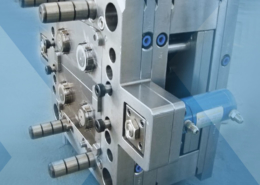
Plastic Injection Moulding - injection moulders
Author:gly Date: 2024-10-15
Both processes depend heavily on being able to control where, when, and how gas is introduced to the plastic as it cools in the tooling cavity. Adapting part design to the gas-assist injection molding process is crucial. This involves identifying where gas will be present on the part so gas zones can be isolated in the part and tool design. Modifying thickness of local areas of the part is often required to influence how the gas interacts with the part design.
In some cases gas will be turned on before the part cavity is full of resin to assist in the filling phase of the process in addition to packing the part out. In other applications the gas is turned on after the part is full of resin while a downstream relief gate is opened too allow the gas to push resin into an overspill pocket as the gas channel is formed. Overspills are removed and can be utilized as regrind.
In the medical field, we often see metal combined with the plastic part. This is called insert molding and is a very common practice for injection molders to do. You see this all over the medical arena from needles to EKG hook up leads and more.
Once these new devices are produced, we assist our customers in transitioning the project into the production phase. Quality and customer satisfaction are our primary goals, and Aberdeen can work with both high and low quantity requirements with over 700 square feet of cleanroom injection molding space.
Internal gas, also known as structural web, is particularly useful for molding extreme thick sections in tube- or rod-shaped parts such as handles and foot pedals, as well as tray-like parts with thick perimeter sections by creating hollow channels in these features. External gas excels at reducing required press tonnage and improving part aesthetics and flatness on skins and panels.
A key advantage of this process to consider is its ability to pack out thick geometry that would result in sink marks with a traditional molding process. This allows for core side ribs and boss features to be designed thicker than traditional design rules typically allow. In turn, parts will undergo less differential shrinkage which is a primary factor in part distortion and warpage in the molding process.
The most common types of materials used in medical insert molding are thermoplastics. These are materials that can be heated up into a molten state and pushed through a barrel into a mold. These molds can simply be open and shut type designs, which are what you would expect for, say a simple product such as a cake mold. Or they can be very complex with moving side parts called slides. Of course, the simpler the mold the better for maintenance and longevity. However, complex parts will need these complex designs in order to produce the desired part.
For internal gas, boss pin and overspill locations are typically added to non-aesthetic areas of the part to facilitate gas entry and plastic evacuation. Moldflow simulation is often relied upon to understand the filling pattern of a part as this impacts when in the process gas can be turned on, in turn dictating proper zone isolation and/or channel development. Molders also need to be equipped with a supply of nitrogen and a gas control unit that programs the timing and pressure characteristics of the gas process.
By opening design and manufacturing options for numerous applications, gas assist molding expands upon the versatility of traditional plastic processing while benefiting from its proven repeatability in high-quality part production. Due to its availability, cost and inertness, Nitrogen is typically used for external and internal gas assist molding.
Prime examples were molding non-communicating passageways through a plastic manifold, molding critical tolerance pacemaker components, and even molding around glass formations without breaking or cracking. Our advanced injection molding equipment makes even the most difficult projects possible.
Sometimes the components need to be manufactured separately and then assembled. This is very common in many cases and this can be done by hand or robot.
Without gas-assist technology, many features could not be incorporated into part design because of economic, functional or tooling reasons. Thanks to the evolution of gas-assist injection molding technology there are several techniques to help customers achieve their desired results. Whether it is a part thick sections, such as handles, or a part with localized thick areas or other features, Mack is prepared to leverage its gas-assist expertise to bring your project to fruition.
In external gas-assist, nitrogen is introduced as a micro-thin layer on the non-aesthetic side of the part when the mold is filled with plastic but not fully packed out. The gas is held at a high pressure, pushing uncured molten plastic to the opposite side of the tool. This replaces the traditional holding phase of the injection molding process, packing the part evenly, and ultimately resulting in a clean, uniform appearance on the aesthetic side of the part.
Aberdeen’s primary goal is total customer satisfaction for even your most challenging projects. Our company culture is one of honor, respect and service with the highest degree of competence and professionalism that you will find anywhere.
While plastic designers are typically beholden to rib/wall ratios of 65% or less, external gas allows for this rule to be increased to 100% or more in some cases. A rib to wall ratio describes the thickness of a rib feature relative to the nominal wall it intersects with. Designing these features too thick is a common source of sink and rib readout in molded parts. Because the gassed side will have a wavy or “sinky” appearance, while the aesthetic side will have enhanced cosmetic attributes, external gas assist molding is the perfect option for parts that require high aesthetic quality but whose gassed side will be unseen in the final application.
In addition to enabling the creation of geometry that traditional molding could not produce, internal gas also can create lighter parts which can be crucial to product performance while remaining cost effective and reducing cycle time. Because press cycle times typically depend on the part thickness, the cavity created where internal gas assist has been utilized results in reduced cooling times.
The process is capable of making FDA approved medical devices that are both durable and reliable. This type of molding can also be used to make prototypes to send and get the much-needed FDA approval. Medical injection molding can be performed in a clean room and the components can be sterilized without harm as well. Let's take a look at injection molding.
Gas assist molding is a subset of plastic injection molding that expands on the capabilities of traditional design and processing limitations. By using nitrogen gas pressure to assist in packing out a part, molders can produce components that are functionally and cosmetically superior, especially when working with thick geometry.
Both types allow designers to create larger and more-complex parts while minimizing high tooling costs incurred with complicated hot-runner systems. In addition, the smaller presses and shorter cycle times provide part cost benefits.
We provide assistance throughout each stage of your program, from design recommendation through mold tooling fabrication, prototyping, first article approval, process validation, full scale production medical molding, and transfer of turnkey system to customer facilities if requested.
Medical injection molding is a core technology of Aberdeen Technologies and represents a cutting edge solution to the manufacturing needs of healthcare companies who produce medical molded devices. As an insert molding manufacturer, we provide assistance to device manufacturers who approach us with new product concepts and ask us to mold parts for clinical trials and marketing evaluations.
Internal gas-assist is used specifically to mold parts with very thick sections. The process has many similarities to external gas assist, however, here the gas is introduced inside the part geometry. The gas displaces a portion of the molten plastic inside thick geometry and then performs the packing forcing the polymer melt against the external walls to create a hollow channel through the thick region and a packed-out appearance.
However, there are other types of plastics called thermosets that also can be used for injection molding, but the process is far different. These materials are most likely not going to be used for medical molding as they cannot be recycled as easily as the thermoplastic materials. Because of this, you don't see thermosets used as often as you do thermoplastics. A good example of a thermoset is your car tires. This is where they cannot be melted down and reshaped into something.
Medical injection molding is a manufacturing process that produces plastic medical devices and components. It involves melting plastic resin pellets and injecting the molten material into a mold to create a specific shape. This process allows for precise control over the product's size and shape and is subject to strict quality and regulatory standards.
Injection molding is a very common way to form plastic parts and components. Depending on the material, the parts can be very strict with their tolerances as well as easy to process. Injection molding is one of the most common types of forming plastics. It is used in a variety of industries and not just for medical injection molding. In fact, you probably have a wide variety of injection molded parts all around you and simply don't know it. Your basic pens, your keyboard, and even your phone have injection molded components in them.
After the gassing phase, the pressure is released either by gas recycling or by releasing the gas into the atmosphere. The part can be ejected when ambient pressure is reached and the plastic is sufficiently cooled. By contrast, traditional molding requires extremely high pressures to fully pack a part due to pressure loss from gate to end of fill. By evenly distributing the nitrogen gas pressure, external gas assist molding replaces some of that work load. This reduces internal stress and warping resulting in better overall part flatness, thus improving part quality. Additionally, it reduces the clamp tonnage needed to create a part, ultimately leading to lower part costs.
GETTING A QUOTE WITH LK-MOULD IS FREE AND SIMPLE.
FIND MORE OF OUR SERVICES:
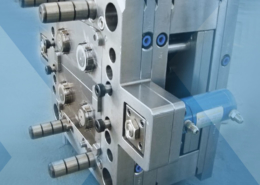
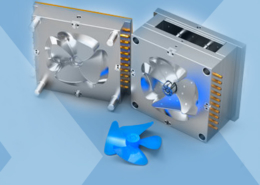
Plastic Molding

Rapid Prototyping
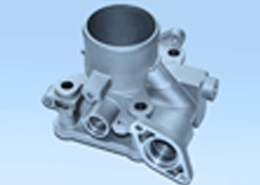
Pressure Die Casting
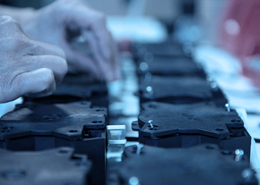
Parts Assembly
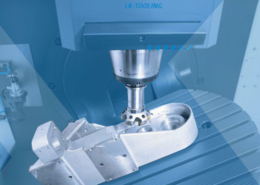