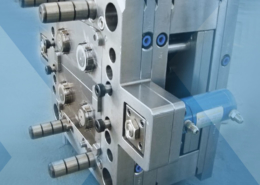
Plastic Prototype You Should Know in 2022 - plastic prototype manufacturing
Author:gly Date: 2024-10-15
Medical-grade plastic materials are simply plastics designed to create medical products. It is also suitable for manufacturing Vitro diagnostics and primary packaging products. These products help preserve and contain medicines to avoid contamination in pharmaceuticals.
The medical injection molding process uses a vast range of material options to manufacture medical and pharmaceutical parts. There are various plastic injection molding materials used that give the process high efficiency. Some of them are:
If you want to produce high-quality machined parts with a sleek appearance, it’s essential to consider some critical factors related to CNC machining.
Medical injection molding is a cheaper and more efficient method of making medical and pharmaceutical parts, including medical devices, laboratory tools, equipment, and testing instruments. Medical parts made from this method reach a high level of precision, quality, and accuracy.
Generally, atomization technology creates a powder mix from the desired metals. This powder is made into a pellet (feedstock), which includes a binding agent that makes it easier to mold.
Absolutely! We have decades of experience with complex molding projects. We are well equipped to handle even the most intricate molds. We've successfully tackled diverse projects, providing precision and efficiency for both simple and highly complex parts.
Many prototype molders only apply sand or bead blast textures. While we do offer this services, acid etching is more accurate and will last for many, many more cycles.
Additionally, soft materials, like aluminum or mild tool steels, will not retain this "shiny" appearance after repetitive injection molding cycles. To truly provide an SPI A series finish, the mold requires special steel, like very specific grades of hardened 420SS with a very tight grain structure. Be sure to specify this finish requirement in your RFQ (Request For Quote) or discuss this with your CSE (Customer Service Engineer) before beginning your project.
• Low volume production • Parts in 2-4 weeks • Capable of 10k+ cycles • Undercuts & unscrewing details • Square corners • 55 to 1200 tons
After injection comes the removal of the binding agent through various means, including solvent, a catalytic process, thermal furnaces, or even a combination of these methods. This leaves behind injection parts with a 100% density at the end.
If you need assistance making your payment ask your CSE (Customer Service Engineer) to connect you with our orders department.
The ability to withstand adverse conditions is a crucial consideration for plastic molding materials. They must be reliable and durable when subjected to heat, corrosives, liquid, vibrations, and other human body movements. Most of the plastics used in this process come out tops in this requirement.
There are 100s of available thermoplastic materials. These are just a few of the resins we stock. Many are also available with additives, like glass or carbon fibers, and fillers like talc.
Think of the best laboratory facility and medical devices, made with top quality finish, and it’s undoubtedly through the medical plastic molding process. One good thing about the procedure is that it is both cost-efficient and delivers with exceptional accuracy and consistency. Besides, it comes in handy when the volume of productions is high and requires a masterpiece level of construction.
We take care to restrict access to your data/information to a need to know basis. Each customer that registers on our website is afforded these standard confidentiality terms. For more information, contact your CSE (Customer Service Engineer).
Bridge molding utilizes a bridge tool to accomplish low to moderate volumes of molded parts quickly and cost efficiently. There are small sacrifices in tool longevity with a bridge mold versus a production mold, but often times a bridge tool has more life than many projects need (300k+ cycles). Whereas rapid production molding spares no expense when it comes to tooling and is therefore the king of low cost, high-volume production injection molding.
Yes, we have provided plastic product design services for over 30 years and have engineers on staff that are very knowledgeable about injection molded part design.
Yes, but selecting the plastic material for each application is the customer's choice and responsibility. We have engineers with decades of experience who can digest your requirements and make suggestions, as well as, provide technical data on various material, but in the end you will need to make this choice.
Prototype molds are constructed for use in our proprietary system and for that reason the customer does not own these mold inserts and only pays a "tooling setup fee".
There should be no breakable plastics in manufacturing devices to avoid or minimize biohazards in the medical field. Hence, each selected material should have a satisfactory durability index before being put to use. More so, they should be able to exhibit a high level of tensile strength.
The way the medical plastic injection process is set up helps cut unnecessary injection molding costs — massive production deliveries and high-volume manufacturing help to maximize the process. Hence, whenever there is an extraordinary volume of medical injection parts being produced, the injection molding process can reduce the cost per part.
The innovative medical injection molding process is a ground-breaking invention that has swept through the industry. The manufacturing of medical injection parts not only satisfies laid down industry standards but makes the usage process smooth. This article explained some of the rudiments of the process and other important details.
Yes, 2D drawings in PDF format are acceptable for inspection and communication purposes, but cannot be used as a substitute for the 3D CAD formats listed above.
The strict requirements of this process require a hygienic environment for production. This environment ensures that no ambient air, dust, or moisture settles on the mold or mixture while it sets. The rubber-like substance produced through this process is highly chemical resistant.
Yes, all production molds, and most prototype molds, are eligible for acid-etched textures using dozens of industry standard patterns.
Additionally, steel molds are much more durable, can survive fully automatic molding and are much easier to modify. If cost is driving you to consider aluminum molds, submit an RFQ and see what we can do for you.
In our process, there is no tangible difference in the parts. Some prototype molders may take shortcuts, like rounding off corners or eliminating water lines in the mold in an effort to reduce costs. We do not make these compromises.
We provide injection molding services up to 1,200 tons in the US and up to 2,800 tons in Asia. The maximum part size will depend on the material selected and the part geometry, but as a general rule, injection molded parts may require 2-5 tons per square inch of projected surface area. For example, a 10"x10" part might require 200 to 500 tons of clamp force, depending on part geometry, nominal thickness, material selection and other factors.
It is important to note that aluminum can become "shiny" and appear to have a mirror finish, but that does not qualify as an SPI A series finish. For this reason your average prototype mold may not actually meet your project requirements.
The extremely high level of precision needed within the aerospace industry makes CNC machining a suitable manufacturing process for the sector.
Plastics have a wide range of use in the medical field. They are almost indispensable in creating plastic injection molding medical parts and tools like Syringes, surgical gloves, IV tubes, catheters, etc. These products are for one-time use only, erasing the need for sterilization and reducing the spread of highly contagious or virulent diseases.
The process of medical injection molding edges out similar production procedures in the industry. With its smooth and seamless operation, there are numerous advantages the process offers, and they include but are not limited to:
In the process of plastic injection for the medical device industry, exceptional accuracy is a must. Due to the tight tolerance margin, every inch, millimeter, or centimeter count can influence the whole molding development. Besides, it is essential to use skilled injection molding facilities to achieve this high-level accuracy.
Nothing, the term "tool" is a broad term that could refer to many different types of tools or dies, but in our process it is interchangeable with the term "mold".
Devices produced with this injection molding type include wearable devices, surgical tools, and catheter ablation tools.
• High volume production • Parts in 4-8 weeks • Capable of millions of cycles • Unlimited part complexity • Optimized automatic production • Highly competitive pricing
Silicone doesn’t react with biological tissue, making it even more suitable to implant it safely. However, this injection molding process requires many steps. This is also dependent on the properties expected of the resultant silicone product.
Yes, even when the design change is not a "steel safe" change. We build all of our molds from steel, as a result we can easily cut away more steel or "add" steel back in using modern welding techniques. This is a much more difficult task with aluminum and one of the many reasons we do not typically use aluminum to manufacture our molds.
The process of plastic injection molding for medical devices is critical, with a high probability of failure. Thus, there are some factors one needs to consider before and during the design, planning, and operational procedure. They include:
Get prototype injection molded parts fast! With Rapid Molding you won’t break the bank doing it. Components ranging from 0.5″ x 0.5″ up to 20″ x 20″ have never been less expensive. Get a prototype injection molding quote right now, simply upload your 3D CAD file and answer a few questions.
If you’re looking for an injection parts medical manufacturer, you can visit RapidDirect’s Injection Molding Services for more in-depth information. RapidDirect, an ISO 9001 certified industry, is a renowned name in the injection parts industry, offering you a rich experience in making injection molded parts, including medical injection parts. Also, we provide custom injection molding services at a competitive price and detailed reports of inspection and material tests. You can stand to get an instant quote and free automated DfM feedback after you upload a CAD file.
No, due to the limitations in accuracy associated with this file format it is not a viable option for building injection molds.
Yes, we warehouse and maintain all molds in our possession for the life of the project. If the project becomes dormant for more than 12 months we will contact you to understand your intentions and future needs. We may charge a storage fee for molds held beyond reasonable dormant periods.
Rapid Molding prides itself on swift turnarounds. Typically prototype injection molding lead-times are are 2-4 weeks. Whereas bridge tooling and production tooling lead-times can run 3 to 8 weeks depending on the size and complexity of the parts. In general, we typically deliver production molds 50% to 70% faster than industry standards, ensuring your projects hit the market without unnecessary delays.
Yes, we have several good suppliers that we partner with for retail packaging. For more information, contact your CSE (Customer Service Engineer).
We manufacture molds with all levels of complexity, everyday. Features like undercuts and internal or external threads are no problem. We can even incorporate these features into prototype molds. Molds that require multi-stage ejection, floating cores and cavities, reverse injection and ejection are all available to build your molds.
The materials used in production are greatly dependent on the object being made. These molds (prototypes) go through extensive rounds of testing to ensure their usability.
• Moderate volume production • Parts in 3-6 weeks • Capable of 300k+ cycles • Family and multi-cavity molds • Automatic undercut details • Automatic unscrewing molds • Fully automatic production
As a result, the resin ends up looking misshapen, ugly, and weaker structurally than it should due to the sink marks. Gas-assisted injection molding is the solution to this problem of making plastic injection molding medical parts.
Some medical devices like tubes and respiratory masks are quite difficult to keep hygienic. So, liquid silicone injection molding is generally the most suitable in producing equipment like these.
If you need assistance with 3D CAD creation or modifying your part design for better results with injection molding, inquire with your CSE (Customer Service Engineer).
Equipment made in this manner has a high requirement for its material. While the walls are thin, the device or tool maintains its integrity and durability to an extent. As a result of these requirements, its base materials tend to be plastic (especially LCP or Polypropylene, or even nylon).
The process involves running gas through the channels built into the mold. The gas (Nitrogen gas) passes through the middle of these thicker sections. Also, this creates the pressure necessary to press the resin tightly against the mold, making a smooth, structurally sound part with zero sink marks.
The application of plastic molding injection in the medical device industry is diverse. Medical suppliers go for this process as the products easily attain the stipulated standards of quality and safety. Besides, medical device plastic injection molding comes in handy in areas like:
The use of metal in medical device manufacturing is a technique that we cannot overlook. The reason is that metal equipment plays a significant role when it needs equipment with high density, small size, and maneuverability. This doesn’t detract from the numerous uses and advantages of traditional 3D printing, medical plastic molding, or gas-assisted molding.
The materials utilized in this production process easily withstand the invasion of contaminates. Also, they don’t need much sterilization to stay germ-free. Because of this factor, the material easily meets the FDA standards and other stipulated requirements.
In plastic injection molding for the medical device industry, thin-wall molding is one of the most common processes. It is for producing tools or effects that involve both function and patient comfort. The walls of the injection parts of the medical device are much thinner relative to the complete pieces. The walls are usually thinner than 1mm.
For medical component manufacturing, FDA requirements are the standards to aim at in all processes. The regulations for sterility and cleanliness are stringent and require strict observance. In all the stages of productions, ensure all inputs meet or surpass the laid down standards. For medical-grade approval, the factory must pass the standards in the components and production process.
A known fact about plastics used in injection molding is that it is ruggedly durable. These materials provide dogged strength and resistance to adverse environments and usage. Therefore, the products of this process can comfortably withstand heat, blunt force, and vibration without any incidence of cracks or breakages. Also, when they undergo sterilization in autoclaves, they don’t cave to the heat.
A minimal need for medical products but is important. All housing equipment or facility, or device parts that come in contact with the human body must be contaminant-resistant. They should also go through sterilization processes without damage.
With the level of results of this process, it’s no surprise that it serves as the medical prototype development approval process for the FDA. Here, we explain what this medical injection molding process entails and its role in the medical industry.
This is a more complicated molding type. When carrying out regular molding, the thicker parts tend to dry or solidify slower than the thinner walls. The reason is that there isn’t enough pressure to pack the resin properly and make it even.
The gas-assisted injection molding method is not suitable for creating tools with sharp corners in their design, because gas pressure will reduce if it doesn’t flow in a straight line. However, this type is more suitable for producing complex parts.
No. In the 1990s we experimented for several years with aluminum molds. We found that modern high-speed machining techniques can actually remove more steel per hour than aluminum! This is due to the amount of energy released in ultra-high-speed machining. When removing high volumes of aluminum the energy actually makes the aluminum soft, nearly melting it to a liquid form. As a result the aluminum reaches a point of diminishing returns and UHS cutting of steel surpasses the removal rate of aluminum.
Manufactures providing injection molding services use different plastic molding techniques to produce medical-grade parts. But here, we will be looking at the 4 common types, which include:
One way of producing durable and reliable medical-grade components that meet FDA standards is through medical injection molding. The process is now the go-to procedure for manufacturing state-of-the-art medical equipment because it offers countless advantages.
The injection molding procedure offers the widest range of options for choosing materials. Although medical injection molding narrows the scope of injection molding materials, there are still many materials that are suitable for manufacturing medical-grade components. We’ll touch on that more in the later parts of this guide.
Always consider the material’s area of use before selection. For instance, single-use materials like syringes, needles, tubing, and connectors should be transparent, flexible, and easy to sterilize. Likewise, surgical injection parts should be lightweight and ergonomic.
Yes, in 2023 we changed our branding to better reflect the full-service nature of our business, which is building rapid molds and providing rapid injection molding services.
Yes, we are a full-service, custom injection molder, as such we offer assembly services and a wide array of secondary services from printing to sonic welding.
GETTING A QUOTE WITH LK-MOULD IS FREE AND SIMPLE.
FIND MORE OF OUR SERVICES:
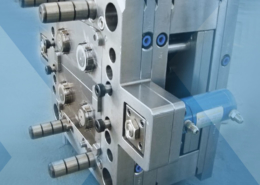
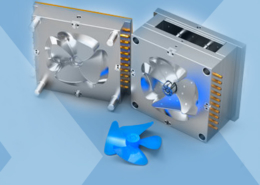
Plastic Molding

Rapid Prototyping
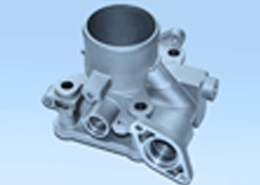
Pressure Die Casting
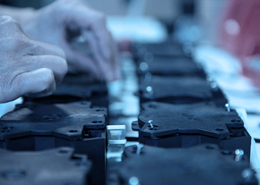
Parts Assembly
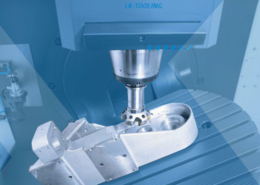