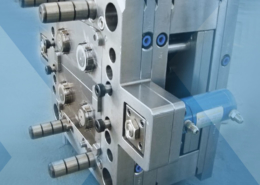
Unveiling the Precision of Plastic Injection Manufacturing
Author:gly Date: 2024-06-08
Introduction
Plastic injection manufacturing stands as a cornerstone of modern industry, enabling the production of diverse products with unparalleled precision and efficiency. From intricate automotive components to everyday consumer goods, plastic injection molding plays a pivotal role in shaping our world. This article delves into the depths of plastic injection manufacturing, exploring its processes, applications, innovations, challenges, and future prospects.
The Art of Injection Molding
Plastic injection molding is a versatile manufacturing process that involves injecting molten plastic into a mold cavity under high pressure. This process allows for the production of complex geometries with exceptional detail and consistency. By leveraging a wide range of thermoplastics and thermosetting polymers, manufacturers can tailor material properties to meet specific product requirements.
The injection molding process comprises several stages, including mold preparation, material melting, injection, cooling, and ejection. Each step requires precise control and optimization to ensure optimal part quality and production efficiency. Advanced technologies, such as computer simulations and real-time monitoring systems, enhance process predictability and reliability.
Applications Across Industries
Plastic injection manufacturing finds applications across a myriad of industries, ranging from automotive and aerospace to healthcare and electronics. In the automotive sector, injection-molded components such as dashboards, bumpers, and interior trim contribute to vehicle aesthetics, performance, and safety. Similarly, in the medical field, disposable syringes, surgical instruments, and implantable devices benefit from the precision and sterilizability offered by injection molding.
Furthermore, the consumer goods industry relies heavily on injection molding for the production of household appliances, packaging materials, and consumer electronics. The versatility of the process enables manufacturers to cater to diverse market demands while maintaining cost-effectiveness and production scalability.
Innovations Driving Efficiency
Innovation is at the core of plastic injection manufacturing, driving continuous improvements in efficiency, sustainability, and product performance. One notable innovation is the integration of Industry 4.0 technologies, such as IoT devices and AI-driven analytics, into injection molding machines. These smart manufacturing solutions enable real-time monitoring of production parameters, predictive maintenance, and adaptive process control, optimizing resource utilization and minimizing downtime.
Additionally, advancements in material science have expanded the range of materials suitable for injection molding. Biodegradable polymers, recycled plastics, and bio-based resins offer eco-friendly alternatives to conventional plastics, addressing growing concerns about environmental sustainability.
Challenges and Future Outlook
Despite its numerous advantages, plastic injection manufacturing faces several challenges, including rising material costs, regulatory compliance, and the need for skilled labor. Moreover, the ever-increasing demand for customization and shorter lead times necessitates agile manufacturing strategies and flexible production systems.
Looking ahead, the future of plastic injection manufacturing is ripe with opportunities for innovation and growth. Emerging technologies, such as micro-injection molding and multi-material molding, promise to expand the capabilities of the process, opening new avenues for product design and functionality. Furthermore, the integration of digital twins and virtual simulations will revolutionize mold design and optimization, further enhancing product quality and time-to-market.
Conclusion
In conclusion, plastic injection manufacturing represents a cornerstone of modern manufacturing, enabling the production of diverse products with precision, efficiency, and scalability. Through continuous innovation, adaptive strategies, and a commitment to sustainability, plastic injection manufacturers are poised to shape the future of industry. By embracing emerging technologies and collaborative partnerships, they can overcome challenges and unlock new opportunities for growth and development.
GETTING A QUOTE WITH LK-MOULD IS FREE AND SIMPLE.
FIND MORE OF OUR SERVICES:
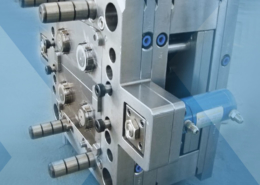
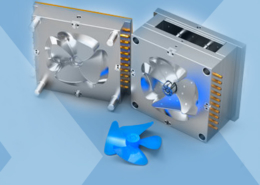
Plastic Molding

Rapid Prototyping
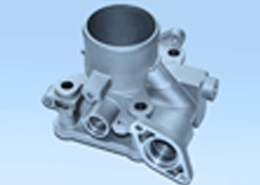
Pressure Die Casting
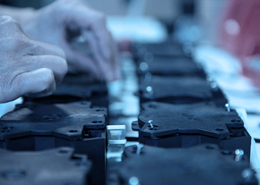
Parts Assembly
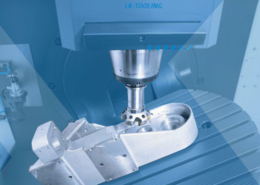