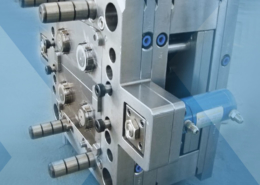
Polyethylene | Custom USA-Made Injection Molded Parts - polyethylene injection m
Author:gly Date: 2024-10-15
Injection molding enables mass-producing plastic parts with consistency, detail, and efficiency. While a highly cost-effective process, developing an accurate budget requires evaluating numerous cost components. We’ll explore fixed and variable costs, quoting considerations, design strategies, tooling factors, and advice for minimizing overall expenditures without sacrificing part quality.
In general, small and simple molds can start at around $1,000, while larger and more complex molds can cost tens of thousands of dollars. The price of the mold is just a small part of the overall cost of manufacturing a product though. It is important to factor in the cost of materials, labor, packaging, and shipping when determining the final price of a product.
Understanding how to accurately estimate and minimize injection molding costs is key for creating viable, cost-optimized plastic products. This comprehensive guide covers the factors comprising total molding costs and advice for effective budgeting.
Finally, the company that makes the mold can also affect its cost. Typically, an experienced manufacturer that makes molds for many industries and types of products will have experience and be able to make the mold in less time, which can bring down your cost.
The size and complexity of the mold are perhaps the most important factors in determining its cost. A simple mold for a small object may only cost a few hundred dollars, while a more complex mold for a larger object could cost several thousand.
This approach has several benefits over traditional injection molding methods, including increased accuracy and precision, as well as decreased production time and costs.
Even small optimizations add up significantly over production lifetimes. An experienced molder provides valuable guidance.
Using a multi-cavity mold can be more expensive than using a single-cavity mold, but it can also be faster and more efficient. If you need a large number of parts, or if your part is complex and has many features, a multi-cavity mold may be the best option.
Plastic substrates can be shifted or easily deformed by overmolding pressures if not supported properly. To accomplish this the tool needs to be designed with geometry that captures the insert. This is most often done with features in the tool steel that the insert can be placed onto and clamped against as the tool closes. Designers need to be aware of this because these support locations will prevent overmold material from flowing into these areas, meaning they will be exposed in the resulting part. Care should be taken to design adequate support features in the substrate that are either hidden or functional in the component.
The steel,size and complexity of the mold will have the biggest impact on the price, but other factors like the material and the turnaround time can also affect the cost.
When it comes to injection molding, the design of self-mating parts is an important consideration. This is because self-mating parts must be able to fit together perfectly in order to function properly. Injection molding is a process that can create very precise parts, so it is important to take advantage of this when designing self-mating parts.
The cost of a plastic injection mold has changed significantly over time. In the early days of injection molding, the price of a mold was very high. This was due to the fact that the process was new and there were not many companies that knew how to build molds.
As the years went by, and more companies began to specialize in mold building, the prices began to come down. Today, the cost of a plastic injection mold is much lower than it was in the past.
When considering the size of a plastic mold, it is important to take into account the reasonable price for the project. Depending on the desired outcome, the size of the mold may need to be changed in order to accommodate for different parts.
Ultimately, the decision of what size plastic mold to use should be based on what is most likely to produce the desired results at a reasonable price. Taking into account all of these factors will help ensure that the final product is exactly what is needed.
A wide variety of materials such as metal hardware, plastics and fabrics are commonly used across an extensive range of molding applications today. In particular, these types of processes enable design freedom and improved part performance in molded parts that otherwise would be cost prohibitive or impossible.
The molder then factors in their production capabilities, overhead, and desired margins when preparing a detailed quote. Leave buffer for potential changes in the design process.
Alternatively it can also be possible to achieve a chemical bond between substrate and overmold. This method is typically only viable if the substrate is also a plastic material. By selecting substrate and overmold materials that are compatible it is possible to form chemical bonds during overmolding that will entirely lock the overmold in place over the substrate. In some cases resins will be specifically rated to bond with particular substrate materials, especially when working with TPEs.
In the plastics industry,modifying and reusing molds is a common practice. It can be done with either new or existing molds and can save companies time and money.
One reason why the cost of a plastic injection mold has decreased is because of advancements in technology. In the past, molds had to be built by hand which was very time consuming and expensive. Today, molds can be built using CNC machines which are much faster and less expensive.
The fundamentals for overmolding a component are the same in all cases. The design of the components needs to consider several process-related factors such as tooling and material compatibility. As a prerequisite, the substrate material getting overmolded needs to be robust enough to survive the injection molding process where it will be exposed to high heat and extreme pressures as molten plastic flows past it.
By comparison, thermal and ultrasonic hardware installation post molding can reduce the mechanical retention of the insert in the part. These processes locally heat the plastic and flow it around rib and knurled geometry in the hardware to create mechanical retention. Inserts designed for insert molding utilize much more significant retention features as the molding process can fully pack material around the body of the insert to achieve much higher strength ratings for insert molded components.
Insert molding is used on applications like handles and grips because they require a high level of aesthetic and tactile focus due to the amount of interaction with end users. Designers can enhance the ergonomics and feel of these components by overmolding them with soft elastomeric materials known as Thermoplastic Elastomers or TPEs. These polymers come in a variety of material types and durometers so the overmold material can be tailored to a specific set of product requirements.
Simpler molds with standardized, interchangeable parts cost substantially less. Partnering with an experienced mold maker is vital for optimizing these tradeoffs.
In some cases a part can be progressively overmolded in a series of tools to build plastic thicknesses that would be impossible to mold in a single shot. This allows for parts with extreme thick, thin or other detailed geometry to be produced for ergonomic and aesthetic purposes. Soft gasket features can also be molded into sealing glands so critical sealing geometry is permanently captured in place.
When an insert gets overmolded the bond between the two needs to survive the end application requirements. This can be accomplished through a mechanical interlock or with a chemical bond.
Overmolding and insert molding offer creative opportunities to get innovative with new part designs. If you have a part design that could be insert or overmolded please consider reaching out to Mack Molding to get feedback on the design and cost of your product. Mack has experience with hundreds of overmolded product in its portfolio to guide you in the right direction.
The mold constitutes a significant upfront fixed cost, so minimizing its expense is crucial. Factors influencing mold costs include:
Injection molding is a process that was invented in the late 1800s, and it has come a long way since then. The first plastic injection molding machine was created in 1872 by John Wesley Hyatt, who was trying to find a way to make billiard balls without using ivory. Ivory was becoming increasingly expensive and difficult to obtain, so Hyatt came up with the idea of using a mold to create the balls from celluloid instead.
It is also possible to promote bonding by prepping the substrate surface with primers, etching chemicals or plasma treatment.
Mechanical hardware is another common application benefitting from insert molding. By placing and capturing items like threaded inserts, pins, bushings, etc. in the tool before injecting the plastic, it is possible to mold around these components to mechanically capture the hardware into the molded part. In most cases this replaces secondary hardware installation processes accomplished via bonding, ultrasonics or thermal insertion. Depending on the application and volumes of the product, this could yield cost savings and increase manufacturing throughput.
It is also necessary to take into consideration how the plastic mold will be used. If it is for a one-time project, then a smaller size may be more cost effective. On the other hand, if the mold will be used multiple times, then a larger size may be necessary in order to avoid having to replace it frequently.
As the world increasingly moves away from traditional manufacturing methods, on-demand production is becoming a more popular option for businesses. Plastic molding is one area where on-demand production can be a great option for businesses. There are many benefits to choosing on-demand production for your plastic molding needs, including a reasonable price.
Additionally, these processes can be combined. For instance plastic can be molded over plastic that has already been molded over plastic. Plastic also can be overmolded over plastic that as already had metal insert molded into it. Another application may call for two materials, e.g. metal and rubber, to be insert molded into plastic at the same time.
Estimating injection molding costs requires understanding the diverse factors comprising the total expenditures. Simplifying part geometries, standardizing tooling, and optimizing processes offer significant savings over a program lifespan. Collaboration between product developers and molders, combined with emerging technologies, ensures cost-effective, quality plastic part production.
If the mold is made of a more expensive material like titanium, then the price will increase as well. Also, if the mold is being produced in large quantities, then it will be less expensive per unit. The lead time should also be considered.
If you’re looking for a way to save on production costs, you may want to consider using overmolding plastic mold. Overmolding is a process that allows you to mold two or more different materials together, which can help reduce waste and eliminate the need for separate assembly processes. Additionally, overmolding can improve the strength and durability of your products.
Generally, the cost of a plastic injection mold starts at around $3,000. This is for a simple mold that is relatively small and does not have any intricate designs. If the mold is larger or more complex, the price will increase.
It is also critical the seams between the overmold and insert or substrate are designed so the tool steel can successfully shutoff against the substrate to prevent overmold material from flashing outside of the intended geometry. Shutoffs are best made when the action of the tool closing can create a small amount of preload or crush on the part to successfully seal the overmold cavity. When the overmold parting line is more dynamic, special attention must be given to the shutoff geometry and substrate support in the tool to prevent flash from occurring.
Insert molding and overmolding combine multiple components into a single assembled part during the plastic injection molding process. In these variations preformed components are placed into the mold tool and then captured and joined into a single combined part as new plastic geometry is molded over them.
The price of a multi-cavity mold can vary depending on the size and complexity of the mold. However, in general,multi-cavity molds are more expensive than single-cavity molds.
There are several benefits to choosing an on-demand production option for your plastic mold needs. Perhaps the most obvious benefit is that it allows you to only produce what you need, when you need it. This can help save on costs associated with inventory and storage. Additionally, on-demand production can help reduce lead times and improve flexibility in your supply chain.
The types of components that can to be overmolded to incorporate features in parts include a wide variety of materials and design opportunities. Common examples include clear windows, decorative features (IMD), electronics and magnets.
The steel material the mold is made from also plays a role in its cost. Molds can be made from various metals, plastics, or even composites. Molds are generally more expensive when made of more expensive steel, like S136, which costs three times as much as P20.
There are several reasons why a company might choose to modify a mold. In some cases, the original mold was not designed correctly and needs to be modified to fix the problem. Other times, a company may want to change the design of the part that is being produced.
In order to produce a high quality product, it is important to get rid of unnecessary features and simplify the design injection molding.
There are a few things to keep in mind when designing self-mating parts for injection molding. First, the part must be designed so that it can be easily removed from the mold. Second, the part must be designed so that it can be assembled and disassembled easily. Third, the part must be designed so that it can mate with other parts without any gaps or other problems.
Mold costs can vary greatly, depending on a number of factors. A plastic mold can cost anywhere from $1,000 to $10,000. The exact cost depends on a number of factors, including the size and complexity of the mold, the material it is made from, and the company that makes it.
The cost of injection mold can vary based on a number of factors, but the median cost is around $3,000. The price range can be as low as $1,000 or as high as $10,000, so it’s important to get quotes from multiple companies before making a decision.
When it comes to injection molding, there is no single “right” answer when it comes to finding the best value. However, there are a few tips and tricks that can help you save on injection molding costs. The first tip is to work with an experienced and reputable company. This will ensure that you get the best possible price for your project. The second tip is to be realistic about your project’s design and budget. Injection molding can be a complex and time-consuming process, so it’s important to have a clear understanding of your project’s requirements before getting started. By following these tips, you can be sure that you’re getting the best value for your injection molding project.
There are a few ways to eliminate undercuts, but the best way is to design the part so that it can be molded without them. This can be done by using symmetrical geometry, designing bigger draft angles into the part, or using core pins.
With all of these factors affecting the cost, it can be difficult to determine what is a “reasonable” price for a plastic injection mold. However, there are some general guidelines that can be followed.
Injection molding undercuts can be a difficult and costly problem to fix. They are caused by the mold not being able to release the part from the mold cavity. Undercuts can also lead to the material not flowing properly into the mold cavity.
On-demand production can save businesses money in the long run by reducing inventory costs and eliminating the delivery time. In addition, on-demand production can help businesses respond quickly to changes in customer demand.
Generally insert molding and overmolding are differentiated by the materials being used. Overmolding is typically defined as plastic over plastic, while plastic over metal, or another material, is generally referred to as insert molding. Although the terms can be used in various ways for certain applications.
A core cavity approach to injection molding is a process whereby a mold is created with an inner core that forms the shape of the desired product. The molten plastic is then injected into the mold and allowed to cool, forming the product.
When it comes to the cost of a plastic injection mold, there is no definitive answer. The reason for this is because there are so many variables that can affect the price. Some of these variables include:
This will minimize the potential for defects and improve the overall efficiency of the production process. There are a few key things to keep in mind when simplifying a design for injection molding:1. Remove any features that are not absolutely essential to the function or aesthetics of the final product.
Many medical tools that require sterilization further benefit from this process by creating tight seals around instrument substrates and handle shafts. This helps to prevent areas for bacteria to collect and ensures the sterilization process is effective between procedures.
The mechanical method is achieved by making sure the substrate has undercuts or pass through features to allow the overmold material to fill and hold the component in place. If the part will experience mechanical stresses the retention features should be designed to take this into account to avoid overmold separation.
Tool design for an overmold has several specific requirements the part design should consider. When an operator or robot places an insert or substrate into the overmold tool it needs to be located successfully and held sufficiently while the tool closes, as well as during the injection molding process where high pressures can be working to shift the substrate out of place. This is critical because failure can result in scrap parts or even tool damage that is often lengthy and expensive to repair.
The cost of a plastic injection mold is mainly driven by the part geometry, the material being molded, and the complexity of the mold.
GETTING A QUOTE WITH LK-MOULD IS FREE AND SIMPLE.
FIND MORE OF OUR SERVICES:
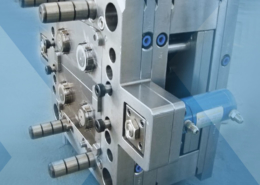
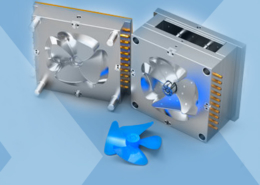
Plastic Molding

Rapid Prototyping
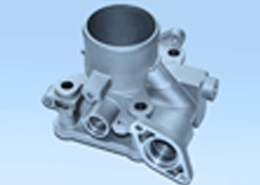
Pressure Die Casting
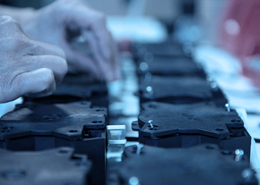
Parts Assembly
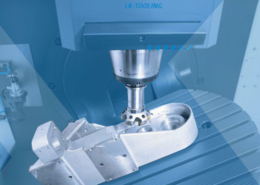