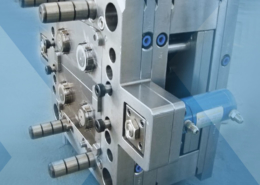
Plastic Materials for Injection Molding | Ten Common Types - flexible injection
Author:gly Date: 2024-10-15
The cost of plastic molds, like all products, is “you get what you pay for.” The more complex, precise, and durable the mold, the higher the cost.
In the medical device industry, where stringent regulations and precision are paramount, short run injection molding accelerates the development process for medical devices. It enables cost-effective production of small-batch components, making it suitable for niche applications or specialized medical devices that require limited quantities. Short run molding ensures high quality and reliability while meeting tight timelines and maintaining compliance with regulatory standards.
Of course, there is also a certain percentage of waste (e.g., 3%) during the injection molding process, but because the proportion is relatively small, it can be ignored when estimating costs.
Because this process produces semi-finished products that require further processing, there may be an increased risk of defects in the coating process. An economically viable suggestion is, if you want to save costs and achieve a beautiful finish, consider adding colorants directly to the raw material. This eliminates the need for secondary processing while still allowing for the production of products in various colors.
Factors affecting the cost of plastic molds include: size, complexity, material, expected quantity, and different mold cavity numbers and tolerance requirements also affect cost. For detailed mold costs, please refer to the article “Injection Mold Costs”.
It’s frustrating to have a brilliant product idea or a new project that requires rapid prototyping or small-batch production, but not having the capability to produce the test product. The lengthy and costly tooling process associated with conventional injection molding can be a significant roadblock, hindering innovative product development and market entry. Production delays can result in missed opportunities and potential loss of customers and market share.
The more cavities on a mold, the higher the complexity and precision of mold development, and consequently, the mold price will be higher.
Common raw material prices: PEEK > PA66 > PC > PA6 > ABS > PS > LDPE > HDPE > PBT > PET. Specific prices can be referenced based on local market prices.
Employee wages are a relatively easy part to calculate. The wages of employees involved in mold design, mold processing, etc., are calculated as part of the mold cost. However, the wages of employees in the injection molding production workshop are only calculated as part of the company’s operational costs when the customer commissions injection molding production. For example, depending on the characteristics of different products, some products may require workers to be stationed at the injection molding discharge position for processing. Common processing steps include trimming runners, visual inspections, packaging, etc.
The electronics industry benefits from short run injection molding through rapid prototyping and quick production of consumer electronics. This fast-paced process allows companies to test and validate product designs before committing to large-scale manufacturing. Unlike 3D prototyping, which often limit sample quantities, short run molding offers the ability to produce more samples in less time, providing greater flexibility for design iterations and improvements.
It is also important to note that there is a basic operation time for mold setup and removal. The time required depends on the size and function of the mold. If the order quantity is lower than the cost of changing the mold, there may be additional costs. However, plastic injection molding manufacturers usually clarify the minimum purchase quantity in advance.
Controlling injection molding costs is a shared responsibility between factories and product designers. The majority of methods to save on injection molding costs come from the injection molding factory. Here are some suggestions for reducing injection molding costs provided to injection molding factories as peers.
Note: If the mold used for injection molding has a cold runner system, there will be residual material in the runners after each injection molding cycle. When calculating, the weight of the runner material should also be included.
Today, we will mainly introduce the cost structure of injection molding factories. If you are a peer in the injection molding industry, you are also welcome to read the latter part of the article about how injection molders can reduce injection molding costs.
For example, for a mold with a 1-to-1 layout and a molding time of 60 seconds, only 60 parts can be produced in one hour. So, the machine cost per part is $100,000 / 60 = $0.08.
Regarding the specific cost of raw materials consumed by injection molded products, this part of the raw material cost can be deduced from the weight of the molded shells in injection molding.
Assuming the price of an injection molding machine is $100,000, then the daily machine cost is $100,000 / 5 / 180 = $111. If the injection molding machine works 22 hours per day, the hourly cost is approximately $5. Based on the hourly output of one injection molding machine (related to the layout of the mold and the molding time), the injection molding cost per part can be calculated.
The operational costs of a company are very complex and include employee wages, rental costs, electricity bills, administrative expenses, etc.
Short run injection molding provides a game-changing solution for companies seeking efficient and cost-effective manufacturing processes for small-scale production. We have explored the numerous benefits of this innovative technique, from its ability to meet the demands of various industries to its flexibility in customization and rapid prototyping.
Unlike many mold release brands, Stoner Molding Solutions formulates, manufactures, and distributes our own products. Check out our full line of mold releases, sealers, cleaners, rust preventatives, and lubricants. In stock products are ready to ship now!
Some clients who frequently outsource injection molding production also often feel confused about how to evaluate the cost of plastic injection products, and they may doubt whether the quotations from plastic injection manufacturers are reasonable. This confusion stems from a lack of understanding of the cost structure of plastic injection products, leading to clients spending a lot of time and energy when asking for quotes from manufacturers, and sometimes they have to pay the cost of trial and error to gain experience.
The packaging of plastic injection molded products generally includes plastic bags and cardboard boxes for semi-finished parts. For assembled components, there is the cost of assembly equipment. The more complex the product, the longer the assembly time, which may result in higher costs and affect the overall expense.
The cost composition of injection molding is actually quite transparent in the industry, mainly including: plastic mold costs, molding costs, secondary processing costs, raw material costs, packaging and transportation costs, and factory operation costs.
A more complex example: Assuming the cost of ABS plastic pellets is $1500 per ton. A mold produces parts in a 1-to-4 ratio, with each part weighing 200 grams and the runner material for 1-to-4 being 100 grams. What is the cost of raw materials per part? The calculation method is to account for each part’s weight as 200 grams + 25 grams of runner material, totaling 225 grams, and then calculate the cost as described above.
Here's where short run injection molding offers a breath of fresh air. By leveraging advanced technologies and skilled expertise, short run injection molding provides a cost-effective and efficient solution for small-scale production. With reduced tooling costs, quick turnaround times, and the ability to produce quality parts in the thousands or even just a few hundred, short run injection molding empowers companies to respond swiftly to market demands, effectively manage product development, and seize opportunities.
Utilizing the right molding products is crucial to enhance the short run injection molding process. Mold sealers are commonly used to fill in the microporosity of molds, resulting in an even finish on the molded parts. Mold release agents aid in easily releasing items from the mold after the molding process is complete. Mold cleaners help maintain the cleanliness and longevity of molds, ensuring optimal performance over multiple production cycles.
Many companies struggle with finding efficient ways to produce high-quality components in small quantities. Traditional injection molding processes may not be suitable due to high tooling costs, extended lead times, and the need for large production volumes. These limitations often hinder the ability to respond quickly to market demands, leaving businesses at a disadvantage.
The advantages and benefits of short-run injection molding are numerous. First, it allows for quick turnaround times, enabling companies to bring their products to market faster. This fast process is particularly advantageous for industries where time-to-market is crucial. Additionally, short run injection molding is a cost-effective solution, eliminating the need for expensive tooling and molds associated with larger production runs. Companies with limited budgets can benefit from this approach without compromising on quality. Furthermore, this process allows flexibility and agility in design iterations and product improvements, making it ideal for companies that value innovation and adaptability.
I am Li Yang. If you are interested in the injection molding service quotation from FirstMold, please click “Injection Molding Service Quotation“.
Short run injection molding offers cost advantages compared to larger production runs. Since fewer parts are required, less expensive mold materials such as aluminum or lower steel grades can be used, reducing tooling costs. With lower upfront costs, short run injection molding becomes accessible to a broader range of customers with smaller budgets. Additionally, adjustments and modifications can be made without significant financial commitments, and prototypes may require less finishing than in 3D printing, saving both time and cost.
Short run injection molding refers to a manufacturing process that specializes in producing plastic parts in small quantities, typically ranging from a few hundred to a few thousand units. It offers a cost-effective solution for companies that require rapid prototyping, low-volume production, or customized components. In this process, a mold is created, and thermoplastic materials are injected into the mold cavity under high pressure. The mold is opened once the material cools and solidifies, and the finished part is ejected.
If the product needs to be produced in large quantities, it is recommended to develop a mold with multiple cavities. Although the cost of mold development may be relatively higher, the production efficiency will be faster. Additionally, due to large-scale production, the unit price of the product can be reduced. Comparisons based on the number of cavities can be seen in the table below: The number of cavities represents the quantity of products produced at once, with lower costs for higher production quantities. If you are still unsure, just tell the plastic injection molding factory the estimated production volume, and an experienced plastic injection molding factory will help you calculate the most suitable number of mold cavities.
With the development of digital marketing, the prices of injection molding processes online are becoming more transparent. Understanding the costs of injection molding processes helps product design companies create better products and encourages injection molding factories to adhere to industry standards, creating a positive atmosphere for the injection molding industry.
If the product structure is simple and the quantity to be produced is small, a one-to-one cavity mold can be used, which will be relatively cheaper.
We have previously detailed the costs of injection molds. For product design companies or companies outsourcing plastic part production, they are more likely to commission injection molding factories to provide plastic injection molding services for their products, rather than just commissioning the factory to produce injection molds. After all, the mold is one part of the entire injection molding production process. Therefore, they are more concerned with the injection molding costs.
The cost of plastic injection molding depends on the size of the machine and the molding cycle. There are differences in processing costs, so injection molding costs can also be said to be part of the injection molding machine’s cost. The larger the machine, the more energy it consumes, which can increase the molding cost. Additionally, the shorter the production cycle, the faster the production speed.
By leveraging our advanced products experienced team, and commitment to excellence, we aim to make your production processes more efficient, cost-effective, and responsive to market demands. Contact us today to explore how our short run injection molding products can empower your business to create precise, high-quality parts quickly and easily.
When considering short run injection molding solutions, several factors come into play. These include cost factors and budget considerations, design limitations, material selection, and the use of the right molding products.
For example: Assuming ABS plastic pellets cost $1500 per ton (this is an example, please refer to the actual local price). If the shell weight of a product after injection molding is 200 grams, then the raw material cost of the product is $1500 / 1000000 * 200 = 0.0015 * 200 = $0.3.
Some plastic injection molding factories also provide finishing services, including surface treatments such as coating, printing, painting, and electroplating.
We can calculate the annual injection molding cost based on a 5-year depreciation of the injection molding machine. For example, if the industry’s startup rate for the injection molding machine is 50% (i.e., 180 days per year), divide the annual depreciation of the injection molding machine by 180 days to calculate the daily machine cost.
The volume and weight of the packaged plastic products, as well as the method of transportation, will affect transportation costs.
It is worth mentioning that if the quantity of plastic parts produced is not large, the cost of the mold will account for a relatively large proportion of the total price; if the quantity of plastic parts produced is large enough, many factories may even waive the mold cost.
Short run injection molding does not significantly restrict resin requirements due to the mold material. It allows for utilizing a wide range of resins available in higher volume molding processes. Material selection plays a critical role in determining the final product's quality, durability, and performance. Factors such as environmental conditions and specific requirements need to be considered when choosing the appropriate material. By carefully selecting the right material and considering design limitations, companies can ensure that the chosen material meets all necessary requirements while remaining cost-effective.
The packaging industry benefits from short run injection molding by enabling the creation of unique packaging designs for limited-edition products. It allows companies to meet specific packaging requirements for new product launches, ensuring eye-catching and functional packaging solutions. Short run molding provides the flexibility to produce a limited number of parts while keeping options open for future design changes or additions.
By considering these factors and leveraging the benefits of short run injection molding, companies can achieve efficient and cost-effective production for their customized components prototypes.
As for other complex company operational costs, each company will have its own calculation standards. These costs are usually calculated by the factory’s finance department, with a rough formula to distribute the results evenly among each injection molded part.
Different products have different tolerance standards, with higher precision leading to higher costs. The cost of a mold with a tolerance of ±0.2mm will certainly differ from that of a mold with a tolerance of ±0.02mm.
Short run injection molding finds application in various industries. Still, four key sectors stand out for reaping significant benefits from this manufacturing process: the automotive industry, the electronics industry, the medical device industry, and the packaging industry.
In the automotive industry, short run injection molding plays a vital role in customizing parts for specific models. It enables manufacturers to produce limited quantities of high-quality components with precision, ensuring a perfect fit and finish. This top-tier quality is particularly valuable for luxury and exotic car manufacturers who offer high-end vehicles in limited numbers. By leveraging short run molding, they can maintain exceptional quality standards while meeting the demand for exclusivity.
General-purpose plastic raw materials are relatively inexpensive. If the plastic raw material has high strength and strong chemical resistance, the cost will be higher (including some modified materials).
The cost of raw materials depends on the functionality and requirements of the product. Common plastic raw materials include PP, PE, PC, ABS, PBT, and dozens of others. All plastic raw materials are influenced by fluctuations in the price of petroleum raw materials. If the product requires blending or colorants, the costs will be calculated separately.
GETTING A QUOTE WITH LK-MOULD IS FREE AND SIMPLE.
FIND MORE OF OUR SERVICES:
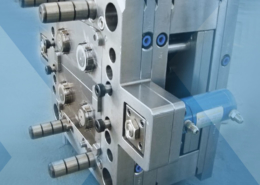
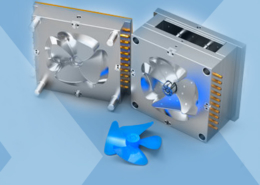
Plastic Molding

Rapid Prototyping
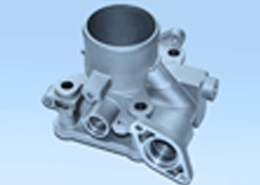
Pressure Die Casting
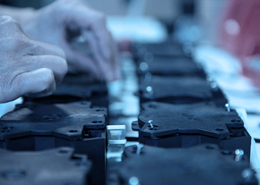
Parts Assembly
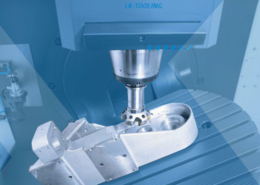