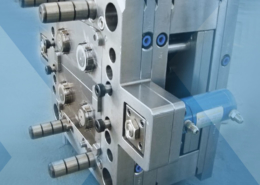
Plastic Molding Processes - wire plastic molding
Author:gly Date: 2024-10-15
When it comes to medical products, such as syringes, gloves, and masks, the ability to produce high volumes with consistency is crucial. This is where injection molding excels. With this technique, once the mold is created, thousands of identical parts can be produced without the need for maintenance.
Because these cookies are strictly necessary to deliver the website, refusing them will have impact how our site functions. You always can block or delete cookies by changing your browser settings and force blocking all cookies on this website. But this will always prompt you to accept/refuse cookies when revisiting our site.
These cookies are strictly necessary to provide you with services available through our website and to use some of its features.
Are you searching for high-quality, precise mold manufacturing solutions for your medical devices? At Remington Medical, we offer excellent contract manufacturing services that ensure consistent, high-volume production.
Plastic injection molding involves melting plastic polymers at high temperatures to create sterile and contaminant-free medical equipment. By reshaping the plastics in aluminum or steel molds, manufacturers can produce precise and customized medical devices that meet the highest standards of hygiene.
We excel at creating unique solutions for you by first understanding your product's applications. Let us become your single source for plastic products — contact us to learn more.
Did you know that injection molding is revolutionizing the medical device industry? This innovative manufacturing process ensures the creation of high-quality, precise, and cost-effective medical devices.
Plastics have become a part of everyday life, with more and more product developers opting for the benefits of rotationally molded components. The manufacturing process we specialize in — rotational molding — affords inventors, designers, and product manufacturers enhanced flexibility when compared to other forms of manufacturing.
Our injection mold manufacturing process is ideal for products and plastic parts that require large-scale production. With scalable injection molding machines, we can easily adjust to meet your needs with consistent, high-quality production every step of the way. Contact us today to learn more about injection molding for medical devices.
Injection molding is not only automated, but it also significantly reduces labor costs. With computer-controlled precision, each part is efficiently produced, resulting in lower costs per unit.
Similar to overmolding, the insert molding technique involves molding a secondary component over an existing part, or the insert. What sets insert molding apart is that it is a single process and can be used with various materials, such as plastics, metals, or alloys.
Polypropylene (PP) is a highly effective plastic polymer commonly used in medical injection molding. With its exceptional strength and resistance to cracking, radiation, impact, temperature, wear, and tear, it’s no surprise that it is a top choice in the healthcare industry. From life-saving syringes and connectors to essential knee and hip replacements, PP is the preferred material for producing critical components in healthcare.
We also use different external services like Google Webfonts, Google Maps, and external Video providers. Since these providers may collect personal data like your IP address we allow you to block them here. Please be aware that this might heavily reduce the functionality and appearance of our site. Changes will take effect once you reload the page.
With additive manufacturing, medical professionals can now rely on high-quality injection parts that meet the strictest industry standards. Whether it’s intricate surgical tools or complex implantable devices, injection molding for medical devices ensures that every component is flawlessly fabricated for optimal performance. This medical parts manufacturing process is common to develop a wide range of components, devices, and parts, such as:
We fully respect if you want to refuse cookies but to avoid asking you again and again kindly allow us to store a cookie for that. You are free to opt out any time or opt in for other cookies to get a better experience. If you refuse cookies we will remove all set cookies in our domain.
The medical injection molding process involves melting medical-grade plastics and molding them into the desired shape of medical devices. This process creates strong, durable equipment with impeccable surface finishes and precise measurements.
Polyetheretherketone (PEEK) is a high-quality thermoplastic known for its exceptional resistance to harsh environments, including radiation, high temperatures, chemicals, and wear and tear conditions. PEEK is perfect for creating medical and surgical implants and offers impeccable dimensional stability, even after being exposed to stress.
Injection molding guarantees tight tolerances and dimensional accuracy, which are crucial in the medical field. With injection molding, even the smallest deviations can be avoided, reducing the risk to patients.
Overmolding is an advanced technique that involves molding one or two components over an existing structure, resulting in a strong and durable grip. This two-step process, also known as two-shot molding, may have a longer production cycle, but the benefits are well worth it. With overmolding, manufacturers can create ergonomic handles to improve the comfort of everyday devices, which adds value and functionality to a wide range of items.
We provide you with a list of stored cookies on your computer in our domain so you can check what we stored. Due to security reasons we are not able to show or modify cookies from other domains. You can check these in your browser security settings.
Jason Dickinson (President)… 320-630-3571 James Dickinson (Vice President)… 320-360-4437 Jim Dickinson (Mold Builder)… 320-232-3559
The seamless plastic products we make within our rotational molding facility are numerous and ever growing. From water-tight tanks to mudguards and toolboxes, the possibilities are endless — and we are proud to be a part of that advancement. Whether you designed a new product headed for prototyping, or are searching for a better production solution for an existing one, Advanced Plastics Rotomolding is the first place to start.
Our custom rotational molding capabilities allow us to create a wide variety of products to meet your exact resin type, size, thickness, and color specifications.
Polyethylene (PE) is a versatile, durable medical-grade plastic polymer composed of thousands of ethylene polymers, giving it impressive tensile strength and rigidity. PE is also highly compatible with biological tissues and can withstand harsh environmental conditions, including sterilization. Thanks to these properties, PE is widely used in the medical field for manufacturing joint prostheses, connectors, tubing, pharmaceutical containers, and more.
We may request cookies to be set on your device. We use cookies to let us know when you visit our websites, how you interact with us, to enrich your user experience, and to customize your relationship with our website.
Polystyrene (PS) is a high-quality engineering-grade plastic that’s not as flexible as others, but it has exceptional mechanical properties and is compatible with body tissues. Polystyrene offers excellent dimensional stability, making it ideal for creating critical medical components like petri dishes, culture trays, and diagnostic parts.
Polycarbonate (PC) is transparent and has excellent mechanical properties. It’s tough, flexible, and resistant to abrasion, breakage, and temperature. Polycarbonate is also highly compatible with bodily tissues, making it ideal for manufacturing various medical equipment, from clear masks to protective gear and oxygenators.
Family owned and operated with nearly two decades of rotomolding experience, you can count on our company to meet the requirements of yours. Here are some of the reasons others choose Advanced Plastics Rotomolding, LLC…
Click on the different category headings to find out more. You can also change some of your preferences. Note that blocking some types of cookies may impact your experience on our websites and the services we are able to offer.
Liquid silicone injection molding involves heating silicone to a liquid state and then molding it into various shapes, making it a versatile solution for developing medical products. Silicone, a plastic polymer, is specifically designed to meet the needs of the medical industry. However, it’s important to note that silicone molds may not be as durable as aluminum or steel molds, making this technique more suitable for small quantities and initial prototyping stages.
Medical injection molding ensures that the produced components meet all necessary regulatory requirements set by the FDA.
Silicone, a unique chemically inert compound similar to synthetic rubber, offers exceptional mechanical properties and compatibility with biological tissues. With its exceptional flexibility, silicone is the go-to medical-grade plastic polymer for manufacturing a wide range of products and devices, such as catheters, connectors, and tubing.
GETTING A QUOTE WITH LK-MOULD IS FREE AND SIMPLE.
FIND MORE OF OUR SERVICES:
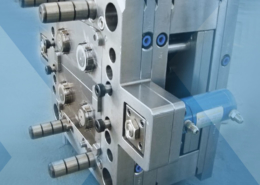
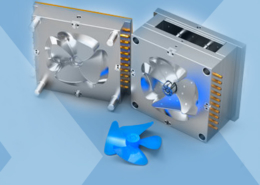
Plastic Molding

Rapid Prototyping
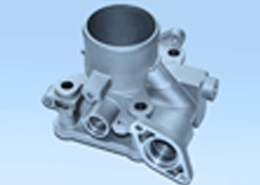
Pressure Die Casting
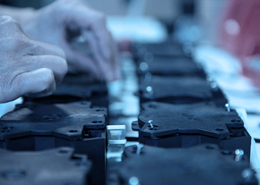
Parts Assembly
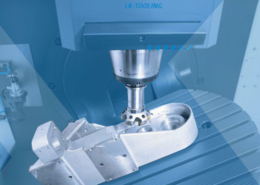