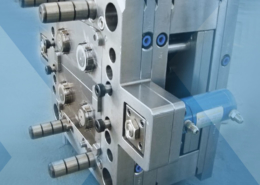
Plastic Injection Molding Service for Medical Devices - medical injection moldin
Author:gly Date: 2024-10-15
8. It’s essential to consider whether the flow of plastic during the second injection might disturb the already molded product from the first injection, causing deformation. If this is a possibility, remedial measures should be taken.
Dual-color molds typically consist of two parts. One half is fixed on the stationary platen of the dual-color injection molding machine, which is the side with the injection gate. The other half is mounted on the rotating platen, which is the side from which the mold ejects. Both molds’ rear cavities are usually identical, while the front ones differ. After the first material is injected into the first mold, the machine’s stationary and moving molds open. The rotating platen, carrying the rear parts of both molds, rotates 180 degrees. At this point, the semi-finished product from the first mold isn’t ejected. Instead, the molds close again, and the second material is injected. After cooling, the molds open, and the finished product from the first mold’s moving mold is ejected. This cycle produces one semi-finished and one finished product each time.
Within the intricate landscape of the plastic injection molding industry, the process of injection molding emerges as a pivotal methodology, indispensable for the fabrication of an extensive gamut of products characterized by their meticulousness and efficacy. As we navigate through the year 2024, the imperative of identifying a proficient manufacturing facility specializing in injection molding has escalated, attributed to the evolving intricacies inherent in product development designs and material specifications. This guide aims to scrutinize prominent injection molding companies, each distinguished by their commitment to innovation, excellence, and customer service in this niche sector.
10. In 99% of cases, the hard plastic part of the product is molded first, followed by the soft plastic part, primarily because soft plastic is more prone to deformation.
4. The sprue of a three-plate mold should ideally be designed for automatic demolding. Special attention should be paid to ensure the reliable demolding action of the soft plastic sprue.
UBE Machinery, a distinguished subsidiary of the UBE Industries Group, has consistently been at the forefront of the injection molding industry since its establishment in 1947. Operating from its base in Japan, UBE Machinery excels in the fabrication of large-scale injection molding machines, specifically engineered for the automotive and industrial sectors. These machines are highly acclaimed for their robust construction, exceptional precision, and adept capability in managing intricate molding operations, thereby positioning UBE as a supplier of choice for manufacturers worldwide.
The seal position refers to the junction or boundary between hard and soft plastics. A good design avoids a “feathered” appearance (i.e., the seal position shouldn’t gradually thin out), as overly thin edges can lead to poor adhesion and warping. Ideally, the design at the seal position should have a distinct step or recess to ensure consistent wall thickness. In some products, especially those with long flow paths or areas prone to wear, mechanical connections can be designed between the soft and hard plastics, ensuring a strong bond between the two materials.
Through the passage of time, ACO Mold has become emblematic of dependability and superlative quality, proffering an all-encompassing suite of services that span the entire spectrum of a mold’s lifecycle—from the genesis of the concept and design to the intricacies of prototyping and voluminous production. Their unwavering dedication to fulfilling client requisites is manifest in their adaptable project management paradigms, meticulously fashioned to accommodate the distinct demands and schedules of each patron. This client-oriented ethos, amalgamated with their profound technical acumen, positions ACO Mold as a preeminent collaborator in the international injection molding domain, specializing in main products that involve insert molding and injection mold design, facilitated by injection molders and programmers adept in harnessing advanced technology for manufacture.
What distinguishes ENGEL is their holistic approach to solution provision. By intricately integrating advanced process technology with state-of-the-art automation, they engineer systems that not only optimize production workflows but also significantly enhance the quality of the end product and maximize operational efficiency. This comprehensive suite of services, fortified by ENGEL’s unwavering commitment to perpetual innovation, firmly positions them as a cornerstone entity in the progressive trajectory of the plastic injection molding industry. ENGEL’s expertise in CNC machining, their prowess in crafting high quality plastic injection products, and their capacity to produce prototypes that meet the stringent demands of the industry, further consolidate their status among the elite plastic injection molding companies.
Taking TPE overmolding as an example, given the high cost of TPE material, designers must consider cost reduction during product design by using a thinner TPE wall. The tactile feel of TPE is directly related to its wall thickness and hardness. When the TPE thickness is less than 1.5mm, the softness or hardness is primarily influenced by the hardness of the underlying hard plastic. Reducing the thickness of TPE can severely affect its bonding strength with the hard plastic, mainly because an overly thin TPE cools too quickly in the mold, leading to reduced adhesion strength.
Multi-shot injection molding, also known as multi-color injection molding, refers to the process where two or more colors or different materials are molded using a mold with one or more channels. Historically, dual-color injection molding was the pioneer in this field. A common example many of us interact with daily is the toothbrush. The handle of most toothbrushes is produced using dual-color injection molding, typically combining PP (hard plastic) with TPE (soft plastic). TPE is chosen because of its excellent compatibility with PP, and the soft plastic overlay enhances the grip.
Jomar’s devotion to exemplary customer service is manifest in their all-encompassing support initiatives, which encompass educational programs, technical assistance, and maintenance services. This client-centric philosophy, when amalgamated with their profound technical acumen, cements Jomar’s reputation as a dependable ally in the injection blow molding sphere, underlining their commitment to fostering enduring partnerships within the industry.
Dual-color and multi-color injection molding has become a focal point in the evolution of injection molding technology, and its benefits are manifold. Various techniques allow for different hardness and resilience within the same component. Soft plastics like TPE offer diverse color options, transparent surfaces, and other appealing features, enhancing aesthetic design. This method eliminates assembly steps, shortens the molding cycle, reduces processing costs, and offers added value to the end-users in terms of design, quality, and functionality.
The ethos of UBE Machinery is firmly rooted in innovation, a principle that is vividly reflected in their ongoing enhancements to machine functionalities. A notable advancement is the integration of advanced servo-hydraulic systems, which markedly improves control and elevates energy efficiency. This unwavering focus on technological progression has cemented UBE’s stature as a purveyor of dependable, high-caliber injection molding solutions.
Moreover, Shibaura Machine’s dedication to upholding exceptional quality standards is further exemplified by its comprehensive array of customer service offerings. These encompass extensive training programs, meticulous maintenance services, and robust support systems, all meticulously structured to optimize the operational performance of Shibaura machinery. This amalgamation of technological prowess and steadfast customer support solidly positions Shibaura Machine Co., Ltd. as a leader within the injection molding machinery arena.
Products made using multi-color injection molding have a significantly different structure compared to regular plastic products. When designing the structure and shape of these products, it’s essential to consider their intended use and purpose. It’s crucial to delve deep into the structural design of the injection-molded product, taking into account the compatibility features of the various materials used. Typically, the design aims to increase the contact area of the raw materials to enhance solidity. This can be achieved by incorporating numerous small recesses and protrusions within the product, which serve to increase the material’s contact area, thereby improving the product’s strength, lifespan, and practicality.
In the design of multi-color/multi-material injection molded products, two primary methods are used to join adjacent components:
The expansive global footprint of Netstal, coupled with its exhaustive support services, guarantees that clients have unfettered access to profound expertise and support, tailored to their precise needs. This synthesis of technological mastery and a client-oriented service ethos solidifies Netstal’s position as a leading purveyor of injection molding solutions, underscoring their commitment to excellence and sustainability in the field.
Tracing its origins to 1857, Netstal, a distinguished member of the KraussMaffei Group, stands as a paragon of Swiss engineering, exemplifying unmatched precision and exemplary quality in the arena of high-performance injection molding machinery. Netstal caters to the exigent requirements of sectors such as packaging, medical, and electronics, where their machinery is tailored for unparalleled speed, accuracy, and dependability. Their specialization in high-velocity, thin-wall applications differentiates them, providing solutions that harmonize elevated production rates with superior product integrity.
Name:Email:WhatsApp:Message:File Type: STEP, X-T, IGS, STL, DXF, DWG, PDF, JPG etc.*We respect your confidentiality and all information are protected.
With the development of the injection molding industry, innovative techniques have emerged, pushing the boundaries of what’s possible in manufacturing. One such groundbreaking method is multi-shot injection molding. At Prototool, we’ve harnessed this advanced process, allowing for the creation of intricate and multi-material components in a single cycle. This offers unparalleled precision and design flexibility. In this article, we’ll delve into the nuances of this technique, shedding light on its benefits, design considerations, and its transformative potential in the realm of injection molding.
ACO Mold, entrenched within the dynamic industrial expanse of China, has meticulously honed its expertise in the realm of custom injection molding, with a pronounced focus on complex mold designs and high-volume manufacturing endeavors. Inaugurated in the year 2000, ACO Mold’s odyssey commenced with a steadfast commitment to crafting bespoke solutions adept at servicing a plethora of sectors, encompassing consumer electronics, automotive, and medical apparatuses. The enterprise is heralded for its integration of advanced CAD/CAM technologies, synergized with venerable artisanal methodologies, culminating in the creation of molds that epitomize unparalleled precision and durability.
With a venerable legacy spanning over 24 years and a manufacturing facility encompassing 2,000 square meters, ACO Mold is equipped to churn out 25-35 injection mold sets on a monthly basis, exemplifying their manufacturing acumen. This prowess is fortified by an arsenal of cutting-edge machinery, including high-velocity CNC apparatus and precision EDM devices, guaranteeing that each mold adheres to the zenith of quality and functional standards. ACO Mold’s allegiance to pioneering advancements is further exemplified in their sustainable approach, adopting environmentally benign materials and methodologies to diminish their ecological footprint.
The ambit of Jomar’s innovation extends well beyond the confines of machine fabrication; the company is also a vanguard in the evolution of novel blow molding methodologies and technological advancements. This unwavering commitment to the progression of blow molding technology ensures that Jomar’s clientele is consistently at the cutting edge, benefiting from enhancements in product quality and manufacturing efficiency.
Multi-shot injection molding requires a high level of process and plant resources. This plastic-making method has changed how we design and make products, making them look and work better. As industries continue to seek innovative solutions, Prototool emerges as a leader in the field, specializing in plastic products and parts manufacturing using the two-shot injection molding process and multi-shot techniques. With a commitment to precision, quality, and cutting-edge technology, Prototool is not just a manufacturer but a partner for businesses aiming for excellence. As we navigate the future of plastic manufacturing, aligning with pioneers like Prototool ensures a journey marked by innovation, efficiency, and unparalleled expertise.
Nave ISK-8, Parque Industrial y Logístico Sky Plus, Avenida Mineral de Cinco Señores No.100, del Parque Industrial Santa Fe, Silao de la Victoria, Guanajuato, México
6. When designing the cavity for the second injection, some voids can be incorporated to prevent the newly formed product from being scratched or scraped by the mold. However, it’s crucial to carefully assess the strength of each sealing position to ensure that no flash occurs due to high injection pressures.
Beyond the realms of machine production, UBE Machinery’s expertise proliferates into the realm of pioneering new molding techniques and material development. This unyielding dedication to innovation ensures that clients of UBE Machinery are consistently at the vanguard of injection molding technology. Such access to cutting-edge advancements empowers them to realize optimal production efficiencies and outcomes, further solidifying UBE Machinery’s position as an industry leader in the field.
Established in 1964, EVCO Plastics has emerged as a preeminent purveyor of bespoke injection molding services within the United States. Renowned for their specialization in the fabrication of high-precision, compliance-oriented plastic components, EVCO caters to essential industries including medical, automotive, and consumer electronics. Their prowess is anchored in an integrated project management paradigm that spans the spectrum of design, prototyping, and large-scale production, guaranteeing cohesive execution and superior quality deliverables.
Shibaura Machine is unwavering in its commitment to propel the boundaries of injection molding technology, with a substantial emphasis placed on research and development initiatives. This relentless pursuit of innovation results in the provision of machinery that is endowed with the most advanced control systems, automation capabilities, and energy efficiency measures, thereby ensuring that Shibaura’s clientele are equipped with the most advanced, sustainable manufacturing solutions presently available.
Milacron, a venerable institution with origins tracing back to 1884, stands as a colossus within the realm of plastic processing, anchoring its presence in the United States. Over the decades, Milacron has diversified its portfolio to encompass a sophisticated array of injection molding machines, extrusion apparatus, and an extensive suite of ancillary offerings. The cornerstone of their esteemed reputation rests on the seamless integration of advanced technologies coupled with a client-centric modus operandi, yielding solutions that are comprehensive in scope—spanning system architecture, process refinement, and an unwavering commitment to post-sale assistance.
Choosing the best injection mold provider is a pivotal choice with significant implications for the outcome of your production efforts. The firms spotlighted within this overview stand out as leaders in the realm of injection molding, each with distinct proficiencies and insights. Whether your prerequisites involve bespoke mold designs, sizeable manufacturing runs, or state-of-the-art methodologies, these premier mold manufacturers deliver the necessary resources and assistance to fulfill your production goals. In the ever-advancing domain of injection molding, teaming up with a distinguished expert guarantees the benefit of the most recent innovations, unparalleled quality benchmarks, and the most inclusive range of services presently available.
At the vanguard of technological convergence, Milacron is renowned for the infusion of intelligent systems within their machinery, empowering manufacturers with pivotal insights and operational efficiencies. This dedication to the forefront of innovation permeates their spectrum of services, meticulously curated to bolster clients across the entire spectrum of their equipment’s lifespan—from the initial commissioning and educational undertakings to the continuous maintenance and enhancement of performance.
5. Choosing the right material is vital. Consider factors like the material’s adhesiveness, potential deformation during injection, and risks associated with melting.
Shibaura Machine Co., Ltd., originally inaugurated as Toshiba Machine, has been a pivotal force in the injection molding machinery sector since its establishment in 1938. Esteemed for its integration of avant-garde technological innovations and unmatched reliability, Shibaura furnishes a broad spectrum of engineered solutions, intricately designed to address the complex requisites of the injection molding industry. Their commitment to fostering applications that necessitate elevated velocity and precision has rendered them a preferred partner among manufacturers within key sectors, including automotive, electronics, and premium consumer goods.
EVCO’s state-of-the-art facilities are equipped with the latest in injection molding machinery and technological innovations, empowering them to navigate the complexities of sophisticated projects with utmost efficiency and exactitude. Their dedication to pioneering advancements is paralleled by a fervent commitment to sustainable manufacturing protocols, underscoring a profound cognizance of both the environmental and fiscal advantages of green operations.
Jomar Corp, inaugurated in 1968 within the United States, has ascended to a position of distinction as an expert in the domain of injection blow molding machinery. Their equipment serves as a pivotal resource for sectors demanding superior-grade, precision-engineered plastic bottles and containers, notably within the pharmaceutical and cosmetics industries. The injection blow molding machines crafted by Jomar are celebrated for their steadfast reliability, operational efficiency, and versatile compatibility with an extensive assortment of materials and mold configurations.
Adding a textured finish to the surface of TPE products can give a leather-like feel, enhancing tactile sensation and masking surface imperfections. Some textures can also adjust the surface hardness of TPE products, making them softer or harder than when made with a smooth TPE surface. If designers polish the TPE surface to a mirror finish, it may exhibit many flow lines and color streaks, or it may turn white during use, degrading the surface quality.
12. Provisions for venting during the first, second, or subsequent injections need to be thought out in advance to prevent defects and ensure quality.
Netstal’s machinery represents the zenith of technological advancement, incorporating sophisticated control systems and mechanisms for energy conservation. This dedication to pioneering innovation and operational efficiency ensures that Netstal’s clientele can realize optimal manufacturing outcomes while concurrently mitigating environmental footprints.
Milacron’s machinery is crafted with an emphasis on enduring resilience, impeccable precision, and adaptability, thereby ensuring compatibility with an extensive variety of materials and application scenarios. This adaptability, in conjunction with Milacron’s expansive network of service and support, guarantees that clients are equipped with the necessary resources to maintain a competitive edge in an industry characterized by its relentless pace of evolution. The proficiency of Milacron’s machinists in managing the intricate processes of discharge, mold closing, product design, and the fabrication of production molds further cement their status as a pivotal entity within the industry.
11. To achieve tighter bonding between materials, consider the “stickiness” between materials and the roughness of the mold surface.
ENGEL Austria GmbH, inaugurated in the year 1945, epitomizes the zenith of innovation and unparalleled quality within the specialized sphere of plastic injection mold manufacturing. Originating from the industrious landscapes of Austria, ENGEL has burgeoned into a globally recognized colossus, acclaimed for its cutting-edge injection molding machinery and comprehensive system solutions. The spectrum of offerings from ENGEL is a testament to their engineering acumen, encompassing an array of machines from high-precision, compact units designed for intricate component fabrication to robust, large-scale systems engineered for the mass production of automotive parts.
The company’s adeptness in orchestrating complex endeavors, allied with an unwavering dedication to client contentment, establishes EVCO Plastics as a vanguard in the realm of custom injection molding. Their capacity to furnish bespoke, top-tier solutions affirms their status as the go-to collaborator for entities in pursuit of comprehensive injection molding services, epitomizing their role as a beacon of excellence in the industry.
3. Before designing the mold, it’s crucial to understand the parameters of the multi-color injection molding machine intended for mass production. This includes data like maximum/minimum mold capacity, mold thickness, and the distance between ejector pins.
7. The product from the first injection can be slightly oversized. This ensures a tighter fit during the second molding, achieving a better sealing effect.
2. It’s imperative to ensure that after the back mold rotates around its center, it aligns perfectly with the front mold. This aspect requires careful attention during design.
As products became more intricate, the demand for tri-color and even quad-color molding began to rise. Generally, there are two types of tri-color machines: the two-station tri-color machine (colloquially known as the “pseudo tri-color”) and the three-station tri-color machine (known as the “true tri-color”). The distinction between the two isn’t about authenticity but rather the product structure design and the turntable control method adopted.
The accolades bestowed upon ENGEL’s machinery underscore their exceptional accuracy, operational efficacy, and multifaceted adaptability, making them indispensable to a wide range of industries, including but not limited to, the medical, automotive, and consumer goods sectors. ENGEL’s allegiance to sustainable manufacturing practices is evidenced by their commitment to developing machines that are both energy-efficient and resource-conserving. This not only facilitates a reduction in operational overheads but also aligns seamlessly with the imperative global endeavors towards environmental sustainability.
GETTING A QUOTE WITH LK-MOULD IS FREE AND SIMPLE.
FIND MORE OF OUR SERVICES:
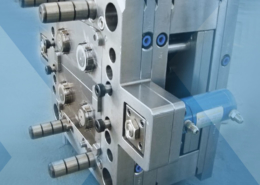
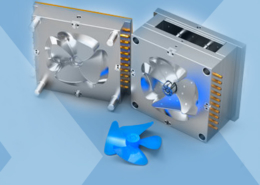
Plastic Molding

Rapid Prototyping
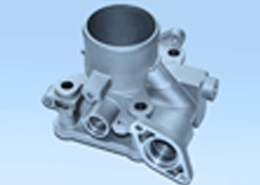
Pressure Die Casting
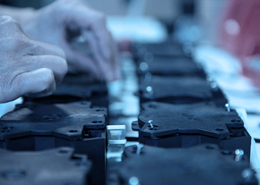
Parts Assembly
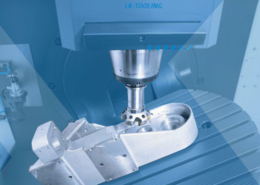