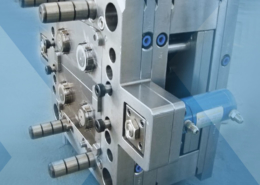
Plastic Injection Moulding | Plastic Manufacturing Product ... - hard plastic mo
Author:gly Date: 2024-10-15
Additionally, always verify that the machine’s injection capacity matches the design and material requirements to avoid short shots caused by insufficient power or pressure.
However, be cautious when adding lubricants—they should improve flow without restricting the material’s ability to fill the mold.
This technique is particularly useful for larger or intricate parts where traditional gating might struggle to fill the mold entirely.
In addition, Associated Biotech must ensure sustainability and environmental management in compliance with the emerging trend of green practices in the pharma industry. These environmental conservation practices help to ensure a safer and healthier environment hence improving the reputation of their partners.
Another advantage is research and development which helps Associated Biotech to develop new ideas of injectable formulations. They work directly with their partners to achieve tailor-made process manufacturing solutions that maintain product stability and enhance bioavailability and patient compliance. The expertise of a technologically advanced third-party manufacturer can be beneficial for improving the stability of injectable products of pharmaceutical companies.
In hot runner systems, discrepancies in temperature control can freeze flow channels, further preventing proper filling.
If the fill volume is too low or the pack and hold pressure settings are incorrect, the material won’t fill the entire mold.
Before starting production, many manufacturers now use simulation software to test how the plastic will flow through the mold.
By understanding the causes—such as material flow, machine settings, and mold design—you can implement effective solutions to optimize production and prevent these issues.
Using mold flow simulations allows engineers to refine the mold design and manufacturing process, minimizing defects from the outset.
By opening and closing gates in sequence, these systems allow for better material distribution, reducing the risk of short shots in hard-to-reach areas of the mold.
Progressive Short Shot Tests: This involves stopping the injection process partway through to see how far the molten plastic is filling the mold. This method helps identify problem areas in the mold design or flow.
Low melt or mold temperatures can cause the plastic to solidify before it fills the mold, leaving voids or incomplete sections.
We are committed to helping you elevate quality standards, fostering enterprise growth, and actualizing your internationalization strategy.
Process Monitoring: Monitoring the injection pressure, temperature, and speed during the molding process helps catch short shots in real-time, allowing for adjustments before defects occur.
Manufacturing resources offered by Associated Biotech include almost all types of injections such as vials, ampoules, prefilled syringes, etc. Their experience in managing different therapeutic classes of products including antibiotics, analgesics, and vaccines empowers their partners to expand their product ranges while at the same time not having to start new production lines. This flexibility allows the pharmaceutical company to adapt quickly to market needs as well as capitalize on potential opportunities that may arise.
To avoid short shots, manufacturers can optimize material selection by using materials with suitable flowability and adjusting melt temperatures. Machine settings like injection pressure and speed should be fine-tuned to ensure proper flow. Additionally, mold designs can be enhanced by enlarging gates and runners, improving venting, and ensuring consistent temperature control to prevent premature plastic solidification.
Reach out to our team today for expert guidance and solutions to enhance your production efficiency and product quality!
HITOP is committed to assisting customers by offering a comprehensive one-stop solution, encompassing product design enhancement, initial sample creation, mold fabrication, injection molding, and product assembly.
Additionally, using an undersized machine or one with insufficient capacity for the material can result in incomplete parts.
Visual Inspection: One of the quickest ways to detect short shots is by examining the part for incomplete filling, voids, or thin areas.
Short shots happen when the molten plastic fails to fill the entire mold cavity during the injection molding process. This results in incomplete parts, often with voids or missing sections, such as a missing prong on a plastic fork. Short shots are typically caused by improper material flow, inadequate machine settings, or mold design flaws.
These tools help to identify potential problem areas, optimize gate placement, and adjust runner designs, all of which can significantly reduce the likelihood of short shots.
Ghatti Post Office, Khasra no. 121 Min, 122 Min, SIDCO INDUSTRIAL COMPLEX, Pandrar Ghatti,Nanan, Kathua, Jammu & Kashmir,
Also, maintaining consistent mold cooling will prevent early solidification of the plastic, reducing the risk of short shots.
The pharmaceutical industry is dynamic and advancing by improving new technological features and products. This is why Third Party Injectable Manufacturers such as Associated Biotech get to learn of these advancements, and they go ahead to incorporate them in their facilities by acquiring advanced equipment as well as processes. They have to be committed to their innovations for their partners to get to profit from the improved manufacturing techniques and technologies.
Hi, I am Sparrow Xiang, COO of the HiTop company, me and my team would be happy to meet you and learn all about your business, requirements and expectations.
We have manufacturing facilities thus ensuring that we maintain the latest and most modern equipment Acceptable for the regulations. This keeps their partners benefiting from economies of scale and efficient production processes, owing to their vast experience in manufacturing injectable products. This efficiency helps to reduce the costs of production, which in turn helps the pharmaceutical companies to address other critical issues competently.
The role played by third party injection manufacturers is very crucial in the operation of the pharmaceutical industry. Outsourcing is highly beneficial to injectable production, and Associated Biotech is an example of how outsourcing impacts cost, reliability, technology, and compliance in the industry. Third-party manufacturing can help pharmaceutical organizations improve their effectiveness while always remaining committed to the production of the best injectable medicine that can be chosen by patients from all over the world. Overall, the role of third-party manufacturers is critical and will continuously play a significant role in the industry growth and availability of vital products such as life-saving medications.
Short shots in injection molding can cause significant defects in plastic parts, impacting their quality and functionality.
Quality control standards at Associated Biotech undertake a strict quality system whereby every aspect of production is closely monitored to ensure that only high-quality products are produced. Its quality control officers do extensive inspection and testing of each lot of injectable products to meet set quality standards. As such, working with Associated Biotech, pharmaceutical companies can effectively minimize the risks of losing clients due to non-compliance with legislation and product recalls.
When Third Party Injectable Manufacturing is outsourced, pharmaceutical companies can focus on their strengths, including new drug discovery, product promotion, and delivery. New drugs take time, skill, and capital to discover and bring to the market. Outsourcing of the manufacturing aspect therefore allows companies to not only cut on costs but also reduce the overall time it takes for them to bring a certain product to the market.
Addressing short shots is crucial for maintaining high product standards and ensuring efficient production processes, saving both time and costs in the long run.
Common signs of a short shot include visible gaps, weakened structural integrity, and parts that fail to meet dimensional specifications.
Identifying and addressing short shots early on is crucial to ensuring the quality and performance of your plastic products.
It is essential to adhere to the laws that govern the trade of drugs and to supply high-quality products. Third party injection manufacturers such as Associated Biotech are proficient in these aspects. They are well accredited with credibility assessment as reflected in the Good Manufacturing Practices (GMP) and other ISO certifications.
Pharmaceutical manufacturing is vulnerable to various disruptions including natural disasters and supply chain disruptions or changes in regulatory requirements. Third Party Injectable Manufacturer in India also help reduce risk and ensure business continuity, which is essential for the industry. Since Associated Biotech has many manufacturing facilities and has already established strong supply chain management, its partners can ensure a stable supply of injectable products even if there are some difficulties.
Adjusting Process Conditions: Increasing injection speed or pressure can improve material flow and ensure the mold is fully filled. Sometimes, fine-tuning the melt and mold temperatures can prevent premature cooling and solidification of the plastic.
A short shot in injection molding occurs when the molten plastic doesn’t fully fill the mold cavity, leaving parts incomplete or missing material.
Another benefit of outsourcing with certain Third Party Injection Manufacturing, such as the Associated Biotech that has been described in the article, is the fact that the cost is likely to be lower in the long run. The development and sustenance of manufacturing plants for injectable products are capital-intensive in terms of infrastructure, equipment, and regulatory standards. Pharmaceutical companies do not have to make these capital expenditures when outsourcing to a third-party manufacturer, which also lowers costs.
Improving Mold Design: In cases where the mold design is causing the issue, solutions include enlarging gates and runners, optimizing venting to avoid trapped air, or simplifying the part geometry to ensure even flow.
In this article, we’ll explore the causes behind short shot injection molding, how to troubleshoot them effectively, and strategies to prevent them.
Dimensional Analysis: Measuring the part’s dimensions can reveal areas where the mold wasn’t completely filled, especially if the part is out of spec.
The primary cause of short shots is excessive flow resistance, which prevents the molten plastic from fully filling the mold cavity. Several factors contribute to this issue, including part wall thickness, mold and melt temperatures, injection pressure, and material properties. When these factors are not properly managed, short shots can occur, leaving parts incomplete.
It occurs when the molten plastic doesn’t fully fill the mold, leaving voids or incomplete sections in the final product.
Additionally, flow restrictions caused by narrow runners or improperly placed gates can limit how well the material reaches all parts of the mold.
Third Party Injection Manufacturers – Third-party manufacturing is now one of the industry’s pillars as the pace of development of the pharmaceutical industry speeds up. This model also enables companies to remain faithful to their core competencies while accessing the capabilities and infrastructure of contract manufacturers to achieve economies of scale. Among the market-leading third-party injection manufacturers, Associated Biotech can be considered one of the major players in this field. In this article, the author focuses on the role of a third-party injection manufacturing and describes how Associated Biotech exemplifies the advantages of this model.
GETTING A QUOTE WITH LK-MOULD IS FREE AND SIMPLE.
FIND MORE OF OUR SERVICES:
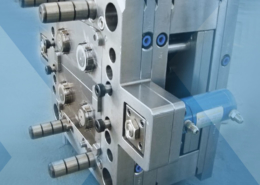
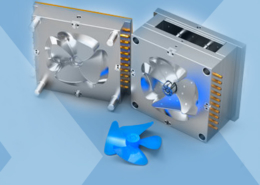
Plastic Molding

Rapid Prototyping
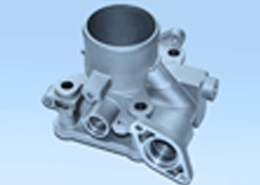
Pressure Die Casting
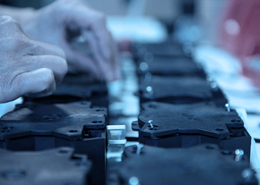
Parts Assembly
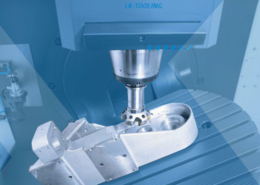