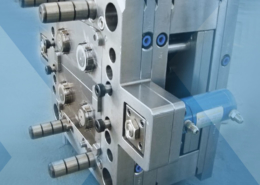
Plastic Parts Precision Injection Molding - precision plastic molding
Author:gly Date: 2024-10-15
The strength of the bond between the base material and the cover material depends on the compatibility between the materials, the process temperature, the bonding surface, the moulding sequence and the design of the internal bonding surface mechanical interlocking structure.
1) Used in power switches, mobile phone keys, car switches, etc. to meet the requirements of partial light guidance or light transmission.
Today I’m going to show you an article to let you understand 2k injection molding in 2022!(2k Injection Molding Factory/Expert/Supplier based on China.)
2k injection moulding is the simultaneous injection of two plastics at once in a dedicated two-colour injection moulding machine.
Plastics are different, their chemical properties are different, and their compatibility will directly affect the bonding strength and bonding effect of2 K injection moulding/double injection molding.
3)Products that require a multicoloured appearance, such as keyboards, the use of two-colour injection moulding makes them beautiful without the risk of rubbing off during use.
2)Application to hand-held products such as walkie-talkie housings, toothbrush handles, power tool handles, spanners and thermoses to improve feel.
The first injection of the base material and the second injection of the cover material are injected out simultaneously, requiring two injection nozzles on the injection machine, each injecting a different colour or a different base material and cover material.
2 shot injection moulding can integrate multiple functions into one plastic part, such as soft-sensitive surfaces, ergonomic design, two-colour appearance, brand identity, feature improvement, noise reduction, shock absorption, water resistance and impact protection, saving design space and reducing the number of components, etc.
On the first injection, the part should be attached to the moving mould; on the second injection, the part should be attached to the ejector side of the mould.
2) The plastic is in a molten state throughout the entire process of two-colour injection moulding, with no cooling shrinkage, which means that there is the opportunity to form a strong chemical link between the base material and the overlay material, with high strength and reduced risk of burrs occurring.
3) Compared to insert/overmold injection moulding, 2k injection moulding does not require the insertion of inserts, resulting in shorter and more efficient moulding cycles, as well as higher quality.
ENGEL ES 330/80 HL injection moulding machine was built in Austria in 1995. A highly reliable and efficient machine equipped with high-end components, is used in the processing of plastics by injection moulding. The combination of high mould clamping force and a powerful screw with a diameter of 35 mm guarantees the high quality of the manufactured products.
Because of the different chemical properties of different plastics, their compatibility will directly affect the bonding strength and bonding effect of the bonding surface, not all plastics have good compatibility with each other.
PTS Industrial Ltd is Specializing in precision manufacturing and injection molding parts since 2002. We supply CNC machining (milling&turning) parts and injection molding parts for various industries to customers worldwide.
The two plastics are injected on the same injection moulding machine and moulded twice, but the product only comes out once. Therefore, two-colour injection moulding is usually done by one set of moulds and requires a special two-colour injection moulding machine.
When the internal bonding surface is too small, the roughness can be increased by nibbling on the bonding surface on the one hand, and mechanical interlocking structures can be designed on the other.
2k injection moulding is a type of injection moulding, so DFM design guidelines for injection moulding, such as uniform wall thickness, avoidance of sharp corners and even transitions, must also be observed for 2k injection moulding.
The weight difference between the base material and the cover material should not be too big different, otherwise it will affect the moulding cycle and injection pressure etc.
After the first injection of the base material, the mould is opened and then rotated by 180° using the rotatable structure of the injection machine, then closed the mold and start second shot inejction by using a different colour of material or a different material (covering material) than the first injection.
The design of the Cosmetic mating surface at the first and second injection is very challenging and must provide sufficient bonding strength, otherwise flying edges, burrs, rolled edges and flaking can easily occur, especially in 2k injection moulding of hard and soft plastics. Common Cosmetic mating surface designs include stepped and fluted.
(1) Insert/over moulding is done using a common injection moulding machine, where the product is taken out from one mould and then put into another mould for a second injection moulding.
After the 1st injection, if the surface of the part fits directly into another fixed mould, it should be ensured that the plane has a sufficiently large release slope to avoid scratching when the mould is closed.
A toothbrush is a product that combines hard and soft plastics. A hard plastic is used for the main part of the toothbrush to provide sufficient strength; a soft plastic is used for the part that comes into contact with the hand to ensure a tactile feel; at the same time two-colour injection moulding provides the toothbrush with a colourful appearance.
The different TPE models from RTP, as pictured, differ considerably in their compatibility with plastics, even though they all belong to the TPE range (X indicates good compatibility).
After the second opening of the mould, the moving mould, which has already been injected twice, will ejected the plastic 2k part.
In this article, the first injected material is referred to as the base material and the second injected material is referred to as the overlay material.
Therefore, when designing products for two-colour injection moulding,The first and most important thing is to choose the most suitable substrate material and covering material。
The injection moulding machine works with injection moulds with a height from 170 to 370 mm, which placed on 710 x 660 mm platens are closed with a force of 80 tonnes. The machine is equipped with an ENGEL CC100 CNC controller for setting injection moulding process parameters, an ENGEL ERC 23/1-CH servo-driven multi-axis robot and a pneumatic and hydraulic core. The tie-bar-less injection moulding machine weighs 5300 kg.
In the plastics family, only ABS and polysulfone (PSU) surfaces can be plated. If a partial area or a single side of the product requires plating, the plated area should be injected with ABS and the area that does not require plating should be injected with other materials such as PC.
2k injection molding(2shot injection molding or double shot injection molding)is a manufacturing process used when referring to molding two materials/colors into one plastic part. This plastic molding technology blends two materials or two different colours materials into one ending plastic part by using 2k injection molding machine.
2)The difference between the melting temperature of the base material and the covering material does not exceed 30-60°. The melting temperatures of common plastics are shown in the following chart.
The Draft Angle is important for two-colour injection moulding because it determines which mould the part is attached to during the rotation process.
The chart above can be used as a general selection guide only. It is always best to contact your plastics supplier for a more professional opinion when selecting a specific material type. You can contact us too! info@ptsindu.com
GETTING A QUOTE WITH LK-MOULD IS FREE AND SIMPLE.
FIND MORE OF OUR SERVICES:
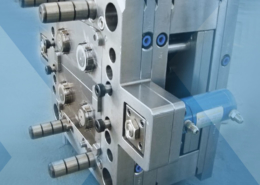
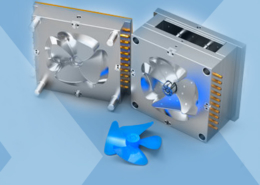
Plastic Molding

Rapid Prototyping
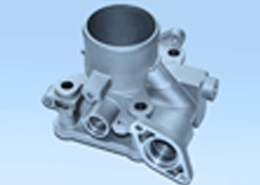
Pressure Die Casting
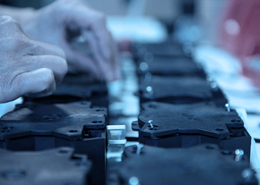
Parts Assembly
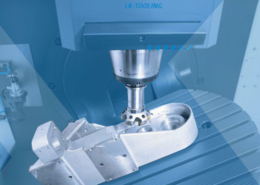