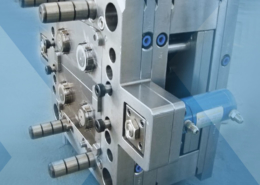
Plastics - flexible plastic molding
Author:gly Date: 2024-10-15
Our helpful design aid demonstrates part features that are too thin or too thick, bad bosses, right and wrong ribs, and other considerations to be mindful of while designing parts for injection molding.
It's most often used for the manufacturing plastic parts at scale due to its low material waste and low cost per part. It’s an ideal manufacturing process for industries like medical devices, consumer products, and automotive.
Tolerances: Typically, Protolabs can maintain a machining tolerance of +/- 0.003 in. (0.08mm) with an included resin tolerance that can be greater than but no less than +/- 0.002 in./in. (0.002mm/mm).
We can support you through the entire process of bringing your product to market or upgrading and modifying existing products. All manufacturing, assembly, testing and validation is carried out at one of our UK sites in Oxford or South Wales.
Our basic guidelines for plastic injection molding include important design considerations to help improve part moldability, enhance cosmetic appearance, and reduce overall production time. View our design guidelines page for more details.
Critical-to-quality (CTQ) dimensions you call out on models let us know what areas are most crucial to the success of your parts. Once the parts start molding, the process and samples are qualified using automated inline CMM technology, generating a detailed FAI and process capability study with no additional lead time.
OGM Medical is a UK based plastic injection moulding company supplying medical equipment manufacturers globally. We manufacture components and devices for a wide range of customers in the medical, pharmaceutical and life science sectors.
We will prepare a bespoke master validation plan and validation protocol for you including a full production part approval process (PPAP).
We have wide selection of more than 100 thermoplastic and thermoset materials. And if you're looking for alternative material options, check out our guide to resin substitutes for ABS, PC, PP, and other commonly molded plastics.
Want to learn more about injection molding? Sign up to receive a Design Cube. This physical aid demonstrates how to properly design features commonly found on molded parts.
With ISO 13485 medical standard manufacturing and our new ISO 7 clean room (Class 10,000 clean room) for medical devices, we can help you design and develop high quality injection moulded products as cost effectively as possible. We can also reduce injection mould tool modification or repair times from weeks to just days and shorten the overall product development lead time.
Our digital factories create prototypes and low-volume parts fast, while our manufacturing network, offers advanced capabilities and volume pricing.
We guarantee complete quality control with full product inspection, testing and validation services accredited to medical standard ISO 13485, manufacturing standard ISO 9001 and environmental standard ISO 14001.
Our thermoplastic injection molding is a standard process involving an aluminum mold with no heating or cooling lines running through it, which means cycle times are a bit longer. As part of the scientific molding process, our molders independently optimize and monitor fill speed, hold pressure, and hold time, and periodically inspect part quality and cosmetics. During the molding process, we use an automated inline CMM to ensure dimensional accuracy, as well as generate a detailed process capability study and FAI report.
Our tool designers can help you with everything you need to produce a successful injection mould design including the best choice of medical grade materials.
Tough Black (Loctite Henkel 3843) and Ceramic-Filled (BASF 3280) are two new advanced photopolymer materials now available for 3D printing.
While the molds themselves are similar, part quantities, lifetime maintenance, quality documentation, and pricing vary depending on which service option is chosen. The right one depends on your project needs.
No one ever said that designing and manufacturing molded parts was easy. Our goal is to get you through it quickly and with quality parts. A good starting point is our Design for Moldability Toolkit.
OGM first started supplying medical device companies in the UK over 20 years ago. Our first cleanroom was built in 2000 and today we are one of the leading plastic injection moulders for medical devices and components.
To learn more about our plastic injection moulding services please call us on +44 (0)1865 844300 or you can email us at info@ogmmedical.com
We specialise in high-volume production of plastic parts using precision-controlled robotics. We invest heavily in the latest technology from 3D metal additive manufacturing to high-definition vision systems for inspection and quality control.
Get machined parts anodized and chromate plated with our quick-turn finishing option. Eligible materials include aluminum 6061/6082 and 7075.
Our team is committed to delivering the best plastic injection moulding service with dedicated project management from concept to finished product.
Resin pellets are loaded into a barrel where they will eventually be melted, compressed, and injected into the mold’s runner system. Hot resin is shot into the mold cavity through the gates and the part is molded. Ejector pins facilitate removal of the part from the mold where it falls into a loading bin. When the run is complete, parts (or the initial sample run) are boxed and shipped shortly thereafter.
Depending on your application's requirements, you can choose from the following when requesting an injection molding quote.
Proto Labs, Inc. 5540 Pioneer Creek Dr. Maple Plain, MN 55359 United States P: 877-479-3680 F: 763-479-2679 E: [email protected]
Our experienced team will work closely with the design team to transform your mould tool design into the highest quality injection mould tooling.
Injection molding is a manufacturing process that consists of filling a metal mold cavity with liquid plastic resin, which then cools and forms a plastic part.
This complete reference guide walks you through everything from quoting, design analysis, and shipment to best practices that ensure your model is optimized for molding.
Our plastic injection molding process produces custom prototypes and end-use production parts with lead times as fast as 1 day. We use aluminum molds that offer cost-efficient tooling and accelerated manufacturing cycles, and stock about 200 different thermoplastic resins.
As a UK based manufacturer, we can offer help with reshoring to reduce lead-times and production delays of medical devices and components.
The manufacturing process for molded parts is complex. Before your parts are even molded, we're there to help you with comprehensive manufacturability feedback and consultative design services, so you can avoid mold design pitfalls before the resin hits the mold. From there, our production process is documented and optimized using scientific molding so you get high-quality parts consistently and reliably with every production run.
It has been very enlightening to us here at HP that we are able to get parts so rapidly out of the actual materials that we're going to use in the final production.
GETTING A QUOTE WITH LK-MOULD IS FREE AND SIMPLE.
FIND MORE OF OUR SERVICES:
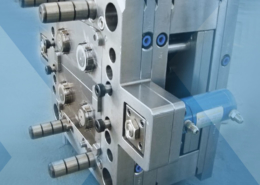
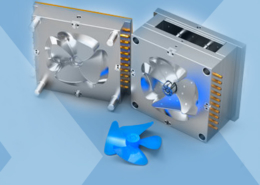
Plastic Molding

Rapid Prototyping
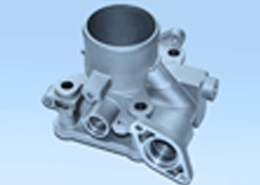
Pressure Die Casting
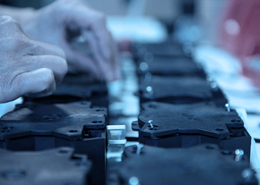
Parts Assembly
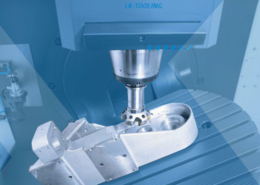