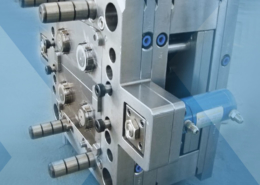
Plastic Injection Molding Services | ABS, PC, PMMA Parts - plastic injection mou
Author:gly Date: 2024-10-15
Senior Product Engineer For Plastic Injection Molding Products Focus on Product Design Optimization and Price Evaluation at zetarmold.com
Mold manufacturing and precision manufacturing are both highly specialized fields that require a great deal of skill and expertise. Mold manufacturing involves the creation of molds for various types of products, such as plastic parts or metal castings. Precision manufacturing, on the other hand, involves the production of highly precise and accurate components or products, often using advanced machinery and techniques. #mold#mokd manufacturing#hashtag#Injection Moldinghashtag #ManufacturingTech hashtag#ManufacturingExcellence hashtag #QualityMolds hashtag#plasticmold hashtag#plasticmould hashtag #mold hashtag#mould hashtag#injectionmold hashtag #injectionmould hashtag#moldmaking hashtag#moldsupplier hashtag#moldmanufacturing hashtag#moldmanufacturer hashtag #moldmaker hashtag#moldsupply hashtag#moldfactory hashtag #moldinspection hashtag#plastictooling hashtag#tooling hashtag #toolmaker hashtag#toolmaking hashtag#toolingsolutions hashtag #toolroom
In the summer of 2018 my partner Paul and myself put the plans in place to launch Integrity Injection Moldings Inc. in Pulaski Tennessee. This injection molding operation has been up and running since summer of 2019, we have seen many challenges with strikes and covid but managed to pull through these challenging times and even expand the operation in 2021. I have enjoyed working with a fine team over the years and owe the success to every individual that I have had the pleasure to work with at IIM. Today I happy to announce that as of April 9th we have completed the sale of this business to Century Mold to carry this successful operation forward. I wish Ron Ricotta and the entire team at Century all of the success into the future. https://lnkd.in/gAn_qU7w)
A Behind-the-Scenes Look at Injection Molding Manufacturing Website: https://zetarmold.com https://zetarindustry.com Email: info@zetarmold.com Whatsapp: +8613681808140 Injection molding manufacturing is a fascinating process that involves the production of a wide range of plastic products. This method utilizes molten material that is injected into a mold, where it cools and solidifies to form the desired shape. The versatility of injection molding allows for the creation of intricate designs and complex geometries, making it a popular choice for industries such as automotive, medical, and consumer goods. One key aspect of injection molding is the selection of materials. Different types of plastics have varying properties, such as strength, flexibility, and heat resistance. Manufacturers must carefully choose the right material for each product to ensure optimal performance and durability. For example, high-impact polystyrene is often used for packaging materials due to its strength and affordability, while polycarbonate is preferred for products that require transparency and impact resistance, like eyewear and medical devices. Another important consideration in injection molding is the design of the mold itself. The mold must be precisely engineered to create the desired shape and dimensions of the final product. Complex molds may include multiple cavities and intricate features, requiring advanced tooling and machinery. Additionally, factors such as cooling time, pressure, and injection speed must be carefully controlled to ensure consistent quality across production runs. In terms of efficiency, injection molding offers significant advantages over other manufacturing processes. The ability to produce large quantities of parts quickly and cost-effectively makes it an ideal solution for mass production. Additionally, the high level of automation in injection molding reduces the need for manual labor, resulting in consistent output and lower labor costs. Overall, injection molding manufacturing is a complex and versatile process that plays a crucial role in the production of a wide range of products. By understanding the intricacies of material selection, mold design, and process optimization, manufacturers can achieve high-quality results and meet the demands of today's competitive market. #injectionmolding #injectionmold #zetarmold #injectionmoulding #plasticinjection #plasticmold
Plastic parts are needed everywhere. Injection molding is the most popularly manufacturing method for producing these plastic parts. The process is a quick, economical way to mass produce a number of parts, ranging from high-precision engineering components to cosmetic product enclosures.
The global Low Pressure Injection Molding Machine market was valued at US$ 2836 million in 2023 and is anticipated to reach US$ 3949.4 million by 2030 witnessing a CAGR of 4.9% during the forecast period 20242030. #LowPressureInjectionMolding #InjectionMoldingMachines #GlobalMarket #AutomotiveIndustry #PlasticsIndustry #HomeApplianceIndustry #Manufacturing #IndustrialMachinery #MarketGrowth #SustainableManufacturing
Use a uniform or constant wall thickness throughout the part (if possible) and avoid overly thick walls to prevent parts from warping or sinking. Designing wall thickness can be tricky and differ depending on material choice. Generally, staying within a 1.2–3.0mm thickness is safe for most materials.
There are several factors that may affect the quality of the final part and the repeatability of the process. To take full take advantage of the process, it is important that your design follows a set of design guidelines. In this article, we cover the considerations of the injection moulding process, best design practices, and design tips to keep costs to a minimum.
For best results, avoid adding threads directly on your injection moulded part. Threaded inserts can be overmoulded into the part.
To avoid flaws on injection moulded parts, avoid sharp corners and round all edges. When designing internal edges, experts recommend using a radius of at least 0.5 times the wall thickness.
Use ribs for strength. Injection moulded parts with poorly designed ribs are most prone to sinking. Rib thickness should be equal to 0.5 times the nominal wall thickness, and the rib height should be limited to less than three times its thickness.
How Injection Molding Products Are Made: Step-by-Step Guide Website: https://zetarmold.com https://zetarindustry.com Email: info@zetarmold.com Whatsapp: +8613681808140 Injection molding is a popular manufacturing process used to create a wide range of products. It involves the melting of plastic materials and injecting them into a mold cavity, where they cool and solidify to form the desired shape. This method is commonly used in the production of toys, automotive parts, packaging materials, and many other items. The process of injection molding typically involves several steps. First, the mold is designed and created based on the specifications of the product being produced. The mold is then clamped shut, and the plastic material is injected into the cavity under high pressure. Once the material has cooled and solidified, the mold is opened, and the newly formed product is ejected. One of the key advantages of injection molding is its ability to produce large quantities of products quickly and efficiently. This makes it a cost-effective option for mass production. Additionally, injection molding allows for complex shapes and designs to be easily replicated with high precision. Overall, injection molding is a versatile and reliable manufacturing process that is used across various industries to create a wide range of products. Its efficiency, precision, and cost-effectiveness make it a popular choice for manufacturers around the world. #injectionmolding #injectionmold #zetarmold #injectionmoulding #plasticinjection #plasticmold
Production and sales of various molds, supporting customization #machining #mould #moldmaker #injectionmolding #siliconemold #moldmaking #plasticinjectionmold #shaped #plasticmold #injectionmold #molddesign #moldmanufacturing
Parts with vertical walls (and no draft angle) are most prone to drag marks. A minimum draft angle of 2° is recommended. A good rule of thumb is to increase the draft angle by one degree for every 25 mm. For example, add a draft angle of 3 degrees to a feature that is 75 mm tall.
Rapid injection moulding is a low-to-mid volume plastic part production process. After the part’s design is finished, a mould is created and machined with precision to form the part’s features. The mould is installed into an injection mould press, and molten plastic is injected into the mould tool under pressure. The part is then cooled, ejected, and the process repeats.
When using injection moulding, you have to be prepared to bear the high initial investment associated with making the hard tools. While it is a given that tooling will be costly, there are several ways you can optimize your injection mould design to save on costs:
Because an injection molded part is essentially the inverse of its machined metal tooling, the rules on engraving/embossing are reversed. For injection moulding, choose embossed over engraved text, as it’s easier to CNC machine such detail into the mould tool. We recommend a minimum height of 0.5mm to ensure readability. Use a font with uniform thickness and a minimum font size of 20 points for better results.
Senior Product Engineer For Plastic Injection Molding Products Focus on Product Design Optimization and Price Evaluation at zetarmold.com
Plastic parts are needed everywhere. Injection molding is the most popularly manufacturing method for producing these plastic parts. The process is a quick, economical way to mass produce a number of parts, ranging from high-precision engineering components to cosmetic product enclosures.There are several factors that may affect the quality of the final part and the repeatability of the process. To take full take advantage of the process, it is important that your design follows a set of design guidelines. In this article, we cover the considerations of the injection moulding process, best design practices, and design tips to keep costs to a minimum. Injection Moulding ProcessRapid injection moulding is a low-to-mid volume plastic part production process. After the part’s design is finished, a mould is created and machined with precision to form the part’s features. The mould is installed into an injection mould press, and molten plastic is injected into the mould tool under pressure. The part is then cooled, ejected, and the process repeats. Injection Moulding Process ConsiderationsWarping: When certain sections cool and shrink at different rates in different directions, it can result in permanently bents in parts due to internal stresses.Sink Marks: When a section shrinks faster on the outside than on the inside, it can cause the material to collapse in on itself, resulting in sink marks.Drag Marks: When the plastic is injected into the mould, it flow along the walls of the mould cavity. The plastic then cools and solidifies. During ejection, the walls of the part will slide and scrape against the mould, which can result to drag marks. Injection Moulding Design GuidelinesWall ThicknessUse a uniform or constant wall thickness throughout the part (if possible) and avoid overly thick walls to prevent parts from warping or sinking. Designing wall thickness can be tricky and differ depending on material choice. Generally, staying within a 1.2–3.0mm thickness is safe for most materials. Recommended wall thickness for common resins available at HLH Rapid:Common materialsRecommended wall thickness (mm)ABS1.2 – 3.5Acrylic (PMMA)0.7 – 3.8PC/ABS1.2 – 3.5Polycarbonate (PC)1.0 – 4.0PEEK1.0 – 3.0Polyethylene (PE)0.8 – 3.0POM0.8 – 3.0Polypropylene (PP)0.8 – 3.8Nylon (PA)0.8 – 2.9 RibsUse ribs for strength. Injection moulded parts with poorly designed ribs are most prone to sinking. Rib thickness should be equal to 0.5 times the nominal wall thickness, and the rib height should be limited to less than three times its thickness. Draft AnglesParts with vertical walls (and no draft angle) are most prone to drag marks. A minimum draft angle of 2° is recommended. A good rule of thumb is to increase the draft angle by one degree for every 25 mm. For example, add a draft angle of 3 degrees to a feature that is 75 mm tall. Threads and BossesFor best results, avoid adding threads directly on your injection moulded part. Threaded inserts can be overmoulded into the part. CornersTo avoid flaws on injection moulded parts, avoid sharp corners and round all edges. When designing internal edges, experts recommend using a radius of at least 0.5 times the wall thickness. Text and LogosBecause an injection molded part is essentially the inverse of its machined metal tooling, the rules on engraving/embossing are reversed. For injection moulding, choose embossed over engraved text, as it’s easier to CNC machine such detail into the mould tool. We recommend a minimum height of 0.5mm to ensure readability. Use a font with uniform thickness and a minimum font size of 20 points for better results. Summary of Best Design Practices Walls ThicknessStay within 1.2 – 3.0mmRib ThicknessNo more than 0.5x of wall thicknessRib HeightNo more than 3x of rib thicknessDraft AngleMinimum of 2°Internal EdgesAt least 0.5x of wall thicknessEmbossed DetailsMinimum of 0.5mm Cost Reduction TipsWhen using injection moulding, you have to be prepared to bear the high initial investment associated with making the hard tools. While it is a given that tooling will be costly, there are several ways you can optimize your injection mould design to save on costs: Eliminate Undercuts: Avoid undercuts where possible, as they’ll add to the complexity and cost of the tool.Choose Embossed Over Engraved: It’s easier to CNC machine text into the mould tool, as it involves the removal of less material which overall translates to less cost.Simplify As Much As Possible: Unless it adds value to the function or quality of your design, avoid overly complex features, as they often drive costs up unnecessarily.
Injection Molding vs. Casting: A Comprehensive Comparison #injectionmolding #casting #diecasting #cnc #CNCMachining #plasticinjectionmolding #manufacturing #plasticmanufacturing #djmolding https://lnkd.in/g4-Rzn7W
Get in touch to discuss your project's needs: leyla@hlhprototypes.com Considering both injection moulding and vacuum casting but not sure which is best for your project? Read our blog to find out: https://lnkd.in/eSSdxfgV Choosing the best manufacturing technique for your project is vital to it's success
GETTING A QUOTE WITH LK-MOULD IS FREE AND SIMPLE.
FIND MORE OF OUR SERVICES:
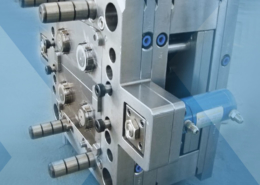
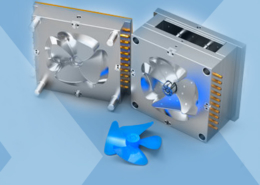
Plastic Molding

Rapid Prototyping
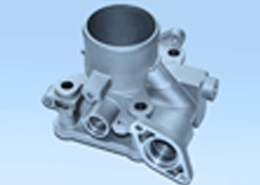
Pressure Die Casting
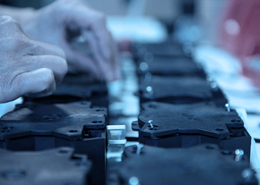
Parts Assembly
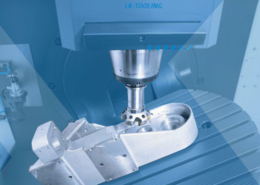