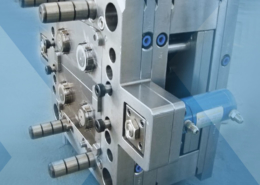
Polypropylene (PP) Injection Molding - plastic granules for injection molding
Author:gly Date: 2024-10-15
The Thermoset Transfer molding process starts with pre-forming a cylindrical “pill” of material of the proper weight. The pill is usually hand loaded into a mold, where a plunger pushes the material into the cavity, and the thermoset material cures, through a chemical reaction, under heat and pressure.
As an amorphous engineering material, PC features an exceptionally high resistance to impact / heat, great clarity, outstanding sterilizability, admirable flame retardancy, and good resistance to stain. The notched Izod resistance to impact of the PC materials is pretty high, with a low and consistent mold shrinkage rate of (0.1 – 0.2 mm).
While both of these methods are more labor-intensive than injection molding, some thermoset materials are only available in transfer and compression grades. In order to achieve some of the special properties of thermoset materials, compression and transfer molding processes are sometimes necessary.
Thermoset materials are typically used in applications where retention of mechanical properties at extremely elevated temperatures is a requirement. The thermoset manufacturing process requires significant experience with plastic injection molding. Whether using thermoplastic or thermoset material, injection molding is the most cost-effective method because it can be automated, eliminating labor-intensive preliminary or secondary operations.
We produce custom-molded plastic parts for OEMs in the Defense, Avionics, Instrumentation, Medical, Consumer Products, Energy, and Transportation industries. ISO 9001 certified ITAR Registered, DoD Certified Munitions Supplier, QPL Approved, FDA Class I, II, and III medical devices. The parts we create range from dime-sized to gallon-sized, from parts designed to last 50 years to those designed as disposables, in quantities from 500 pieces to 20,000,000 pieces per year, and for environments as pleasant as an air-conditioned office to as unforgiving as an oil drilling borehole.
Polycarbonates, more commonly known as PC, are a group of thermoplastic polymers containing carbonate groups in their chemical structures. Although PC are commercially available in a diversity of different of colors (either translucent or opaque), the raw material is able to transmit light internally in a capacity similar to that of glass. The PC material is typically applied to produce a wide range of materials and are especially useful when the product requires outstanding resistance to impact and / or good transparency (for example, when used in production of bullet-proof glass). The PC material is most commonly applied for production of plastic lenses in eyewear, medical equipment, plastic auto components / parts, protective gears, greenhouse material, digital disks (CD, DVD, and Blu-ray), as well as exterior lighting fixtures. PC is also very resistant to heat and is able to be mixed with flame retardants without causing significant degradation to the material. PC is a group of engineering plastic materials, since they are able to be used for more capable and robust applications, e.g. in “glass-like” surfaces that are strongly resistant to impact.
PC injection molding materials that have a high molecular weight (meaning the melt flow rate is rather low) usually features higher mechanical properties, but it becomes more difficult to process such grades of PC. It is a good idea to choose the PC type for a specific application on basis of the desired requirements, e.g. for high impact resistance, choose a low-MFR (Melt Flow Rate) PC; on the contrary, for optimal processability, choose a high-MFR (Melt Flow Rate) PC.
During the hydrolysis (the chemical breakdown of a compound due to reaction with water) process, it is very likely that some types of PC materials can be harmful when contacting with food, due to the unwanted release of Bisphenol A (BPA). The most commonly produced PC types are created by combining BPA and COCl2, but there are BPA free PC materials available, which are especially marketable for applications that involve perishable water or food.
PC is one of the polyesters of carbonic acid, and all of the general-purpose PC materials are produced on basis of bisphenol A (BPA). In the molecules, the BPA component leads to its relatively higher glass transition temperature of 150 degrees Celsius (or 302 degrees Fahrenheit), while the rotational mobility of the carbonyl group inside the molecules allows the material to be highly ductile and tough.
The most common way to produce plastic parts is via the injection molding process. When the process uses raw materials that can be heated to soften or melt, it is called thermoplastic injection molding. Many plastic parts are made from thermoplastic materials including Nylon, Polycarbonate, and ABS. When the process uses materials that permanently solidify through a chemical reaction, it is called thermoset molding. Thermoplastic injection molding, which relies on the rapid cooling of the melted plastic material inside the mold, typically results in a much faster processing cycle than thermoset molding. Typical thermoset materials include DAP, Phenolic, and Epoxy.
We produce thermoplastic and thermoset custom molded parts using hundreds of different standard and custom plastic formulations (see alphabetical listing below) and offer a wide spectrum of insert-molding (plastic molded around metal parts), over-molding (plastic molded around plastic parts), and post-molding services (machining, assembly, printing, laser marking, ultrasonic welding, heat staking, etc). We specialize in a wide spectrum of molding services, including insert molding and over-molding services. 95% of the parts we produce are smaller in size than a gallon jug of milk, weigh less than one pound, and have a maximum dimension shorter than 12 inches.
Since our founding in 1962, we've offered many types of plastic molding processes to meet our Customers’ diverse needs including thermoplastic injection molding, insert molding, wire over-molding, thermoset injection, compression, and transfer molding. No matter the process, we can recommend and manufacture plastic parts in the appropriate material for any project.
One specialized type of plastic injection molding performed at Rebling is called insert molding. This process involves molding plastic around another part, which could be made of metal or another plastic material. Wire over-molding, or wire plastic molding, is a special type of insert molding where plastic is molded over different sizes of wires to form a plug or strain relief.
No matter which molding method is used, processing parameters for each part are documented and stored in machine memory to insure lot-to-lot consistency.
Using modern, state-of-the-art primary and auxiliary processing equipment enables Rebling to provide the highest quality molded parts available anywhere. To ensure part consistency and minimize machine downtime, all processing equipment is serviced using an extensive preventative maintenance program. This includes all the Customer-owned molds and fixtures which undergo routine maintenance during and after production runs. Every mold is tracked for a number of cycles in our ERP system to ensure maintenance is performed at the proper interval.
According to the publication, AZO Materials, the PC injection molding plastic material was invented in the middle of the 20th century at the same time by GE in the US and Bayer in Germany. In today’s society, the material is produced by a great number of companies worldwide, each usually having their own manufacturing processes, exclusive formulas and trade names, including well known variant resins, such as Lexan® by produced SABIC, or Makrolon® produced by Bayer MaterialScience.
Thermoset Compression molding uses a loose, powdery molding material that must be weighed before an operator or automated equipment places the material into an open mold cavity. The press applies heat and pressure until the part is cured.
Whether you have a drawing, a sample, or simply an idea, our team can design the part and select the material which best fits your needs, perform 3D modeling, create full-size prototypes, design and create the molds, perform first article inspection and then produce production quantities. We are ITAR registered and ISO 9001 certified.
In the market, many different industry grades of the PC injection molding plastic materials are commercially available, most of which are referred to by their generic name (PC). Usually, they are differentiated by how much reinforcing glass fiber they contain, as well as the difference in melt fluidity among them. Some PC materials are combined with additives, such as the “UV stabilizers” that help protect it from long period direct exposure to the sunlight. PC materials that are plastic injection moldable may contain some other additives, such as mold release agents that help lubricate the mold during the injection molding process. Finished PC materials are usually sold in rods, cylinders or sheets.
The melt viscosities of PC are usually Newtonian up to shear rates of 1000 s-1 and reduce more than that. The Heat Deflection Temperature under Load usually ranges between 130 and 140 degrees Celsius (or 266 – 284 degrees Fahrenheit) and the Vicat Softening Point is usually around 155 degrees Celsius (or 311 degrees Fahrenheit).
GETTING A QUOTE WITH LK-MOULD IS FREE AND SIMPLE.
FIND MORE OF OUR SERVICES:
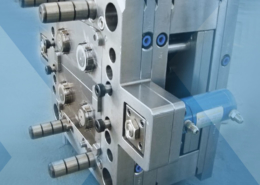
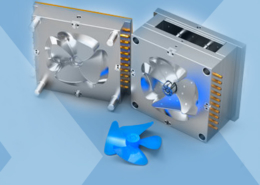
Plastic Molding

Rapid Prototyping
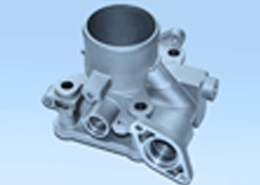
Pressure Die Casting
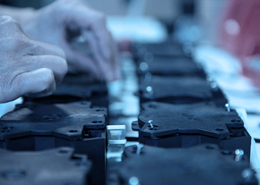
Parts Assembly
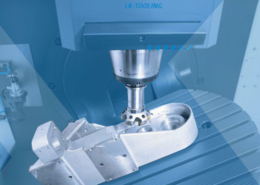