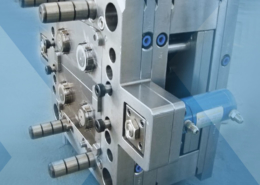
Plastic Prototype 101: What Is It and How to Manufacture It - plastic prototype
Author:gly Date: 2024-10-15
The two side actions, shown in dark grey, intersect the mold perpendicular to the parting line. Image Credit: Shutterstock.com/Solcan Design
An unscrewing action is an automated motor or manual hand screwing that creates screw or threaded features. These actions prevent damage to the threads with careful unwinding between cycles.
It should also be noted that because side actions do not follow the general tool direction, undercut features require draft angles specific to the actionâs movement. For more design strategies, download our Injection Molding Design Guide.
To perform in mold labeling during the injection molding process, the involvement of the following partners is required:
Side actions are beneficial because they increase the options for what part geometries your part can have. However, side actions can dramatically increase molding production costs, so it is helpful to consider whether you need them or whether you can avoid them by designing slot features.
Collapsible cores are mechanisms that release a circular undercut feature in a method similar to a lifter. These allow the actions to collapse inward, providing clearance for part ejection.
Hand-loaded cores are substitutes for slides or lifters, and are manually placed features which are molded around and then manually removed from the part. These are replaced each cycle.
IML for injection molding means that the decoration of the product takes place in the mold. An IML label is inserted into the mold. During the injection process, the injected molten polymer fuses with the in mold label. The end result is a decorated packaging part, produced in one step.
Slides create and release external undercut features by collapsing into place via a cam as the tool closes. It then pulls away as the tool opens.
You can also read our Ultimate Guide to Injection Molding to read about injection molding technology or view our plastic injection molding services page.
When side actions are unavoidable, it is important to understand which type of side action your manufacturer recommends for your part, as each has different cost impacts on your tooling costs. The following table describes the different types and their use cases.
Side actions are beneficial because they increase the options for what part geometries your part can have. Learn which type is best for your project.
During the injection molding process an amount of heated liquid mass is injected under high pressure into a mold. The mass cools off and solidifies in the shape of the mold. Injection molding is used for all kinds of containers, such as butter tubs and yogurt pots.
Hand loads are used for prototype and low-volume tooling as a cheaper alternative to automated slides and lifters. Hand loads can be adaptable to different part configurations in one tool.
Lifters create and release internal undercut features. Similar to slides, lifters move into place via a cam as the tool closes and move away as the tool opens.
The injection molding process is based on injecting material into a mold. The technique is most commonly performed with thermoplastic and thermosetting polymers.
Injection molding side actions are inserts (sometimes referred to as âfeaturesâ) added to the mold in order to create undercut geometry. Undercut features are perpendicular to the main parting line and cannot be produced with a straight-pull mold, or in other words, by pulling apart the two halves of the mold and ejecting the part. When side actions are added to the mold, they allow material to flow around them to form the undercut feature. The side actions must then be removed manually or automatically to allow part ejection.Â
GETTING A QUOTE WITH LK-MOULD IS FREE AND SIMPLE.
FIND MORE OF OUR SERVICES:
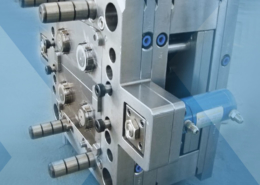
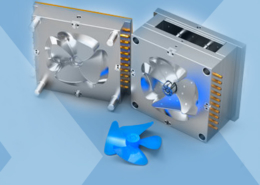
Plastic Molding

Rapid Prototyping
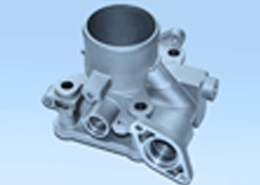
Pressure Die Casting
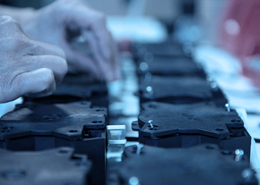
Parts Assembly
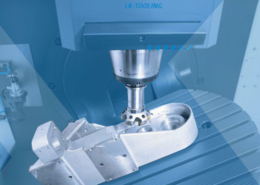