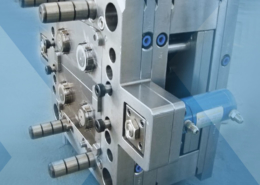
Plastic Parts Mold Manufacturer | Injection Molding | GPI - plastic part manufac
Author:gly Date: 2024-10-15
Unsurprisingly, the most common type of multi-shot moulding is the double-shot injection moulding, or what is commonly known as 2K injection moulding.
While understanding a plastic’s melting and moulding temperature is typically straight forward, there are other important factors to consider.
That is because 3K and more material or colour injection processes entail more detailed studies on the bonding of materials, geometry parts, and many other considerations.
It is important to note that such method is ideal for surfaces with maximum friction, i.e. first shot hard plastics with a second shot soft rubber designed to enhance grip non-slip surfaces for industrial hand-held devices and infant products.
Finally, the molecular structure of a plastic is important to consider. Crystalline polymers (consisting of syndiotactic and isotactic polymer chains) that are highly structured, typically have more specific melting points, which can be reliably targeted to achieve the same effect at a definite temperature.
First, the substrate is injected into its respective mould cavity, while the second shot over mould is injected into its own cavity over the substrate from the first half of the injection moulding cycle.
Amorphous polymers (made from atactic polymer chains) on the other hand have no such structure, which can make their exact melting temperature less predictable, leading to temperature ranges being more suitable for classifying their melting points.
This information should be used as an 'on the spot' reference only. Users should always follow the material suppliers processing data sheets. The data is provided “as is” and without any representation or warranty of any kind, including that it is fit for any purpose or of merchantable quality, or functions as intended or at all. Your use of this data is entirely at your own risk and PlastikCity accepts no liability of any kind.
Alternatively, in cases where the substrate and over-mould plastic material are not chemically compatible, the substrate geometry has to incorporate mechanical bonding features such as through holes or other similar features.
Another consideration is melting point depression caused by impurities in a particular plastic material. This is easily understood as analogous to roads being “salted” during the winter, with an impurity being added to adjust the melting point of ice.
For a double-shot plastic injection moulding to work, the substrate and over-mould plastic material has to be chemically compatible in order for them to form a solid bond.
Knowing the correct plastic material melt & mould temperatures is essential for all manufacturers. Injection moulding at the incorrect temperatures can have a significant impact on the final product, including the appearance & strength of the product. The table below demonstrates the optimal melt and mould temperature ranges of various plastic materials, to ensure product quality and manufacturing efficiency.
Since double-shot injection moulding is the most common multi-shot injection type, we will discuss this topic in further details below.
Multi-shot moulding is a process that moulds two or more more materials onto each other, in a single injection moulding cycle.
This is an application for employment with Kore Industries. This application will be considered current for a period of sixty (60) days following the date of application. If, at the end of this period, you still wish to be considered for employment by Kore Industries. It will be necessary for you to complete another application. Kindly complete the attached Consent Form before the application is considered valid.
As plastic heats up and melts, thermal expansion causes it to occupy more space. Because of this, application, or lack of atmospheric pressure may suppress, or accelerate the expansion: applying an adjustment to the ultimate melting or moulding temperature in any given scenario.
Next, the mould opens and the moving half or the core side of the mould is rotated 180 degrees and closed for the second half of the injection moulding cycle.
For any technical consultation or to get a quick quote, please contact us by filling up the form below. We’ll get back to you as soon as we can.
GETTING A QUOTE WITH LK-MOULD IS FREE AND SIMPLE.
FIND MORE OF OUR SERVICES:
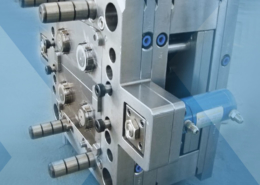
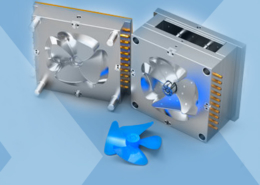
Plastic Molding

Rapid Prototyping
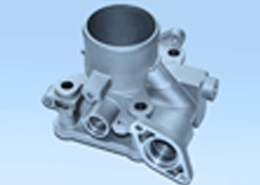
Pressure Die Casting
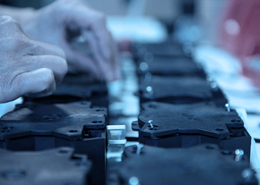
Parts Assembly
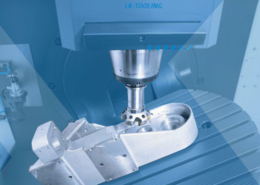