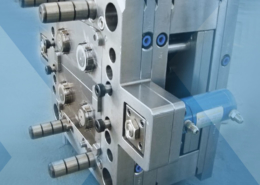
Plastic Injection Moulding By Allmould Plastics - injection moldable plastics
Author:gly Date: 2024-10-15
In the medical field, micro injection molded products present a rapidly increasing demand. We challenge the limits of micro injection molding and produce more sophisticated medical plastic parts, promoting the development of medical technology.
Medical insert molding is a cost-effective and efficient means which we use to manufacture high-precision, high-accuracy, and high-quality medical and pharmaceutical parts. Insert mold is critical for close-tolerance medical products molding.
Tight tolerance production is important in medical devices as a small difference can alter the performance of a component. With injection molding, a high quantity of medical components can be produced with exceptional accuracy.
As a top medical plastic injection molding company, medical grade plastics we use for medical plastic injection features stability, compression resistance, and chemical resistant properties. They can withstand extremely high temperatures and tensiles. We could give you some advice on material selection for injection molding.
To join molded pieces, mechanical or manual methods are used. We are a clinic equipment supplier in the development of injection mold products for a variety of industries. Our injection molds are produced from high-quality raw materials, making them sturdy and long-lasting.
We have the cutting-edge technologies needed to create exceptionally high-quality products and Ultra-Precise Dual Lumen Medical Overmold . This kind of mold technology is very suitable for complex medical device injection. You can take your business to the next level by getting in touch with us now.
As a leading medical molding supplier, we provide medical and pharmaceutical industries with injection molded parts that have undeniable importance in their long and useful life.
Seasky Medical serves you with medical injection molding solutions from design to tooling to material selection and manufacturing. Contact our specialized team and solve your problem now.
Seasky Medical is a one-stop solution for custom medical plastic injection molding and plastic medical devices. We provide high-quality custom service for your medical devices and consumables. If you need a professional medical equipment supplier, medical moulded products from us won’t let you down.
Medical device plastic injection molding is a crucial process that must be handled properly. As such, some considerations must be taken to ensure a successful production.
All medical grade materials for medical injection are available in Seaskymedical. Materials that have superior thermal and mechanical properties could be selected as per your need, biocompatibility would also be considered when choosing the medical materials.
Medical-grade plastic materials used in medical device injection molding are resistant to contaminants, making them safe for healthcare purposes.
The plastic material to be used must have the intrinsic properties that will help in actualizing the suitability of the molded products for the required application.
You may get more than simply a representative depiction of your medical component when you deal with expert medical plastic injection molding suppliers. We provide you the most versatility and ingenuity in your medical prototype design, choice of materials, pricing, and final product design, usage, and performance.
When an unwanted element gets caught in the molten material while the injection molding procedure, contamination ensues. However, Seskymedical medical plastic injection molding in the cleanroom leads to increased safety and sterilization of plastic medical parts.
Strength、chemical and heat resistance are considered when selecting medical plastics, we need to ensure our medical moulded products could withstand extrusion and sterilization via autoclave. Our medical plastics and technology guarantee the durability of products.
The melted material is forced into the preheated mold where the material solidifies. Temperature control units are used to preheat the mold and then to keep the mold at the temperature set point by circulating coolant (water or oil) through the mold.
With robust capabilities in injection molding, we, a ISO Certificated medical plastic injection molding producer, are capable of completing customized injection molded products in high volume and with tight tolerance. Also, our ISO 8 cleanroom can meet the strict requirements for product cleanliness in the medical plastic molding field. In addition, micro injection molding is also one of our specialties. We are able to manufacture the most micro medical injection molding parts for your need.
The coolant absorbs heat from the mold (which has absorbed heat from the hot plastic) and keeps the mold at proper temperature to solidify the plastic.
Different injectin molding services could be provided according to your medical moded products need. No matter medical overmolding or micro molding, we will provide suitable molding technology to match your custom products.
As one of the medical plastic injection molding manufacturers, We have been providing various quality medical injection molding solutions to the medical and pharmaceutical industry for many years. We specialize in Insert molding、overmolding、micro molding and others.
Our ISO 13485:2016 certified facility is one of the few in the world that has both class 100,000 cleanroom and advanced injection molding equipment, enabling us to manufacture a wide range of sterile and non-sterile equipment and medical consumables.
With the help of our advanced injection mold machines, we are able to manufacture thousands and millions of medical plastic products without any compromise of quality. Fewer materials and the reduced weight help our customers reduce a lot of costs.
Precision injection molding is a complex procedure that necessitates the use of precision molds and machines. It’s different from typical injection molding procedures. It provides design flexibility and precision with complicated designs, enhancing the value of our products for our consumers.
2171 Highway 175 • Richfield, Wisconsin 53076 262.628.0331 • 800.733.4204 • fax: 262.628.0332 Email
Seaskymedical is adept at injection mold in clean room for medical devices and consumables. Our class 7&8 cleanroom could reduce pollutants and dust particles so as to improve medical products quality and reliability. This is critical for firms who have high requirements for health and safety.
All medical grade materials for medical injection are available in Seaskymedical. Materials that have superior thermal and mechanical properties could be selected as per your need, biocompatibility would also be considered when choosing the medical materials.
Seasky Medical is one of the market leading manufacturers in medical device component, medical plastic injection molding components, and materials. Our medical plastic injection molding technology, medical molding machines, and medical grade plastics are some of the best in the country.
Seasky Medical serves you with medical injection molding solutions from design to tooling to material selection and manufacturing. Contact our specialized team and solve your problem now.
The plastic material selected and the end product of the injection molding process must meet the FDA standards for approval of safety to the health.
Our advanced medical injection molding facility can satisfy your exact specifications with our specialist medical plastics. We are also ISO 13485:2016 certified, which guarantees comprehensive quality management in the manufacturing of medical plastic products.
Your medical plastic parts design, molding method and application requirements would be considered when we custom your products, ensuring our customers receive a finished product that performs as required.
As one of medical plastic injection molding companies, we fulfill the medical industry’s rigorous demands and regulatory requirements. Our products process routinely quality checks and exceed our partners’ expectations. While quality qualifications are crucial, our outputs are what really matter.
Many plastics used in injection molding have outstanding properties like toughness and resistance to harsh environments, heat blunt force, and vibrations, making them to last long.
Medical micro injection molding solutions for finished medical devices and components are available from us. We evaluate and discuss specific factors that will contribute to the growth of your final injection molded part or packed finished medical equipment throughout our development phase.
When bulk medical plastic products are required, plastic injection molding is the best option. The nature of its manufacturing process makes it more cost-effective as less money will be spent when large volumes are produced.
We offer custom design services, device development facilities, and a variety of packaging solutions for your special plastic medical products needs, including cleanroom-rated assembly and packaging. This also includes Precision Color Blending、Cavity Sorting、Decoupled III Systematic Molding.
Working with a full-service injection molding production partner like us also gives you the printing of logo service to your part. You may also rely on us with high-quality parts for finished medical devices for maximum performance and you profit from a lower overall manufacturing cost.
Injection Molding increases the functionality of the equipment and the components. We also utilize medical-grade materials which also makes them sturdy. Advanced medical plastic injection molding could help manufacture more complex and functional medical plastic products.
Injection molding temperature controllers or temperature control units, are commonly used in the plastic injection molding industry. Injection molding is a manufacturing process in which parts or products are produced by injecting various plastic materials into molds. Pelletized, raw plastic material is fed through a hopper into a heated barrel with a reciprocating screw. Molds can be of a single cavity or multiple cavities. Depending on the size of the cavities and the dimension of the mold, more than one temperature control unit like Delta T Systems’ may be needed for precise temperature control.
Our items are made to accurate weight and length measurements, with little room for error. Reduced weight helps in easy handling and better endurance of the product, which means less raw materials but does not affect the quality of medical plastic products. You could get a large number of plastic medical parts at a competitive price.
Tight tolerance manufacturing is critical in the medical device industry, where millimeters or microns can make or break a component's performance. Our plastic injection molding facilities with specialized foreign injection equipment produce large quantities of components and devices with tight tolerance.
Our company has kept up with the growing demand for full medical device solutions by expanding our contract manufacturing capabilities. We offer a variety of medical plastic injection molding options for minor or complex medical components.
This is a compulsory requirement for any medical device. All medical injection molded components must be contaminant-resistant and able to be sterilized. This is to prevent the spread of diseases.
Seaskymedical Class 100,000/ISO Class 7& 8 clean room is equipped with the technologies and capabilities required to ensure our commitment to quality is never compromised. With a wide range of medical injection molding capabilities, we can accomplish the most demanding and rigorous requirements for medical device component molding.
We’re able to custom the size of equipment according to your requirements and demands. Our German and Japanese injection machines allow us to manufacture all sizes of medical products no matter how small and complex.
There is a long list of plastic materials that can be used in making medical products. However, this list is narrowed down by medical-grade standards.
Medical plastic injection molding is a relatively higher investment cost than general injection molding. This includes investment in cleanrooms, as well as investment in precision, thin-walled and micro injection molds and machinery. In addition, gantry cranes or hoists and specialized injection molding technicians also cost a lot. Leave your challenges to us – the professional medical plastic injection molding company.
The cleanliness of medical products directly affects the safety and health of users. Faced with the strict requirements of the medical industry, we use ISO 8 dust-free workshops for injection molding production to ensure product cleanliness and safety.
GETTING A QUOTE WITH LK-MOULD IS FREE AND SIMPLE.
FIND MORE OF OUR SERVICES:
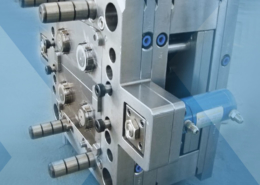
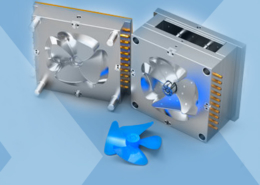
Plastic Molding

Rapid Prototyping
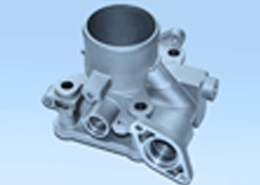
Pressure Die Casting
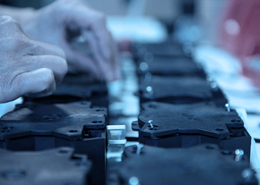
Parts Assembly
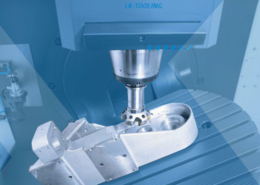