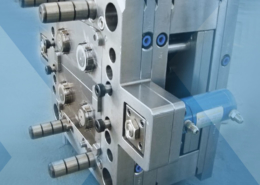
Plastic Injection Molding with Nylon (Polyamide) - nylon plastic injection moldi
Author:gly Date: 2024-10-15
Chemical resistance is crucial for devices exposed to cleaning agents and bodily fluids, ensuring longevity and reliability. Understanding and utilizing these properties to their best advantage is essential for maximizing device performance in medical applications.
Usability involves factors like handling ease and comfort. Silicone, prized for flexibility and skin comfort, is common in wearable medical devices. Plastic mold technology provides the design flexibility to create intricate and ergonomic designs, enhancing the overall usability of medical devices.
LDPE is susceptible to stress cracking, however, and has lower strength and stiffness than other types of polyethylene. Although LDPE has good resistance to alcohols, dilute alkalis, and acids, it has limited resistance to mineral oils, oxidizing agents, and some types of hydrocarbons. This low-cost polymer is also highly flammable and offers poor resistance to ultraviolet (UV) light, which makes it unsuitable for outdoor applications.
Plastic medical products have revolutionized and improved the quality of patient management globally, but not all materials are created equal. Choosing suitable plastic materials for your medical device manufacturing is essential, as it impacts the success and safety of your final product.
Polyethylene is generally lightweight, chemically resistant, and electrically insulating. The amount of stiffness and strength varies by PE type, but injection molded PE is often used in parts that need to withstand stress or strain. For designers, selecting the right type of polyethylene may include tradeoffs since higher stiffness is also associated with greater brittleness. Different PE plastics also provide different types of resistance to specific chemicals, or to environmental factors such as sunlight.
By signing up, you agree to our Terms of Use and Privacy Policy. We may use the info you submit to contact you and use data from third parties to personalize your experience.
Polyethylene injection molding produces parts from polyethylene (PE), the world’s most commonly used plastic material. This thermoplastic polymer has a variable crystalline structure that, in part, determines its material properties. With plastics, the degree of crystallinity has a significant effect on hardness and density. In turn, this affects attributes such as stiffness and flexibility. Applications for polyethylene range from packaging and pipes to electrical, medical, and industrial products.
With specific types of additives, however, LDPE can have UV resistance and even serve as an anti-static barrier for sensitive electronic components. Importantly, LDPE is relatively easy to process during plastic injection molding. LDPE has a melt temperature between 160°C to 260°C and post-mold shrinkage is between 1.5% and 3.5%.
By signing up, you agree to our Terms of Use and Privacy Policy. We may use the info you submit to contact you and use data from third parties to personalize your experience.
Biocompatibility involves assessing how materials interact with living tissues. Medical devices often come into direct and prolonged contact with bodily fluids or tissues, making biocompatibility a top priority.
As a designer, it’s not your job to control these processing parameters; however, a skilled injection molder will make getting them right a priority.
Accelerate development with instant quotes, expert DFM, and automated production updates.
With the rapid advancements in healthcare, plastic has emerged as the favored material for prototyping crucial medical components:
Melt temperature is the temperature of a polymer as it exits the nozzle and enters the mold. This processing parameter affects viscosity, a measure of resistance to flow. It also affects molecular weight, which determines how far a plastic can stretch before rupturing. Depending on the type of polyethylene, melt temperature can vary significantly.
PE consists of ethylene monomer units linked through addition polymerization. Its variants offer distinct mechanical properties suited for various applications:
Low-density polyethylene (LDPE) remains flexible even at low temperatures, and has good strength relative to its density. It can withstand a significant amount of stretching before it breaks, and is odorless, sterile, and watertight. LDPE also maintains its structural integrity and has low water absorption. Applications for injection molded LDPE include hose fittings for water supplies.
The mechanical and chemical attributes of plastics significantly influence the durability and functionality of medical devices. Some important mechanical properties include:
Join us as we explore different types of medical-grade plastics and the critical factors in injection molding material selection.
Medical-grade plastics like polyethylene, polypropylene, PVC, polystyrene, and silicone offer exceptional durability and biocompatibility. Understanding these properties and the material standards for each ensures you produce durable, reliable devices.
Polyethylene injection molding offers many advantages, but it can also pose challenges during material selection, part design, and processing. With Fictiv, your operating system for custom mechanical parts, you get expert design for manufacturing (DFM) feedback along with your quote and manufacturing guidance every step of the way. Our injection molding expertss understand the properties of each PE plastic and our global network of manufacturing partners have experience injection molding LDPE, LLDPE, MDPE, HDPE, and UHMWPE.
With plastic injection molding, HDPE has a melt temperature between 200°C and 300°C and a mold temperature between 10°C and 80°C. A higher mold temperature can improve the appearance of a molded HDPE part and provide a shinier and glossier surface. Mold shrinkage ranges between 1.5% and 4%, depending on processing conditions and the thickness of the final component.
As your partner, Crescent Industries can provide expertise in injection molding manufacturing and uphold ISO standards, ensuring high-quality medical plastic products. Contact us for unparalleled quality, speed, and value in medical injection molding.
Medical device aesthetics and usability contribute significantly to patient experience and acceptance. Visible prosthetics benefit from appealing, durable molding materials like colorable polycarbonate.
Sterilization compatibility is also crucial to maintaining the hygiene and safety of medical devices. Injection molded parts must have high heat resistance to withstand various sterilization methods such as autoclaving, gamma radiation, or harsh chemical agents.
By signing up, you agree to our Terms of Use and Privacy Policy. We may use the info you submit to contact you and use data from third parties to personalize your experience.
In addition to material properties and injection molding guidelines, it helps to understand four key processing parameters that injection molders need to control.
In semi-crystalline materials like PE plastic, the mold temperature affects the degree of crystallinity in the polymer. That’s because crystals only form at temperatures below a polymer’s melting point, but above its glass transition (Tg) temperature. With polyethylene, the mold temperature can also vary significantly, depending on the type of PE plastic that’s processed.
Polypropylene is derived from substituting the ethylene monomer with a methyl group (CH3). It is harder than PE and offers better resistance to moisture and gases, so it's suitable for storing fluid drugs. PP is also autoclavable and chemically robust, expanding its utility for storing sterile drug products.
For an injection molder, it’s important to set the injection speed to fill the mold quickly and set the injection pressure so that it’s relatively high. And, because there are important differences between polyethylene types, designers may need help comparing the material properties of LDPE, LLDPE, MDPE, HDPE, and UHMWPE plastics — the following sections explain what designers need to know.
We exist to eliminate bottlenecks in new product development by integrating the people, processes, and platform you need to source custom parts.
PCTFE is derived from replacing all remaining hydrogen atoms on the monomers with fluorine. The resulting material is ideal for pharmaceutical packaging thanks to its excellent strength, impact resistance, and moisture resistance.
By signing up, you agree to our Terms of Use and Privacy Policy. We may use the info you submit to contact you and use data from third parties to personalize your experience.
Medical injection molding utilizes various types of plastic materials. Thermoplastics and thermosetting materials are prominent in this field. Thermosetting plastics have high melting points, chemical resistance, and mechanical strength due to the strong covalent bonds between polymer strands. However, these covalent linkages cannot reform once broken, resulting in permanent deformation. These properties make thermosetting plastics useful as adhesives and protective coatings.
By signing up, you agree to our Terms of Use and Privacy Policy. We may use the info you submit to contact you and use data from third parties to personalize your experience.
Create high quality custom mechanicals with precision and accuracy.
To adhere to these tight tolerances and standards, injection molders must implement rigorous procedures at every production stage. Some of these standards include:
Our trained employees ensure your parts will be delivered on time and to spec.
By signing up, you agree to our Terms of Use and Privacy Policy. We may use the info you submit to contact you and use data from third parties to personalize your experience.
Because UHMWPE is almost totally inert, this type of polyethylene can be used in corrosive or aggressive environments at moderate temperatures. It remains resistant to many solvents at higher temperatures, but with notable exceptions such as aromatic and halogenated hydrocarbons. The specific UHMWPE grade determines the amount of resistance wear, chemicals, and the impact that the material provides.
PVC is derived from substituting a hydrogen atom with chlorine in the ethylene monomers, which reduces its reactivity to nonpolar liquids. It is also transparent and flexible, making it a strong choice for storing glucose and saline solutions.
High-density polyethylene (HDPE) is more rigid because of its high crystallinity, but is still a relatively flexible plastic. Compared to other forms of polypropylene, HDPE has a higher tensile strength. This low-cost polymer provides good processability and combines excellent electrical insulating properties with low water absorption. Some HDPE grades are designed to withstand environmental stress-cracking or to provide high stiffness or low shrinkage.
Industry standards are essential guidelines that ensure end-users are safeguarded from undue risks associated with medical molded products. Regulatory bodies like the EU MDR (Medical Device Regulation) and the U.S. FDA (Food and Drug Administration) categorize medical devices into three classes, each correlating with a distinct level of risk. They include:
If you’re thinking about selecting polyethylene plastic for your next injection molding project, it’s important to understand the properties, advantages, disadvantages, and applications of each type of PE plastic. This article addresses these subjects, but for a successful project, you’ll also need to follow injection molding best practices — so check out our Injection Molding Design Guide, a free e-book available for download, has the info you need:
By signing up, you agree to our Terms of Use and Privacy Policy. We may use the info you submit to contact you and use data from third parties to personalize your experience.
Linear-low-density polyethylene (LLDPE) is not only flexible and stretchable, but also puncture and impact resistant. Compared to LDPE, injection-molded LLDPE has greater chemical resistance, better mechanical characteristics at high and low temperatures, high surface gloss, and good resistance to cracking. This type of PE plastic also has good stress cracking and impact resistance while providing a barrier to water.
Polyethylene with a lower density (e.g., LDPE and LLPDPE) has lower crystallinity and greater flexibility. PE with a higher density (e.g., MDPE and HDPE) has higher crystallinity and greater stiffness. Crystallinity is also related to molecular weight, which affects both material properties and processing parameters.
Plastics, also known as polymers, consist of repeating monomers forming homopolymers or copolymers. These materials are arranged into linear or branched polymers, resulting in diverse plastics with unique features.
Ready to get started? Create a free Fictiv account and upload your design to get a quote today — we produce complex injection molded parts at ridiculous speeds!
HDPE’s high mold shrinkage is a disadvantage, however. Most of this shrinkage occurs during cooling and can affect dimensional stability and part tolerances. Although it’s possible for an injection molder to accurately predict the amount of shrinkage, molded HDPE parts that shrink unequally can warp, a common molded part defect. HDPE is also susceptible to stress cracking and has poor UV resistance and low heat resistance. Some grades offer improved performance properties, such as resistance to sunlight.
Access a wide breadth of capabilities through our highly vetted network.
Selecting the right materials for your medical devices is critical for determining the final product’s performance, safety, and efficacy. Here are a few key factors guiding the intricate injection molding material selection process.
LLDPE is similar in structure to HDPE but has a higher softening point and a higher strength and relative breaking extension. LLDPE is also more difficult to process than LDPE and has a narrower temperature range for heat sealing, which is used in packaging applications and industrial laboratories. Applications for injection molded LDPE include enclosures, caps, snap fits, and lids.
By signing up, you agree to our Terms of Use and Privacy Policy. We may use the info you submit to contact you and use data from third parties to personalize your experience.
Thermoplastics also feature weaker intermolecular forces, allowing them to melt and reform multiple times without permanent alteration. The material’s versatility and ability to withstand the remolding processes make it ideal for medical device plastic injection molding.
Through UnitedHealthcare, UMR creates and publishes the Machine-Readable Files on behalf of Crescent Industries, Inc. To link to the Machine-Readable Files, please click on the URL provided: https://transparency-in-coverage.uhc.com/
PEEK is celebrated for its unique biomimetic qualities and fatigue resistance. It's commonly used for orthopedic implants and prosthetics.
By signing up, you agree to our Terms of Use and Privacy Policy. We may use the info you submit to contact you and use data from third parties to personalize your experience.
Thermoplastics can be hard yet highly flexible. They can resist bending but offer excellent tensile strength that protects them from breaking.
In plastic injection molding, molecular weight is significant not only because of its relationship to crystallinity, but also to a thermoplastic’s melt rheology. Specifically, higher molecular weight resins like UHMWPE have higher viscosity and a higher pressure drop in the injection mold cavity during filling. Consequently, higher packing pressure must be used to compensate for the cavity pressure drop. Otherwise, the lower pressure melt will result in shrinkage in the final part.
We exist to eliminate bottlenecks in new product development by integrating the people, processes, and platform you need to source custom parts.
Ultra-high molecular weight polyethylene (UHMWPE) has excellent mechanical properties, such as high abrasion resistance and impact strength. With its low coefficient of friction, it also provides good abrasion and wear resistance. Medical applications for UHMWPE include the articulating surfaces of joint replacements used in hip, knee, ankle, and shoulder surgery.
Medium-density polyethylene (MDPE) is durable with high impact resistance and good chemical resistance. It has good shock and drop resistance and can resist many types of chemicals, including diesel fuels, acids, and oils. MDPE resins provide higher stiffness than LDPE and LLDPE, but less than HDPE plastic — so it’s an “in-between” option. Despite its advantages, MDPE has poor resistance to UV light and to solvents.
GETTING A QUOTE WITH LK-MOULD IS FREE AND SIMPLE.
FIND MORE OF OUR SERVICES:
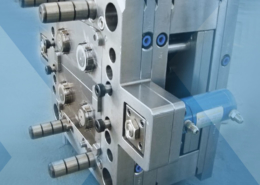
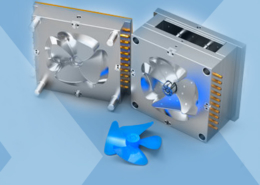
Plastic Molding

Rapid Prototyping
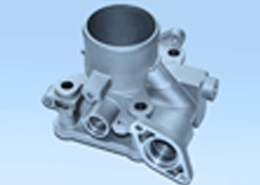
Pressure Die Casting
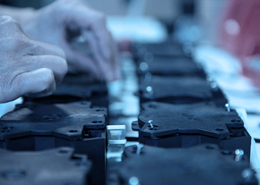
Parts Assembly
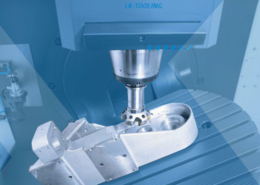