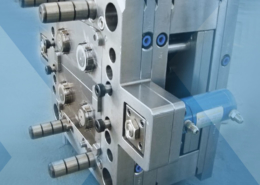
Polyethylene Terephthalate (PET) for Injection Molding - polyethylene terephthal
Author:gly Date: 2024-10-15
HITOP Industrial was founded in 2002 and is now an injection molding big gun. They have the people and services – mold design, creation, prototyping, and production of injection molded parts.
Their online marketplace is the bridge between manufacturers and a global network of suppliers. Businesses can source parts, get quotes and lead times, and reduce development time and supply chain volatility.
Kaysun works with you throughout the entire process. This is evident from their pre-production phase where it spends a lot of time understanding your application. The partnership approach ensures a seamless transition from design to production and reduces potential issues and time-to-market.
Cold runner systems come in two primary forms: two-plate and three-plate systems. The two-plate system is the simpler of the two; it uses a single parting line, allowing the plastic material to enter the mold on one side. While it has fewer moving parts, this system can only manufacture less complex plastic parts.
Deciding between a hot runner and a cold runner system is not a straightforward choice; it hinges on several factors. The type of product you intend to manufacture, your budget constraints, the materials you’re planning to use, and the scale of production are crucial variables influencing the decision. Choosing between hot and cold runners depends on your manufacturer’s capabilities, as top manufacturers like those listed in our China Mold Manufacturer article often have advanced technologies.
Britech Industries is experienced and innovative. Over 35 years in the business and always adding more to what they do to meet customer needs.
However, cold runner molds are not free from downsides. They produce more waste in the form of a solidified “sprue.” The slower cycle times could affect output rates, and the variety of moldable parts is somewhat limited. Balancing these pros and cons is key to choosing which system is the best fit for manufacturing requirements.
In the end, understanding your project’s unique requirements and the characteristics of your desired plastic parts is key to making an informed decision.
The cold runner’s disadvantage lies within the production of scrap, as the leftover plastic in the runner is ejected with the final product, producing waste resin. Additionally, utilizing a cold runner system might restrict the types of thermoplastics you can work with, particularly heat-sensitive polymers.
Choosing the right injection molding company means high-quality parts and fast production. This article looks at the top 10 plastic injection mold companies worldwide. Here are some of them:
The cost comparison of hot runner vs cold runner is reliant on several factors besides the upfront mold price. While cold runner systems are less expensive initially, their ongoing operational costs can increase due to slower cycle times and the need to recycle or dispose of the runner waste.
That’s where expert services like those provided by Aco Mold can prove invaluable. Specializing in custom injection molding services, Aco Mold can offer guidance and expertise to help you navigate the technical details. The breadth of their experience with both hot runner and cold runner systems means they can cater to your specific needs effectively and professionally, whether your goal is high volume, faster cycle times, or a more budget-friendly solution.
With over 20 years of experience in the industry, HITOP has a history of exporting high-quality molds to the world. They can handle all sizes and weights of molds, showing their strength.
Hi, I am Sparrow Xiang, COO of the HiTop company, me and my team would be happy to meet you and learn all about your business, requirements and expectations.
Injection molding, a manufacturing process frequently used in the production of plastic parts, uses varying systems to achieve its purpose. The main categories are hot runner and cold runner systems, also called hot runner molds and cold runner molds, respectively.
Cold runner molds provide several benefits, one of which includes low startup costs—the simpler design and functionality mean a less-expensive mold and lower maintenance costs. Cold runner molds also offer more flexibility. They can be used with heat-sensitive polymers or those that may degrade in hot runner systems. Plus, color changes are easier and faster in cold runner molds since there’s no risk of leaving behind molten material.
In 1987, they moved to a new, larger facility in Rochester Hills, Michigan, and became Hi-Tech Mold & Engineering. This was the start of a period of rapid growth, with four more plants added in Rochester Hills by 1995.
Second, they put quality first. ISO 9001 certified and using high-grade materials, your parts will meet the highest standards. Third, Valencia Plastics is eco-friendly. They use recycled resins and energy-efficient practices whenever possible.
Founded in 1982, Bennett Plastics is your go-to custom plastic injection molder in the NY area. Their 36,000 sq. ft. facility in Paterson, NJ, has state-of-the-art equipment. It also has a team of experts to get the job done.
From design and prototyping to mold creation, manufacturing, and fulfillment. No outsourcing and no complexity; they cover the entire process. Their commitment to quality and American manufacturing means consistent results, fast turnaround, and good parts.
Founded in 1984, Fathom Digital Manufacturing has grown from a traditional manufacturer to a leading on-demand digital manufacturing platform.
Looking for a quality injection molding partner that goes above and beyond? Contact HITOP Industrial today to talk about your project and get a quote.
Hi-Tech Mold & Engineering is the ideal partner for a business enterprise in search of a comprehensive one-stop manufacturing solution.
Address: Ironwood Plastics, Michigan Location (Ironwood Division), 1235 Wall Street, Ironwood, MI 49938. P: 906.932.5025
It analyzes complex parts in real time and matches buyers with the best suppliers globally. Time and money saving and production optimized. Xometry also has convenience in spades through its marketplace.
The plastic injection molding world is huge, and many companies are vying for your business. Choosing the right one depends on your project needs and priorities. This article listed the top 10 injection molding companies in the world, their areas of expertise, and unique selling points.
The company values everything, be it high-quality parts, cost savings, and product improvement recommendations. Their commitment to reliability means projects will get done on time and on budget.
HITOP is committed to assisting customers by offering a comprehensive one-stop solution, encompassing product design enhancement, initial sample creation, mold fabrication, injection molding, and product assembly.
Several reasons are there to choose Four Processes for your injection molding. Open communication and honesty build trust that everyone is working towards the same goal.
Rapid prototyping and secondary processing services are also available for automotive, electronics, and medical products.
This has accumulated over forty years of experience, which in turn equates to their knowledge of the sector. Client-centric approach equals the organization’s focus on client needs in each phase of the process. It ensures the timely delivery of products.
Both hot runner and cold runner systems have their rightful place in the intricate world of injection mold manufacturing. Hot runner molds offer swift cycle times, and minimal waste, and are ideal for large-scale production. On the other hand, cold runner molds provide a cost-effective alternative with easier color changes, making them perfect for heat-sensitive materials or smaller-scale operations.
In 1974, Hubert Fox, a US Army veteran and entrepreneur, founded Four Process Ltd. started as a small machine shop. More than a manufacturer, Four Process is your reliable friend working with you through the entire process.
They do it all in-house, from product design and prototyping to final production and fulfillment. So, you have one-stop shopping for all your plastic parts needs.
Cold runner systems, with their easier handling of heat-sensitive polymers and simpler setup, are commonly seen in the production of smaller, less complex parts. They’re also the go-to choice for low-volume production scenarios and jobs requiring frequent material or color changes.
And the company is run by a team of old hands with tech, finance, and manufacturing experience. That’s cutting-edge tools, options, and leadership – Xometry is the future of smart manufacturing.
Quality and service are evident in their just-in-time inventory and custom manufacturing. Whether you require rubber parts, custom extrusions, or injection molded plastics, Britech can be a one-stop shop for your needs.
As an ISO company, HITOP puts quality first. Their strict adherence to international standards means both their injection molds and end products are top-notch.
HITOP Industrial has high-capacity molding machines that can mold up to 3500 tons – multi-cavity, two-color, gas assist, and low-pressure molds.
The products include 3D Printing (plastic and metal), CNC Machining, Injection Molding & Tooling, Sheet metal fabrication, Prototype Fabrication, and more.
Hot runner molds bring with them a host of advantages. For starters, they lead to faster cycle times, making the manufacturing process significantly quicker. This system reduces the amount of scrap produced during the molding cycle, saving valuable resin and contributing to a greener manufacturing environment. A hot runner mold also allows for color changes and molding larger parts, widening the scope of manufacturing possibilities.
We are committed to helping you elevate quality standards, fostering enterprise growth, and actualizing your internationalization strategy.
Hot runners keep the plastic in a molten state via heated runners, while cold runners allow the molten plastic to cool and solidify within unheated runners. Understanding the nuances of each system helps deliver the final product with the best quality.
But if you want cost and global, HITOP Industrial might be the way to go. Their quality and innovation, combined with competitive pricing, make them a contender.
A cold runner system can potentially lead to slower cycle times – however, it does offer benefits. A significant one is that the manufacturing process is simpler, and the mold’s design and maintenance are less complex. This simplification may result in lower initial and maintenance costs, an enticing factor for many manufacturers.
Conversely, cold runner systems may be the best choice for handling heat-sensitive polymers. These systems prevent material degradation that can happen when such polymers are subjected to prolonged exposure to high temperatures found in hot runner systems. Thus, understanding your material’s characteristics will guide you toward the most suitable runner system.
Ironwood Plastics has several reasons why you should choose them for your complex molding needs. They have a team that has over 200 years of combined experience. Also, they handle your toughest projects; insert molding and engineered materials are our specialty.
The main products include Injection Molding, 3D Printing/Prototyping, Custom Plastics Mold Design, Value-Added Finishing Warehousing and Fulfillment.
In the hot runner mold system, the plastic injection molding process results in no wasted resin, thus offering another form of efficiency: material use. Therefore, with hot runner molds, you can anticipate minimal material waste, effective use of energy, and quicker cycle times.
The hot runner vs cold runner debate is not new in the plastic components manufacturing industry. Each system has its unique range of advantages, disadvantages, and best choice of materials. The primary difference between these two systems lies in the pathway, or runner, whereby the molten thermoplastic travels from the heating cylinder to the individual molding cavities. Understanding the basics of injection moulding is key to choosing the right runner system, which is why we recommend reading our Injection Moulding Parts Basics for foundational knowledge.
However, it’s not just about speed. The hot runner approach is also about efficiency. The molten material travels straight from the heating cylinder to the mold cavities without leaving any scrap, fundamentally different from the cold runner system.
Founded in 1979, Ironwood Plastics has been a leader in complex injection molding for years. Acquired by CTB, a Berkshire Hathaway company, in 2010, we continue to invest in the latest technology and quality craftsmanship.
The internet helped them grow, and now they have dedicated divisions for custom rubber extrusions and injection molded plastics. They are a one-stop shop for all rubber and plastic needs.
That said, there are cons to consider. For instance, the initial setup cost of a hot runner mold is higher than that of their cold runner counterparts, which can deter manufacturers who are mindful of initial expenses. Besides, the technical complexities of maintaining a hot runner system can increase the overall operation cost.
We’ll look at their experience, niches, and what sets them apart. Whether you’re looking for a partner for your next project or just interested in plastic molding, this is for you.
Our Ironwood, Michigan, and Two Rivers, Wisconsin, facilities have a team with over 200 years of combined experience. So, you can trust us with your toughest projects.
Britech Industries was founded in 1984 as a small Florida supplier of basic rubber parts. They started by serving local manufacturers with extruded rubber products like grommets. Their customer-centric approach led them to add custom molded parts and die production in 1995.
Established in 1982 as Amtech Mold & Engineering in Fraser, Michigan, Hi-Tech Mold & Engineering has become an industry leader. Throughout the years, they have added capabilities and facilities to meet customer needs.
They serve a wide range of clients. It includes some of the world’s most innovative companies in technology, defense, aerospace, medical, automotive, and IoT.
Several reasons to choose Bennett Plastics for your injection molding needs. They will communicate openly and work closely with you to ensure your project meets your vision.
It offers Plastic Injection Molding, Blow Molding Products, Design and Development, Mold Making, Inventory Management, and Additional Services.
In contrast, the three-plate system employs two parting lines, offering the advantage of simultaneous ejection of the molded part and the runner. The three-plate system can mold more complex, yet smaller, plastic parts with ease. However, the intricacies and additional moving parts could lead to slightly increased maintenance efforts.
Injection molding is used in many industries to make so many different parts. It’s a process of injecting molten plastic into a mold cavity that cools and solidifies into shape.
Apart from this, it covers Custom Inventory Management, Component Sourcing, Prototyping, Part Assembly, Specialized Packaging, Product Testing, and Program Management.
For companies looking for a reliable partner with a history of complex projects, Ironwood Plastics stands out. They have the experience and the technology to handle the toughest jobs.
Fathom’s commitment to innovation and full service makes them a great partner for your product development journey. They offer everything from rapid prototyping to low to mid-volume production.
Founded in 2000, Valencia Plastics has become a full-service plastic injection and blow molding manufacturer. Their mission is to turn ideas into products and guide clients through the entire development process from concept to shelf. They are a recommended partner for companies looking for reliable plastic parts.
It offers CNC Machining, Additive Manufacturing, Plastic Injection Molded Components, Value-added assembly, Product Design and Development.
Need metal injection molding, die casting, or metal stamping? Xometry has access to all the manufacturing capabilities you need, and it is an all-in-one online platform.
The insulated hot runner keeps the plastic material molten through the thermal insulation that envelops an unheated runner. On the other hand, the heated hot runner mold features an externally heated runner. The heating permits a uniform temperature throughout the molding cycle, ensuring consistent quality of the molded parts.
The company also invests in the latest technology and processes to meet your specific needs. Their core values – respect, trust, excellence, communication, and teamwork – guarantee a collaborative and professional working relationship.
The type of molded part or product you want to produce is crucial when selecting the right runner system. Hot runner systems, thanks to their efficient cycle times and material usage are often used for the high-volume production of plastic parts, especially in precision industries like automotive and medical instruments. They’re more suited for manufacturing larger parts and components that require exact dimensional stability.
Within the injection molding domain, the hot runner mold embodies a popular system used in the formation of plastic parts. With a manifold system that’s heated, the hot runner mold ensures the plastic remains in a molten state through the entire molding cycle, from the nozzle to the mold cavities. This approach can lead to faster cycle times, thereby speeding up the manufacturing process.
Despite the slower cycle times, both the insulated and heated hot runner systems have their merits and drawbacks. Understanding the performance of each is crucial to deciding the best option for a specific manufacturing process.
Yes, definitely. Material choice is an important consideration in the hot runner vs cold runner debate. Hot runner systems excel in working with a wider variety of polymers. High-temperature thermoplastics, for example, can maintain their molten state longer in a hot runner system, enhancing the final product’s consistency and quality.
Have you ever thought about how all those plastic things around you got there? From water bottles to phone cases, plastic injection molding is the magic behind many everyday items. It uses molds to shape molten plastic into specific shapes.
A cold runner mold, unlike its hot runner counterpart, is not heated. The molten thermoplastic travels from the heating cylinder to the molding cavities via an unheated runner. This journey allows the molten plastic to cool and harden before being injected into the mold cavities.
Several reasons to choose Valencia Plastics for your plastic molding needs. First, they offer a complete solution, from concept development to production.
Their one-stop shopping eliminates the need to manage multiple vendors and saves you time. Fathom has a national footprint with over 450,000 sqft of manufacturing space across 12 facilities. All that capability is under one roof.
On the flip side, hot runner systems, despite their higher initial cost, usually have lower operating costs. They leave no runner waste, significantly reducing material costs. Faster cycle times also lead to higher productivity, appeasing those who emphasize efficiency and speed. Still, they require careful maintenance and can be more expensive in terms of energy consumption. Weighing initial investments against long-term benefits is key in the hot runner vs cold runner decision-making process.
Founded in 1946, Kaysun Corporation has a long history in the injection molding industry. It aims to make a positive impact on people’s lives through the products we make and the services we provide. Kaysun is more than just a supplier; it is a partner that will exceed your expectations.
HITOP doesn’t just sit back and settle for the status quo. They actively seek and integrate the latest technology to achieve higher precision in their injection molding process. That’s what excellence means to them.
But HITOP’s goal is not just to comply. They want to create real value for their customers, drive their satisfaction, and exceed their expectations. HITOP sees customer satisfaction as the starting point, not the finishing line, of its service.
Xometry was founded in 2013 and is now a leading digital company in the $2.4 trillion manufacturing industry. The company is based in Maryland and uses AI to make manufacturing and procurement easier.
The company offers Short-run, medium-run, and long-run Injection Molding, Insert Molding, Over Molding, Hot Runner Molding, and Cold Runner Molding.
GETTING A QUOTE WITH LK-MOULD IS FREE AND SIMPLE.
FIND MORE OF OUR SERVICES:
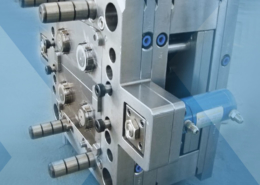
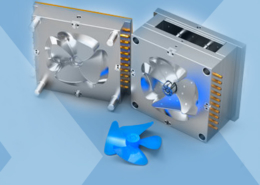
Plastic Molding

Rapid Prototyping
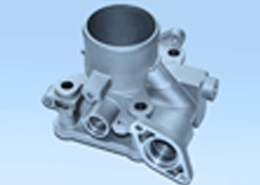
Pressure Die Casting
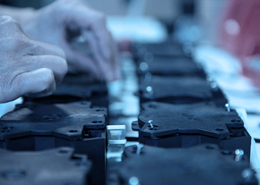
Parts Assembly
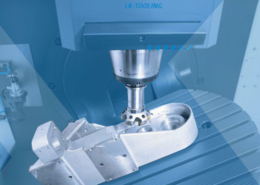