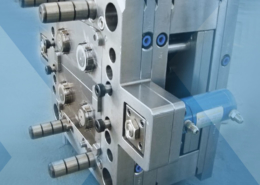
Plastic Injection Mouldings & Manufacturing Solutions | Hi ... - hitech plastics
Author:gly Date: 2024-10-15
Advancements in material manufacturing techniques and technologies have led to the widespread use of plastics in modern manufacturing operations. In the medical and pharmaceutical industries, plastics are often used alongside the injection molding process to produce prototypes and full-production units of medical device and equipment components. As newer plastic materials and component designs are developed, injection molded plastics have increasingly contributed to lower infectious disease rates, better pain management, and lower medical costs.
The injection molding process accommodates a wide range of plastic materials, making it well-suited to produce medical and pharmaceutical parts from whatever medical-grade plastic is required for the project. There are numerous plastics suitable for medical injection molding operations, each of which offers unique properties and performance characteristics. Common plastic material options for medical injection molding include:
There are no good parts without good injection tools. You invest in a quality mold made to European standards. The design, the manufacture and the maintenance are performed internally in our mold workshop. We guarantee the servicing.
As indicated above, injection molding is one of the most efficient and cost-effective ways of manufacturing parts that meet the strict specifications and standards of the medical and pharmaceutical industries. For example, the process is often used to manufacture the small, high-precision components found in diagnostic testing kits, such as the lateral flow in-vitro diagnostic test cartridge produced in large quantities by our team.
Specialist in plastic injection in China for more than 15 years. From the study to industrialization of parts and sub-assemblies, we can guarantee you secure, easy, qualitative and competitive cooperation.
Given the broad selection of suitable material options available, the first step in choosing a material for a project is narrowing down the list to the material family that fulfills the most part requirements (e.g., tensile strength, temperature load rate, etc.). From there, it is much easier to select the grade that best suits the project. Online databases—such as UL Prospector, MAT Web, and The British Plastics Federation—can provide information about materials that can further facilitate the selection process.
At Sterling Healthcare Manufacturing, we specialize in full-service, turnkey plastic component injection molding solutions. Our comprehensive part manufacturing capabilities allow customers to maintain oversight over the production of their parts, resulting in greater transparency and accountability. Additionally, we maintain ISO 9001:2015, our new ISO 13485 cleanroom certification and employ the use of FDA/medical-grade materials to ensure our injection molded components fully meet the strict specifications and standards of the medical and pharmaceutical industries.
To see an example of our work in the medical industry, check out this case study documenting how we optimized the mold design for a polystyrene diagnostic kit. You’ll also learn about how our custom capabilities — such as machine vision inspection — guarantee quality, cost efficiency, and 100% reliability for every order we complete.
Nous utilisons des cookies pour optimiser notre site web et notre service.Conformément à vos choix, certains partenaires et nous pouvons accéder à votre terminal pour vous reconnaître via des traceurs comme des cookies, collecter, stocker, croiser, et transférer des données comme vos adresses IP et email, vos paramètres de logiciels, votre navigation ou votre localisation, à ces fins : Publicités standards et mesure de performance des publicités, Profil de publicités personnalisées et affichage, Contenu personnalisé et Mesure de performances du contenu, données d'audience, et développement produit.Nous vous en remercions et vous proposons d'appliquer vos choix à ces partenaires également. Vous pouvez bien sûr refuser leurs traceurs et traitements.
We provide different finishing operations (marking, stamping, screen printing, etc.) and the decoration of injected plastic parts to give the desired appearance.
Once the manufacture of the tools is finished, we launch the production in our injection workshop. Our production lines are completely automated, and each batch is checked. Our expertise concerns as much injection as bi-injection; over-molding, gas assisted injection.
As mentioned above, there are many types of plastics available for medical injection molding operations. Each plastic possesses distinct qualities that influence how it performs in specific applications. Some of the key factors to consider when choosing between the material options include:
Medical and pharmaceutical products play a vital role in the health and safety of patients. As such, ensuring the quality of each product and its individual components throughout the manufacturing process—from design to final inspection—is essential. For this reason, it is vital to partner with an experienced medical/pharmaceutical component manufacturer that emphasizes quality and offers complete part traceability from start to finish.
Our integrated design office is in charge of the optimization of the part and the design of the plastic injection molds. It can intervene upstream of the prototyping phase.
Expert in plastics injection molding, in our workshop in China we produce all types of plastic technical and appearance parts from small runs to mass production. We have fully automated injection presses from 70 to 1200T. The injected parts can then be assembled on our assembly lines and finalized by various finishing and decoration operations (metalizing, painting, inserts, etc.).
Upstream of series production, we offer different fast prototyping technologies. These prototypes allow us to test a pre-series, and to perform visual, functional and mechanical tests.
At The Sterling Healthcare Manufacturing, we understand the importance of quality in component manufacturing. By leveraging our extensive knowledge of the medical and pharmaceutical industries, we provide full-service, turnkey plastic injection molding solutions that fully comply with industry specifications and standards. For additional information about our plastic injection molding capabilities and how we serve the medical and pharmaceutical industries, contact us today.
We work with all types of thermoplastic and elastomer materials according to customer specifications: ABS, PC, PMMA, TPE, PA, TPU, POM etc., with or without loading. We master different injection processes depending on the characteristics of the parts to inject. Our design office, a department central to our organization, ensures the optimization of the part whether it is at the prototyping or the molding by injection stage. In addition, it takes charge of the design of the plastic injection molds and the 3D drawings will be given to you. The molds will be manufactured in our tooling workshop and maintained in our dedicated and laid-out storage room.
Compared to other plastic manufacturing processes, plastic injection molding offers a number of clear advantages, especially when working with a knowledgeable and skilled injection molding partner. These benefits encompass the following:
Plastic injection molding is an efficient and cost-effective method of producing medical and pharmaceutical parts to high levels of precision, accuracy, and quality. It is used to create components from medical devices and equipment to laboratory tools and testing instruments. The following page provides an overview of the plastic injection molding process and its essential role in the medical and pharmaceutical industries.
GETTING A QUOTE WITH LK-MOULD IS FREE AND SIMPLE.
FIND MORE OF OUR SERVICES:
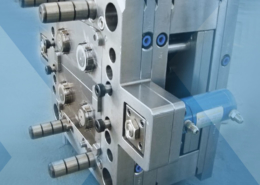
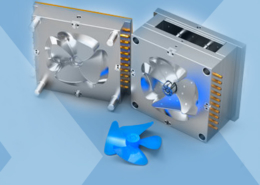
Plastic Molding

Rapid Prototyping
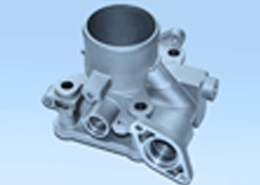
Pressure Die Casting
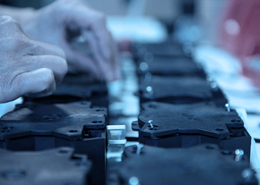
Parts Assembly
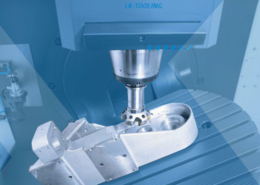