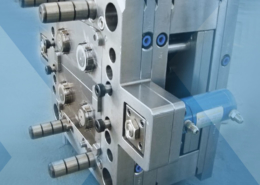
Plastic Injection Moulding Machine - plastic injection press
Author:gly Date: 2024-10-15
Ergonomics is the top priority for this injection molding machine. The clamping unit enables ergonomic overmolding of inserts. Thanks to the wide range of options and the flexible machine concept, the machine can be adapted to your requirements.
Our custom mould makers take your overall product design, break it down into required components, then create the required CNC-compatible files needed to machine your injection mould. Considering factors like component complexity and scale of production, weâll optimise your tooling to match your manufacturing needs.
Our electric machine portfolio reaches from the standard e-mac stock machine and the customizable e-mac and e-motion to the high-performance e-cap and e-speed, which are especially suited for the packaging industry. In addition, the integrated encapsulated toggle of the injection molding machines is the optimum solution for cleanroom applications. The clamping force ranges from 300 to 6,500 kN.
Whether hydraulic, hybrid or all-electric: ENGEL injection molding machines are among the most efficient machines on the market. Servo-hydraulic machines consume less than 60% compared to hydraulic injection molding machines with a fixed displacement pump. For all-electric injection molding machines, energy consumption can usually be cut in half.
Our two-platen injection molding machines are characterized by an extensive clamping force on the smallest footprint. It includes machines from 3,500 to 55,000 kN clamping force: from the entry-level t-win model and the customizable duo tech to the fast duo speed. The duo series is one of the most energy-efficient machines of this type - with up to 55% less energy consumption than machines without servo hydraulics.
Pharmaceutical and medical technology products such as syringes, pipettes, or other products with high levels of cleanliness,
With integrated temperature control solutions and our digital assistance systems, an additional energy-saving potential of up to 67% can be possible.
Have your productâs plastic components mapped out in CAD but scratching your head on how to get the moulds made? Shopped around and found only extraordinarily long wait lists? At NDC Plastic Moulding, youâll find the tooling design and manufacturing services you need to mould your vision on your schedule.
Our two-platen injection molding machines are characterized by an extensive clamping force on the smallest footprint. It includes machines from 3,500 to 55,000 kN clamping force: from the entry-level t-win model and the customizable duo tech to the fast duo speed. The duo series is one of the most energy-efficient machines of this type - with up to 55% less energy consumption than machines without servo hydraulics.
Our electric machine portfolio reaches from the standard e-mac stock machine and the customizable e-mac and e-motion to the high-performance e-cap and e-speed, which are especially suited for the packaging industry. In addition, the integrated encapsulated toggle of the injection molding machines is the optimum solution for cleanroom applications. The clamping force ranges from 300 to 6,500 kN.
We focus on forward-looking development and the production of injection molding machines and automation. Innovative technologies, modern production facilities and sustainable service and support enable our customers to be competitive and successful.
Often, we’ll use a combination of technologies to create custom injection moulds. For example, for optimum results where an extra deep cavity is required, we might opt for spark erosion EDM. This requires machining a custom electrode (often copper) which creates an impression in the billet in its own shape. To engineer the electrode, we might use a combination of CNC milling and wirecut EDM, if any perfectly square corners are required.
Our product portfolio ranges from 280 kN to 55,000 kN clamping force. It includes hydraulic, hybrid and electric injection molding machines with horizontal or vertical injection units. From fast available stock machines and customized machines to high precision production cells with the shortest cycle times.
Toolâs down? We might be able to get it up and about again! Send us some details of your issue or arrange a one-on-one with a tooling technician today.
As you can see, tooling design and production demand diverse skills and equipment. With NDC Plastics you can be confident that we’ll devise the most efficient and effect plan for creating custom tooling that meets your specifications and project requirements.
Has your product design evolved, requiring changes to its components? Slight defect in an otherwise functional mould? Sometimes our masters of mould machining can modify the size and shape of the mouldâs cavities to accommodate design changes, or rectify minor structural issues, avoiding the cost and time involved in starting from scratch.
Pharmaceutical and medical technology products such as syringes, pipettes, or other products with high levels of cleanliness,
Once the cavities are created, we’ll carry out manual processes like surface grinding the outer surface of the mould to ensure its completely flat.
With over 20 proven injection molding processes, ENGEL allows economical production despite increasing product requirements.
We focus on forward-looking development and the production of injection molding machines and automation. Innovative technologies, modern production facilities and sustainable service and support enable our customers to be competitive and successful.
The process for designing custom tooling typically involves several stages, including concept development, design and engineering, prototyping, testing, and final production. During the concept development stage, our design team works with the client to identify their specific needs and requirements. From there, weâll create detailed design plans and 3D models, which will be used to create prototypes for testing and refinement. Once the final design has been approved, we’ll manufacture injection moulds ready for mass production.
Whether hydraulic, hybrid or all-electric: ENGEL injection molding machines are among the most efficient machines on the market. Servo-hydraulic machines consume less than 60% compared to hydraulic injection molding machines with a fixed displacement pump. For all-electric injection molding machines, energy consumption can usually be cut in half.
With over 20 proven injection molding processes, ENGEL allows economical production despite increasing product requirements.
We know that the requirements of our customers and the products they produce are versatile. At ENGEL, we see ourselves as a turnkey solution provider. We support our customers with their challenges. Our injection molding machines stand for efficiency, quality and reliability.
Once designs have been finalised for required components, we can begin the precision engineering of your custom injection mould/s (also known as âtoolingâ). Our CNC machining expertise and access to the latest equipment enable us to provide precise, professional tool manufacturing services 100% in-house.
Weâre keen to get working on a mould that will go from our toolroom âstraight to the pool room!â Send us a message, give us a call, or arrange a time for an obligation-free consultation with an expert.
When choosing an injection molding machine, the customer's requirements are the most relevant. ENGEL therefore classifies the machines based on the following customer requests:
We use a range of CNC and manually operated machinery to precision engineer the finished mould. Most of our injection moulds are made from steel, although it’s possible to use aluminium. We start with a solid block of metal (or billet), creating one or more cavities in it using various cutting, milling and eroding tools. These cavities are filled with molten plastic during the injection moulding process.
Ergonomics is the top priority for this injection molding machine. The clamping unit enables ergonomic overmolding of inserts. Thanks to the wide range of options and the flexible machine concept, the machine can be adapted to your requirements.
Compact, energy-efficient and consistently high part quality: The victory series - from 280 to 5,000 kN clamping force - offers you the perfect modular system to produce technical parts. The patented Force Dividers, which distribute the clamping force evenly over the entire clamping surface, guarantee consistently high part quality, even with multi-cavity molds. In addition, the proven tie-bar-less technology allows the use of a small injection molding machine for large molds. You only invest in the clamping force that is needed, saving valuable production space.
Let us write the rules for the tools you need to create custom components. Get in touch or book a meeting with our team.
Compact, energy-efficient and consistently high part quality: The victory series - from 280 to 5,000 kN clamping force - offers you the perfect modular system to produce technical parts. The patented Force Dividers, which distribute the clamping force evenly over the entire clamping surface, guarantee consistently high part quality, even with multi-cavity molds. In addition, the proven tie-bar-less technology allows the use of a small injection molding machine for large molds. You only invest in the clamping force that is needed, saving valuable production space.
In most cases, yes, we do all the tool design and manufacture 100% in -house. If an especially large injection mould is needed, we may recommend outsourcing to a specialised toolmaker. Our modern toolroom and injection moulding experts are well equipped to handle most tooling requests.
Depending on your project parameters, we can create multiple cavities on the same mould to scale up your output. Employing such efficiency-enhancing strategies means we can measure up to manufacturing metrics more quickly.
With integrated temperature control solutions and our digital assistance systems, an additional energy-saving potential of up to 67% can be possible.
GETTING A QUOTE WITH LK-MOULD IS FREE AND SIMPLE.
FIND MORE OF OUR SERVICES:
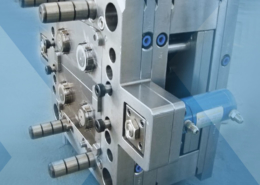
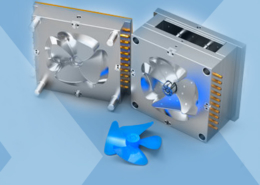
Plastic Molding

Rapid Prototyping
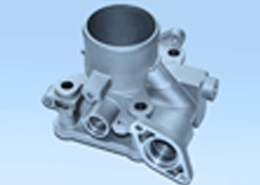
Pressure Die Casting
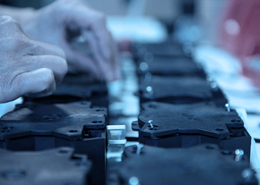
Parts Assembly
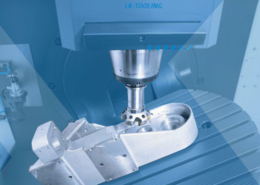