and money while retaining the accuracy and viability of your ideas.
Texas Injection Molding offers in-house tooling design and engineering support for new injection molds and has both in-house and outside plastic mold building resources to provide cost effective solutions to new tooling. Our in-house tooling group provides routine preventative tooling maintenance and tooling repairs to keep customer production running on-time.
The success of your plastic prototype depends critically on the material you choose. Think about the traits and qualities you want to duplicate or test. The material selected will impact strength, adaptability, aesthetics, and temperature resistance.
The intended smoothness or texture of your prototype’s surface finish might impact the price. The cost of total post-processing operations such as polishing, painting, or coating will also increase.
Although short turnaround times may be achieved using rapid prototyping methods, the intricacy of your design and the chosen manufacturing process might affect the lead time.
Due to its quick manufacturing capabilities, 3D printing is often preferred when time is essential. However, the setup and tooling times for processes like CNC machining or injection molding might be longer.
Selecting the most efficient way to implement your concept is ensured by evaluating the intended shape of your prototype.
Plastic prototyping is essential to developing new products since it helps bring imaginative concepts to life. Before proceeding with mass manufacturing, you can visualize and test your ideas.
Knowing precisely what you want the prototype to do can help you concentrate your efforts and allocate your resources efficiently.
Our cutting-edge manufacturing skills and knowledgeable staff guarantee that your prototypes are manufactured precisely and quickly, saving you time and money.
How your plastic prototype is made might affect the price. Typical processes include CNC machining, 3D printing, and injection molding.
Injection molding is often used to manufacture plastic components. High production efficiency and consistent quality are offered, but only after a significant investment in tooling.
Every prototype project, including plastic rapid prototyping, depends on time. Consider the project’s timeline restrictions when evaluating the lead time needed to produce the prototypes.
Your prototype’s design complexity significantly influences the cost. More time and resources are needed to create sophisticated designs with intricate elements, which might raise the final price.
This article will examine four common methods for manufacturing plastic prototypes: vacuum casting, 3D printing, CNC machining, and injection molding. You will explore their advantages and uses to decide which method suits your prototyping requirements.
For limited production runs or complicated geometries, 3D printing and CNC machining may be more cost-effective than injection molding owing to lower tooling costs.
Several procedures are available for producing plastic prototypes, each with a unique set of benefits and factors to consider. This article will examine four standard processes.
Typical choices include nylon, polypropylene, ABS, and polycarbonate. Due to causes like performance, performance criteria, or availability, certain materials may be more costly than others.
You benefit from seeing and touching your product in actual form when you use plastic prototyping. This gives you a more precise understanding of its size, characteristics, and general shape. The prototype’s ergonomics, user experience, and room for development may all be better understood by touching the part in your hands.
Using prototypes, you may evaluate several design options, streamline production, and eliminate waste. Purchasing a plastic prototype in advance might save costs and improve product quality.
You may choose the best material by identifying the qualities of the material that match the needs of your project. This guarantees that your prototype resembles the finished product, allowing you to perform reliable and accurate evaluations.
Kemal Plastic Injection Molding Services can be a trustworthy collaborator in all phases of the plastic prototype process.
Kemal Plastic Injection Molding Services can help you with anything from idea development to creating high-quality plastic prototypes owing to their experience in prototyping technology.
The cost of your prototype may increase if it has many parts or has to be put together. Prices may rise due to intricate assembly procedures.
Plastic prototypes are ideal for iterative and rapid prototyping. A physical prototype lets you swiftly apply feedback and testing findings. Iterative development cycles reduce time to market and setbacks.
Plastic prototypes may be made using the flexible and economical vacuum casting technique. It includes creating a silicone cast using a master pattern, often created via CNC machining or 3D printing.
Integrity – We will be known in the industries we serve as a company that fulfills our commitments and operates to high ethical standards.
It’s essential to remember that plastic prototyping is more than simply making a physical version of your product; it’s also a tactical tool that enables you to iterate, improve, and verify your ideas before going into mass production.
The price may vary depending on your needed prototypes. Spreading out fixed expenses by producing many prototypes helps lower per-unit prices.
An Adventure to Live – We will continuously evaluate business opportunities and seek to realize those opportunities that provide great value to the customer, inspire the organization, and provide great satisfaction to the organization when realized.
It allows you to demonstrate your product’s size, shape, and general look, making it easier for stakeholders and prospective buyers to understand your idea. Observing your concept come to life can enable you to get user input and make the required adjustments.
There are a few essential factors to consider while working on a plastic quick prototyping project to guarantee an excellent outcome. By carefully weighing these aspects, you may decide how to optimize the prototype process best to match your unique demands.
Before mass production, creating a plastic prototype can save you time, effort, and money. Early detection and correction of design flaws may result in cost savings and decreased product failure.
Texas Injection Molding provides custom plastic injection molding services for OEM manufacturing and consumer products. Located in Houston but also serving in Austin, San Antonio, and the S. E. United States, Texas Injection Molding provides product design assistance and engineering services for the development of plastic injection molded products. We offer decades of experience in processing commodity and custom engineered plastic resins and partner with the world’s leading resin manufacturers and custom compounders to bring solutions to complex plastic engineering applications. We strive to be known in the markets we serve as the best partner for custom plastic injection molding manufacturing services that operates to the highest ethical standards.
GETTING A QUOTE WITH LK-MOULD IS FREE AND SIMPLE.
FIND MORE OF OUR SERVICES:
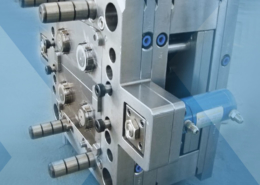
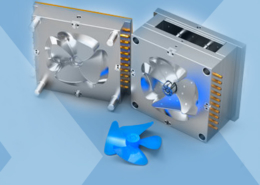
Plastic Molding

Rapid Prototyping
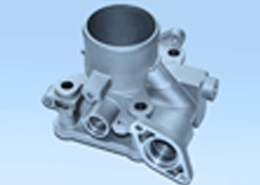
Pressure Die Casting
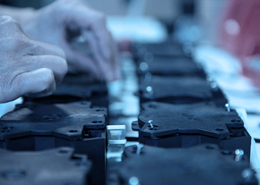
Parts Assembly
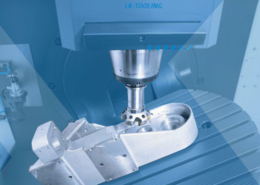