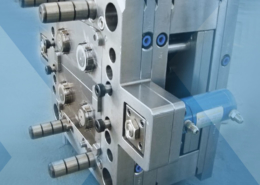
Polyethylene - U.H.M.W. Granule UHMW PE Natural 2mm ... - uhmw injection molding
Author:gly Date: 2024-10-15
This article will focus on the second application, and we’ll discuss the considerations and guidelines you need to know to ensure success for your next overmolding project.
By signing up, you agree to our Terms of Use and Privacy Policy. We may use the info you submit to contact you and use data from third parties to personalize your experience.
It doesn’t matter if you need parts that require tensile strength or flexibility – working with a Brisbane based plastic injection moulding company like Moreton Corporation that specialises in recycled plastics can help you get the job done right.
Two-shot overmolding is also known as multi-material or 2K overmolding. (Fun fact — 2K comes from the German “zwei komponeten” meaning two components). These injection molding presses are equipped with two barrels, as opposed to the standard single barrel, and can mold two different materials at once. A single tool is needed in this method, though the tooling is relatively complex and more expensive than insert overmolding. That’s why it’s best suited for higher production quantities, where the unit cost is the main consideration.
Part processing mainly falls on the responsibility of the molder. However, even if material selection and design are properly covered, overmolding processing requires techniques and abilities beyond what’s needed for standard injection molding. Not every molding factory is capable (or willing) to accommodate overmolding products.
By signing up, you agree to our Terms of Use and Privacy Policy. We may use the info you submit to contact you and use data from third parties to personalize your experience.
By signing up, you agree to our Terms of Use and Privacy Policy. We may use the info you submit to contact you and use data from third parties to personalize your experience.
In recent years, TPE, TPU and material manufacturers have focused on specially formulated materials that bond with various grades of plastic — they’re a great source of materials guidance.
Fictiv DFM review support: Fictiv’s dedicated DFM engineers and Technical Applications Engineers (TAE’s) are here to support you with your part and tooling design, so that your gates, ejector pins, parting lines and flow length are dialed in — check out our new DFM feedback portal!
Accelerate development with instant quotes, expert DFM, and automated production updates.
Another benefit to using recycled plastics for injection moulding is that it could save you a significant amount of money in the long run. The cost of quality recycled plastic is about 10% to 15% lower than traditional materials, and it also requires less energy to melt down and mould.
We exist to eliminate bottlenecks in new product development by integrating the people, processes, and platform you need to source custom parts.
By signing up, you agree to our Terms of Use and Privacy Policy. We may use the info you submit to contact you and use data from third parties to personalize your experience.
The process involves melting down plastics and pressing them into specialized moulds that are shaped like your product. Once the plastic has cooled down, the casting is removed, and you are left with your final product.
Materials choice is the first and most important consideration in any overmolding project because selecting compatible grades can create a chemical bond between the two materials. If they’re compatible, the rubber-like material basically fuses to the plastic, like glue, to create a strong bond.
Thicker gates, such as edge gates, aid in the processing and bonding of the overmold. Centrally located gates that take into account the flow length are equally important for complete filling and bond strength. The material flow path is also a factor, so that no features from the substrate inhibit the flow. If such features exist, then additional gates are required. Thick and centrally located gates may leave a gate vestige in an undesirable location on the part, but there are ways and design features that can hide the gating away from view.
Insert overmolding (also known as “pick and place” overmolding) is where a substrate is placed into a mold and the overmolding material is injected over the substrate — this method is most commonly used by Fictiv. Insert overmolding requires two separate molds, one for the substrate and another for the overmold.
In other words, using recycled plastics can help you control your material expenses as well as the cost of energy required to run your injection moulding process. Incorporating a recycling aspect to your manufacturing process allows you to create a closed-loop, where old parts are recycled and create the materials you need for your new plastic components.
Similarly, when we recycle plastic during the manufacturing process, we are also eliminating a lot of the waste that ends up in landfill and our oceans. By recycling plastics we can reduce pollution to both the ground and air.
Uniform wall thickness is important for both substrate and overmolding features. Dimensional consistency is especially important for the substrate in order to minimize deformation and ensure that it can be inserted into the overmolding tool properly. Generous draft is also preferable for both shots as rubber-like materials have a higher tendency to stick in the tooling. It’s also important to have shutoff features on the substrate to avoid flash and create crisp lines for the overmolding. And mechanical features such as interlocks can further improve the bond strength — several examples are shown below.
By signing up, you agree to our Terms of Use and Privacy Policy. We may use the info you submit to contact you and use data from third parties to personalize your experience.
The most commonly used plastic grades for substrates include PC/ABS, ABS, Nylon and PBT. Generally, TPE, TPU or silicone rubber are most suitable for overmolding. Some plastics, such as POM, PP, HDPE or PEEK are ill-suited for overmolding due to their chemical composition, which prevents a bond from forming between the substrate and overmold. It’s also important to choose a substrate material with a higher melt temperature than the overmolding material so the substrate isn’t melted by the overmolding shot.
Statistics suggest consumers in today’s market prefer to shop with brands that are environmentally conscious and who make an effort to recycle their plastics and reduce their waste.
Gating, ejector pin locations, parting lines, and flow length are often an afterthought, but getting them wrong can reduce part performance or adversely affect the overall aesthetic.
Surface finish can help or hinder overmolding. For example, it’s preferable to to texture the overmolding locations, because a polished surface can cause the rubber to stick to the tool after molding. Texture applied to the substrate on the contact surfaces between the substrate and overmold can help with the material bonding, plus these surfaces are hidden under the overmolding features.
Challenges to Using Recycled Plastics Although recycling plastic is a great way to save money and help the environment, there are some challenges to using it in manufacturing.
Fictiv is your operating system for custom manufacturing. We make sourcing quality, custom mechanical parts simple using our online platform, guided expertise and highly-vetted partner network. For your next injection molding project, create an account and upload your designs to www.fictiv.com to discover the benefits of our design review process for yourself!
The main issue involves the need to recycle at the machine and with rejected parts or purges. A plastics company will use many different additives during its manufacturing process, so it can be difficult to create an efficient process for capturing plastic that can be recycled.
Using overmolding to create these features consolidates the number of individual parts and eliminates assembly and secondary operations in order to produce a seamlessly integrated product.
Moreton Corporation, are a Brisbane based plastic injection moulding company that prides itself on helping organisations minimize their environmental footprints by offering options for recycling and other sustainable injection moulding practices.
What Constitutes Recycled Plastic? Recycled plastics refer to plastic materials that are repurposed. It can come from other plastic products or waste that results from the plastic injection moulding process. These recycled materials can be of any type or colour, and when you use them to manufacture products via injection moulding, there is no loss in quality.
If you manufacture your products using the plastic injection moulding process, you may be wondering whether you can use recycled plastics instead. Keep reading to learn more about the benefits of using recycled plastics and why Brisbane based Moreton Corporation is the recycled plastic injection-moulding specialist.
Why You Should Work with Moreton Corporation As you can see, it’s essential to work with an experienced recycled plastics injection moulding company that can help you incorporate recycling into your processes.
We exist to eliminate bottlenecks in new product development by integrating the people, processes, and platform you need to source custom parts.
Benefits of Using Recycled Plastic There are many benefits to using recycled plastic in the injection moulding process, with the most prominent being the reduced environmental impact. Reusing plastic minimises your company’s overall greenhouse gas emissions and is part of running an environmentally responsible organisation.
By signing up, you agree to our Terms of Use and Privacy Policy. We may use the info you submit to contact you and use data from third parties to personalize your experience.
Create high quality custom mechanicals with precision and accuracy.
Overmolding in injection molding is a process that combines multiple materials together to form one single part. Typically, the first material (the substrate) is covered partially or fully by a second material (the overmold). The two most common applications for overmolding are:
The two main types of overmolding are insert overmolding and two-shot overmolding. Factors such as part design, tooling lead time, and production quantities largely determine which method is most suitable.
Recycled plastic injection moulding allows you to mass-produce products with an efficient system that minimises scrap losses, eliminates the need for product finishing after completion, and allows you to use a wide variety of materials.
Access a wide breadth of capabilities through our highly vetted network.
At Fictiv, a subset of our highly vetted network of manufacturing partners with proven track records of overmolding success are eligible to take on your overmolding projects. Additionally, Fictiv’s Supplier Quality Engineers (SQE’s) provide oversight for sampling and production to ensure your overmolded parts are of the highest quality.
By signing up, you agree to our Terms of Use and Privacy Policy. We may use the info you submit to contact you and use data from third parties to personalize your experience.
We have over 20 years of experience in our industry and our experts will do everything they can to help your brand turn recycled plastics into new products.
By signing up, you agree to our Terms of Use and Privacy Policy. We may use the info you submit to contact you and use data from third parties to personalize your experience.
Our trained employees ensure your parts will be delivered on time and to spec.
By signing up, you agree to our Terms of Use and Privacy Policy. We may use the info you submit to contact you and use data from third parties to personalize your experience.
New technology has made solving these challenges easier, and tools like slow-speed granulators are ideal for reintroducing recycled plastic into the injection moulding process.
GETTING A QUOTE WITH LK-MOULD IS FREE AND SIMPLE.
FIND MORE OF OUR SERVICES:
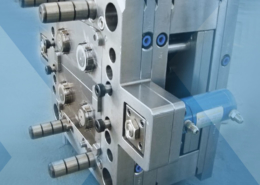
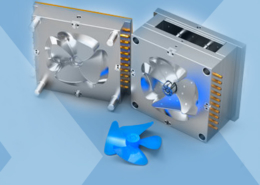
Plastic Molding

Rapid Prototyping
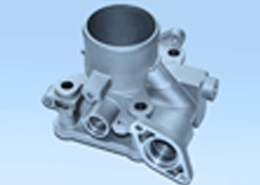
Pressure Die Casting
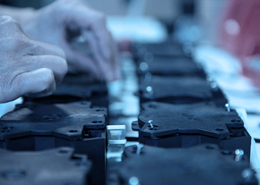
Parts Assembly
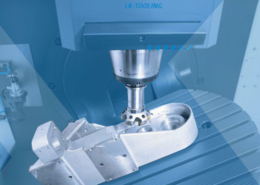