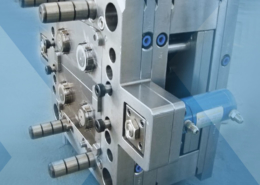
Plastic Injection Moulding | Afaridan Plastics | Perth Australia - large scale p
Author:gly Date: 2024-10-15
Content marketing encompasses blogs, eBooks, videos, and infographics, and contributes to a stronger online presence for your manufacturing brand when other digital marketing strategies like SEO and online ads work in tandem. Digital marketing ensures you stay connected with customers and continue getting seen by new prospects — and more manufacturers are investing in its technologies. Due to the in-person limitations of COVID-19, reports show that manufacturers are no longer able to avoid digital marketing’s reach and effectiveness and have adjusted their approach from dated tactics like print ads to generating new customers using their website, social media, and digital ads.
Injection molding produces many products standard in everyday households and industries. Injection-molded parts can be found in military, defense, and aerospace applications just to name a few. In 2018, medical equipment sourcing spiked as the healthcare industry boomed, driven by an aging population’s demographic wave requiring medical care. Then the COVID-19 pandemic accelerated the demand for medical devices and manufacturers turned to plastic injection molding to meet the demand for durable, lightweight, and malleable material.
See how D&M Plastics uses infographics throughout their website to simplify the complexities of plastic injection molding and engage B2B buyers looking for leading suppliers in that industry. B2B buyers like procurement managers research to familiarize themselves with new products or services. Rather than sifting through text-based information, a creative infographic presents all the data and stats buyers need in an engaging way.
Clean rooms sometimes use Ultra Low Penetration Air (ULPA) filters, which provide even higher filtration that can catch particles invisible to the naked eye.
Medical device manufacturing adheres to ISO 13485, a global quality management system standard. While it doesn’t classify clean rooms, It’s in place to safeguard the quality and safety of medical devices produced in clean room environments.
Copyright© 2024 Thomas Publishing Company. All Rights Reserved. See Terms and Conditions, Privacy Statement and California Do Not Track Notice. Thomas Register® and Thomas Regional® are part of Thomasnet.com. Thomasnet Is A Registered Trademark Of Thomas Publishing Company.
THY Precision understands the importance of clean room injection molding in delivering safe, sterile, and quality products for the medical, pharmaceutical, and biotechnology industries.
“About half of our new custom work comes from Thomasnet.com leads. We could not have competed for — and won — all the new business we have without our strategic Thomasnet.com program.”
Products are packaged in specialized containers or packaging materials to protect against contamination during storage and transportation.
Injection molding plays a significant role in the automotive industry too, which will encompass a bigger electric market in the next few years. Common components that use customized injection molding applications in the automotive industry include glove compartments, door handles, wheel trims, and many more.
High-Efficiency Particulate Air (HEPA) filters are essential in injection molding. They catch and remove 99.9% of microparticles from the environment.
It’s so effective that clean rooms are essentially classified based on the number of particles allowed per cubic meter of air.
“Our goal in acquiring other companies is to increase our support and capabilities for our customers across the country, so, in return, they will bring their manufacturing business back to the United States,” Plastic Molding Manufacturer (PMM) CEO George Danis told Plastics Today. PMM had deals of acquiring a plastic company with facilities across New England in 2020.
According to MarketWatch, the Plastic Injection Molding Sales Market is the most booming and promising sector of the industry. So to make sure you’re ahead of competitors, contact us for a free digital health check. Our industry experts have been connecting buyers and suppliers for more than 122 years.
Connect with the most active and qualified network of B2B buyers on the world's leading platform for product discovery and supplier selection.
The pharmaceutical industry takes cleanliness and hygiene to a microscopic level. Clean rooms help manufacturers create products that adhere to strict quality control standards and regulatory compliance.
Among these standards, ISO 8 is commonly used in medical device manufacturing. Learn more about these classifications in this article: What is an ISO 8 Cleanroom? Principles & Requirements
A Thomasnet.com Company Profile gets you in front of more than a million B2B buyers sourcing industrial services like plastic injection molding. Get Listed For Free.
In injection molding, a clean room provides a sterile space to melt plastic resins, inject them into molds, and cool them off. They aim to ensure that the final products are safe and effective. Below is the common industries that require cleanroom environments:
Companies who are certified ensure their customers consistently receive high-quality products and services and the benefits are two-fold because the requirements of certain certifications also benefit managers and employees. For example, because the ISO 9001 certification specifies the requirements for an effective quality management system, employees benefit from the improved processes and management garners the benefits of saved costs.
With over 40 years of experience and state-of-the-art facilities, including ISO Class 7 and 8 cleanrooms, we’re able to handle even the most demanding projects. Our commitment to quality and safety is also reflected in our ISO 13485:2016 and ISO 9001:2015 certifications.
In industries like healthcare, pharmaceuticals, and biotechnology, cleanliness is an absolute necessity. A single spec of dust can contaminate a life-saving drug or compromise a medical implant. That’s why clean room injection molding has become an indispensable part of manufacturing in these industries.
The resins are melted and injected into precision molds inside the clean room. Temperature, pressure, and injection speed, are controlled to achieve the desired product quality and consistency. Click here to know more details about how injection molding works.
ISO 14664-1 is the current international standard clean room classification system. It classifies clean rooms into ranges from ISO 1 (the cleanest) to ISO 9, each with a specific limit for particles in the environment.
For some industries, certifications are a legal or contractual requirement. Injection molding companies seeking to increase their sales and expand their market share of other industries can solidify their expertise with quality certifications, like:
How do you work? What’s the quality of your services and products? Which industries do you have expertise in? Content marketing can persuade potential partners and influence buyers at every stage of the buying cycle.
In recent decades, American companies offshored a huge portion of their injection molding, but today, many companies are weighing the benefits of reshoring versus offshoring, and there has been an upward trend of reshoring and demand for services in the plastics and molding services industry. Mergers and acquisitions in the industry are also contributing to growth.
Fs 209E is an older US federal standard that ISO standards have mostly replaced. Although some industries, like semiconductor manufacturing, still use this as a benchmark. Classifications range from Class 1 (the strictest) to Class 100,000 — each class also has a specific particle count.
Clean rooms are classified based on their level of cleanliness, which is determined by the number and size of particles allowed per cubic meter of air.
Clean rooms have specialized airflow systems to control the movement of air and keep the environment clean. There are two types of airflow:
With the help of clean room injection molding, medical manufacturers can safely provide quality-assured products to hospitals, clinics, and patients. This process ensures that medical devices are safe, ultimately improving patient care.
UNLOCK: See which companies are looking for your injection molding services with our free customer in-market buyer report.
Similarly, The Rodon Group optimized targeting for specific industries with videos to encourage engagement and diversify content. According to HubSpot, marketers who incorporate videos into their content strategies have seen 49% faster revenue growth than those who don’t.
When labeling a product or system as certified to an ISO standard, don't just say "ISO certified" or "ISO certification." Be clear and say "ISO 9001:2015 certified" or "ISO 9001:2015 certification" (for example). Showcase the PDF certifications and icons on your website and Thomasnet.com Company Profile so you can effectively target buyers in the industries sourcing certified suppliers.
Biotechnology workers know how important it is to stay clean. They often work with sensitive biological materials like cells, tissues, and microorganisms. Clean rooms help maintain a sterile environment and avoid contamination.
According to a DemandGen Report, 67% of B2B buyers rely more on content to research and make purchasing decisions than they did a year ago. That's why your website's content is crucial for lead generation to reach the right buyers and increase market share and profits.
The industry’s growth has an upward trajectory. Last month, RFI submissions on Thomasnet.com for plastics molding services were up 80% year-over-year. As U.S. companies find that they can manufacture injection molded products more profitably right here at home, how can these companies market their services to take advantage of the opportunities?
Clean rooms are highly controlled environments that minimize the risk of airborne particles getting into products or equipment. They prevent dust, dirt, and microbes from contaminating sensitive materials.
Inject molding in clean rooms has a strict operating procedure to ensure the product manufactured is safe and effective:
Products typically go through sterilization processes to remove remaining microorganisms so they are safe for medical or pharmaceutical use. Manufacturers commonly use ethylene oxide (EtO) sterilization and gamma irradiation.
Thomas Tip: Get ahead in the plastic injection molding industry with videos of your services. Thomas offers video production for free with the purchase of an advertising program.
Choosing the right clean room injection molding manufacturer makes all the difference in ensuring product safety and quality. Here are some key questions to help you choose:
Raw plastic resins are selected and prepared according to strict quality control standards. This often includes drying or pre-heating the resin so that they are easier to process.
Quality control tests, such as visual inspection, dimensional measurements, and functional testing, are performed to make sure the product works as intended.
GETTING A QUOTE WITH LK-MOULD IS FREE AND SIMPLE.
FIND MORE OF OUR SERVICES:
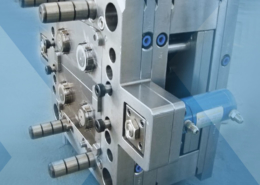
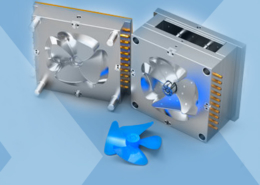
Plastic Molding

Rapid Prototyping
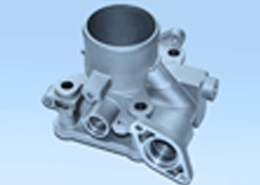
Pressure Die Casting
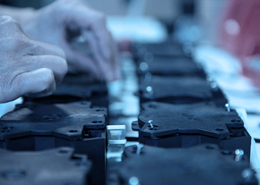
Parts Assembly
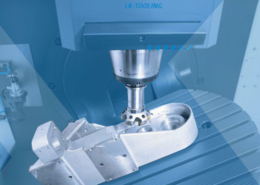