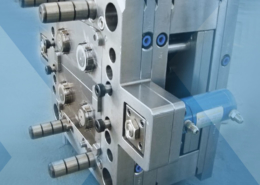
Unveiling the Dynamics of the Plastic Molding Business
Author:gly Date: 2024-06-08
The plastic molding business stands as a cornerstone of modern manufacturing, shaping the production landscape across diverse industries. From automotive components to consumer electronics, the versatility and efficiency of plastic molding processes have revolutionized the way products are designed, prototyped, and mass-produced. In this article, we embark on a comprehensive exploration of the plastic molding business, delving into its intricacies, applications, challenges, and future prospects.
Understanding the Essence of Plastic Molding Business
Plastic molding encompasses a range of manufacturing processes that involve shaping molten plastic material into desired forms using molds or dies. This business sector encompasses techniques such as injection molding, blow molding, rotational molding, and extrusion molding, each offering unique advantages and applications. The plastic molding industry caters to a broad spectrum of markets, from aerospace and medical devices to packaging and consumer goods, driving innovation and economic growth worldwide.
Historical Evolution
The roots of plastic molding can be traced back to the mid-20th century, coinciding with the rapid development of synthetic polymers and industrial manufacturing processes. Since then, advancements in materials science, machinery, and automation have propelled plastic molding into a dominant force in the global manufacturing landscape, enabling the mass production of complex and lightweight components with high precision and efficiency.
Process Overview
Plastic molding processes typically involve several key stages, including material preparation, mold setup, heating and melting of the plastic resin, injection or shaping of the molten material into the mold cavity, cooling and solidification, and ejection of the formed part. Each step demands careful attention to parameters such as temperature, pressure, and cooling rate to ensure optimal part quality and production efficiency.
Exploring Diverse Applications
Automotive Industry
In the automotive sector, plastic molding plays a crucial role in producing interior and exterior components, such as dashboards, bumpers, door panels, and engine parts. The lightweight, durable, and design-flexible nature of plastic components contributes to fuel efficiency, vehicle aesthetics, and overall performance.
Consumer Electronics
The consumer electronics industry relies heavily on plastic molding for the production of housings, enclosures, and components for smartphones, laptops, televisions, and other electronic devices. The ability to achieve intricate designs, tight tolerances, and various surface finishes enables manufacturers to meet consumer demands for slim and aesthetically pleasing products.
Medical Devices
In the medical field, plastic molding is instrumental in manufacturing sterile and biocompatible components, including syringes, vials, implants, and diagnostic equipment. The stringent regulatory requirements for safety, reliability, and cleanliness necessitate precision molding techniques and materials with specific properties, ensuring the integrity of medical devices and equipment.
Embracing Technological Innovations
Industry 4.0 Integration
The integration of Industry 4.0 technologies, such as IoT sensors, AI-driven analytics, and robotics, is revolutionizing plastic molding operations. Real-time monitoring of production processes, predictive maintenance, and data-driven optimization enhance efficiency, quality control, and resource utilization, driving the industry towards smart and sustainable manufacturing practices.
Advanced Materials
Ongoing research in polymer science leads to the development of advanced materials tailored for specific applications in plastic molding. Bio-based polymers, recyclable resins, and high-performance compounds offer improved sustainability, durability, and performance characteristics, addressing environmental concerns and market demands for greener solutions.
Additive Manufacturing Synergy
The synergy between plastic molding and additive manufacturing technologies, such as 3D printing, opens up new possibilities for rapid prototyping, tooling fabrication, and customization. Hybrid approaches combine the strengths of both processes, enabling faster product development cycles, on-demand manufacturing, and cost-effective production of low-volume parts.
Addressing Challenges and Future Directions
Sustainability Imperatives
Despite its advantages, plastic molding faces scrutiny regarding its environmental impact, particularly concerning plastic waste and energy consumption. Embracing sustainable practices, such as material recycling, circular design principles, and energy-efficient processes, is essential for mitigating these challenges and fostering a more environmentally responsible industry.
Supply Chain Resilience
Global supply chain disruptions, exacerbated by events like the COVID-19 pandemic, highlight the need for resilience and agility in plastic molding operations. Strategies such as regionalization, digital supply networks, and inventory optimization enhance supply chain flexibility, risk management, and business continuity in the face of unforeseen disruptions.
Design Innovation and Customization
Consumer preferences for personalized products and rapid product iterations drive the demand for flexible manufacturing solutions in plastic molding. Embracing digital design tools, collaborative design platforms, and agile manufacturing processes enables manufacturers to respond quickly to changing market demands, offering customized solutions and enhancing customer satisfaction.
Conclusion: Shaping the Future of Manufacturing
In conclusion, the plastic molding business continues to be a driving force in the global manufacturing landscape, enabling innovation, efficiency, and sustainability across industries. By embracing technological advancements, addressing challenges, and fostering collaboration across stakeholders, the plastic molding industry can unlock new opportunities for growth, resilience, and environmental stewardship. As we look towards the future, a commitment to innovation, sustainability, and continuous improvement will be essential for shaping a brighter and more resilient future for the plastic molding business.
GETTING A QUOTE WITH LK-MOULD IS FREE AND SIMPLE.
FIND MORE OF OUR SERVICES:
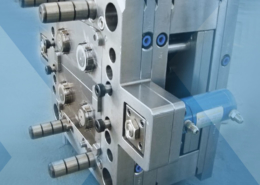
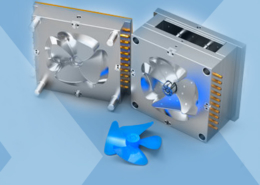
Plastic Molding

Rapid Prototyping
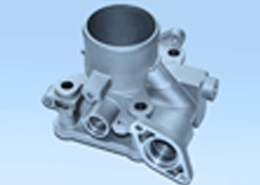
Pressure Die Casting
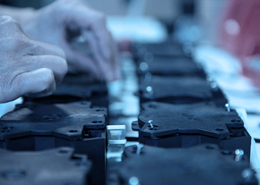
Parts Assembly
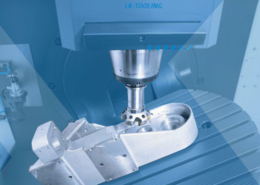