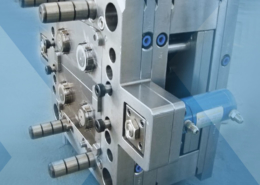
Polyester (PET) at Aline Components - polyethylene terephthalate injection moldi
Author:gly Date: 2024-10-15
Plastic molding in air conditioning units serves multiple purposes. It contributes to the functional efficiency of the unit by creating components that aid in the circulation of air, cooling, and heating. Additionally, plastic materials offer a lightweight yet sturdy alternative to traditional materials like metal, which makes air conditioners more portable and easier to install. Moreover, plastic parts are less prone to corrosion and are more resistant to the elements.
PVC is a relatively stiff flow material and has a narrow processing range. The molecular weight determines the flow characteristics. Higher molecular weight materials are more difficult to process (this could be modified by addition of lubricants). Typically, however, relatively low molecular weight grades are used in molding).
Water distribution piping, home plumbing, house siding, business machine housings, electronics packaging, medical apparatus, packaging for foodstuffs, etc.
It is very important to process the material at the correct melt temperature; otherwise severe problems from decomposition (which produces hydrochloric acid which in turn accelerates decomposition) could result.
We continues to enhance our visibility and reputation, including exhibitions all over the world and we also actively taking corporate social responsibility.
Sprues should be as short as possible; typical runner sizes are 6 - 10 mm and should have a full round cross-section. Insulated hot runners and certain types of hot sprue bushings may be used with PVC.
In the modern era of technology, plastic molding has become an integral part of the air conditioning industry. The use of plastic in air conditioning units is not just for aesthetics but also for its durability and efficiency. This article will delve into the various aspects of plastic molding for air conditioners, discussing its importance, the four key dimensions that define its use, and concluding with a summary of the key points.
In conclusion, plastic molding plays a crucial role in the production of air conditioners. It allows for precise control over the size and shape of components, ensuring that they function efficiently and effectively. While there are environmental considerations that need to be taken into account, with proper recycling and disposal practices, plastic molding can continue to contribute to the efficiency and durability of air conditioning units.
Viewmold company provides injection molding services for your part with PVC plastic material. PVC injection molding processing condition Generic Class PVC (Polyvinyl Chloride) Typical Applications Water distribution piping, home plumbing, house siding, business machine housings, electronics packaging, medical apparatus, packaging for foodstuffs, etc. Injection Molding Processing Conditions Drying Not usually necessary as PVC absorbs very little water. Melt Temperature 160 - 220 C (320 - 428 F) Mold Temperature 20 - 70 C (68 - 158 F) Material Injection Pressure Up to 150 MPa Packing Pressure Up to 100 MPa Injection Speed Relatively slow, to avoid material degradation Runners and Gates All conventional gate types may be used; pin-point and submarine gates are used for molding small components and fan gates are typically used for thick sections. The minimum diameter of pin-point or submarine gates should be 1 mm and the thickness of fan gates should not be less than 1 mm. Sprues should be as short as possible; typical runner sizes are 6 - 10 mm and should have a full round cross-section. Insulated hot runners and certain types of hot sprue bushings may be used with PVC. If you need high quality cutom aluminium casting parts Pls contact us sales@viewmold.com If you need high quality injection mold tooling, Contact us. Chemical and Physical Properties Rigid (unplasticised) PVC is one of the most widely used plastic materials. It is produced from sodium chloride and natural gas. The repeat chemical structure is vinyl chloride. Additives are mixed with PVC to make it processible. PVC grades produced by suspension or mass polymerization techniques are the major types used for melt processing. PVC is substantially an amorphous material. Some of the additives used include stabilizers, lubricants, processing aids, pigments, impact modifiers, and fillers. Some features of PVC include low combustibility, toughness (designed to be virtually unbreakable), good weatherability (including good color and impact retention, and no loss in stiffness), and excellent dimensional stability. PVC is highly resistant to oxidizing and reducing agents, and strong acids. However, unplasticised PVC is not recommended for environmental and continuous use above 60 C (140 F). It is not resistant to concentrated oxidizing acids such as sulfuric or nitric acid and is unsuitable for use with aromatic and chlorinated hydrocarbons. It is very important to process the material at the correct melt temperature; otherwise severe problems from decomposition (which produces hydrochloric acid which in turn accelerates decomposition) could result. PVC is a relatively stiff flow material and has a narrow processing range. The molecular weight determines the flow characteristics. Higher molecular weight materials are more difficult to process (this could be modified by addition of lubricants). Typically, however, relatively low molecular weight grades are used in molding). Shrinkage is fairly low (0.002 - 0.006 mm/mm or 0.2 - 0.6%). If you need to look for more plastic resin injection molding processing condition, could you please click it. If you need high quality plastic extrusion services, Pls contact us sales@viewmold.com If you need high quality sheet metal parts, Pls contact us sales@viewmold.com The following is other plastic processing condition: ABS injection molding processing condition, HDPE injection molding processing condition, LDPE injection molding processing condition, PA12 injection molding processing condition, PA6 injection molding processing condition, PBT injection molding processing condition, PC-ABS injection molding processing condition, PC-PBT injection molding processing condition, PEI injection molding processing condition, PETG injection molding processing condition, PMMA injection molding processing condition, POM injection molding processing condition, PPE injection molding processing condition, HDPE injection molding processing condition, PP injection molding processing condition, PS injection molding processing condition, PVC injection molding processing condition, SAN injection molding processing condition,
Some of the additives used include stabilizers, lubricants, processing aids, pigments, impact modifiers, and fillers. Some features of PVC include low combustibility, toughness (designed to be virtually unbreakable), good weatherability (including good color and impact retention, and no loss in stiffness), and excellent dimensional stability. PVC is highly resistant to oxidizing and reducing agents, and strong acids. However, unplasticised PVC is not recommended for environmental and continuous use above 60 C (140 F). It is not resistant to concentrated oxidizing acids such as sulfuric or nitric acid and is unsuitable for use with aromatic and chlorinated hydrocarbons.
All conventional gate types may be used; pin-point and submarine gates are used for molding small components and fan gates are typically used for thick sections. The minimum diameter of pin-point or submarine gates should be 1 mm and the thickness of fan gates should not be less than 1 mm.
There are various types of plastic molding used in air conditioners. Injection molding is one such technique where plastic is injected into a mold to create the desired shape. This process allows for precise control over the size and shape of the components. Additionally, there is rotational molding, a process where plastic is applied to a rotating core to create hollow objects with consistent thickness. These techniques enable the production of parts that are both durable and efficient.
Plastic molding offers numerous benefits for air conditioners. Firstly, it allows for precise control over the size and shape of the components, ensuring that they fit into the unit perfectly. Secondly, plastic parts are lightweight yet sturdy, making it easier to transport and install the air conditioner. Furthermore, plastic is a good conductor of heat, ensuring that the unit can efficiently transfer heat and cool the air effectively. Additionally, plastic parts are less prone to corrosion and can withstand exposure to various elements.
While plastic molding offers numerous benefits for air conditioners, it is important to consider the environmental impact of the materials used. Proper recycling and disposal practices must be followed to ensure that plastic waste does not harm the environment. Additionally, research is ongoing to develop more environmentally friendly plastics that can be used in air conditioning units without causing harm to the environment.
Rigid (unplasticised) PVC is one of the most widely used plastic materials. It is produced from sodium chloride and natural gas. The repeat chemical structure is vinyl chloride. Additives are mixed with PVC to make it processible. PVC grades produced by suspension or mass polymerization techniques are the major types used for melt processing. PVC is substantially an amorphous material.
GETTING A QUOTE WITH LK-MOULD IS FREE AND SIMPLE.
FIND MORE OF OUR SERVICES:
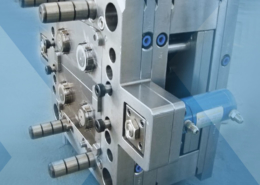
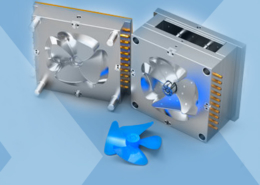
Plastic Molding

Rapid Prototyping
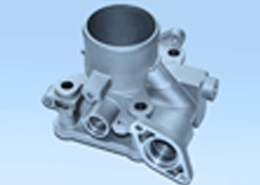
Pressure Die Casting
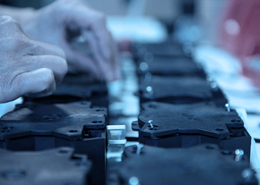
Parts Assembly
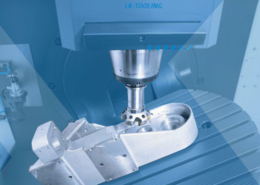