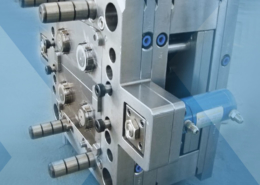
PMMA acrylic injection Molding Defect Causes and Solutions - pmma injection mold
Author:gly Date: 2024-10-15
Nylon is one of the most versatile materials used in plastic injection molding. It’s commonly combined with a range of other materials to enhance its characteristics. Thanks to its high melting temperature and low friction properties, it’s useful for a wide range of products such as nylon rope, reinforced automotive parts, and even clothing.
down the final fill speed. In severe burn mark cases, it may be necessary to modify the venting in the mold. But the molder should always try the simpler solution of reducing final fill rate before taking the time (and expense) of modifying the tool.
Paulson presents at NPE2024's General Education Session and hosts Daily in-booth Molding Simulation demos Join us for...
From the plastic’s point of view there are only 4 basic variables in the injection molding process – plastic pressure in the cavity, melt temperature, plastic flow rate and plastic cooling rate in the mold. These 4 basic variables are what determine the properties of the finished injection molded part.
When plastic flows, the molecules orient, meaning they line up in the direction of flow. This is called molecular orientation . The faster they flow, the more they line up (orient). If the polymer molecules remain oriented, the molded part will be stronger in the direction of plastic flow but weaker in the transverse direction. If the parts crack, the cracks will form between the oriented molecules. The flow rate also affects the surface of the plastic part. A molded part defect called crazing shows up as tiny cracks. Crazing can show up days, weeks or even months after the part is molded. Crazing is caused by highly oriented plastic molecules trapped near the surface of the part.
A family-owned company created in 1971, Paulson Training is a global provider of workforce development solutions for the plastics industry.
Injection molding is considered to be one of the fastest and most optimized methods of producing large numbers of identical plastic components at one time. Injection molding is used for nearly every consumer plastic product and is the most common plastic manufacturing method around. Because of the wide range of applications and industries where plastics are used, different chemical formulations are required for the plastic injection molding process.
Much like Acetal, polypropylene is a plastic with a naturally glossy surface when properly manufactured. Its chemical resistance and elastic properties make it useful for a wide variety of food-related applications, including plastic kitchenware, dishwasher-safe plates, and storage containers. Polypropylene is also commonly used to make toys, hard luggage containers, and even external car parts.
The problem of jetting (which is also sometimes called “worm tracks”) appears as a line in the plastic part when the injected plastic fails to form a flow front. The plastic reaches the gate then shoots straight through the cavity rather than flowing smoothly with a well formed flow front. The solution to a jetting problem is to reduce the fill rate just as the plastic reaches the gate. Once a small flow front has formed the molder can increase the fill rate.
As a general rule, the molder should fill the mold quickly to save cycle time. It’s a good rule up to the point where the fill rate is so fast that it starts to cause problems.
Polycarbonate is a useful plastic material for applications needing transparency or high impact resistance. For this reason, polycarbonate is most commonly used in eyewear applications, but it’s also used in pipes for LED lights, clear windows, and sporting equipment.
Also known as Plexiglas, acrylic is a hard transparent plastic material often used in electronics and automotive parts. Other forms of acrylic are also used in everyday products due to its natural transparency and coloring properties, everything from eyewear lenses, acrylic paint, and even acrylic nails. Acrylic can also be colorized to be either translucent or opaque.
When in need of rigid, heat-resistant plastic, HDPE is the best material to use. Since polyethylene is a food-grade plastic – meaning it is safe to use around food – this material is commonly manufactured in storage containers, kitchenware, and refrigerator shelving. HDPE is also a good plastic for holding chemical-based products such as cleaning agents, laundry detergent, bleach, and shampoo.
Polystyrene is a polymer used in a wide variety of plastic and foam applications across a range of industries. Due to its bending and flexing properties, polystyrene is often used in hinged applications, such as disposable food containers and bottles. It’s also widely used to make rigid foam insulation and sheeting for laminate floors.
When any of the defects discussed here occur, the molder who understands the scientific molding principles behind the injection molding process will analyze the problems on the basis of the 4 variables and then decide which machine controls need to be adjusted to solve the problems.
All modern injection molding machines have fill rate controls on the control panel. The molder can use these fill rate controls to vary the plastic flow rate. Because flow rate is one of the 4 basic variables in molding it has a major effect on the directional properties and surface finish properties of the molded parts. By controlling the fill rate, the molder can solve molded part defects like jetting and burn marks. Fill rate can also be used to reduce the severity of weldlines.
In commercial applications, acrylic falls under #7 (OTHER). This can include other types of plastics including polycarbonate, polylactic fibers, nylon, and fiberglass.
Polyetherimide, also known as Ultem, is an amorphous material with extremely high heat resistance compared to other plastics. Due to its rigidity and high heat performance, polyetherimide is most commonly used in medical devices, electronics, and industrial plastic parts.
Burn marks are created when air inside the mold cavities cannot escape fast enough. The air gets compressed so much that auto-ignition occurs. To fix burn marks using flow rate, the molder should slow
ABS plastic is one of the most commonly used plastics in injection molding due to its wide temperature range, good stability, and insulating properties. ABS is commonly found in plastic toys such as Lego bricks, but it’s also often used in many types of electronics, tools, and home repair equipment.
Our expert plastic part designers will work on your new or existing design concept to find the best material for your particular application. Whether you need electronic enclosures molded from ABS or pull-out drawer handles made from acetal (POM), our experts will address your needs and help you build the best part possible out of the best materials available.
Also known as Acetal, polyoxymethylene is a semi-crystalline polymer which is very rigid and has a naturally glossy surface, making it a useful material for a wide range of industries. Acetal is most commonly found in automotive applications, household appliances, and electronics.
In commercial applications, polycarbonate falls under #7 (OTHER). This can include other types of plastics including acrylic, polylactic fibers, nylon, and fiberglass.
The professionals at Retlaw Industries use a wide variety of plastics when manufacturing our molded products, depending on what type of plastic product our customers need.
GETTING A QUOTE WITH LK-MOULD IS FREE AND SIMPLE.
FIND MORE OF OUR SERVICES:
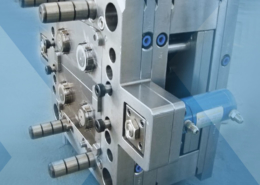
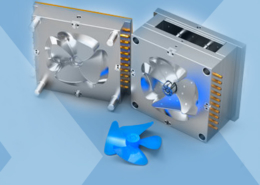
Plastic Molding

Rapid Prototyping
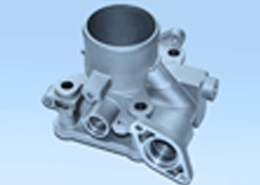
Pressure Die Casting
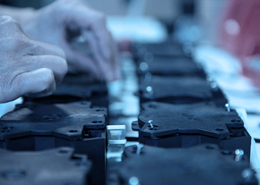
Parts Assembly
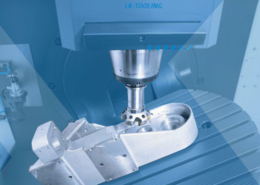