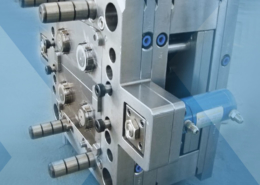
Plastic Injection Molding at Home: Revolutionizing DIY Manufacturing
Author:gly Date: 2024-06-08
Plastic injection molding has long been hailed as a cornerstone of industrial manufacturing, revolutionizing the production of various components and products. However, with advancements in technology and accessibility, this once exclusive process is now within reach for enthusiasts and hobbyists to explore and utilize within the comfort of their homes. In this article, we delve into the realm of plastic injection molding at home, exploring its possibilities, implications, and the burgeoning community surrounding it.
The Rise of Home-Based Plastic Injection Molding
Accessibility
The advent of affordable desktop injection molding machines has democratized the process, making it accessible to a broader audience. These compact machines, often utilizing open-source designs, offer hobbyists and small-scale manufacturers the opportunity to create intricate plastic parts without the need for expensive industrial equipment.
Cost-Efficiency
Compared to traditional manufacturing methods, such as CNC machining or 3D printing, home-based injection molding can be remarkably cost-efficient for producing large quantities of identical parts. The initial investment in a machine can be recouped through savings on material costs and production time, especially for recurring projects.
Customization
One of the most appealing aspects of plastic injection molding at home is the unparalleled level of customization it offers. Enthusiasts can experiment with various resins, colors, and molds to create bespoke components tailored to their specific needs or artistic visions.
Technical Considerations and Challenges
Machine Operation
Operating a home injection molding machine requires a certain level of technical proficiency. Users must familiarize themselves with machine settings, injection pressures, and cooling times to achieve optimal results. However, with online resources, tutorials, and community forums, the learning curve can be significantly reduced.
Material Selection
Choosing the right resin for a given application is crucial for achieving desired outcomes. Home users must consider factors such as strength, flexibility, and heat resistance when selecting materials. Additionally, proper handling and storage of resins are essential to maintain quality and prevent contamination.
Design and Tooling
Designing molds and tooling for injection molding requires precision and attention to detail. While software tools like CAD (Computer-Aided Design) facilitate the process, users must still account for factors such as draft angles, undercuts, and parting lines to ensure moldability and ease of ejection.
Impact and Future Prospects
DIY Manufacturing Revolution
The emergence of home-based plastic injection molding represents a paradigm shift in DIY manufacturing. It empowers individuals and small businesses to prototype, iterate, and produce high-quality plastic parts in-house, reducing reliance on outsourcing and streamlining the product development cycle.
Community Collaboration
The growing community of home injection molders fosters collaboration, knowledge-sharing, and innovation. Online forums, social media groups, and maker spaces serve as hubs for enthusiasts to exchange ideas, troubleshoot issues, and showcase their creations, contributing to a vibrant ecosystem of creativity and expertise.
Conclusion
In conclusion, plastic injection molding at home has transcended its industrial roots to become a viable and exciting avenue for DIY manufacturing. With accessible technology, a supportive community, and boundless creativity, enthusiasts around the world are harnessing the power of injection molding to bring their ideas to life. As this burgeoning field continues to evolve, it holds the promise of democratizing manufacturing and inspiring the next generation of makers and innovators.
GETTING A QUOTE WITH LK-MOULD IS FREE AND SIMPLE.
FIND MORE OF OUR SERVICES:
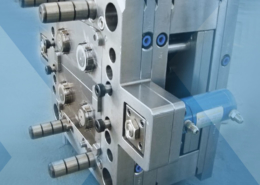
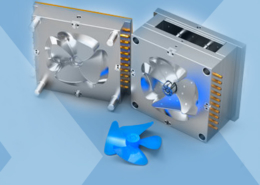
Plastic Molding

Rapid Prototyping
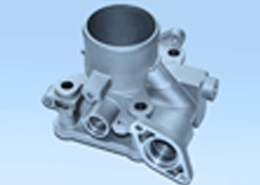
Pressure Die Casting
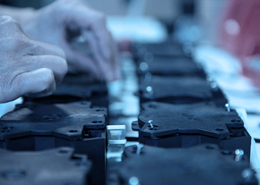
Parts Assembly
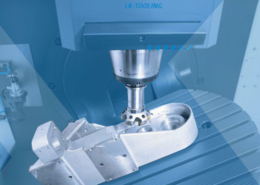